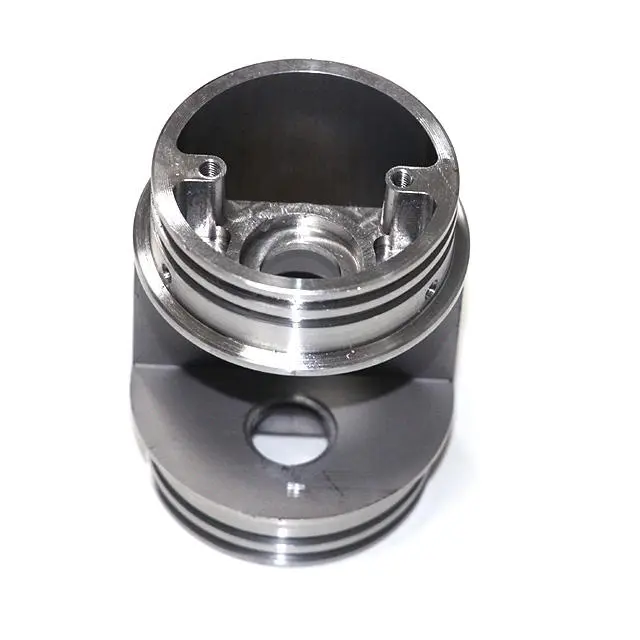
- +8615586668226
- [email protected]
- Hongbang ipari park, 30. szám, Shenzhen
A esztergapad egy sokoldalú szerszámgép amely a munkadarabot egy forgástengely körül forgatja különböző műveletek, például vágás, csiszolás, bütykölés, fúrás vagy deformálás, homloklapozás és esztergálás elvégzésére. Esztergályos vágószerszámok alapvető összetevői ennek a folyamatnak. Arra tervezték őket, hogy eltávolítsák az anyagot a munkadarabból, és a kívánt formára alakítsák azt. CNC-gyártási szolgáltatásokra szakosodott vállalatként megértjük, hogy ezek az eszközök milyen kritikus szerepet játszanak a pontosság és a hatékonyság elérésében.
Vannak különböző típusú esztergák eszközök, amelyek mindegyike egy adott esztergálás. Például egy esztergályozó szerszám egy forgó munkadarab külső átmérőjéről történő anyageltávolításra szolgál. A szembefordító szerszám a munkadarab végén egy sík felület létrehozására szolgál. Elválasztó szerszámok, más néven vágószerszámok, a munkadarab levágására szolgálnak az alapanyagról. Ezután következik a fúrószerszám ami létrehozásához használt vagy egy munkadarabon lévő lyuk megnagyobbítása, sokkal nagyobb pontossággal és hatékonysággal, mint egy hagyományos fúrófej. Egyéb esztergályos szerszámok menetes szerszámok, ferde szerszámok, és bütykölő szerszámok.
A esztergályos vágószerszám úgy működik, hogy anyagot távolít el egy forgó munkadarabról. A használt eszköz általában álló, szerszámoszlopra szerelt, a munkadarab pedig forog. A élvonalbeli a szerszám a munkadarabhoz nyomják, és az anyagot forgács formájában eltávolítják. Az alakja a vágószerszám meghatározza a vágás alakját. A fő tényező az, hogy a vágószerszám anyaga és geometriája a siker kulcspontjai.
A vágási sebesség, az előtolási sebesség és a vágási mélység fontos paraméterek, amelyek befolyásolják a megmunkálási folyamatot. Vágási sebesség a munkadarab forgási sebességére utal. Az előtolási sebesség az a sebesség, amellyel a vágószerszám a munkadarab mentén mozog. A vágási mélység az egy menetben eltávolított anyag vastagsága. CNC-gyártási szolgáltatásokat nyújtó szolgáltatóként gondosan ellenőrizzük ezeket a paramétereket a megmunkálási folyamat optimalizálása és a kívánt eredmények elérése érdekében.
A jobb esztergályos vágószerszám kulcsfontosságú minden megmunkálási projekt sikeréhez. A esztergaszerszám típusa a kiválasztott függ a vágás típusa művelet, a munkadarab anyaga és a kívánt felületkezelés. A helytelen szerszám rossz felületkezeléshez, méretezési pontatlanságokhoz, sőt, akár az anyag sérüléséhez is vezethet. esztergapad vagy vágószerszám.
Például, durva esztergálási szerszámok úgy tervezték, hogy eltávolítsa nagy mennyiségű anyag gyorsan, míg befejező esztergályozó szerszámok a sima felület eléréséhez használják. Gyémánt szerszámok kivételesen kemények, és gyakran használják őket nagyon kemény anyagok megmunkálására vagy rendkívül finom felületkezelés elérésére. Karbid szerszámok népszerűek a tartósságuk és a magas hőmérsékletnek való ellenálló képességük miatt. Mi, mint CNC gyártási szolgáltatásokat nyújtó vállalat, aprólékosan kiválasztjuk a megfelelő esztergályos vágószerszám minden egyes projekthez, biztosítva az optimális eredményeket és az ügyfelek elégedettségét.
A jobb esztergályos vágószerszám több tényező gondos mérlegelését igényli. Először is meg kell határoznia, hogy milyen típusú műveletet fog végezni. Esztergál, homloklapátol, fúr, vagy menetvágás? Mindegyik művelethez speciális esztergaszerszám típusa. Segítünk Önnek válassza ki a megfelelő esztergapad vágás eszköz az Ön egyedi igényei alapján.
Ezután vegye figyelembe a munkadarab anyagát. A különböző anyagok különböző vágási jellemzőkkel rendelkeznek. Egyes anyagok kemények és koptató hatásúak, míg mások puhák és gumiszerűek. A esztergályos vágószerszám anyagnak keményebbnek kell lennie, mint a munkadarab anyagának. CNC-vágószerszámok a gépek különböző anyagokból, többek között nagysebességű acélból, keményfémből, kerámiából és gyémántból készülnek.
A esztergályos vágószerszám számos kulcsfontosságú összetevője van, amelyek hozzájárulnak a vágóhatáshoz. Ezek közé tartozik a élvonalbeli, a szár és a szerszámtartó. A élvonalbeli az a része a szerszám amely érintkezik a munkadarabbal és eltávolítja az anyagot. A fő vágóél az elsődleges vágási műveletért felelős, míg a oldalsó vágóél és vágóél további vágási képességeket biztosít.
A lábszár a teste a vágószerszám amelyet a szerszámtartóban tartanak. A szerszámtartó egy olyan eszköz, amely biztonságosan tartja a vágószerszám a helyén a esztergapad. A geometria a élvonalbeli, beleértve a forgácsolási szöget, a távolsági szöget és az orrsugarat, döntő szerepet játszik a vágási teljesítményben. esztergályos vágószerszám.
CNC esztergálás forradalmasította a hagyományos esztergapad automatizálás és precíziós vezérlés bevezetésével. A CNC eszterga, a mozgás a vágószerszám egy számítógépes program vezérli. Ez lehetővé teszi az összetett formák és bonyolult minták nagy pontossággal és megismételhetőséggel történő megmunkálását.
CNC esztergálás számos előnyt kínál a hagyományos esztergapad műveletek. Gyorsabb megmunkálási időt, jobb felületi minőséget és kevesebb kezelői beavatkozást tesz lehetővé. CNC gépek több műveletet is elvégezhet egyetlen beállítással, ami tovább növeli a hatékonyságot. A CNC-gyártási szolgáltatások vezető szolgáltatójaként kihasználjuk a következők erejét CNC esztergálás hogy kiváló minőségű alkatrészeket szállíthassunk ügyfeleinknek különböző iparágakban, többek között a következőkben repülőgépipar, autóipari és orvostechnikai eszközök.
Esztergályos vágószerszámok különböző anyagokból készülnek, amelyek mindegyike egyedi tulajdonságokkal és alkalmazásokkal rendelkezik. A legtöbb közös típus a használt eszköz a oldalon. esztergák nagysebességű acélból (HSS) készül. A HSS-szerszámok viszonylag olcsók és könnyen újraélezhetők. Anyagok széles körének megmunkálására alkalmasak.
Karbid szerszámok keményebbek és kopásállóbbak, mint a HSS szerszámok. Magasabb vágási hőmérsékletet bírnak el, és ideálisak kemény anyagok megmunkálásához. Kerámia és gyémánt szerszámok még keményebbek, és speciális alkalmazásokhoz használják őket. Mi, mint CNC gyártási szolgáltatásokat nyújtó vállalat, a következő termékek széles választékát használjuk fel vágószerszám anyagokat, hogy megfeleljenek ügyfeleink egyedi igényeinek. Lemezgyártás egy másik specialitás, amelyet fejlett anyagok és technikák felhasználásával kínálunk.
Megfelelő karbantartás és élezés esztergályos vágószerszámok elengedhetetlenek a vágási teljesítményük fenntartásához és élettartamuk meghosszabbításához. A tompa vágószerszám rossz felületet eredményez, túlzott hőt termel, és növeli a vágóerő szükséges.
Esztergályos vágószerszámok rendszeresen ellenőrizni kell a kopás vagy sérülés jelei miatt. A élvonalbeli élesnek és repedés- vagy repedésmentesnek kell lennie. Ha egy szerszám tompa lesz, újra kell élezni egy csiszolókorong vagy egy speciális szerszámcsiszoló segítségével. Az élezés helyreállítja a éles vágóél és optimális vágási teljesítményt biztosít.
Számos gyakori műveletet végeznek egy esztergapad, amelyek mindegyike különleges típusú esztergályos vágószerszámok. Az alábbi táblázatban összefoglaljuk a leggyakoribb műveleteket és a használt eszközök:
Művelet | Leírás | Használt eszköz |
Fordulás | Anyag eltávolítása a munkadarab külső átmérőjéről | Esztergályozó szerszám |
Szembenézés | Sík felület létrehozása a munkadarab végén | Szembenéző szerszám |
Unalmas | Meglévő furat nagyítása egy munkadarabon | Fúrószerszám |
Elválás/elvágás | A kész alkatrész elválasztása a raktáranyagtól | Elválasztó szerszám |
Szálazás | Belső vagy külső menet vágása a munkadarabon | Menetvágó szerszám, külső menetvágó szerszámok |
Knurling | Mintás felület létrehozása a munkadarabon a jobb fogás érdekében | Bütykölő szerszám |
Grooving | Vájat vagy mélyedés vágása a munkadarabba | Nútfúró szerszámok |
Fazettázás | Ferde él létrehozása a munkadarabon | Ferde szerszám |
Fúrás | Lyuk készítése egy munkadarabon | Fúrófej |
Reaming | A fúrt lyuk pontos méretre és sima felületre történő kikészítése | Fúrógép |
Tapping | Belső menet vágása egy lyukban | Tap |
Formanyomtatás | Összetett formák létrehozása egy munkadarabon egy speciálisan kialakított vágószerszám | Forma eszköz |
Kúpos esztergálás | Kúp alakú forma létrehozása egy munkadarabon | Kúpos esztergálás vagy CNC-vezérlés |
Fordulás a leggyakoribb esztergálás. Esztergályozó szerszámokat használnak a munkadarab átmérőjének csökkentése. A jobb oldali szerszám jobbról balra vág, a vágóél a bal oldalon, míg a bal oldali szerszám balról jobbra haladva, a vágóél a jobb oldalon.
Szembenéző eszközöket használnak hogy a forgástengelyre merőleges sík felületet hozzon létre. Fúrószerszámokat használnak a meglévő lyukak bővítéséhez. Elválasztó szerszámokat használnak a kész munkadarab levágása az alapanyagról.
A modern gyártás nagy pontosságot, hatékonyságot és termelékenységet igényel. Fejlett esztergályos vágószerszámok, mint például a karbidból, kerámiából vagy gyémántból készültek, jelentős előnyöket kínálnak ezen igények kielégítésében. Ezek a szerszámok nagyobb vágási sebességet és hőmérsékletet képesek elviselni, ami gyorsabb anyagleválasztási sebességet tesz lehetővé.
Haladó vágószerszámok jobb kopásállóságot is biztosítanak, ami hosszabb szerszámélettartamot és a szerszámcserék miatti kevesebb állásidőt eredményez. Kiváló felületi felületkezelésre képesek, csökkentve a másodlagos befejező műveletek szükségességét. Mint előremutató CNC-gyártási szolgáltatásokat nyújtó vállalat, elfogadjuk a korszerű esztergályos vágószerszámok hogy kiváló minőséget és értéket nyújtsunk ügyfeleinknek, különösen az olyan igényes ágazatokban, mint a orvostechnikai eszközök és robotika.
Mi a különbség a jobb és a bal oldali vágószerszám között?
A jobb oldali vágószerszám úgy van kialakítva, hogy jobbról balra vágjon, és a élvonalbeli a szerszám bal oldalán, ahogy a szerszámmal szemben áll. A bal oldali szerszám úgy tervezték, hogy balról jobbra haladva vágjon, a élvonalbeli a jobb oldalon. A jobb és bal oldali szerszám közötti választás a vágás irányától és a szerszám beállításától függ. esztergapad.
Mire használják a bütykölőszerszámot?
A bütykölő szerszám a munkadarab felületén texturált mintázat létrehozására szolgál. Ez a minta jellemzően egyenes, szögletes vagy keresztezett vonalakból áll, amelyeket az anyagba nyomnak vagy hengerelnek. A bütykölést általában a fogantyúk, gombok és egyéb alkatrészek jobb tapadásának javítására használják. Mi a bütykölő szerszámok különböző alkalmazásokban a gyártott alkatrészek funkcionalitásának és esztétikájának fokozására.
Miért előnyösek a keményfém szerszámok kemény anyagok megmunkálásához?
Karbid szerszámok a kemény anyagok megmunkálásához előnyben részesítik, mivel sokkal keményebbek, mint a nagysebességű acélszerszámok. A keményfémek jelentős kopás nélkül képesek ellenállni a kemény anyagok vágásakor keletkező magas hőmérsékletnek és koptató erőknek. Ez hosszabb szerszámélettartamot és jobb vágási teljesítményt eredményez.
Milyen gyakran kell élezni az esztergályos vágószerszámokat?
Az élesítés gyakorisága több tényezőtől függ, többek között a következőktől vágószerszám anyag, a munkadarab anyaga, a vágási sebesség, és a kívánt felületi kialakítás. Általános szabályként, esztergályos vágószerszámok rendszeresen ellenőrizni kell a kopás jeleit, és amint az élezés megkezdődik, meg kell élezni. élvonalbeli unalmassá válik. Egy unalmas szerszám többre lesz szükség vágóerő, rossz felületet eredményez, és túlzott hőt termel.
Mit jelent az esztergapad forgácsolószerszámoknál a "forgácsolási szög" kifejezés?
A dőlésszög az a szög, amely a cső felső felülete és az vágószerszám (az a felület, amely mentén a forgács áramlik) és egy, a munkadarab felületére merőleges síkot a élvonalbeli. Az élszög befolyásolja a vágóerő, forgácsképződés és hőtermelés a megmunkálás során. A pozitív forgácsolási szög csökkenti a vágóerő és javítja a forgácsáramlást, de gyengítheti a élvonalbeli. A negatív dőlésszög növeli a vágóerő hanem erősíti a élvonalbeli, így alkalmas kemény anyagok megmunkálására.
Milyen előnyei vannak a CNC esztergának a hagyományos esztergával szemben?
CNC esztergák számos előnyt kínálnak a hagyományos esztergákkal szemben, többek között nagyobb pontosságot, nagyobb termelékenységet, automatizálási lehetőségeket, összetett formák megmunkálásának képességét, jobb ismételhetőséget, kevesebb kezelői beavatkozást és több művelet elvégzésének lehetőségét egyetlen beállítással.
Esztergályos vágószerszámok elengedhetetlenek a munkadarabok megformálásához és megmunkálásához egy esztergapad.
Vannak különböző típusú esztergák speciális műveletekre tervezett szerszámok, például esztergálás, homloklapozás, fúrás és menetvágás.
A jobb esztergályos vágószerszám döntő fontosságú az optimális megmunkálási eredmények eléréséhez.
CNC esztergálás forradalmasította esztergapad automatizálás és precíziós vezérlés bevezetésével.
Esztergályos vágószerszámok különböző anyagokból készülnek, többek között nagysebességű acélból, karbidból, kerámiából és gyémántból.
Megfelelő karbantartás és élezés esztergályos vágószerszámok elengedhetetlenek a vágási teljesítményük fenntartásához.
Haladó esztergályos vágószerszámok jelentős előnyöket kínálnak a modern gyártás során, beleértve a megnövekedett termelékenységet, a jobb kopásállóságot és a kiváló felületi felületeket.
Vezető CNC-gyártó szolgáltatóként elkötelezettek vagyunk a legmodernebb technológiák felhasználása mellett. esztergályos vágószerszám technológiákat, hogy kivételes minőséget és értéket nyújtsunk ügyfeleinknek.
Szakértelmünk az iparágak széles skálájára terjed ki, beleértve a repülőgépipart, az autóipart, az orvostechnikai eszközöket és még sok más iparágat. Lépjen kapcsolatba velünk még ma, hogy megtudja, hogyan CNC megoldások előnyös lehet a következő projektje számára.
Mi nem csak egy szolgáltató vagyunk; mi az Ön partnerei vagyunk a gyártási kiválóság elérésében.
A minőség, a pontosság és a vevői elégedettség iránti elkötelezettségünk megkülönböztet minket a CNC-gyártás versenyében.
Büszkék vagyunk arra, hogy képesek vagyunk különböző összetettségű projekteket kezelni, az egyszerű alkatrészektől a bonyolult szerelvényekig, mindig a legmagasabb minőségi és precíziós szabványoknak megfelelően.
Blogunkból értesülhet a CNC-gyártással kapcsolatos legújabb trendekről és tényekről.
Shenzhen Runkey Precision Technology Co. Ltd, a Tensun Group leányvállalata, az Ön megbízható egyablakos megoldása az egyedi gyártáshoz a prototípusoktól a gyártásig.Az Ön ötlete digitális gyártási erőforrásokkal, egyszerűsített folyamatokkal, szakértői útmutatással, gyorsított határidőkkel és kompromisszumok nélküli minőséggel válik valósággá.
©2024. CNC Fabrication Minden jog fenntartva.