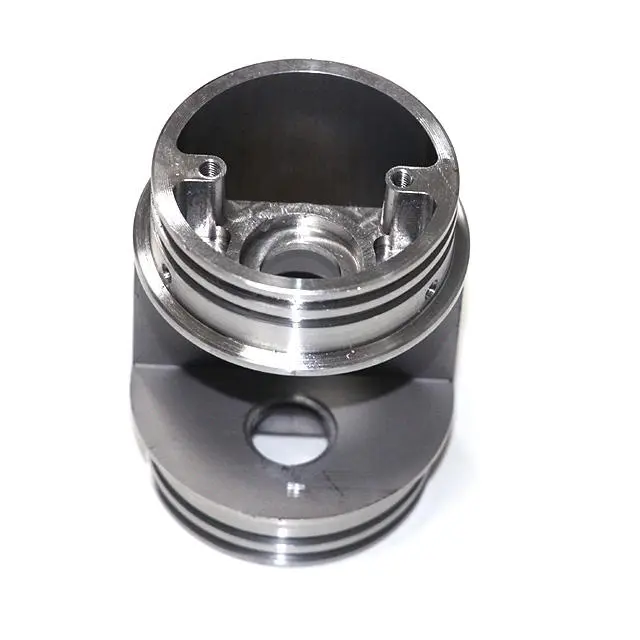
Climb Milling vs. Conventional Milling: Choosing the Best CNC Machining Method
목차
소개
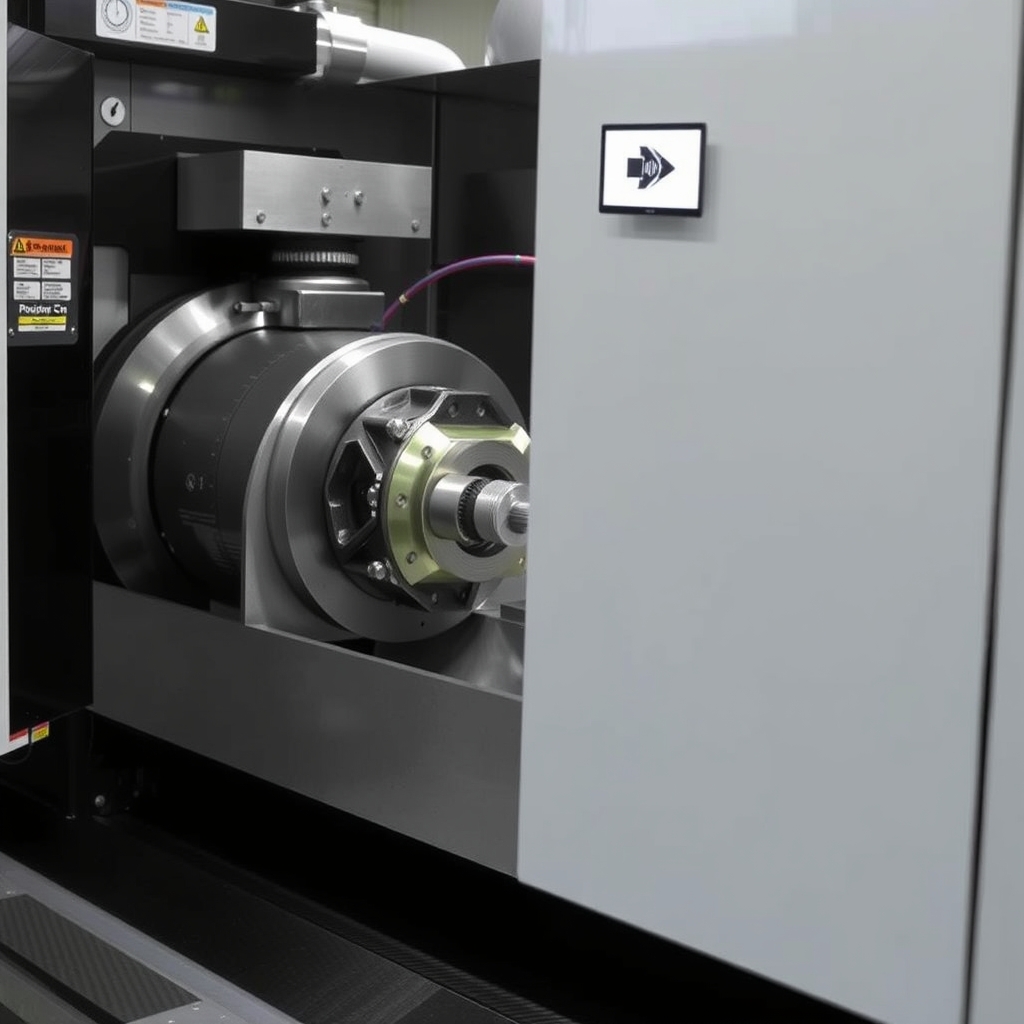
Why Milling Direction Matters in Modern Manufacturing
Milling isn’t just cutting metal—it’s about maximizing performance. The choice between climb (down) and conventional (up) milling impacts:
- Surface finish quality
- Tool longevity
- Machining speed
- Workpiece stability
With industries like 항공우주, 자동차및 의료 기기 demanding micron-level precision, selecting the optimal method is non-negotiable.
Understanding Climb Milling: Precision Meets Efficiency
What is Climb Milling?
Climb milling, or down milling, involves the cutter rotating in the same direction as the workpiece feed. This method starts with maximum chip thickness, reducing friction and heat for smoother cuts.
Key Advantages of Climb Milling
- Superior surface finishes: Ideal for visible components in 소비자 제품.
- 50% longer tool life: Reduced heat and friction.
- Faster feed rates: Boosts productivity in high-volume projects like 자동차 부품.
- Efficient chip evacuation: Prevents recutting.
Limitations to Watch For
- Requires 최신 CNC 기계 with backlash control.
- Unsuitable for rough or uneven surfaces.
- Risk of tool pull-in on older equipment.
Conventional Milling: Stability for Tough Materials
How Conventional Milling Works
In conventional (up) milling, the cutter rotates against the feed direction. It’s ideal for rough surfaces, castings, and manual machines.
Why Choose Conventional Milling?
- Handles hardened materials: Perfect for 산업 장비 컴포넌트입니다.
- Safer for manual machines: No tool pull-in risk.
- Better for deep cuts: Up to 1x cutter diameter.
Drawbacks to Consider
- Poorer surface finish due to chip recutting.
- Higher tool wear from friction.
Climb vs. Conventional Milling: Head-to-Head Comparison
팩터 | Climb Milling | Conventional Milling |
---|---|---|
Chip Thickness | Starts thick, tapers to zero | Starts thin, increases gradually |
도구 수명 | Longer (less heat) | Shorter (more friction) |
Workpiece Forces | Downward (stabilizing) | Upward (requires strong clamping) |
최상의 대상 | Soft metals, finishing passes | Hard materials, roughing |
7 Factors to Determine Your Milling Strategy
- 재료 경도: Soft metals (e.g., aluminum) favor climb; hardened steels need conventional.
- 머신 유형: Modern CNC vs. manual (CNC 솔루션).
- Surface Finish Needs: Climb for 의료 기기; conventional for rough castings.
- 컷 심도: Shallow (climb) vs. deep (conventional).
- Chip Evacuation: Critical for heat-sensitive materials.
- 도구 편향: Climb requires rigid setups.
- 생산 속도: Climb enables faster cycles.
Case Study: Aerospace Component Machining
A manufacturer of aerospace brackets switched to climb milling on a 5-axis CNC machine, achieving:
- 20% faster cycle times.
- Ra 0.4 µm surface finish (vs. Ra 1.6 µm with conventional).
- 30% reduction in tool replacement costs.
FAQs: Your Milling Questions Answered
Which method is better for titanium alloys?
Climb milling is preferred for titanium’s low thermal conductivity, minimizing heat buildup.
Can I use climb milling on a manual machine?
Avoid it—backlash risks tool pull-in. Stick to conventional milling for safety.
How does material thickness affect the choice?
Thin materials (<6 mm) benefit from climb milling’s stabilizing forces.
Is conventional milling outdated?
No—it’s indispensable for roughing cast iron or 중장비 부품.
주요 내용
- Climb milling excels in precision, speed, and finish quality.
- Conventional milling offers control for hard materials and older machines.
- Match the method to your 재료, machine및 production goals.
Ready to optimize your CNC operations? 문의하기 for tailored machining solutions!
댓글
우수 제품 사례
태그
관련 블로그
블로그에서 CNC 제작에 대한 최신 트렌드와 사실을 확인하세요.