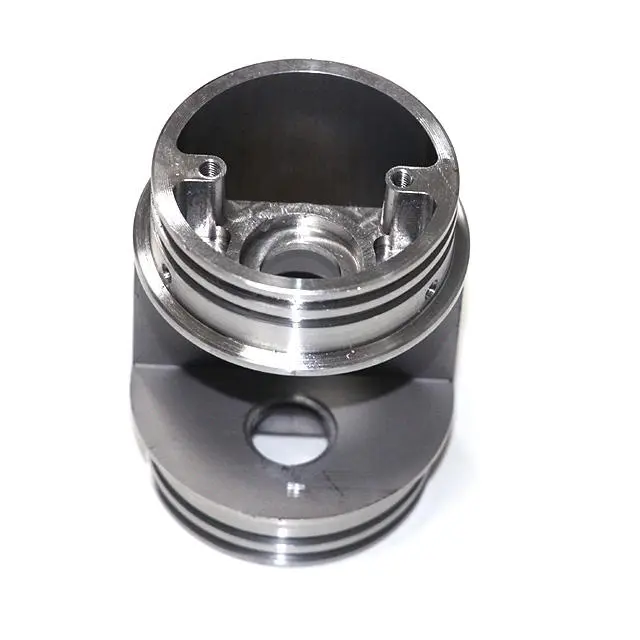
- +8615586668226
- [email protected]
- No. 30, Hongbang Industrial Park, Shenzhen
Métal stamping is a processus de fabrication that uses dies and stamping presses pour transformer flat metal sheets into specific shapes. This cold-forming process can create a variety of forms, including pièces embouties that are used in products we use every day. At its core, métal stamping lies in its ability to produce high-volume, precise, and complex parts efficiently. The sheet metal is placed between a die and a punch and the press applies force to shape the metal.
Le métal stamping process is versatile, allowing for operations like punching, blanking, flexion, coining, and embossing. Métal stamping can be used on many kinds of metal like aluminum, brass, copper, steel, and stainless steel. It is a versatile and efficient manufacturing process that can create a wide range of products, from small parts to large components. Different materials offer varied levels of strength, résistance à la corrosion, and formability, making material selection a crucial step in the métal stamping process. Our experience at CNC fabrication services spans across these materials, ensuring that we can offer tailored solutions for each client’s needs.
Choisir le bon type de métal est cruciale pour la réussite de la tôle stamping. The selection depends on the desired properties of the final product, such as strength, durability, and résistance à la corrosion. Commonly used materials include stainless steel, known for its durability and resistance to rust; aluminum, prized for its lightweight yet strong nature; and various grades of steel, offering a balance of strength and formability. Some applications require special materials like copper, titanium, brass, and nickel alloys.
Each material brings unique benefits to the métal stamping process. For example, stainless steel is often chosen for medical device applications due to its hygienic properties. Applications aérospatiales use titanium because it is strong and light. Understanding the specific requirements of your project—whether it’s high conductivity, resistance to extreme temperatures, or aesthetic appeal—will guide the material selection process. As experts in Services de fabrication CNC, we assist our clients in navigating these choices, ensuring optimal material selection for each project, which can be seen in our successful collaboration with a leading medical device manufacturer, where we used our usinage de précision expertise to produce high-quality stainless steel components.
Il existe plusieurs types of metal stamping processes. There are several different metal stamping techniques to choose from. The most common include estampage progressif, die stamping, compound die stampinget fourslide stamping. Estampage progressif involves feeding a bande métallique through a series of stations, each performing a specific operation until the final part is complete. This method is ideal for high-volume production of pièces complexes.
Fourslide stamping, on the other hand, uses four different slides to shape a piece of metal, allowing for intricate bends and shapes that might be difficult to achieve with other methods. Each metal stamping process provides different advantages and is chosen based on the complexity of the part and production requirements. Dessin en profondeur est un metal forming technique specifically used for creating deep, cup-like shapes, while estampage progressif is ideal for parts that require multiple operations in a sequential manner. With our in-depth knowledge of these processes, we, at CNC fabrication services, ensure that the chosen method aligns perfectly with the project’s specifications.
Tôle stamping offers numerous advantages in the manufacturing process. One of the primary benefits of sheet métal stamping is its cost-effectiveness, especially for large production runs. The métal stamping process has a short cycle time and can make many parts quickly. The automation involved also minimizes labor costs.
Another significant advantage is the precision and repeatability of the métal stamping process. Once the stamping dies are created, the process can produce identical parts with high accuracy. This consistency is essential in industries where precision is paramount, such as in the production of composants métalliques for electronics and automotive parts. We at CNC fabrication services leverage these benefits to provide our clients with high-quality, consistent products.
Le presse d'estampage est le cœur de la fabrication métallique process. It is a machine that applies force to a die, which in turn shapes the feuille de métal. Modern stamping presses are sophisticated machines capable of applying immense pressure with great precision. They can be mechanical, hydraulic, or servo-driven, each offering specific advantages in terms of speed, force, and control.
Le presse d'estampage is used to cut, punch, and shape métal sheets into desired forms. The precision and force applied by the presse d'estampage are essential for achieving the desired shape and quality of the final product. Selecting the right presse d'estampage for a specific task is critical to the success of the métal stamping project. Our team is adept at choosing the appropriate press, which is evident from our work with clients in the aérospatiale industry, where precise and reliable components are non-negotiable.
Le blanking process is a fundamental step in métal stamping where a portion of the tôleconnu sous le nom de vierge, is cut out from a larger sheet or coil. This vierge is then further processed to create the final pièce métallique. Les blanking process requires precision to ensure that the vierge is the correct size and shape for subsequent operations.
During blanking, the sheet metal is placed over a die, and a punch cuts out the desired shape. The blanking process can be combined with other stamping operations to create complex parts. For example, our expertise in Solutions CNC allows us to integrate blanking with other processes efficiently. The accuracy of the blanking process directly impacts the quality of the final product. Any error in this stage can lead to defects later.
Beyond the basic stamping operations, there are several advanced metal stamping techniques that cater to more complex and specialized needs. For example, dessin en profondeur is a technique used for creating deep, cup-shaped, or box-shaped parts by pulling a sheet metal blank into a die with a punch. Progressive stamping is used to make parts that need many steps in a row. It is a complex technique that involves feeding a bande métallique through a series of stations, each performing a different operation until the finished part is produced.
Other advanced techniques include coining, embossing, and fine blanking. Coining is used for flattening or compressing a métal part, while embossing creates raised or recessed designs on the métal surface. Fine blanking is used to create high-precision parts with smooth edges and tight tolerances. These advanced techniques enable us to handle complex projects, such as creating intricate components for the automobile industry, requiring precision and specialized forming.
Métal stamping is largement utilisé across various industries due to its versatility and efficiency. Common applications of metal stamping include the production of automotive parts, electronic enclosures, appliances, and hardware components. In the automotive industry, métal stamping is used to create body panels, brackets, and other structural components. Our métal stamping process is used to make parts for the electronics industry, including connectors, terminals, and cases.
The appliance industry also relies heavily on métal stamping for manufacturing parts such as housings, panels, and internal components. Additionally, métal stamping is used in the construction, aerospace, and medical industries for a wide range of applications spécifiques. The ability to produce parts with varying complexities, from simple brackets to intricate designs, makes métal stamping a preferred choice in many sectors.
Métal estampillage play a pivotal role in industries with stringent requirements for precision and reliability, such as aerospace and medical devices. In applications aérospatiales, métal stamping is used to create lightweight yet strong components that can withstand extreme conditions. These components include brackets, panels, and structural parts that must meet rigorous safety and performance standards.
Dans le cadre de la medical device applications, métal stamping is used to manufacture a variety of instruments, implants, and equipment. The materials used in medical stamping, such as stainless steel and titanium, must be biocompatible and offer résistance à la corrosion. Métal stamping can make parts with precise shapes and tolerances that are important for the function and safety of medical devices. For example, our services de fabrication have been instrumental in producing components for surgical instruments, demonstrating our commitment to quality and precision in this critical field.
L'avenir de la métal stamping looks promising, with ongoing advancements in technology and materials. Innovations in presse d'estampage design, such as servo-driven presses, offer greater control and efficiency, allowing for more complex and precise stamping operations. The integration of automation and robotics further enhances the speed and accuracy of the métal stamping process.
Moreover, the development of new materials, including high-strength alloys and composites, expands the possibilities for métal estampillage applications. These materials offer improved properties, such as higher strength-to-weight ratios and enhanced résistance à la corrosion, making them ideal for demanding applications in industries like aerospace and automotive. As a forward-thinking company, we continuously invest in these advancements to offer cutting-edge services d'usinage and stay ahead of industry trends.
What is metal stamping and how does it work?
Métal stamping is a processus de fabrication that uses dies and stamping presses à form metal sheets into specific shapes. The sheet metal is placed between a die and a punch, and the press applies force to shape the metal. This process can include various operations like punching, blanking, bending, and embossing to create the desired métal part.
What are the different types of metal stamping?
Il existe plusieurs types of stamping les processus, y compris estampage progressif, transfer die stamping, fourslide stamping, and deep drawing. Estampage progressif involves feeding a bande métallique through multiple stations, each performing a specific operation. Transfer die stamping uses multiple dies to form the part, while fourslide stamping utilizes four slides to create complex shapes. Dessin en profondeur is used to form deep, cup-like shapes by drawing a metal blank into a die.
What materials are commonly used in metal stamping?
Common materials used in metal stamping include stainless steel, aluminum, copper, brass, and various grades of steel. The choice of material depends on the desired properties of the final product, such as strength, durability, and résistance à la corrosion. Specialized materials like titanium and nickel alloys are also used for specific applications requiring unique properties.
What are the benefits of using metal stamping for manufacturing?
Métal stamping offers several benefits, including cost-effectiveness, high precision, and repeatability. The process is highly automated, reducing labor costs and production time. Once the dies are created, métal stamping can produce identical parts with high accuracy, making it ideal for high-volume production. Additionally, métal stamping is versatile and can be used to create a wide range of parts with varying complexities.
How does metal stamping contribute to the aerospace and medical industries?
In the aerospace industry, métal stamping is used to create lightweight, high-strength components such as brackets, panels, and structural parts that can withstand extreme conditions. In the medical industry, métal stamping is used to manufacture instruments, implants, and equipment that require precision, biocompatibility, and résistance à la corrosion. Materials like stainless steel and titanium are commonly used in medical device applications to ensure safety and reliability.
What innovations are shaping the future of metal stamping?
L'avenir de la métal stamping is being shaped by innovations in presse d'estampage technology, such as servo-driven presses, which offer greater control and efficiency. Automation and robotics are also enhancing the speed and accuracy of the métal stamping process. Additionally, the development of new materials, including high-strength alloys and composites, is expanding the possibilities for métal estampillage applications in various industries.
Voici les points les plus importants à retenir métal stamping:
Métal stamping is a versatile and efficient processus de fabrication used across numerous industries.
The process involves using dies and stamping presses to shape flat metal sheets into specific forms.
Communs types of metal stamping inclure estampage progressif, transfer die stamping, fourslide stampinget dessin en profondeur.
Materials commonly used in metal stamping include stainless steel, aluminum, copper, brass, and various grades of steel.
Métal stamping offers benefits such as cost-effectiveness, high precision, and repeatability.
Le blanking process is a crucial step in métal stamping where a portion of the tôle is cut out to form the vierge for further processing.
Avancé metal stamping techniques like coining, embossing, and fine blanking cater to complex and specialized needs.
Métal stamping is used in various applications, including automotive parts, electronic enclosures, appliances, and medical devices.
Innovations en matière de presse d'estampage technology, automation, and new materials are shaping the future of métal stamping.
Choisir le bon type de métal et processus d'estampage is essential for achieving the desired quality and efficiency in métal stamping projects.
By understanding these key points, you can appreciate the significance of métal stamping in modern manufacturing and its potential for future advancements. As industry leaders, we are committed to leveraging our expertise in métal stamping to deliver exceptional results for our clients. Whether you need components for produits de consommation or intricate parts for medical devices, we have the knowledge and technology to meet your needs.
Découvrez les dernières tendances et les faits les plus récents concernant la fabrication CNC sur notre blog.
Shenzhen Runkey Precision Technology Co. Ltd, une filiale du Groupe Tensun, est votre solution unique de confiance pour la fabrication sur mesure, du prototypage à la production. Transformer votre idée en réalité grâce à des ressources de fabrication numérique, des processus rationalisés, des conseils d'experts, des délais accélérés et une qualité sans compromis.
©2024. CNC Fabrication Tous droits réservés.