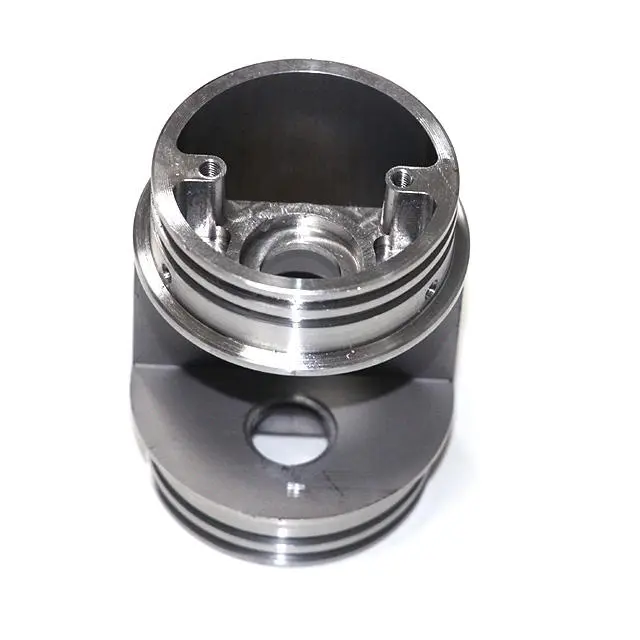
- +8615586668226
- [email protected]
- Nº 30, Hongbang Industrial Park, Shenzhen
Digital Light Processing (DLP) is a powerful 3D printing technology that utilizes a light source to cure a photopolymer resin layer by layer, creating a three-dimensional object. As a type of fabricación de chapa metálica, the process begins with a digital design file, which is sliced into thin layers. A projector then projects the image of each layer onto the surface of the liquid resin, causing it to solidify. The build platform then moves, allowing the next layer to be cured on top of the previous one. This process continues until the entire object is built.
DLP offers several advantages over other 3D printing methods, including high resolution, fast printing speeds, and the ability to create complex geometries. DLP 3D printing is capable of printing objects at high resolution at a high speed. For example, the study mentioned using a projector intensity of ~18 mW/cm², and the exposure time of each layer was 4 seconds. This is especially beneficial for industries like aerospace, automotive, and medical devices, where precision and intricate designs are paramount. Our factory utilizes state-of-the-art DLP technology to deliver parts with exceptional accuracy and detail.
Cellulose nanocrystals (CNCs) are derived from natural sources, such as wood pulp, and possess remarkable properties, including high strength, high Young’s modulus, biocompatibility, and renewability. Think of them as tiny, incredibly strong fibers that can be used to reinforce other materials. These properties make them ideal as a reinforcement phase in polymer composites, significantly enhancing the performance of the final product.
The incorporation of CNCs into composite materials offers numerous benefits. For instance, they can dramatically improve the strength and stiffness of the material while maintaining a lightweight profile. CNCs are highly crystalline cellulose nanoparticles, which have a diameter of 5 to 50 nm and a length of 100 to 1000 nm. The high axial elastic modulus of 110 to 220 GPa exceeds the modulus of glass, Kevlar, and some metal fibers. This is particularly valuable in industries such as aerospace and automotive, where weight reduction is critical for fuel efficiency and performance. As a company specializing in Mecanizado CNC, we recognize the immense potential of CNCs in creating high-performance parts. The use of CNCs also aligns with the growing demand for sustainable and eco-friendly manufacturing processes.
The addition of CNCs to photopolymer resins used in DLP 3D printing leads to significant improvements in the mechanical properties of the printed parts. Research has shown that CNC incorporation can increase the Young’s modulus, ultimate strength, and overall durability of the composite material. CNCs act as reinforcing agents, similar to how steel bars reinforce concrete, enhancing the structural integrity of the printed object.
In the study presented in the PDF, the addition of CNCs resulted in a continuous increase in the average Young’s modulus as the concentration of CNCs increased. The average ultimate strength displayed a peak value of 7.6 ± 0.3 MPa at 1 wt% CNC concentration. For example, the study demonstrated a significant increase in average modulus from 52.8 ± 1.4 MPa to 133.0 ± 4.0 MPa with the addition of CNCs. This means that parts printed with CNC-reinforced resins can withstand greater loads and stresses, making them suitable for demanding applications in industries such as equipamiento industrial y aeroespacial. Our expertise in materials science allows us to optimize CNC incorporation for your specific application.
One of the challenges in using CNCs in 3D printing is ensuring their compatibility with the photopolymer resin. CNCs are naturally hydrophilic, meaning they are attracted to water, while many photopolymer resins are hydrophobic. This difference in properties can lead to poor dispersion of CNCs within the resin, resulting in weak and inconsistent material properties. It’s like trying to mix oil and water – they just don’t blend well.
To overcome this challenge, researchers have explored the use of 1,3-diglycerolate diacrylate (DiGlyDA) as a compatibilizer. DiGlyDA has a similar chemical structure to PEGDA but also has hydroxyl groups, making it more compatible with CNCs. By blending DiGlyDA with PEGDA, the compatibility between CNCs and the resin is improved, allowing for better dispersion and stronger bonding. The study found that a 1:1 PEGDA to DiGlyDA ratio provided maximum CNC compatibility. At our manufacturing facility, we leverage this knowledge to formulate custom resin blends that maximize the benefits of CNC reinforcement.
The mechanical properties of 3D printed CNC composites can be tailored by adjusting various parameters during the printing process. One of the key parameters is the concentration of CNCs in the resin. As mentioned earlier, increasing the CNC concentration generally leads to an increase in the Young’s modulus of the material. However, there is an optimal concentration beyond which the properties may start to degrade due to agglomeration of CNCs.
CNC Concentration (wt%) | Young’s Modulus (MPa) | Ultimate Strength (MPa) |
---|---|---|
0 | 52.8 ± 1.4 | 6.5 ± 0.5 |
0.2 | 60.2 ± 2.1 | 7.1 ± 0.4 |
0.5 | 85.5 ± 3.8 | 7.4 ± 0.3 |
1 | 133.0 ± 4.0 | 7.6 ± 0.3 |
2 | 165.7 ± 5.2 | 6.8 ± 0.6 |
5 | 188.3 ± 6.9 | 5.9 ± 0.7 |
Another important parameter is the curing layer thickness. The study found that the Young’s modulus could be tuned from 80.7 ± 3.7 MPa to 54.4 ± 7.5 MPa as the curing layer thickness increased from 25 µm to 300 µm. By varying the thickness of each cured layer during the DLP process, we can influence the density of crosslinking within the material, thereby affecting its stiffness and strength. This level of control allows us to fine-tune the properties of the printed parts to meet the specific requirements of different applications. For instance, a thicker layer might be suitable for parts requiring greater flexibility, while a thinner layer might be preferred for parts needing higher rigidity.
The unique properties of DLP 3D printed CNC composites make them suitable for a wide range of applications across various industries. In the industria aeroespacial, these materials can be used to create lightweight yet strong components for aircraft and spacecraft, contributing to fuel efficiency and improved performance. For example, complex lattice structures with high strength-to-weight ratios can be fabricated for use in aircraft interiors or structural components.
En el industria del automóvil, CNC composites can be employed to manufacture lightweight parts that enhance fuel economy and reduce emissions. The high strength and durability of these materials also make them ideal for use in high-performance vehicles. The ability to create custom parts on demand is particularly valuable for prototyping and low-volume production runs. The dispositivo médico industry can also benefit from this technology, using it to create custom implants, prosthetics, and surgical tools with tailored properties.
Industria | Aplicación | Beneficio |
---|---|---|
Aeroespacial | Lightweight structural components | Fuel efficiency, improved performance |
Automoción | Lightweight parts, high-performance components | Fuel economy, reduced emissions, enhanced performance |
Productos sanitarios | Custom implants, prosthetics, surgical tools | Tailored properties, biocompatibility, improved patient outcomes |
Productos de consumo | Durable, lightweight, customizable products | Enhanced functionality, aesthetics, and sustainability |
Electrónica | Housings, connectors, structural components | Miniaturization, improved performance, thermal management |
Robótica | Lightweight, high-strength components | Enhanced agility, payload capacity, and energy efficiency |
Energía | Components for wind turbines, solar panels | Improved efficiency, durability, and sustainability |
Defensa y Militar | Lightweight armor, unmanned vehicles | Enhanced protection, mobility, and operational effectiveness |
Construcción | Architectural models, custom building parts | Design freedom, faster construction, improved structural performance |
Tools and Molds | High-performance tooling, custom molds | Increased durability, precision, and efficiency |
The thickness of each cured layer in the DLP 3D printing process has a significant impact on the mechanical properties of the final composite part. As mentioned before, thicker layers tend to have a lower degree of cure compared to thinner layers due to light attenuation. In simpler terms, the light doesn’t penetrate as deeply into thicker layers, resulting in a weaker structure. It’s like baking a cake – if the layer is too thick, the center might not cook properly.
This phenomenon can be leveraged to tune the properties of the printed part. For example, if a part requires greater flexibility, a thicker curing layer can be used. Conversely, if higher stiffness and strength are desired, a thinner curing layer is preferred. The study demonstrated that by varying the curing layer thickness from 25 µm to 300 µm, the Young’s modulus of the composite could be adjusted. This level of control is invaluable for optimizing parts for specific applications. This flexibility in design is one of the core strengths of our Soluciones CNC.
The water swelling behavior of CNC composites is an important consideration, particularly for applications where the part may be exposed to moisture. CNCs are hydrophilic, meaning they tend to absorb water. This can lead to swelling of the composite material, which may affect its dimensional stability and mechanical properties. However, the degree of swelling can be controlled by adjusting the CNC concentration and the curing layer thickness.
The research showed that increasing the CNC concentration led to an increase in the mass swelling ratio. It was also observed that the final water mass infiltration behavior for thin films printed with 100 µm curing layer thickness was similar to that printed with 25 µm. This means that parts with higher CNC content are likely to absorb more water. Additionally, thicker curing layers tend to exhibit greater water swelling due to the lower degree of cure. This is because a less cured material has more free volume for water to penetrate. By carefully balancing these parameters, we can tailor the water swelling behavior of the composite to suit the intended application.
While DLP 3D printing of CNC composites offers immense potential, there are still challenges that need to be addressed. One of the main challenges is achieving uniform dispersion of CNCs within the photopolymer resin, particularly at higher concentrations. Agglomeration of CNCs can lead to weak points in the material, compromising its mechanical properties.
Future research will likely focus on developing new compatibilizers and surface modification techniques to improve CNC dispersion. Additionally, optimizing the printing parameters, such as light intensity, exposure time, and resin formulation, will be crucial for maximizing the performance of CNC composites. Further exploration of new applications and the development of industry-specific standards will also be important for the widespread adoption of this technology. The results indicated that both the hydrophilicity of CNCs and the light attenuation effect from curing layer thickness can be utilized to control the final swelling behavior of the composites.
Como líder Fabricación CNC and product manufacturing factory, we are committed to staying at the forefront of technological advancements. We offer a comprehensive range of CNC manufacturing services, including milling, turning, 5-axis machining, and more. Our expertise in DLP 3D printing, combined with our deep understanding of materials science, allows us to help you harness the power of CNC composites for your specific needs. Our expertise extends to various specialized processes like Mecanizado CNC de 5 ejes, which allows for the creation of highly complex and intricate parts that are impossible to produce with traditional methods.
Whether you require rapid prototyping, on-demand manufacturing, or surface finishing, we have the capabilities and experience to deliver high-quality parts that meet your exact specifications. We work closely with our clients to understand their unique requirements and develop customized solutions that optimize performance, cost, and sustainability. Our team of skilled engineers and technicians utilizes state-of-the-art equipment and software to ensure precision, accuracy, and repeatability in every project.
How does DLP 3D printing work?
DLP 3D printing uses a light source to cure a liquid resin layer by layer, building up a 3D object based on a digital design.
What are the advantages of using CNCs in composite materials?
CNCs enhance the strength, stiffness, and durability of composite materials while also being lightweight and sustainable.
Can the mechanical properties of 3D printed CNC composites be adjusted?
Yes, the properties can be tuned by varying the CNC concentration and the curing layer thickness during the printing process.
What industries can benefit from DLP 3D printed CNC composites?
Aerospace, automotive, medical devices, consumer products, and many other industries can leverage this technology for various applications.
What role does DiGlyDA play in CNC composites?
DiGlyDA acts as a compatibilizer, improving the dispersion and bonding of CNCs within the photopolymer resin.
Is water swelling a concern for CNC composites?
Yes, but the swelling behavior can be controlled by adjusting the CNC concentration and curing layer thickness.
By partnering with us, you can unlock the full potential of this cutting-edge technology and gain a competitive edge in your industry. Let us help you bring your most innovative ideas to life with our expertise in CNC manufacturing and DLP 3D printing.
Dirección
No.30, Hongbang Industry Park, Shenzhen
Correo electrónico
[email protected]
Teléfono
+86 15586668226
Conozca las últimas tendencias y datos sobre fabricación CNC en nuestro blog.
Shenzhen Runkey Precision Technology Co. Ltd, una filial del Grupo Tensun, es su solución integral de confianza para la fabricación personalizada de prototipos para la producción.la transformación de su idea en realidad con los recursos de fabricación digital, procesos simplificados, orientación de expertos, plazos acelerados, y la calidad sin concesiones.
©2024. CNC Fabrication Todos los derechos reservados.