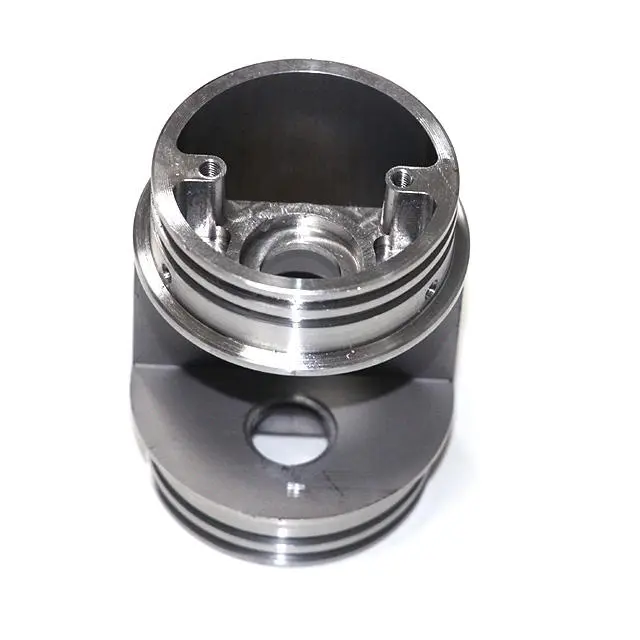
- +8615586668226
- [email protected]
- رقم 30، حديقة هونغبانغ الصناعية، شينزين
Deburring is a finishing process that removes burrs – the raised edges or small pieces of material that remain on a workpiece after machining operations like cutting, punching, or stamping. In sheet metal fabrication, burrs are a common occurrence, and their removal is critical for several reasons.
Firstly, burrs can compromise the safety of the product, posing a risk of cuts or injuries to handlers or end-users. Secondly, they can interfere with the proper assembly and functionality of parts, leading to misalignment or malfunction. Lastly, burrs can negatively impact the aesthetic appeal of a product, making it look unfinished or of poor quality. As a CNC machining service provider, we prioritize deburring to ensure the safety, functionality, and aesthetics of every component we produce.
خبرتنا في التصنيع الآلي باستخدام الحاسب الآلي و التصنيع الآلي الدقيق ensures that burrs are effectively removed, leaving behind smooth, clean edges. This is particularly important in industries like aerospace and medical devices, where precision and safety are paramount.
Barrel finishing is a mass finishing technique that involves placing workpieces, along with abrasive media and compounds, into a rotating barrel. As the barrel rotates, the contents tumble, causing the media to rub against the workpieces, thereby removing burrs and smoothing the edges. The process is akin to the natural smoothing of rocks in a riverbed, but in a controlled environment.
The mechanism of barrel finishing relies on the relative motion between the media, the workpieces, and the compound. The media, typically made of ceramic, plastic, or steel, acts as the abrasive agent. The compound, which can be a liquid or a dry powder, aids in cleaning, lubricating, and enhancing the surface finish. A typical barrel finishing machine, as the research indicates, might be used to process multiple washers at a time by rotating them with media and a special compound.
لدينا خدمات التصنيع include advanced barrel finishing techniques. We use state-of-the-art equipment and carefully selected media to ensure optimal results. As the study demonstrates, the process can be tailored to achieve specific surface finishes, from rough to super-finishing, making it ideal for components in industries such as automotive and electronics.
Barrel finishing offers several advantages over other deburring methods, making it a preferred choice for many applications. One of the primary benefits is its ability to process multiple parts simultaneously, leading to high productivity and cost savings. As noted in the research, barrel finishing can reduce costs by up to 20-30% compared to manual deburring in certain cases.
Another advantage is the uniformity of the finish achieved through barrel finishing. The tumbling action ensures that all surfaces and edges of the workpieces are evenly treated, resulting in a consistent finish across all parts. The process can also improve the surface roughness and even add a polished look. The forces in barrel finishing are minimal. It’s effective and safe for thin, fragile parts.
We leverage these advantages in our تصنيع الصفائح المعدنية processes, ensuring that every component we produce meets the highest quality standards. This is particularly important for our clients in the consumer products and industrial equipment sectors, where both aesthetics and functionality are crucial.
Table: Comparison of Deburring Methods
الطريقة | المزايا | العيوب |
---|---|---|
Barrel Finishing | High productivity, uniform finish, cost-effective, suitable for delicate parts, improves surface roughness | Longer processing time, may not be suitable for very large or heavy parts |
Manual Deburring | Precise control, suitable for complex shapes | Labor-intensive, time-consuming, inconsistent results, risk of injury |
Vibratory | Faster than barrel finishing, good for larger parts | Can be noisy, may not be suitable for very delicate parts |
Abrasive Flow | Suitable for internal passages and complex geometries | Expensive equipment, requires specialized tooling |
Thermal | Fast, good for removing internal burrs | Can affect material properties, may not be suitable for all materials |
Electrochemical | Burr-free, good surface finish | Expensive equipment, requires electrolytes, may not be suitable for all materials |
Robotic | Automated, precise, consistent | High initial investment, requires programming expertise |
Blasting | Cleans and deburrs, good for large areas | Can be messy, may not be suitable for delicate parts, can alter surface texture |
Bold: As highlighted in the table, barrel finishing stands out for its high productivity, uniform finish, and cost-effectiveness, particularly for delicate parts and improving surface roughness.
Barrel finishing is a versatile process that can be used on a wide range of metals, including steel, stainless steel, aluminum, brass, copper, and titanium. The research focused on the deburring of steel washers. But the process is effective for many materials and parts. This makes it suitable for various industries, from aerospace to medical devices.
The process is particularly well-suited for small to medium-sized parts, such as:
As a product manufacturing factory, we have extensive experience in barrel finishing a wide array of products. This includes components for the الطيران والفضاء industry, where precision and reliability are paramount, as well as parts for consumer electronics, where a flawless finish is essential for aesthetic appeal.
Optimizing the barrel finishing process involves carefully selecting the appropriate parameters, including barrel size, rotation speed, media type and size, compound type and concentration, and processing time. The research provides detailed data on how these parameters affect the deburring process, particularly the relationship between processing time and burr height. As an example, the rotation speed affects how the parts and media interact. A speed of 40 rpm was used in the study to create a cascading effect, aiding in deburring.
The ratio of media to parts is also crucial. A higher ratio generally results in a more aggressive action, while a lower ratio leads to a gentler action. The type and concentration of the compound can affect the cleaning and brightening of the parts.
List: Factors Affecting Barrel Finishing Efficiency
As a leading factory in CNC solutions, we have developed proprietary optimization techniques based on years of experience and research. Our النماذج الأولية السريعة services often utilize these optimized processes to deliver quick turnaround times without compromising quality.
Media and compounds are essential components of the barrel finishing process. The media provides the abrasive action necessary for deburring and surface refinement, while the compound aids in cleaning, lubricating, and enhancing the finish.
Media can be made from various materials, including:
Compounds can be:
The choice of media and compound depends on the material being processed, the desired finish, and the specific requirements of the application. For example, ceramic media might be used for deburring steel parts, while plastic media might be preferred for softer metals like aluminum.
As part of our comprehensive حلول CNC, we offer expert guidance on selecting the right media and compounds for your specific needs. We understand that the right combination can make a significant difference in achieving the desired finish and optimizing the process.
While barrel finishing is a highly effective deburring method, it’s essential to understand how it compares to other techniques to make an informed decision for your specific application.
الميزة | Barrel Finishing | Manual Deburring | Vibratory Finishing |
---|---|---|---|
الإنتاجية | High, processes multiple parts simultaneously | Low, labor-intensive | Medium to high, faster than barrel finishing |
التوحيد | Excellent, all surfaces treated evenly | Inconsistent, depends on operator skill | Good, but may not reach all areas equally |
التكلفة | Low to medium, cost-effective for large batches | High, labor costs | Medium, higher equipment cost than barrel finishing |
حجم الجزء | Small to medium | Any size, but more practical for larger parts | Small to large, can handle larger parts than barrel |
Delicate Parts | Suitable, gentle action | Risk of damage, requires careful handling | Can be suitable, but may be too aggressive for some parts |
تشطيب السطح | Good to excellent, can achieve various finishes | Depends on operator skill and tools used | Good to excellent, can achieve fine finishes |
الأتمتة | Easily automated | Difficult to automate | Easily automated |
Initial Investment | Low to Medium | Low | متوسطة إلى عالية |
Space Requirement | معتدل | Low | Moderate to High |
Noise Level | معتدل | Low | عالية |
الصيانة | Low to Moderate | Low | معتدل |
تعدد الاستخدامات | Good, works on various materials and shapes | High, can handle complex shapes and hard-to-reach areas | Good, but may not be ideal for very complex shapes |
Skill Requirement | Low to Moderate | High, requires skilled operators | Low to Moderate |
السلامة | Generally safe, enclosed process | Risk of injury from sharp tools and burrs | Generally safe, but can be noisy |
Environmental | Can be environmentally friendly with proper compound selection | الحد الأدنى من التأثير البيئي | Can generate noise and dust, requires proper disposal |
Manual deburring, while precise, is labor-intensive and time-consuming, making it impractical for large-scale production. Vibratory finishing is faster but may not be suitable for very delicate parts. Abrasive flow machining is ideal for internal passages but requires expensive equipment.
As a full-service manufacturing partner, we offer a range of deburring services, including barrel finishing, to meet the diverse needs of our clients. Our expertise spans across various industries, including السيارات, where we provide precision deburring for engine components and other critical parts.
Barrel finishing finds applications in a wide range of industries, including:
As a manufacturing service provider, we cater to a diverse clientele across these industries. Our state-of-the-art barrel finishing facilities and experienced team enable us to deliver high-quality results for even the most demanding applications.
Determining the cost-effectiveness of barrel finishing involves considering several factors, including:
The research suggests that barrel finishing can lead to cost savings of up to 20-30% in some cases. As a cost-conscious manufacturing partner, we work closely with our clients to optimize their processes and achieve maximum cost-effectiveness.
The field of deburring and barrel finishing is continuously evolving, driven by advancements in technology and the increasing demands of various industries. Some of the key trends include:
As an innovative manufacturing company, we are committed to staying at the forefront of these trends. Our R&D team continuously explores new technologies and processes to improve our services and deliver cutting-edge solutions to our clients.
What if my parts are too large for traditional barrel finishing?
While barrel finishing is ideal for small to medium-sized parts, we also offer alternative deburring solutions for larger components, such as vibratory finishing or robotic deburring.
How long does the barrel finishing process typically take?
The processing time varies depending on factors like material, part size, and desired finish. It can range from a few minutes to several hours. Based on the study’s findings, complete burr removal might take up to 480 minutes for some materials. We can provide a more accurate estimate after evaluating your specific requirements.
Can barrel finishing damage delicate parts?
When done correctly, barrel finishing is suitable for delicate parts. We carefully select the media, compound, and process parameters to ensure gentle yet effective deburring. The research highlights that the minimal cutting forces in barrel finishing make it safe for thin and delicate components.
Is barrel finishing suitable for all types of metals?
Barrel finishing works well with various metals, including steel, aluminum, brass, and more. We have experience with diverse materials and can tailor the process accordingly.
Does barrel finishing affect the dimensional tolerances of parts?
Properly controlled barrel finishing has a minimal impact on dimensions. It primarily removes burrs and improves surface finish without significantly altering part geometry. The study notes that barrel finishing can improve dimensional alterations and deformations, especially in thin sheets.
What kind of surface finish can I expect from barrel finishing?
Barrel finishing can achieve a range of finishes, from matte to highly polished, depending on the media, compound, and processing time. We’ll work with you to achieve your desired aesthetic and functional requirements.
العنوان
رقم 30، متنزه هونغبانغ الصناعي، شينزين
البريد الإلكتروني
[email protected]
الهاتف
+86 15586668226
احصل على أحدث الاتجاهات والحقائق حول التصنيع باستخدام الحاسب الآلي من مدونتنا.
شركة Shenzhen Runkey Precision Technology Co. Ltd، وهي شركة تابعة لمجموعة Tensun Group، هي الحل الشامل الموثوق به للتصنيع المخصص بدءًا من النماذج الأولية وحتى الإنتاج، حيث إنها تحول فكرتك إلى واقع ملموس من خلال موارد التصنيع الرقمية، والعمليات المبسطة، وتوجيهات الخبراء، والجداول الزمنية المتسارعة، والجودة التي لا تقبل المساومة.
©2024. التصنيع باستخدام الحاسب الآلي جميع الحقوق محفوظة.