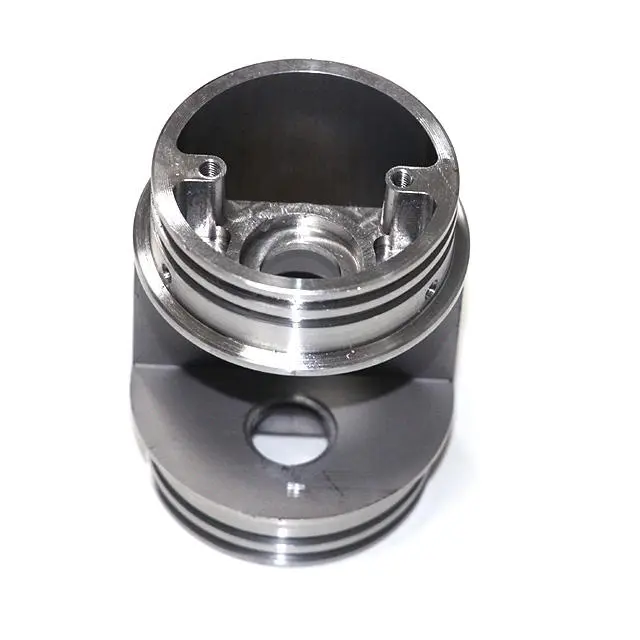
- +8615586668226
- [email protected]
- No. 30, Hongbang Industrial Park, Shenzhen
As a leading CNC Manufacturing Service and Product Manufacturing Factory, we understand the critical role of precision in every component we produce. Whether it’s a critical part for an aircraft, a life-saving medical device, or a high-performance automotive component, accuracy is non-negotiable. ISO 2768, the international standard for general tolerances, is a key tool in achieving this precision. It helps ensure consistency, and high-quality production, that is a must for our valued clients.
ISO 2768 is an internationally recognized standard that specifies general tolerances for linear and angular dimensions, as well as geometrical features. Think of it as the “rule book” for acceptable variations in manufacturing. It’s divided into two parts:
This standard eliminates the need to specify tolerances for every single feature on a technical drawing, saving time and reducing complexity. It’s like having a default setting for precision!
First introduced in 1989, ISO 2768 has been updated and refined over the years to meet the evolving demands of modern manufacturing. The 2003 revision was significant, adding geometrical tolerances to the standard (ISO 2768-2). This expansion made it even more relevant to processes like Usinage CNC, ensuring tighter control over product quality.
By applying ISO 2768 we can simplify and speed up the product manufacturing process.
Here are the main reasons for using the ISO 2768, international tolerance standard:
Imagine a world where every part fits perfectly, every time. That’s the promise of ISO 2768. By adhering to this standard, you can:
ISO 2768 uses different tolerance classes to define the level of precision required. Here’s a breakdown:
ISO 2768-1 (Linear and Angular Dimensions):
ISO 2768-2 (Geometrical Tolerances):
Selecting the appropriate tolerance class is crucial. Consider these factors:
We are committed to delivering the highest quality products, and ISO 2768 is a cornerstone of our quality management system. We can help you navigate the complexities of this standard and ensure your parts are manufactured to the exact specifications you require.
Contact us today to discuss your project and experience the difference of precision manufacturing!
ISO 2768-1 sets the permissible deviations for linear and angular dimensions. This means that instead of specifying tolerances for every single length, width, or angle on a drawing, you can simply refer to the relevant tolerance class (f, m, c, or v).
Linear Dimension Tolerances (Example):
Nominal Size Range (mm) | f (Fine) | m (Medium) | c (Coarse) | v (Very Coarse) |
---|---|---|---|---|
0.5 up to 3 | ±0.05 | ±0.1 | ±0.2 | – |
Over 3 up to 6 | ±0.05 | ±0.1 | ±0.3 | ±0.5 |
Over 6 up to 30 | ±0.1 | ±0.2 | ±0.4 | ±0.8 |
Over 30 up to 120 | ±0.15 | ±0.3 | ±0.6 | ±1.2 |
This table shows how the allowable deviation changes based on the size range and tolerance class. For example, a dimension of 10mm with a “medium” (m) tolerance would have an allowable deviation of ±0.2mm.
ISO 2768-1 also covers external radii and chamfer heights. These are often critical features for ensuring parts fit together properly.
Nominal Size Range (mm) | f (Fine) and m (Medium) | c (Coarse) and v (Very Coarse) |
---|---|---|
0.5 up to 3 | ±0.2 mm | ±0.4 mm |
Over 3 up to 6 | ±0.5 mm | ±1.0 mm |
Angular tolerances are specified in degrees and minutes. The allowable deviation depends on the length of the shorter leg of the angle.
Nominal Length (mm) | f (Fine) and m (Medium) | c (Coarse) | v (Very Coarse) |
---|---|---|---|
Up to 10 | ±1° | ±1°30′ | ±3° |
Over 10 up to 50 | ±0°30′ | ±1° | ±2° |
ISO 2768-2 addresses geometrical tolerances, which control the form and orientation of features. This includes:
Example: Straightness and Flatness Tolerances
Nominal Length (mm) | H (High) | K (Medium) | L (Low) |
---|---|---|---|
Up to 10 | 0.02 mm | 0.05 mm | 0.1 mm |
Over 10 up to 30 | 0.05 mm | 0.1 mm | 0.2 mm |
These two parts of the standard work together. ISO 2768-1 controls the overall size and position of features, while ISO 2768-2 refines the shape and orientation. For example, a part might have a length tolerance defined by ISO 2768-1 and a flatness tolerance defined by ISO 2768-2.
To use ISO 2768, you simply indicate the relevant tolerance classes in the title block of your drawing. For example, “ISO 2768-mK” would specify medium tolerances for linear/angular dimensions and medium geometrical tolerances.
Clear tolerances are essential for:
Understanding the markings (e.g., “ISO 2768-mK”) is crucial for ensuring parts are manufactured correctly.
ISO 2768 is used across a wide range of industries, including:
ISO 2768 improves quality control by:
ISO 2768 promotes consistency across international production lines, facilitating collaboration between manufacturers in different regions.
A company used ISO 2768 to guide the creation of a compressor base. By setting general tolerances, they minimized errors during Fraisage CNC and reduced costs.
What’s the difference between ISO 286 and ISO 2768?
ISO 286 focuses on fits between parts (like shafts and holes), while ISO 2768 provides general tolerances for a wider range of dimensions.
What does ISO 2768-mK mean?
It signifies “medium” tolerances for linear/angular dimensions (“m”) and “medium” geometrical tolerances (“K”).
How does ISO 2768 affect CNC machining accuracy?
It establishes tolerance limits, ensuring parts are produced with the required precision and reducing defects.
Can ISO 2768 be used with other standards?
Yes, it often complements more specific standards, such as those for découpe au laser ou fabrication de tôles.
What are general tolerances?
General tolerances, are the default values.
Are general tolerances good?
Yes. general tolerances, streamline the design and manufacturing process.
Découvrez les dernières tendances et les faits les plus récents concernant la fabrication CNC sur notre blog.
Shenzhen Runkey Precision Technology Co. Ltd, une filiale du Groupe Tensun, est votre solution unique de confiance pour la fabrication sur mesure, du prototypage à la production. Transformer votre idée en réalité grâce à des ressources de fabrication numérique, des processus rationalisés, des conseils d'experts, des délais accélérés et une qualité sans compromis.
©2024. CNC Fabrication Tous droits réservés.