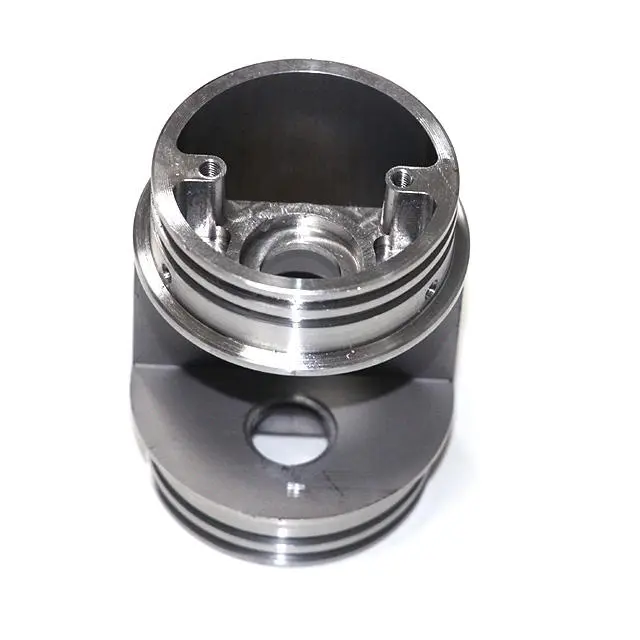
- +8615586668226
- [email protected]
- Nr. 30, Hongbang-Industriepark, Shenzhen
Da keine freiliegenden Verbindungselemente mehr erforderlich sind, verbessern diese Verbindungen die Ästhetik der Produkte und verringern gleichzeitig die Produktionszeit und -kosten. Damit sind sie ideal für eine Reihe von Branchen, von der Unterhaltungselektronik über die Automobilindustrie bis hin zu medizinischen Geräten. In diesem Artikel gehen wir auf die verschiedenen Arten von Schnappverbindungen ein, erörtern ihre Anwendungen und zeigen die besten Verfahren für ihre Konstruktion auf, um eine optimale Leistung zu gewährleisten.
Eine Schnappverbindung ist ein mechanisches Verbindungselement, das für den Zusammenbau von Bauteilen durch Ineinandergreifen von Teilen verwendet wird. Der Mechanismus besteht in der Regel aus einem Vorsprung, z. B. einem Haken oder Bolzen, an einem Teil, der in eine entsprechende Aussparung an einem anderen Teil einrastet. Beim Zusammenbau biegt sich der Vorsprung und rastet in das Gegenstück ein. Je nach Konstruktion kann die Verbindung dauerhaft oder lösbar sein und bietet somit Flexibilität bei der Montage und Demontage.
Schnappverbindungen werden häufig in Kunststoffbauteilen verwendet, da das Material flexibel ist und große Verformungen ohne Beschädigung zulässt. Die Spannungskonzentration an den Verbindungen kann jedoch dazu führen, dass Kunststoffe im Laufe der Zeit kriechen, was zu einem möglichen Spannungsverlust führt. Um dies zu verhindern, werden häufig steife Fixierungselemente, wie z. B. Verschlüsse und Laschen, verwendet, um eine sichere Montage zu gewährleisten.
Freitragende Schnappverbindungen sind die gängigste Art von Schnappverschlüssen, die in der Regel eine einfache Trägerstruktur mit einem Haken an der Spitze aufweisen. Der Kragarm biegt sich beim Einrasten in das aufnehmende Teil, so dass der Haken wieder einrasten kann. Diese Verbindung kann entweder dauerhaft oder lösbar sein, je nach dem Konstruktionswinkel zwischen dem Haken und der Aussparung.
Einige Kragarmkonstruktionen enthalten U- oder L-förmige Träger, die die Länge des Kragarms verlängern und gleichzeitig den Platzbedarf minimieren. Diese Konfigurationen verringern die Durchbiegungskräfte und werden häufig für Kunststoffteile verwendet, um die Montage beim Spritzgießen zu erleichtern.
U-förmige Schnappverbindungen bestehen aus einem U-förmigen freitragenden Träger, der in eine Nut des Gegenstücks passt. Diese Konstruktion wird häufig in Anwendungen verwendet, die einen starken Halt erfordern, wie z. B. Elektronikgehäuse und Innenverkleidungen von Kraftfahrzeugen. U-förmige Gelenke können aus verschiedenen Materialien hergestellt werden, darunter Metall und Kunststoff, und sind daher in verschiedenen Branchen vielseitig einsetzbar.
Torsionsschnappgelenke funktionieren durch Verdrehen einer Stange, um eine trennbare Verbindung herzustellen. Ein Kipphebelmechanismus sorgt für die Auslenkungskraft und ermöglicht ein einfaches Öffnen und Schließen der Verbindung. Diese Gelenke sind äußerst langlebig und werden häufig für Anwendungen verwendet, die eine häufige Demontage erfordern.
Ringförmige Schnappverbindungen werden für kreisförmige oder elliptische Teile, wie z. B. Stiftkappen oder Dosendeckel, verwendet. Ein Steg auf dem einen Teil rastet in eine Nut auf dem anderen ein und schafft so eine sichere Verbindung. Das Design dieser Verbindungen kann so angepasst werden, dass sie je nach Anwendung entweder leicht zu entfernen oder dauerhaft zu montieren sind.
Um eine optimale Leistung bei Schnappverbindungen zu erzielen, müssen bestimmte Konstruktionsrichtlinien eingehalten werden:
Abrundung der Basis des Auslegers: Das Anbringen einer Ausrundung an der Basis des Auslegers verringert die Spannungskonzentration und stärkt die Verbindung. Der empfohlene Ausrundungsradius beträgt mindestens das 0,5-fache der Dicke der Kragarmbasis.
Verjüngung des Designs: Durch die Verjüngung des Querschnitts des Freiträgers wird die Belastung gleichmäßig verteilt, was den Materialverbrauch verringert und die Gesamtleistung verbessert.
Clip-Breite erhöhen: Breitere Klammern geben der Verbindung mehr Festigkeit. Eine Mindestbreite von 5 mm wird für die Stabilität empfohlen.
Laschen hinzufügen: Laschen verbessern die Ausrichtung und Scherkraftübertragung und verringern das Risiko einer Fehlausrichtung der Teile während der Montage.
Baurichtung berücksichtigen: Vermeiden Sie es, Schnappverbindungen zu konstruieren, die vertikal aufgebaut sind, da dies die Verbindung schwächt. Die Durchbiegung sollte nur während der Montage auftreten.
Der Prozess der Herstellung von Druckknöpfen umfasst mehrere wichtige Schritte:
Gestaltung: Beginnen Sie mit der Erstellung eines detaillierten Entwurfs mithilfe einer Software. Prototypen können durch 3D-Druck oder CNC-Bearbeitung hergestellt werden, um das Design zu validieren.
Auswahl des Materials: Je nach Anwendung können Druckknöpfe aus Metall (z. B. Messing oder Edelstahl) oder Kunststoff (z. B. Polycarbonat oder Nylon) hergestellt werden.
Stanzen oder Gießen: Metallverschlüsse werden in der Regel im Stanzverfahren hergestellt, während Kunststoffverschlüsse im Spritzgussverfahren gefertigt werden.
Beschichtung: Eine korrosionsbeständige Beschichtung kann aufgebracht werden, um die Haltbarkeit und Festigkeit des Befestigungselements zu erhöhen.
Qualitätsprüfung: Es werden Inspektionstests durchgeführt, um sicherzustellen, dass die Verbindungselemente richtig sitzen und wie vorgesehen funktionieren.
Profis:
Nachteile:
Schnappverbindungen sind eine vielseitige und kostengünstige Lösung für den Zusammenbau einer Vielzahl von Komponenten, insbesondere von Kunststoff- und Metallteilen. Wenn sie richtig konzipiert und umgesetzt werden, verbessern sie die Effizienz der Montage, senken die Produktionskosten und bieten Flexibilität beim Produktdesign. Durch Befolgung bewährter Konstruktionsverfahren und Berücksichtigung der Materialauswahl, Hersteller können langlebige und leistungsstarke Schnappverbindungen gewährleisten. Ob Sie an Prototypen oder Großserien arbeiten, Schnappverbindungen bieten eine praktische, ästhetische und effiziente Befestigungslösung für moderne Produkte.
In unserem Blog finden Sie die neuesten Trends und Fakten zur CNC-Fertigung.
Shenzhen Runkey Precision Technology Co. Ltd, eine Tochtergesellschaft der Tensun-Gruppe, ist Ihre vertrauenswürdige Komplettlösung für kundenspezifische Fertigung vom Prototyping bis zur Produktion. Wir setzen Ihre Idee mit digitalen Fertigungsressourcen, optimierten Prozessen, fachkundiger Anleitung, beschleunigten Fristen und kompromissloser Qualität in die Realität um.
©2024. CNC Fabrication Alle Rechte vorbehalten.