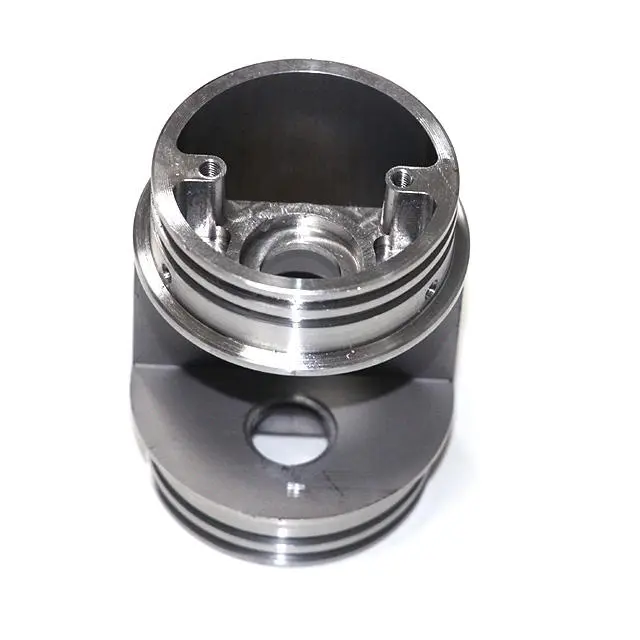
- +8615586668226
- [email protected]
- No. 30, Hongbang Industrial Park, Shenzhen
Urethane casting is a manufacturing process that involves pouring liquid urethane en un silicone mold to create a duplicate of an original part. This processus de coulée is renowned for its ability to produce highly detailed and accurate parts, making it a popular choice in industries like aerospace, automotive, and medical devices. The Le processus implique creating a master pattern, often through Impression 3D or CNC machining, which is then used to form a silicone mold.
Once the mold is ready, the urethane resin is mixed with a curing agent and poured into the mold. The mold is then placed in a vacuum chamber to remove any air bubbles, a technique known as vacuum casting. After curing, the finished urethane part is removed from the mold, ready for any necessary finishing processes. This method allows for the creation of complex shapes and intricate details that are difficult to achieve with other les processus de fabrication.
Lorsque l'on compare les casting and injection molding, it’s essential to understand the unique advantages of each. Urethane casting is often preferred for low to medium-volume production runs due to its lower tooling costs and shorter lead times. Moulage par injection, while ideal for high-volume production, requires expensive steel molds and longer setup times.
Urethane casting does not require the high pressures and temperatures associated with moulage par injection, making it a more cost-effective option for smaller batches. Additionally, urethane casting offers greater flexibility in terms of material selection, allowing for a wider gamme de matériaux with varying properties to be used. This makes urethane casting an excellent choice for prototyping and custom parts where design changes may be frequent. Consider a recent project where we rapidly prototyped parts for a medical device company. Using urethane casting, we quickly adapted to design changes, a flexibility not easily matched by injection molding.
Le type of urethane used in casting plays a crucial role in determining the properties of the final product. Urethane casting materials come in various formulations, each offering different characteristics such as flexibility, rigidity, heat resistance, and chemical resistance. Rigid urethane is commonly used for parts that require high strength and durability, while flexible urethane is ideal for applications that need impact resistance or flexibility.
Choisir le bon urethane formulation depends on the specific requirements of the project. Factors such as the intended use of the part, environmental conditions, and desired mechanical properties all play a role in selecting the appropriate urethane resin. Polyurethane resins can also be customized with additives to enhance specific properties, such as UV resistance or flame retardancy.
La polyvalence des urethane casting makes it suitable for a wide range of industries and applications. In the automotive industry, urethane casting is used to create prototypes and custom parts, such as bumpers, dashboards, and interior trim pieces. The aerospace sector utilizes urethane casting for manufacturing lightweight, high-strength components for aircraft interiors and tooling.
Urethane casting applications also extend to the medical field, where it’s employed to produce medical devices, prosthetics, and diagnostic equipment. The ability to create intricate details and biocompatible parts makes urethane casting ideal for these critical applications. Moreover, consumer products, electronics, and industrial equipment sectors leverage urethane casting for its precision and cost-effectiveness in producing high-quality parts.
Alors que les deux urethane casting et Impression 3D are used for prototyping and manufacturing, they differ significantly in their processes and capabilities. Impression 3D, also known as additive manufacturing, builds parts layer by layer from a digital model. This process is excellent for creating complex geometries and one-off parts but can be slower and more expensive for larger production runs.
Urethane casting, on the other hand, involves creating a silicone mold from a master pattern, which is then used to cast multiple parts. This makes urethane casting a faster and more cost-effective option for producing multiple copies of a part. Additionally, urethane casting offers a wider range of material options compared to Impression 3D, allowing for greater flexibility in achieving desired material properties.
Urethane offers numerous advantages that make it a preferred material in various manufacturing processes. One of the main advantages of using urethane is its exceptional durability and resistance to wear and tear. Urethane can withstand harsh environments, including exposure to chemicals, extreme temperatures, and high-impact forces. This makes urethane an ideal material for parts that require long-term performance and reliability.
Autre benefits of urethane est sa polyvalence. Urethane comes in a wide range of formulations, allowing manufacturers to tailor the material properties to meet specific needs. Whether you need a flexible, rubber-like material or a rigid, high-strength plastique, urethane can be formulated to provide the desired characteristics. Additionally, urethane can be easily colored and finished, providing a wide range of aesthetic options.
Fonctionnalité | Urethane Casting | Injection Molding |
Tooling Cost | Low | Haut |
Délai d'exécution | Short | Long |
Volume | Low to Medium | Haut |
Variété de matériaux | Haut | Limitée |
Flexibilité de la conception | Haut | Modéré |
Sélection de l'outil approprié urethane casting materials is crucial for achieving the desired properties and performance of the final product. The choice of urethane resin depends on various factors, including the intended use of the part, environmental conditions, and required mechanical properties.
Lors du choix d'un urethane resin, it’s essential to consider the specific type of urethane that best suits your needs. For example, if you need a part that can withstand high temperatures, you should select a heat-resistant urethane formulation. Similarly, if you need a flexible part, you should choose a urethane with high elasticity. Consulting with a casting expert can help you make an informed decision and ensure that you select the right urethane casting materials for your project. I recall a project for the defense sector where selecting the right urethane was critical for meeting stringent durability requirements. This highlights the importance of material selection in achieving product success.
Tandis que urethane casting is an excellent choice for low to medium-volume production, it may not be the most suitable method for high-volume manufacturing. Urethane casting typically involves creating a silicone mold, which has a limited lifespan and can produce a finite number of parts before needing replacement.
For high-volume production, moulage par injection is generally a more efficient and cost-effective option. Moulage par injection uses steel molds that can withstand millions of cycles, making it ideal for mass production. However, urethane casting can still be a viable option for high-volume production if the part design requires frequent changes or if the material properties needed are not achievable with moulage par injection.
Vacuum casting is a crucial step in the urethane casting process that helps ensure the production of high-quality, bubble-free parts. During vacuum casting, the filled silicone mold is placed inside a vacuum chamber, where air is removed from the mold cavity. This process eliminates any trapped air bubbles that could weaken the urethane cast part or create surface imperfections.
Vacuum casting is particularly important when working with complex geometries or intricate details, as it ensures that the liquid urethane completely fills the mold cavity, resulting in a precise and accurate reproduction of the master pattern. This technique enhances the overall quality and consistency of the urethane cast parts, making it a preferred method in urethane casting.
Optimiser la urethane casting process involves careful planning and attention to detail at each stage of production. One key aspect is the design and creation of the silicone mold. The mold must be designed to accurately replicate the master pattern while also allowing for easy removal of the urethane cast part.
Another critical factor is the proper mixing and handling of the urethane resin. Les urethane resin components must be mixed in the correct proportions to ensure proper curing and achieve the desired material properties. Additionally, the urethane casting environment should be controlled to maintain consistent temperature and humidity levels, which can affect the curing process.
Here’s a bullet point summary of optimization tips:
Conception du moule : Ensure the mold is designed for easy part removal and accurate replication.
Material Mixing: Mix urethane resin components in the correct proportions.
Coulée sous vide : Utilisation vacuum casting to eliminate air bubbles and ensure complete mold filling.
Curing Environment: Maintain consistent temperature and humidity during curing.
Post-Processing: Plan for any necessary secondary processes after the urethane part is cast, such as trimming, sanding, or painting.
To see these processes in action, visit our pages on Services d'usinage et Services de fabrication.
What is the typical lifespan of a silicone mold used in urethane casting?
Typically, a silicone mold can produce 20-30 parts before it starts to degrade. The exact lifespan depends on the complexity of the mold and the type of urethane utilisé.
Can urethane casting be used to create parts with different colors?
Oui, urethane casting allows for the creation of parts in various colors. Pigments can be added to the urethane resin during the mixing process to achieve the desired color.
What are the limitations of urethane casting compared to injection molding?
Urethane casting has limitations in terms of production volume and mold lifespan. Silicone molds utilisé dans urethane casting have a shorter lifespan compared to the steel molds used in moulage par injection, making it less suitable for very high-volume production.
How does the cost of urethane casting compare to 3D printing?
For small to medium production runs, urethane casting is generally more cost-effective than Impression 3D. Tout en Impression 3D is ideal for one-off parts, the cost per part tends to be higher for larger quantities.
What are the environmental considerations when using urethane casting?
Urethane casting can have environmental impacts related to the use of chemicals and the disposal of silicone molds. It’s important to choose environmentally friendly urethane formulations and follow proper disposal procedures for waste materials.
Is urethane casting suitable for creating food-grade parts?
Yes, certain urethane formulations are FDA-approved for food contact, making them suitable for creating food-grade parts. It’s essential to select a urethane resin that meets the necessary regulatory requirements for food safety.
Urethane casting is a versatile and cost-effective manufacturing process ideal for low to medium-volume production.
Silicone molds are used to create high-quality duplicates of master patterns.
Vacuum casting ensures the production of bubble-free parts with precise details.
Urethane casting offers a wide range of material options, allowing for customization based on specific project needs.
Moulage par injection is more suitable for high-volume production due to its use of durable steel molds.
Proper mold design, material mixing, and environmental control are essential for optimizing the urethane casting process.
Urethane casting finds applications in various industries, including automotive, aerospace, medical devices, and consumer products.
Choisir le bon type of urethane is crucial for achieving desired material properties and performance.
Urethane offers excellent durability, chemical resistance, and versatility.
Consultation d'un casting expert can help you navigate the complexities of urethane casting and ensure successful project outcomes.
For a deeper understanding of related processes, you can explore our pages on Solutions CNC, Usinage CNC, Fabrication de tôleset Prototypage rapide.
Découvrez les dernières tendances et les faits les plus récents concernant la fabrication CNC sur notre blog.
Shenzhen Runkey Precision Technology Co. Ltd, une filiale du Groupe Tensun, est votre solution unique de confiance pour la fabrication sur mesure, du prototypage à la production. Transformer votre idée en réalité grâce à des ressources de fabrication numérique, des processus rationalisés, des conseils d'experts, des délais accélérés et une qualité sans compromis.
©2024. CNC Fabrication Tous droits réservés.