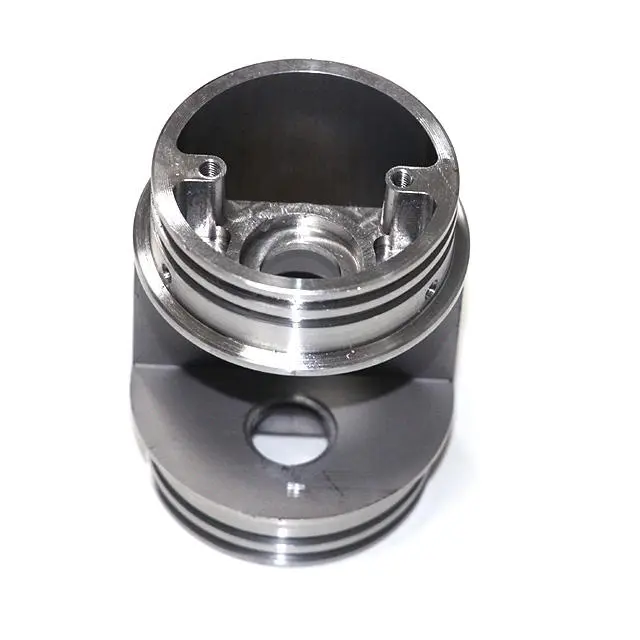
- +8615586668226
- [email protected]
- No. 30, Hongbang Industrial Park, Shenzhen
The size of the part being machined plays a pivotal role in determining the feasibility, cost, and quality of the final product. Larger parts may exceed a machine’s work envelope, requiring multiple setups or specialized equipment. Conversely, smaller parts can pose challenges in securing and machining accurately, especially when tight tolerances are required.
The work envelope defines the maximum dimensions (length, width, height) a CNC machine can handle. For instance, a standard CNC milling machine might have a work envelope of 40 x 20 x 20 inches. If your part exceeds these limits, repositioning or using a larger machine becomes necessary.
Deep cavities or intricate geometries can challenge tool accessibility. Longer tools risk deflection, which compromises accuracy. For example, machining a cavity deeper than 3-4 times the tool’s diameter often leads to poor surface finishes.
CNC machines vary by axis configurations:
Highly complex parts with intricate features may need to be divided into smaller sections for machining. This approach allows for greater flexibility in part size but introduces challenges in assembly and alignment.
Larger parts consume more material, but inefficient designs can lead to excessive scrap. For example, intricate designs with large cavities generate significant waste, driving up costs.
Tööstus | Peamised nõuded | Common Challenges |
---|---|---|
Lennundus | High precision, lightweight materials | Managing thermal expansion |
Autotööstus | Durability, tight tolerances | Machining complex geometries |
Meditsiiniseadmed | Fine details, biocompatible materials | Achieving micro-machining tolerances |
What is the minimum wall thickness for CNC machining?
Typically, walls as thin as 0.030 inches can be reliably produced, depending on the material and machine capability.
How does thermal expansion affect CNC machining?
Materials like aluminum expand more than steel under heat, potentially altering part dimensions during machining.
Can CNC machines handle large parts?
Yes, but parts exceeding the machine’s work envelope may require multiple setups or specialized equipment.
What are the most common design issues in CNC machining?
Deep cavities, inadequate tool access, and thin walls are frequent challenges that can lead to inefficiencies or failed parts.
How do I reduce machining costs for small parts?
Standardize hole sizes, limit intricate features, and use materials with good machinability.
Understanding CNC machining size limitations is crucial for optimizing production outcomes. By balancing part size, complexity, and material properties, manufacturers can achieve high-quality results while minimizing costs.
For more insights, explore our resources on CNC-töötlemine, Täppismehaaniline töötlemineja 5-teljeline CNC-töötlus.
Tutvu meie blogi viimaste suundumuste ja faktidega CNC-valmistuse kohta.
Shenzhen Runkey Precision Technology Co. Ltd, mis on Tensun Groupi tütarettevõte, on teie usaldusväärne ühekordne lahendus kohandatud tootmisele prototüüpimisest kuni tootmiseni. teie idee muutmine tegelikkuseks digitaalsete tootmisressursside, sujuvate protsesside, ekspertide juhendamise, kiirendatud tähtaegade ja kompromissitu kvaliteedi abil.
©2024. CNC Fabrication Kõik õigused kaitstud.