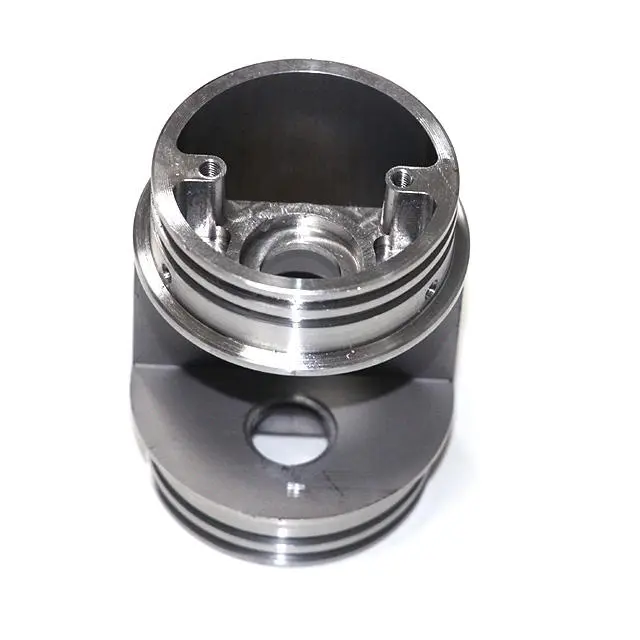
- +8615586668226
- [email protected]
- رقم 30، حديقة هونغبانغ الصناعية، شينزين
Sheet metal forming is a manufacturing process that involves shaping metal sheets into desired forms using various techniques like stretching, bending, and cutting. This process is crucial because it allows for the creation of a wide range of products, from car bodies to aircraft parts, with high precision and efficiency. As a التصنيع الآلي باستخدام الحاسب الآلي service provider specializing in product manufacturing, we understand that sheet metal forming is the backbone of many industries, and mastering its intricacies is essential for delivering top-quality components.
Sheet metal forming offers several advantages. First, it enables the production of lightweight yet strong parts. Second, it allows for complex shapes and designs. Third, it’s a cost-effective solution for mass production. The versatility of sheet metal forming makes it indispensable in today’s manufacturing landscape, where precision and durability are paramount. We see sheet metal forming used almost everywhere, and the demand is ever-growing. That’s why we, as a حلول CNC factory, invest heavily in understanding and perfecting these techniques.
Deep drawing is a sheet metal forming process where a sheet metal blank is radially drawn into a forming die by the mechanical action of a punch. It’s like magic, transforming a flat sheet into a cup-shaped, box-shaped, or other complex-shaped part. This process is particularly useful for creating seamless, hollow parts with excellent strength and precision, which is why it’s a favorite in industries like automotive and المنتجات الاستهلاكية. As experts in خدمات التصنيع الآلي, we often recommend deep drawing for components that require high structural integrity and a flawless finish.
Deep drawing isn’t just about shaping metal; it’s about doing so with unparalleled accuracy and consistency. This process allows for the creation of parts with uniform wall thickness and intricate details. Moreover, deep drawing can be highly automated, making it ideal for large-scale production. The ability to produce high-quality parts at high speeds makes deep drawing a game-changer in the manufacturing world. Want to know a secret? Our factory uses state-of-the-art deep drawing techniques to create components that exceed industry standards, ensuring our clients get the best possible products.
What are the key factors that determine the success of a deep drawing operation? Well, several critical parameters come into play. These include punch nose radius, die shoulder radius, blank holding force, friction, and material properties. Each of these parameters plays a crucial role in ensuring a successful outcome. Let’s break it down: the punch nose radius affects the metal flow, the die shoulder radius impacts the drawing ratio, the blank holding force prevents wrinkling, friction influences the drawing force, and the material properties determine the formability of the sheet. Sounds a bit complicated, right?
But here’s the good news. By carefully controlling these parameters, manufacturers can optimize the deep drawing process to achieve the desired shape and quality. For instance, a larger die shoulder radius reduces the risk of tearing, while an optimal blank holding force ensures a smooth, defect-free surface. As a dedicated التصنيع باستخدام الحاسب الآلي الرقمي service, we meticulously fine-tune these parameters for each project, ensuring optimal results.
المعلمة | Impact on Deep Drawing |
---|---|
Punch Nose Radius | Affects metal flow and drawing ratio |
Die Shoulder Radius | Influences drawing ratio and risk of tearing |
Blank Holding Force | Prevents wrinkling and ensures smooth surface |
الاحتكاك | Impacts drawing force and surface quality |
خواص المواد | Determines formability and overall success of the operation |
Bending, as the name suggests, involves shaping metal around a straight axis. Think of it as folding a piece of paper, but with metal. This process is fundamental in creating parts with angles and curves, such as brackets, enclosures, and panels. Bending is widely used across various industries, from construction to الطيران والفضاء, due to its simplicity and effectiveness.
But there’s more to bending than meets the eye. The process can be categorized into V-bending, U-bending, and wipe bending, each with its unique applications and advantages. Modern bending techniques, such as air bending and bottoming, offer enhanced precision and control, allowing for tighter tolerances and more complex geometries. This is particularly important in industries like electronics and medical devices, where even the smallest deviation can impact product performance. As a forward-thinking CNC manufacturing service, we’re constantly exploring and implementing the latest bending innovations to meet the evolving needs of our clients.
Have you ever wondered why a bent metal piece might slightly return to its original shape after being bent? That’s called springback, and it’s a common phenomenon in bending processes. Springback occurs because of the elastic recovery of the material after the bending force is removed. Several factors influence springback, including material properties, sheet thickness, bend radius, die opening, and punch velocity. Did you ever think that bending metal could be so complex?
Understanding and predicting springback is crucial for achieving accurate bending results. For example, a higher yield strength material tends to exhibit more springback. Similarly, a smaller bend radius can lead to increased springback. By considering these factors, manufacturers can compensate for springback and achieve the desired final shape. Techniques like overbending and using specialized tooling can help minimize springback. At our factory, we use advanced simulation software to predict and account for springback, ensuring that the final product meets the exact specifications.
Blanking and punching are like the cutting heroes of the sheet metal world. Blanking involves cutting out a piece of sheet metal, which becomes the workpiece, while punching creates holes in the sheet. These processes are essential for creating parts with precise outlines and features, such as washers, brackets, and electronic enclosures.
These processes might seem straightforward, but they require a high level of precision. The accuracy of blanking and punching operations directly impacts the quality and functionality of the final product. Factors like tool clearance, material properties, and punch velocity play a significant role in determining the outcome. For instance, proper tool clearance ensures clean cuts and minimizes burr formation, while optimal punch velocity enhances cutting efficiency and reduces tool wear. As a leading product manufacturing factory, we pay meticulous attention to these details to deliver components that meet the highest standards of precision.
Clearance, in the context of blanking, refers to the space between the punch and the die. It’s a small detail, but it has a huge impact on the quality of the blanked part. Proper clearance ensures clean, accurate cuts, while incorrect clearance can lead to problems like excessive burr, distortion, or even tool damage.
So, how do we determine the optimal clearance? It depends on factors like material type, thickness, and the desired quality of the cut edge. Generally, a smaller clearance is used for thinner materials and when a smoother edge is required. However, too small a clearance can increase the cutting force and accelerate tool wear. Finding the sweet spot requires expertise and experience. Our team of skilled engineers uses advanced software and their extensive knowledge to calculate the perfect clearance for each project, ensuring optimal results every time.
Stretch forming is a fascinating process that involves stretching a sheet of metal over a die or form block to create large, contoured parts. It’s like pulling a piece of fabric over a mold, but with metal! This technique is particularly useful for producing parts with smooth, gentle curves, such as aircraft fuselage sections, automotive body panels, and architectural elements.
The beauty of stretch forming lies in its ability to create complex shapes with minimal thinning and wrinkling. By controlling the stretching force and direction, manufacturers can achieve precise contours and maintain uniform thickness across the part. Stretch forming also allows for the use of larger sheet sizes, reducing the need for welding or joining multiple pieces. This not only enhances the structural integrity of the part but also improves its aesthetic appeal. As a company committed to pushing the boundaries of manufacturing, we find stretch forming to be an invaluable tool for creating innovative and high-quality products.
What makes for a perfect stretch forming operation? Several critical parameters come into play, including punch radius, sheet thickness, punch travel, friction, and material properties. Each of these factors significantly influences the outcome of the process. Let’s look closer: the punch radius determines the curvature of the part, the sheet thickness affects the formability, the punch travel dictates the extent of stretching, friction impacts the material flow, and the material properties define the stretchability of the sheet.
Optimizing these parameters is key to achieving flawless stretch forming results. For instance, a larger punch radius creates gentler curves, while a smaller radius allows for tighter bends. Adequate lubrication helps reduce friction, ensuring smooth material flow and preventing tearing. By carefully balancing these factors, manufacturers can create complex shapes with high precision and minimal defects. At our state-of-the-art facility, we leverage our deep understanding of these parameters to deliver stretch-formed parts that meet the most demanding specifications.
Finite Element Analysis (FEA) is a powerful computational tool that’s revolutionizing the way we approach sheet metal forming. By simulating the forming process, FEA allows engineers to predict how a material will behave under various conditions. This helps in identifying potential issues like wrinkling, tearing, or springback before they occur in the actual production.
FEA isn’t just about problem-solving; it’s also about optimization. By analyzing different parameters and scenarios, engineers can fine-tune the forming process to achieve the best possible results. This can lead to significant improvements in product quality, reduced material waste, and shorter lead times. As a company that embraces cutting-edge technology, we use FEA extensively in our design and manufacturing processes. This enables us to deliver superior products while optimizing efficiency and cost-effectiveness.
Advanced sheet metal forming techniques have far-reaching implications across a multitude of industries. Here are some sectors that particularly benefit from these processes:
These are just a few examples. In reality, any industry that requires precision metal components can benefit from advanced sheet metal forming techniques.
What is the difference between deep drawing and stretch forming?
Deep drawing involves forming a flat sheet into a hollow shape using a punch and die, while stretch forming stretches a sheet over a form block to create contoured shapes.
How do you prevent wrinkling in deep drawing?
Wrinkling can be prevented by optimizing the blank holding force, using appropriate lubrication, and ensuring proper die and punch design.
What is springback, and how can it be minimized?
Springback is the elastic recovery of material after bending, causing a slight change in shape. It can be minimized by overbending, using specialized tooling, or employing techniques like stretch bending.
Why is clearance important in blanking operations?
Proper clearance ensures clean cuts, minimizes burr formation, and reduces tool wear in blanking operations.
Can sheet metal forming be used for prototyping?
Yes, sheet metal forming techniques like stretch forming and bending are often used for creating prototypes and custom parts. Check out our النماذج الأولية السريعة service for more information.
What materials are commonly used in sheet metal forming?
Common materials include steel, aluminum, copper, and various alloys, each with different properties suited for specific applications.
By mastering the intricacies of sheet metal forming, manufacturers can unlock new levels of precision, efficiency, and innovation. As a leading CNC manufacturing service provider, we are committed to leveraging these advanced techniques to deliver superior products that meet the evolving needs of our clients across various industries. Contact us today to explore how our expertise in sheet metal forming can benefit your next project.
العنوان
رقم 30، متنزه هونغبانغ الصناعي، شينزين
البريد الإلكتروني
[email protected]
الهاتف
+86 15586668226
احصل على أحدث الاتجاهات والحقائق حول التصنيع باستخدام الحاسب الآلي من مدونتنا.
شركة Shenzhen Runkey Precision Technology Co. Ltd، وهي شركة تابعة لمجموعة Tensun Group، هي الحل الشامل الموثوق به للتصنيع المخصص بدءًا من النماذج الأولية وحتى الإنتاج، حيث إنها تحول فكرتك إلى واقع ملموس من خلال موارد التصنيع الرقمية، والعمليات المبسطة، وتوجيهات الخبراء، والجداول الزمنية المتسارعة، والجودة التي لا تقبل المساومة.
©2024. التصنيع باستخدام الحاسب الآلي جميع الحقوق محفوظة.