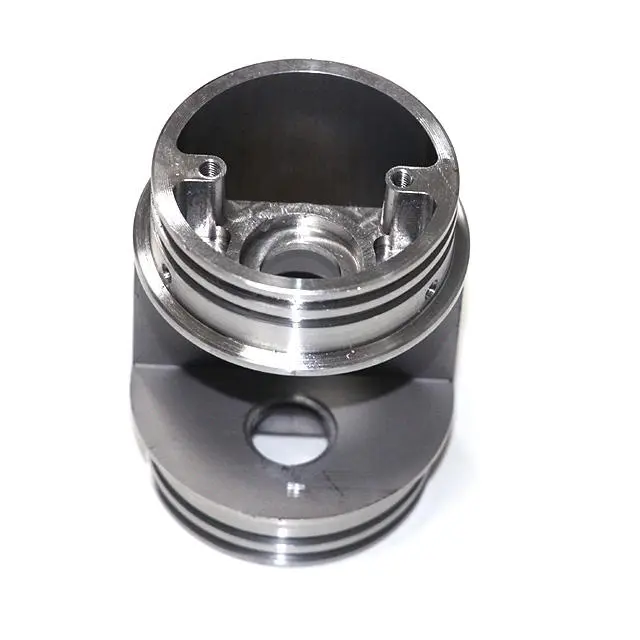
- +8615586668226
- [email protected]
- No. 30, Parco Industriale Hongbang, Shenzhen
A mulino frontale è un taglierina designed to create superfici piane on a workpiece. The face mill cutter has multiple cutting teeth, which work like utensile da taglio located on its face or end, perpendicular to the workpiece. It is a tipo di fresatura that’s used to rimuovere il materiale from the top of a workpiece. The face milling process prevede la rotazione del mulino frontale at high speeds while feeding it across the material. This process removes material from a workpiece, producing a smooth, flat surface.
As a CNC fabrication services provider, we frequently use fresatura frontale in our manufacturing plants. This technique is particularly valuable for industries like aerospace, automotive, and medical devices, where precision and surface finish are paramount. For instance, in aerospace manufacturing, fresatura frontale is used to machine large aluminum panels to precise dimensions, ensuring a flawless surface for aerodynamic efficiency.
Fresatura periferica è un operazione di fresatura dove il bordo di taglio del taglierina is located on its circumference, or periphery. In this type of operazione di fresatura, il taglierina rotates parallel to the workpiece surface. This milling technique is used to create slots, shoulders, and profiles. It is also called “side milling”. It’s effective for creating complex shapes and contours.
Fresatura periferica differs significantly from fresatura frontale. Mentre fresatura frontale is used to flatten surfaces, fresatura periferica is ideal for shaping the edges and sides of a workpiece. In our experience, industries like tooling and dies, heavy equipment, and construction rely heavily on fresatura periferica to craft intricate parts and components. For example, creating the teeth of a gear involves fresatura periferica to achieve the precise shape and spacing required for optimal function.
La differenza principale tra fresatura frontale e fresatura periferica lies in the orientation of the taglierina e il bordo di taglio relative to the workpiece. Here’s a detailed comparison:
Caratteristica | Fresatura frontale | Peripheral Milling |
Cutter Orientation | Perpendicular to the workpiece | Parallel to the workpiece |
Cutting Edge Location | On the face or end of the cutter | On the circumference of the cutter |
Surface Created | Flat, smooth surface | Slots, shoulders, profiles, contours |
Applicazione | Flattening large surfaces, creating flat faces | Shaping edges, creating complex shapes and contours |
Feed Direction | Across the workpiece surface | Along the workpiece edge |
In our manufacturing processes, we carefully assess the project requirements to determine whether fresatura frontale o fresatura periferica is more suitable. For example, if we need to create a perfectly flat surface on a large metal plate for the industria automobilistica, fresatura frontale is the clear choice. However, if we’re machining a complex mold for the food and packaging industry, fresatura periferica might be the preferred method to achieve the desired intricate shapes.
Fresatura frontale isn’t a one-size-fits-all process. Several variations cater to specific machining needs. Here are some common types of face milling:
Conventional Face Milling: In this approach, the taglierina rotates against the direction of the feed. It’s generally used for roughing operations where removing large amounts of material from a workpiece is the primary goal. It is a face milling technique that can be used on most materials.
Climb Face Milling: Qui, il taglierina rotates in the same direction as the feed. This technique is often preferred for finishing operations, as it produces a better superficie liscia finish and reduces tool wear.
Partial Face Milling: This method involves machining only a portion of the workpiece surface. This operazione di fresatura could be useful when specific areas require a flat surface while others need to retain their original shape.
Full Face Milling: Come suggerisce il nome, questo tipo di fresatura involves machining the entire surface of the workpiece.
Ciascuno face milling operation has its unique advantages and limitations. In our Soluzioni CNC, we carefully evaluate the project specifications and material properties to select the most appropriate fresatura frontale technique.
Scegliere il giusto face mill cutter is crucial for achieving optimal results. Here are some key factors to consider when selecting tools used for face milling:
Materiale: The workpiece material significantly influences the choice of cutter material. For example, carbide cutters are often used for machining hard materials like steel, while high-speed steel (HSS) cutters are suitable for softer materials like aluminum.
Diametro: The diameter of the mulino frontale should be appropriate for the size of the surface being machined. Larger diameters allow for faster material removal but may require more powerful machines.
Number of Teeth: The number of teeth on the mulino frontale affects the cutting speed and feed rate. More teeth generally result in a smoother finish but may require lower feed rates.
Insert Geometry: Mulini frontali often use replaceable inserts. The geometry of these inserts (e.g., square, round, diamond) impacts the cutting action and chip formation.
In our manufacturing plants, we maintain a diverse inventory of face mill cutters to accommodate various materials and project requirements. For instance, when working on aerospace projects, spesso utilizziamo indexable face mills with advanced carbide inserts to ensure precision and efficiency when machining high-strength alloys.
Fresatura frontale offers several advantages that make it a preferred choice for many machining applications:
Efficienza: Fresatura frontale is a highly efficient way to remove material and create flat surfaces. The multiple cutting teeth on the mulino frontale allow for rapid material removal, reducing machining time.
Finitura superficiale: Fresatura frontale can produce a high-quality superficie liscia finish, especially when using climb milling. This is important for applications where surface quality is critical, such as in the medical devices industry.
Versatilità: Fresatura frontale can be performed on a wide range of materials, including metals, plastics, and composites. It’s a versatile processo di lavorazione that can be adapted to various project needs.
Costo-efficacia: Due to its efficiency and ability to produce finished surfaces in a single operation, fresatura frontale can be a cost-effective machining method, especially for large-scale production.
Frese a candela are another type of fresa, but they differ significantly from mulini per facce. Unlike end mills and shell mills, which have cutting teeth on their periphery and end, mulini per facce primarily have cutting teeth on their face. Frese a candela are versatile and can be used for various milling tasks, including profiling, slotting, and contouring.
So, when should you choose an fresa a candela over a mulino frontale? Here’s a simple guideline:
Use a mulino frontale when you need to create a large, flat surface quickly and efficiently.
Use an fresa a candela when you need to create complex shapes, slots, or contours, or when you need to machine the edges of a workpiece.
Secondo la nostra esperienza, fresatura frontale is generally preferred for large flat surfaces, while frese a candela are better suited for intricate details and edge work. For example, when machining a large plate for the energy sector, we would typically use a mulino frontale to create the primary flat surface. However, if we needed to create slots or holes in that same plate, we would switch to an fresa a candela for those specific operations.
Achieving optimal results with fresatura frontale requires more than just using the right tools. Here are some key factors that contribute to successful face milling:
Proper Setup: Ensuring that the workpiece is securely clamped and the macchina is properly aligned is crucial for achieving accurate results.
Optimal Cutting Parameters: Selecting the correct cutting speed, feed rate, and depth of cut is essential for maximizing efficiency and tool life. These parameters depend on the material, taglierina, and desired surface finish.
Effective Chip Evacuation: Proper chip removal is critical to prevent chip build-up, which can lead to tool damage and poor surface finish. Using coolant or compressed air can help evacuate chips effectively.
Manutenzione regolare: Keeping the macchina e utensili da taglio in good condition is essential for consistent performance. This includes regular cleaning, lubrication, and tool inspection.
Utilizzo face milling tools effectively requires a combination of knowledge, skill, and attention to detail. Here are some tips for getting the most out of your face milling tools:
Learn about the Different Types of Face Mills: Familiarize yourself with the various types of mulini per facce available, such as shell mills, fly cutters, e indexable face mills. Each type has its unique characteristics and applications.
Understand the Cutting Geometry: Pay attention to the geometry of the cutting inserts. Factors like rake angle, clearance angle, and nose radius can significantly impact cutting performance and surface finish.
Experiment with Different Cutting Parameters: Don’t be afraid to experiment with different cutting speeds, feed rates, and depths of cut to find the optimal settings for your specific application.
Use Coolant or Lubricant: Applying coolant or lubricant during fresatura frontale can help reduce heat, improve chip evacuation, and extend tool life.
Servizi di fresatura CNC play a vital role in modern manufacturing by offering precision, efficiency, and automation. Fresatura CNC machines are computer-controlled, allowing for highly accurate and repeatable machining operations. This is particularly important for industries like aerospace, automotive, and medical devices, where tight tolerances and complex geometries are common.
Servizi di fresatura CNC provide several advantages:
Precisione: Fresatura CNC machines can achieve extremely tight tolerances, ensuring that parts are manufactured to exact specifications.
Automazione: Fresatura CNC automates the machining process, reducing the need for manual intervention and minimizing the risk of human error.
Efficienza: Fresatura CNC can significantly reduce production time, especially for complex parts.
Flessibilità: Fresatura CNC can be used to machine a wide range of materials and create complex shapes, making it a versatile manufacturing process.
Nel nostro servizi di fabbricazione, we leverage the power of Fresatura CNC to deliver high-quality parts and components to our clients across various industries. For example, we use Fresatura CNC to manufacture precision components for the robotics industry, where accuracy and repeatability are critical for the proper functioning of robotic systems. Also our servizi di lavorazione include various types of milling, including fresatura frontale.
What is the main difference between face milling and peripheral milling?
The main difference lies in the orientation of the taglierina and the location of the bordo di taglio. In fresatura frontale, il taglierina is perpendicular to the workpiece, and the cutting teeth are on the face of the tool. In fresatura periferica, il taglierina is parallel to the workpiece, and the cutting teeth are on the circumference.
When should I use a face mill instead of an end mill?
Use a mulino frontale when you need to create a large, flat surface quickly and efficiently. Use an fresa a candela for creating complex shapes, slots, or contours, or when machining the edges of a workpiece.
What are the advantages of using climb milling in face milling operations?
Climb milling, where the taglierina rotates in the same direction as the feed, often produces a better surface finish and reduces tool wear compared to conventional milling.
How can I improve the surface finish when face milling?
To improve the surface finish, consider using a mulino frontale with more teeth, reducing the feed rate, using climb milling, and ensuring proper chip evacuation.
What factors should I consider when selecting a face mill cutter?
Key factors include the workpiece material, the diameter of the mulino frontale, the number of teeth, and the geometry of the inserts.
What type of CNC milling machine is typically used for face milling?
Vertical milling machines are commonly used for fresatura frontale. These machines have a vertically oriented spindle that holds the face mill cutter.
Ecco le cose più importanti da ricordare fresatura frontale e fresatura periferica:
Fresatura frontale is used to create flat surfaces, while fresatura periferica is used to shape edges and create contours.
The orientation of the taglierina and the location of the bordo di taglio are the primary differences between the two methods.
Scegliere il giusto taglierina and optimizing cutting parameters are crucial for successful face milling.
Fresatura frontale offers advantages such as efficiency, high-quality surface finish, versatility, and cost-effectiveness.
Servizi di fresatura CNC play a vital role in modern manufacturing by providing precision, automation, and efficiency.
Comprendere le sfumature di fresatura frontale e fresatura periferica can significantly improve machining outcomes.
My company provides comprehensive Servizi di fabbricazione CNC, tra cui fresatura frontale, to meet the diverse needs of various industries.
For any assemblea operations, or any fresatura frontale operations, feel free to contact us for consultation.
By understanding the principles and best practices of fresatura frontale e fresatura periferica, you can optimize your machining processes, improve product quality, and enhance your overall manufacturing efficiency. Remember, the right choice between fresatura frontale e fresatura periferica depends on the specific requirements of your project. With careful consideration and the right tools, you can achieve exceptional results in your machining endeavors.
Scoprite le ultime tendenze e gli ultimi fatti sulla fabbricazione dei CNC dal nostro blog.
Shenzhen Runkey Precision Technology Co. Ltd, una consociata del Gruppo Tensun, è la vostra soluzione unica di fiducia per la produzione personalizzata, dalla prototipazione alla produzione. Trasformate la vostra idea in realtà con risorse di produzione digitale, processi semplificati, guida esperta, tempi accelerati e qualità senza compromessi.
©2024. CNC Fabrication Tutti i diritti riservati.