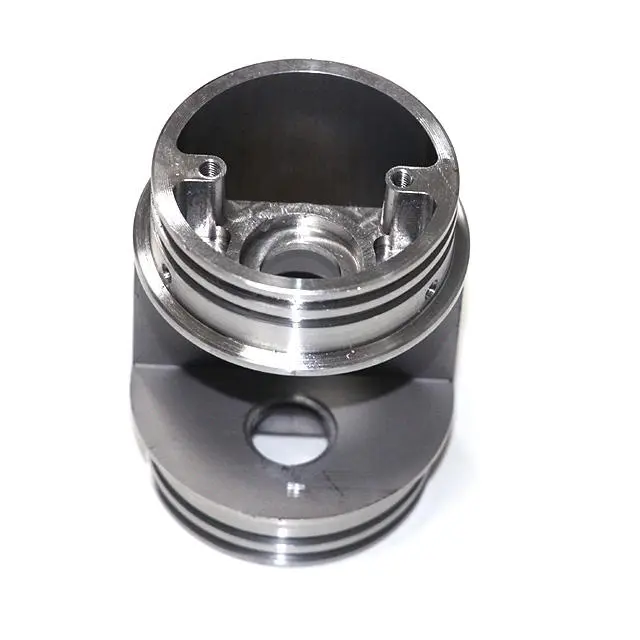
- +8615586668226
- [email protected]
- Hongbang ipari park, 30. szám, Shenzhen
3D metal printing, also known as metal additive manufacturing, is an innovative process of building three-dimensional metal parts directly from a digital design. Unlike traditional subtractive manufacturing, which removes material to create the desired shape, 3D metal printing adds material layer by layer. This is a real game-changer for industries that demand complex geometries, customized solutions, and rapid prototyping.
The core of this revolution lies in its ability to create intricate designs previously impossible to manufacture using conventional methods. This opens up a world of possibilities for industries looking to optimize performance, reduce weight, and improve functionality. We, at [Your Company Name], understand this potential and are committed to providing our customers with cutting-edge 3D metal printing solutions tailored to their specific needs. We can make Fogyasztói termékek!
Several 3D metal printing methods are available, each with its unique strengths and applications. The most prominent techniques include:
Each method offers distinct advantages in terms of material compatibility, precision, and production speed. Choosing the right method depends on the specific requirements of the application, and understanding these nuances is crucial for achieving optimal results. We have CNC megoldások for you!
SLS/SLM is a powder-bed fusion technology where a high-powered laser selectively sinters (fuses) or melts metal powder particles together, layer by layer, according to a 3D CAD model. The process begins by spreading a thin layer of metal powder onto a build platform. The laser then scans the cross-section of the part, solidifying the powder in the desired pattern.
After each layer is completed, the build platform lowers, and a new layer of powder is spread. This process repeats until the entire part is built. Un-sintered powder supports the part during printing, eliminating the need for support structures in many cases. This makes SLS/SLM ideal for creating complex geometries and intricate internal features. Precíziós megmunkálás is in our DNA!
SLS/SLM offers several key advantages:
However, SLS/SLM also has some limitations:
Jellemző | Előny | Disadvantage |
---|---|---|
Design Freedom | Complex geometries, internal features | – |
Anyag | Wide range of metals and alloys | – |
Támogatás | Un-sintered powder acts as support | – |
Felületkezelés | – | Post-processing required |
Porosity | – | Affects mechanical properties |
Költségek | – | Higher initial and operational investment |
EBM, another powder-bed fusion technology, utilizes an electron beam instead of a laser to melt metal powder. The process is conducted in a vacuum environment, which minimizes contamination and enhances material properties. EBM also preheats the powder bed, reducing residual stress and improving the mechanical performance of the final part.
The higher energy density of the electron beam allows for faster melting rates and the ability to process certain materials that are difficult to process with SLS/SLM. However, EBM typically requires larger feature sizes and may result in a rougher surface finish compared to SLS/SLM. Fém hajlítás also requires expertise!
EBM is particularly well-suited for processing reactive materials such as:
These materials benefit from the vacuum environment, which prevents oxidation and ensures high purity. While the material selection for EBM is more limited than SLS/SLM, it offers superior performance for specific alloys.
DMD is a directed energy deposition (DED) process where metal powder is directly fed into a melt pool created by a laser beam. The laser and powder nozzle are moved simultaneously to build the part layer by layer. DMD offers the advantage of building large parts and repairing existing components.
Key benefits of DMD include:
However, DMD typically requires significant post-processing to achieve the desired surface finish and dimensional accuracy. CNC esztergálás can help!
Several factors significantly impact the performance of metal 3D printing:
Controlling these factors is essential for achieving consistent and reliable results. At [Your Company Name], we meticulously manage these parameters to ensure the highest quality for our customers.
Despite its advantages, metal 3D printing is susceptible to several common defects:
Addressing these defects requires a deep understanding of the process and careful optimization of parameters. Our expertise at [Your Company Name] ensures we can minimize these issues and deliver high-quality parts.
In layer-by-layer manufacturing, the strength in the Z-direction (perpendicular to the build layers) is often lower than in the X and Y directions due to the anisotropic nature of the material. This is because the bonds between layers are weaker than within a single layer.
To improve Z-direction strength, consider these strategies:
Understanding and addressing this limitation is critical for ensuring the structural integrity of 3D printed parts, especially for load-bearing applications.
Here’s what we can learn from the 3D metal printing progress:
At [Your Company Name], we are committed to providing our customers with comprehensive CNC manufacturing services, including state-of-the-art 3D metal printing capabilities. We offer:
We serve a wide range of industries including:
Partner with us to unlock the full potential of 3D metal printing and gain a competitive edge in your industry. Contact us today to discuss your project! Let us take care of your On Demand gyártás szükségletei!
Is 3D metal printing expensive? While the initial investment can be significant, the long-term benefits, such as reduced material waste and faster prototyping, can offset the cost.
What is the typical turnaround time for 3D metal printing projects? Turnaround time depends on the complexity of the part, material selection, and production volume, but it’s often faster than traditional methods.
What file formats are compatible with 3D metal printing? The standard file format is STL, but other formats like STEP and CAD files can also be used.
Can 3D metal printing be used for mass production? Yes, as the technology matures, it is becoming increasingly viable for mass production, especially for customized or complex parts.
What types of post-processing are typically required for 3D metal printed parts? Common post-processing steps include machining, heat treatment, and surface finishing to achieve the desired surface finish, dimensional accuracy, and mechanical properties.
Belső hivatkozások:
Blogunkból értesülhet a CNC-gyártással kapcsolatos legújabb trendekről és tényekről.
Shenzhen Runkey Precision Technology Co. Ltd, a Tensun Group leányvállalata, az Ön megbízható egyablakos megoldása az egyedi gyártáshoz a prototípusoktól a gyártásig.Az Ön ötlete digitális gyártási erőforrásokkal, egyszerűsített folyamatokkal, szakértői útmutatással, gyorsított határidőkkel és kompromisszumok nélküli minőséggel válik valósággá.
©2024. CNC Fabrication Minden jog fenntartva.