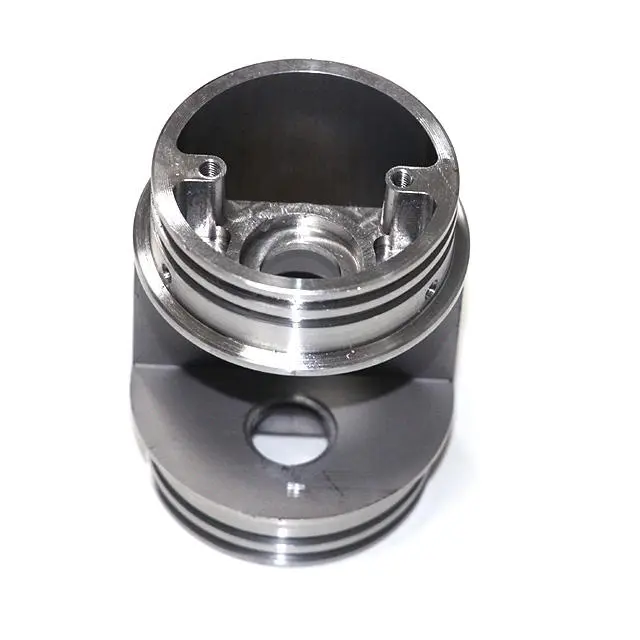
- +8615586668226
- [email protected]
- رقم 30، حديقة هونغبانغ الصناعية، شينزين
In-process inspection is a crucial quality control method used during manufacturing. Instead of waiting until the end, we examine products while they’re being made. This proactive approach is key to maintaining product integrity and streamlining production. It’s like having checkpoints throughout a race, ensuring everything is on track.
Here’s why embracing in-process inspection is beneficial:
Knowing عندما to inspect is just as important as knowing كيف. We strategically place inspection checkpoints where they can most effectively catch errors and ensure top quality.
Key Production Stages for Inspection:
المرحلة | الوصف | Why It’s Important |
---|---|---|
Raw Material Check | Inspecting materials upon arrival for quality and specs. | Ensures only top-quality materials are used, preventing issues later. |
Post-Assembly Check | A detailed review after assembly to confirm correct assembly and function. | Catches any assembly errors before they become bigger problems. |
Final Inspection | A thorough check before shipping to meet all quality and functional needs. | Guarantees the product is ready for the customer, meeting all requirements. |
Initial Processing | Very early production stages. | Checking size accuracy, material defects. |
Key Production Phases | Inspections before and after important changes. | Help to verify no errors were introduced |
Pre-packaging Check | Product meets the quality standards. | No damage, ready to be shipped. |
We use three main types of inspections: visual, dimensional, and functional. Each uses specific tools and methods to ensure thorough and accurate checks.
Visual inspections are the first defense in quality control. Inspectors examine products for surface flaws, alignment, and overall look, ensuring each part meets visual quality standards. We use high-resolution cameras, magnifying glasses, and imaging software to spot even tiny imperfections.
Dimensional inspections measure the physical sizes of parts to make sure they match the specifications. Tools like calipers, micrometers, and Coordinate Measuring Machines (CMMs) are commonly used. These tools give precise measurements, vital for parts that need to fit perfectly in complex assemblies, such as in aerospace and automotive.
Check out our CNC Machining Services here!
Functional testing checks how a part or assembly works under conditions that mimic real-world use. This can include stress tests, leak tests, and electrical tests. We use various tools, from load testers to circuit testers and simulation software, ensuring that every product will perform as expected.
Effective in-process inspections require careful planning, execution, and follow-up. Here’s a step-by-step guide to making every inspection phase count towards overall manufacturing quality:
Clear standards are the foundation of effective inspections. These should be well-defined, documented, and accessible to everyone involved. We use a continuous feedback loop between production and quality assurance to refine these standards.
Thorough training is essential to equip your team with the necessary skills. Training covers the latest techniques, tools, and industry standards like ISO 9001. Regular workshops keep everyone up-to-date.
Learn about our commitment to quality in our Quality Assurance page.
Using the correct tools is crucial for effective inspections. These tools must be accurate, reliable, and efficient.
Essential Inspection Tools:
In-process inspection offers many benefits that significantly improve production efficiency and quality.
المزايا الرئيسية:
While beneficial, in-process inspections also present challenges.
Common Challenges:
Even with robust systems, mistakes can happen. Here’s how to avoid them:
Common Mistakes and Solutions:
خطأ | الحل |
---|---|
Overlooking Minor Defects | Train inspectors to be meticulous and use advanced inspection tools. |
Inconsistent Standard Application | Develop and enforce standardized procedures for all inspections. |
Inadequate Training | Provide ongoing training on the latest techniques and standards. |
Failure to Update Protocols | Regularly review and update inspection protocols. |
Poor Documentation | Implement a robust documentation system to record all results and procedures. |
Statistical Process Control (SPC) is a data-driven method for quality control that uses statistical methods to monitor and control a process. It helps ensure the process operates at its best, producing as much conforming product as possible with minimal waste.
How SPC Works:
Discover how we use advanced techniques in our Precision CNC Machining process.
The quality of materials from suppliers directly affects the quality of the final product. Effective supplier monitoring is crucial.
Supplier Monitoring Methods:
Continuous improvement is essential for modern quality management. It significantly enhances the effectiveness of in-process inspections.
Key Elements of Continuous Improvement:
Effective documentation and analysis of in-process inspection results are vital for maintaining a robust quality assurance system.
Documentation Benefits:
Analysis Methods:
Proper scheduling and planning are essential for effective in-process inspections.
Steps for Scheduling:
Considerations:
In-process inspections are vital across various industries, each adapting its approach to meet specific needs.
Ensures safety and reliability through dimensional checks, material property verification, and assembly testing. Automated systems are common.
Manages complexity through inspections of soldering quality, component placement, and circuit functionality. Advanced imaging and electrical testing are crucial.
Demands high precision and safety. Inspections include checking batch weights, formulations, and testing for contamination. Strict documentation is required.
Precision and adherence to design are paramount. State-of-the-art equipment and comprehensive inspection systems are used.
The field of in-process inspection is rapidly evolving, driven by technological advances.
Key Innovations:
Explore our Advanced Manufacturing Capabilities.
Here are some common questions about in-process inspection:
What’s the main difference between in-process inspection and final inspection?
In-process inspection happens خلال production, catching issues early. Final inspection occurs at the النهاية of production, serving as a last quality check before shipping.
How often should in-process inspections be performed?
It depends on factors like production volume, product complexity, and industry regulations. Critical points in the process should always have inspection checkpoints.
Can in-process inspection completely eliminate the need for final inspection?
While it significantly reduces defects, final inspection is still crucial as a final verification step before products reach customers.
What role does employee training play in effective in-process inspection?
Properly trained employees are vital. They need to understand procedures, use tools correctly, and identify potential issues accurately.
How important is the record?
Very important, to facilitate the tracing of the cause of the problem, and for continuous improvement.
How can our CNC manufacturing services benefit your in-process inspection needs?
We offer state-of-the-art equipment, precise machining capabilities, and rigorous quality control processes, ensuring your parts meet the highest standards at every stage of production. Contact us to learn more about our Custom CNC Machining.
In-process inspection is a cornerstone of modern manufacturing, ensuring quality, efficiency, and customer satisfaction. Here are the key points to remember:
By embracing in-process inspection, your business can achieve higher quality, lower costs, and greater customer satisfaction. Ready to elevate your manufacturing processes? Contact us today to discuss your project!
العنوان
رقم 30، متنزه هونغبانغ الصناعي، شينزين
البريد الإلكتروني
[email protected]
الهاتف
+86 15586668226
احصل على أحدث الاتجاهات والحقائق حول التصنيع باستخدام الحاسب الآلي من مدونتنا.
شركة Shenzhen Runkey Precision Technology Co. Ltd، وهي شركة تابعة لمجموعة Tensun Group، هي الحل الشامل الموثوق به للتصنيع المخصص بدءًا من النماذج الأولية وحتى الإنتاج، حيث إنها تحول فكرتك إلى واقع ملموس من خلال موارد التصنيع الرقمية، والعمليات المبسطة، وتوجيهات الخبراء، والجداول الزمنية المتسارعة، والجودة التي لا تقبل المساومة.
©2024. التصنيع باستخدام الحاسب الآلي جميع الحقوق محفوظة.