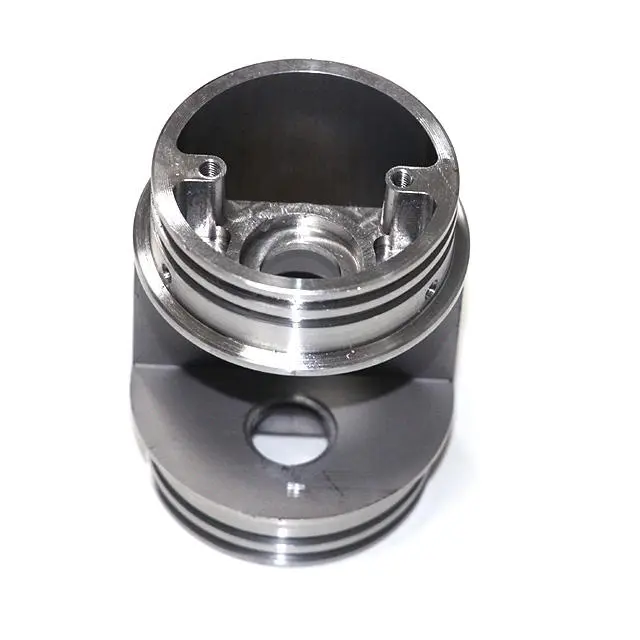
- +8615586668226
- [email protected]
- رقم 30، حديقة هونغبانغ الصناعية، شينزين
Cloud-based CNC (C-CNC) represents a paradigm shift in the world of manufacturing. It moves traditional CNC functionalities from local machines to the cloud, offering a service-based model. In essence, C-CNC allows manufacturing machines to be controlled remotely via the internet, leveraging the vast computational resources available in the cloud. This shift is crucial because it enables even small and medium-sized enterprises (SMEs) to access advanced control algorithms and processing capabilities that were previously out of reach due to hardware limitations.
The importance of C-CNC lies in its ability to democratize advanced manufacturing technologies. By decoupling the control system from the physical machine, C-CNC allows for greater flexibility, scalability, and cost-effectiveness. As a company deeply invested in حلول CNC, we see C-CNC as a game-changer, capable of transforming the way products are designed, manufactured, and delivered. Imagine being able to update your manufacturing processes or troubleshoot issues in real-time from anywhere in the world, these capabilities are now within reach, thanks to C-CNC.
The benefits of C-CNC are far-reaching and applicable across a wide array of industries. For instance, in the الطيران والفضاء sector, where precision and reliability are paramount, C-CNC can enable the implementation of complex algorithms for optimizing flight paths and reducing fuel consumption, الطيران والفضاء. Similarly, in the السيارات industry, C-CNC can facilitate the rapid prototyping and production of custom parts, driving innovation and accelerating time-to-market. Our experience as a product manufacturing factory that caters to many industries has shown that C-CNC can significantly improve production efficiency and quality.
في الأجهزة الطبية sector, C-CNC can enable the production of highly customized implants and prosthetics tailored to individual patient needs. In الإلكترونيات, it allows for the precise manufacturing of intricate components. In the المعدات الصناعية القطاع, التصنيع عند الطلب capabilities provided by C-CNC can optimize inventory management and reduce lead times. Even in sectors like السلع الاستهلاكية و الفن والتصميم, C-CNC can empower creators with the tools to bring their visions to life with unprecedented precision and efficiency. In other words, no matter which field you’re in, C-CNC has the potential to enhance your operations.
Despite its many advantages, implementing C-CNC is not without its challenges. One of the primary concerns is the reliability of real-time control over the internet. Issues such as time delays, dropped packets, and other internet quality-of-service (QoS) problems can compromise the safety and precision of manufacturing processes. For example, inconsistent network connections can cause unexpected pauses or errors in the manufacturing process, which is simply not acceptable in industries with stringent quality standards.
These challenges are particularly pronounced when controlling machines remotely over long distances, where latency can be significant. In a traditional CNC setup, the control system is located locally, ensuring near-instantaneous communication between the controller and the machine. However, in a C-CNC environment, control signals must travel across the internet, introducing potential delays that can affect the accuracy and reliability of the manufacturing process. This is a critical issue that needs to be addressed to unlock the full potential of C-CNC.
Data size reduction plays a pivotal role in mitigating the challenges associated with C-CNC. By minimizing the amount of data transmitted over the internet, we can improve the efficiency and reliability of the control system. This is especially critical in scenarios with high latency or limited bandwidth, where large data packets can exacerbate delays and increase the risk of errors. The smaller the data packets, the quicker they can be transmitted, reducing the impact of network latency.
In the context of 3D printing, reducing the size of control commands can prevent issues such as frequent pauses during printing, which can lead to poor surface finishes and reduced print quality. By ensuring a smooth and continuous flow of data to the printer, we can maintain consistent print speed and accuracy. As a خدمة التصنيع الآلي باستخدام الحاسب الآلي الرقمي provider, we have observed firsthand how crucial data size reduction is for ensuring the seamless operation of cloud-based systems. When data is transmitted efficiently, the entire manufacturing process becomes more robust and dependable.
Traditional data compression methods, such as Deflate, BWT, LZMA, PPMd, and Zstandard, offer a potential solution for reducing data size in C-CNC applications. These algorithms work by identifying and eliminating redundancies in the data, thereby reducing the overall size of the transmitted information. For instance, these methods are widely used in various applications to compress files, making them easier to store and transmit.
However, in the specific context of C-CNC for 3D printing, these methods have limitations. Benchmarking tests have shown that while these algorithms can achieve a certain degree of compression, their performance is often inconsistent, with large variations in compression ratios. Moreover, the computational resources required for decompression can be substantial, often exceeding the capabilities of the microprocessors typically used in 3D printers. This makes them impractical for real-time control applications where low latency and minimal processing overhead are essential. It’s like trying to fit a huge engine into a small car – it just doesn’t work efficiently.
Compression Method | Mean Compression Ratio | Standard Deviation | Memory Usage (MB) |
---|---|---|---|
Deflate | 0.6 | 0.1 | 2 |
BWT | 0.59 | 0.11 | 3 |
LZMA | 0.58 | 0.15 | 7 |
PPMd | 0.49 | 0.08 | 3 |
Zstandard | 0.62 | 0.12 | 1 |
Pseudo-lossless data truncation is a novel approach to data size reduction that leverages knowledge of the physical limitations of the manufacturing system. Unlike traditional compression methods, which focus on eliminating data redundancies, truncation removes information that is not essential for control, based on the specific characteristics of the machine. For instance, in a 3D printer, we can analyze the maximum speed, resolution, and other parameters to determine the minimum necessary precision for motion commands.
The process involves analyzing the motion commands and identifying data points that exceed the physical capabilities of the printer. For example, if a printer has a maximum speed of 100 mm/s and a resolution of 0.000625 mm/step, we can truncate the motion commands to a precision that reflects these limits. This approach ensures that no critical information is lost while significantly reducing the size of the data packets. In simple terms, it’s about keeping what’s necessary and discarding the rest.
Data truncation has proven to be highly effective in real-world 3D printing scenarios. In experiments conducted using a cloud-based controller, implementing data truncation resulted in a fixed data reduction ratio of 45%, significantly outperforming traditional compression methods. By transmitting truncated motion commands, we were able to achieve consistent, high-quality prints even under high-latency network conditions. This is a significant improvement, especially when you consider the variability and limitations of compression methods.
For example, when printing a calibration cube from locations with high latency, such as Mumbai and Sydney, using data truncation eliminated frequent pauses and ensured smooth, continuous printing. The print quality remained consistent, and the print times were comparable to those achieved under low-latency conditions. These results demonstrate the practical benefits of data truncation for enhancing the reliability of C-CNC in 3D printing. It’s like having a secret weapon that ensures your manufacturing process runs smoothly, no matter the conditions.
Here are some statistics from our experiments:
The implications of data truncation extend beyond 3D printing and can benefit various manufacturing sectors. In الطيران والفضاء و السيارات industries, where precision and reliability are critical, data truncation can ensure that control commands are transmitted efficiently, minimizing the risk of errors due to network latency, السيارات. Similarly, in the الأجهزة الطبية sector, where customized, high-precision parts are often required, data truncation can enhance the reliability of remote manufacturing processes. These sectors require parts and tools made with high precision, which is where التصنيع الآلي الدقيق comes in handy.
في عالم المعدات الصناعية, the ability to transmit control data efficiently can streamline operations and reduce downtime. For المنتجات الاستهلاكية, data truncation can enable faster prototyping and production cycles, accelerating time-to-market. Even in الروبوتات, where precise control is essential, data truncation can improve the responsiveness and reliability of cloud-based control systems. By reducing the amount of data transmitted, we can ensure that manufacturing processes remain robust and efficient across a wide range of applications.
While data truncation represents a significant step forward, there is always room for further improvement. One potential avenue is the development of more sophisticated algorithms that can dynamically adjust the level of truncation based on real-time network conditions. This could involve monitoring network latency and bandwidth and adapting the data reduction strategy accordingly. Imagine a system that can intelligently adjust itself based on the current conditions – that’s the future we’re aiming for.
Another approach could involve the use of redundant cloud and local controllers to provide a fallback mechanism in case of severe network degradation or loss of connectivity. This distributed framework could enhance the overall robustness of the system, ensuring that manufacturing processes can continue uninterrupted even under adverse conditions. Additionally, exploring edge/fog computing solutions could further reduce latency by bringing computational resources closer to the manufacturing machines.
The future of C-CNC and data reduction techniques is bright, with ongoing research and development poised to unlock new capabilities and applications. As cloud technologies continue to evolve and mature, we can expect to see even more sophisticated and efficient methods for controlling manufacturing processes remotely. The integration of artificial intelligence and machine learning could further enhance the adaptability and performance of C-CNC systems. The تصنيع الصفائح المعدنية process is also being improved by these advances.
Data reduction techniques, such as pseudo-lossless truncation, will play a crucial role in enabling the widespread adoption of C-CNC across various industries. By addressing the challenges associated with network latency and bandwidth limitations, these techniques will pave the way for more reliable, efficient, and flexible manufacturing processes. As a leading خدمة التصنيع باستخدام الحاسب الآلي الرقمي provider, we are committed to staying at the forefront of these developments, driving innovation and delivering cutting-edge solutions to our customers. The future of manufacturing is here, and it’s more exciting than ever.
What makes C-CNC different from traditional CNC machining?
Traditional CNC machining relies on locally installed control systems, while C-CNC leverages cloud-based resources for control, offering greater flexibility, scalability, and access to advanced algorithms.
How does data size reduction impact print quality in 3D printing?
Data size reduction minimizes the amount of data transmitted over the internet, reducing the likelihood of pauses and errors during printing, thus maintaining consistent print speed and accuracy. It’s about working smarter, not harder, to achieve the best results.
Can data truncation be applied to other manufacturing processes besides 3D printing?
Yes, data truncation can be adapted to various manufacturing processes that require precise, real-time control, such as those in the aerospace, automotive, and medical device industries.
What are the limitations of traditional data compression methods in C-CNC?
Traditional data compression methods often have inconsistent performance and require substantial computational resources for decompression, making them less suitable for real-time control applications in C-CNC.
How does the use of redundant controllers improve C-CNC reliability?
Redundant controllers provide a backup mechanism in case of network issues, ensuring that manufacturing processes can continue uninterrupted even if the primary cloud connection is lost.
What role does edge/fog computing play in enhancing C-CNC?
Edge/fog computing brings computational resources closer to the manufacturing machines, reducing latency and improving the responsiveness of the control system.
بصفتك product manufacturing factory dedicated to innovation, we are excited about the potential of C-CNC and data reduction techniques to revolutionize the manufacturing landscape. By embracing these advancements, we can drive efficiency, enhance quality, and deliver superior products to our customers.
الروابط الداخلية:
العنوان
رقم 30، متنزه هونغبانغ الصناعي، شينزين
البريد الإلكتروني
[email protected]
الهاتف
+86 15586668226
احصل على أحدث الاتجاهات والحقائق حول التصنيع باستخدام الحاسب الآلي من مدونتنا.
شركة Shenzhen Runkey Precision Technology Co. Ltd، وهي شركة تابعة لمجموعة Tensun Group، هي الحل الشامل الموثوق به للتصنيع المخصص بدءًا من النماذج الأولية وحتى الإنتاج، حيث إنها تحول فكرتك إلى واقع ملموس من خلال موارد التصنيع الرقمية، والعمليات المبسطة، وتوجيهات الخبراء، والجداول الزمنية المتسارعة، والجودة التي لا تقبل المساومة.
©2024. التصنيع باستخدام الحاسب الآلي جميع الحقوق محفوظة.