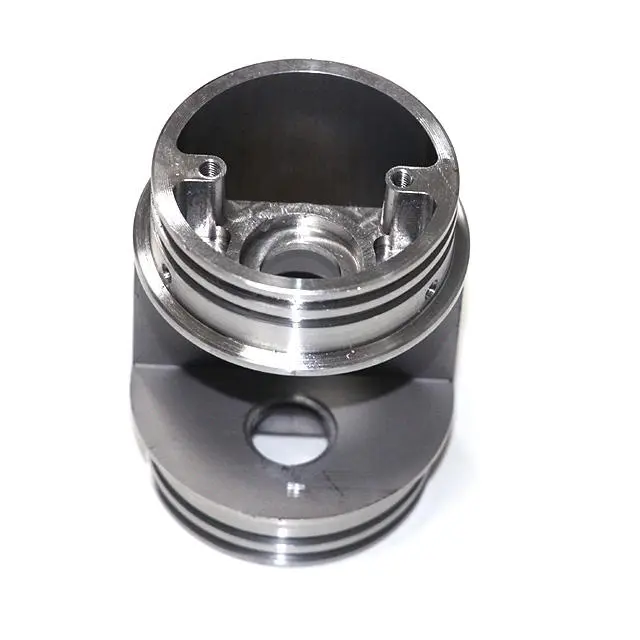
블랙 아노다이즈 알루미늄에 대해 알아야 할 모든 것
목차
소개
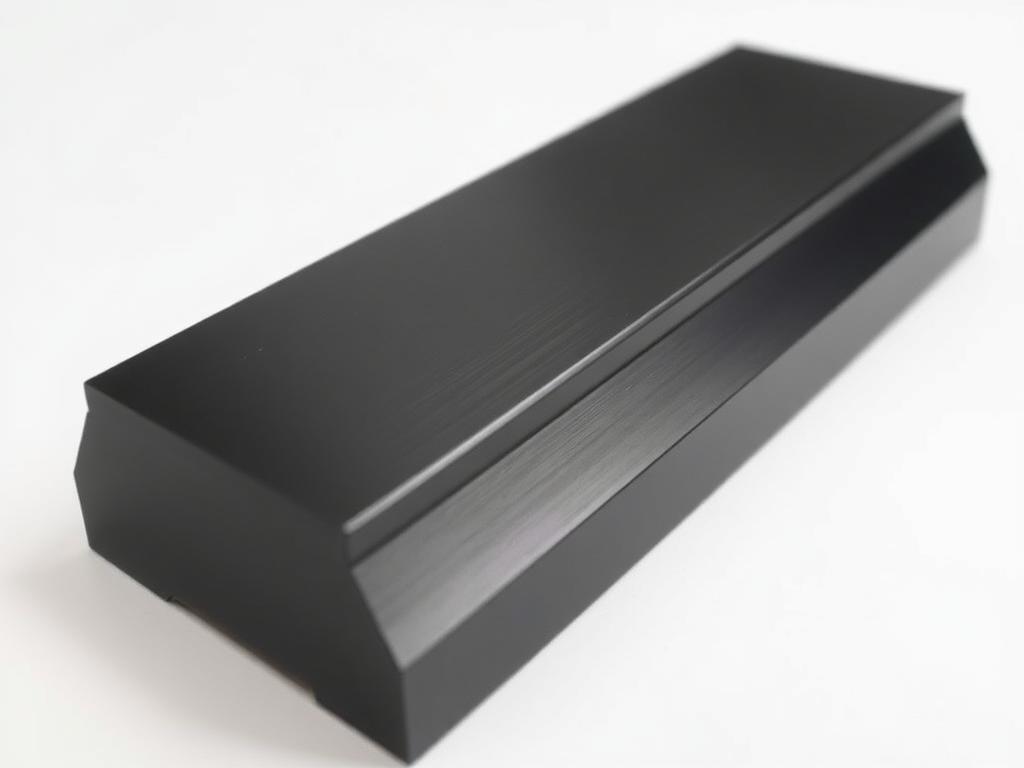
블랙 아노다이즈란 무엇이며 왜 중요한가요?
블랙 아노다이즈 은 내구성이 뛰어나고 매력적이며 오래 지속되는 특수 아노다이징 유형입니다. 블랙 마감 을 알루미늄 부품에 적용합니다. 표준 알루미늄과 달리, 블랙 아노다이징 알루미늄 는 내식성, 내마모성, 방열성이 향상되었습니다. 단순히 미관상의 문제만이 아닙니다. 아노다이징 공정 는 알루미늄 산화물 층 에서 알루미늄 부품의 표면를 사용하여 성능과 내구성을 크게 향상시켰습니다. 항공 우주부터 소비재에 이르기까지 다양한 산업 분야에서 기능적, 시각적 이점을 제공하는 독특한 조합으로 인기를 얻고 있습니다.
제품용 CNC 제조 서비스 제조 공장으로서, 당사는 원재료의 가공을 전문으로 합니다. 알루미늄 고품질의 완성품으로 제작합니다. 당사의 전문성은 다음과 같은 다양한 산업 분야에 걸쳐 있습니다. 항공우주 및 항공, 자동차, 의료 기기, 전자, 방위 및 군사, 산업 장비, 등을 제공합니다. 최적의 제품 성능을 달성하는 데 있어 소재 선택과 표면 처리의 중요성을 잘 알고 있습니다.
블랙 아노다이징 공정은 어떻게 진행되나요?
그리고 블랙 아노다이징 공정 는 복잡한 전기 화학 공정 를 변환하는 알루미늄 표면 를 내구성 있고 부식에 강한 양극산화물 마감 처리합니다. 작동 원리는 다음과 같습니다:
준비: 그리고 알루미늄 부품 에 방해가 될 수 있는 오염 물질을 제거하기 위해 세척 및 전처리됩니다. 아노다이징 공정. 이는 균일하고 높은 품질을 보장하기 위한 중요한 단계입니다. 아노다이징 마감.
아노다이징: 그리고 알루미늄 부품이 잠긴 상태 를 일반적으로 황산이 포함된 전해질 욕조에 넣습니다. 전류가 수조를 통과하여 알루미늄 부품 양극 역할을 합니다. 이렇게 하면 전해질에서 산소 이온이 방출되어 표면의 알루미늄 원자와 결합하여 다음을 형성합니다. 알루미늄 산화물.
염색: 의 주요 기능 중 하나는 블랙 아노다이즈 은 일반 알루미늄과 달리 염료를 흡수하는 능력이 뛰어납니다. 이후 아노다이징 공정은 원하는 두께의 알루미늄 산화물 층이 포함된 염료 욕조에 부품을 담근 후 검은색 염료. 의 다공성 특성으로 인해 양극 산화 처리된 레이어 를 사용하면 검은색 염료 를 사용하여 알루미늄 부품의 표면.
봉인: 마지막 단계는 씰링 프로세스의 모공을 닫아주는 알루미늄 산화물 레이어를 가두어 내부 검은색 염료 내구성이 뛰어나고 오래 지속되는 블랙 마감. 이 단계는 내식성 및 내마모성을 극대화하는 데 매우 중요합니다. 블랙 아노다이징 알루미늄.
블랙 아노다이징 알루미늄의 장점은 무엇인가요?
블랙 아노다이징 알루미늄 제공 양극산화 처리된 알루미늄의 특성은 다양한 응용 분야에 매력적인 선택이 될 수 있는 광범위한 이점을 제공합니다. 다음은 몇 가지 주요 장점입니다:
향상된 내식성: 그리고 양극 산화 처리된 레이어 은 표준 알루미늄에 비해 부식에 대한 탁월한 보호 기능을 제공합니다. 이는 열악한 환경에서 특히 중요합니다. 알루미늄 부품 는 습기, 화학 물질 또는 염수 분무에 노출될 수 있습니다.
향상된 내마모성: 블랙 아노다이징 알루미늄 는 마모와 마모에 강한 단단하고 내구성 있는 표면을 가지고 있습니다. 따라서 마찰이나 기계적 스트레스를 받는 부품에 이상적입니다.
미적 매력: 그리고 딥 블랙 알루미늄 표면의 색상은 검은색 코팅으로 향상시킬 수 있습니다. 블랙 아노다이징 알루미늄 는 시각적으로 매력적이며 제품의 외관을 향상시킬 수 있습니다. 이는 미관을 중요하게 고려하는 소비재 및 건축 분야에서 특히 중요합니다.
열 발산: 블랙 아노다이징 알루미늄 은 베어 알루미늄에 비해 방열 특성이 향상되어 열 관리가 중요한 애플리케이션에 유용할 수 있습니다.
전기 절연: 그리고 양극 코팅 는 전기 절연성이 있어 절연이 필요한 전자 애플리케이션에 유용할 수 있습니다.
표면 경도: 흔히 하드 아노다이징이라고 불리는 타입 III 아노다이징은 알루미늄 표면을 강철처럼 단단하게 만듭니다.
블랙 아노다이징의 다른 유형은 무엇인가요?
'블랙 아노다이징'은 일반적으로 알루미늄에 검은색 양극산화 코팅을 만드는 공정을 말하지만, 이 범주 안에는 다양한 변형이 있습니다. 두 가지 일반적인 블랙의 종류 아노다이징이 있습니다:
타입 II 아노다이징: 이것은 반다공성 알루미늄 산화물 층을 제공하는 알루미늄 아노다이징의 가장 일반적인 방법입니다. 알루미늄 아노다이징 상온에서 황산 욕조를 사용해야 합니다. 타입 II 아노다이징 더 얇은 양극 산화 처리된 레이어 유형 III에 비해 장식용 또는 중간 정도의 내식성이 필요한 경우에 자주 사용됩니다.
유형 III 아노다이징(하드 아노다이징): 이 공정은 타입 II보다 낮은 온도와 높은 전류 밀도를 사용하므로 더 두껍고 단단합니다. 양극 산화 처리된 레이어. 타입 III 아노다이징 는 내마모성과 내식성이 뛰어나며 항공우주 및 군사 부품을 비롯한 까다로운 응용 분야의 기능성 부품에 자주 사용됩니다. 타입 III 아노다이징은 타입 II 아노다이징보다 비용이 더 높습니다.
알루미늄 시리즈 5 와 6은 일반적으로 블랙 아노다이징 아노다이징 특성이 뛰어나기 때문입니다.
블랙 아노다이징은 블랙 산화물 코팅과 어떻게 다릅니까?
흑산화물 코팅은 알루미늄 부품에 보호막을 만드는 데 널리 사용되는 방법입니다. 및 블랙 아노다이징 는 흔히 사용되는 두 가지 표면 처리입니다. 블랙 마감 금속 부품에 사용됩니다. 그러나 프로세스, 속성 및 응용 분야가 크게 다릅니다.
블랙 산화물 코팅 소재 표면을 마그네타이트(Fe3O4)로 변환합니다. 얇고 균일한 검은색 층을 만드는 화학 공정입니다. 반면에 아노다이징은 프로세스입니다. 성장하는 알루미늄 산화물 층 에서 알루미늄 그 자체로 머티리얼에 필수적인 요소입니다.
다음은 핵심 사항을 요약한 표입니다. 흑색 산화물 코팅의 차이점 및 블랙 아노다이징:
기능 | 흑색 산화물 코팅 | 블랙 아노다이징 |
재료 | 주로 철 금속, 일부 스테인리스 스틸 | 알루미늄 및 그 합금 |
프로세스 | 화학적 변환 | 전기 화학 아노다이징 |
레이어 두께 | 얇음(0.00005″ - 0.0002″) | 더 두껍습니다(유형 III의 경우 0.0001″ - 0.001″ 이상). |
내식성 | 제한적 | 우수 |
내마모성 | 보통 | 특히 유형 III(하드 아노다이징)이 우수합니다. |
경도 | Lower | 유형 III의 경우 하드 크롬에 필적하는 더 높은 수준입니다. |
치수 변경 | 최소 | 치수가 약간 증가함(허용 오차 고려) |
색상 | 블랙 | 블랙염료로 가능한 다른 색상 |
비용 | Lower | 더 높음 |
애플리케이션 | 패스너, 도구, 총기류 | 항공우주, 자동차, 소비재 등 |
블랙 아노다이징 알루미늄의 일반적인 용도는 무엇인가요?
블랙 아노다이징 알루미늄 는 고유한 특성 조합으로 인해 다양한 산업과 애플리케이션에서 사용됩니다. 다음은 몇 가지 일반적인 용도입니다:
항공우주: 항공기 구성 요소구조 부품, 하우징 및 브래킷과 같은 알루미늄 부품은 블랙 아노다이징의 가볍고 부식 방지 및 내마모성 특성의 이점을 누릴 수 있습니다. 블랙 아노다이징 알루미늄.
자동차: 트림 부품, 인테리어 구성 요소 및 언더후드 부품은 다음을 활용할 수 있습니다. 블랙 아노다이징 알루미늄 의 미적 매력과 내구성을 높이 평가합니다.
전자 제품: 방열판, 인클로저 및 패널은 종종 다음 재료로 만들어집니다. 블랙 아노다이징 알루미늄 열 방출 및 전기 절연 특성이 뛰어나기 때문입니다.
소비자 제품: 스포츠 용품부터 주방 가전까지, 블랙 아노다이징 알루미늄 다양한 소비재 제품에 내구성 있고 매력적인 마감을 제공합니다.
군사 및 국방: 총기 구성 요소의 견고함과 내식성을 통해 광학 장비 및 통신 장치의 이점을 누릴 수 있습니다. 블랙 아노다이징 알루미늄.
산업 장비: 기계 부품도구 및 비품을 활용할 수 있습니다. 블랙 아노다이징 알루미늄 내마모성과 까다로운 환경에서의 내구성을 인정받았습니다.
프로젝트에 적합한 아노다이징 공정을 선택하는 방법
적절한 아노다이징 공정 는 프로젝트의 특정 요구 사항에 따라 다릅니다. 다음은 고려해야 할 몇 가지 요소입니다:
Material: 사용 중인 알루미늄 합금이 아노다이징에 적합한지 확인하세요. 알루미늄 시리즈 5와 6이 일반적으로 좋은 선택입니다.
애플리케이션: 부품의 기능적 요구 사항을 결정합니다. 혹독한 환경에 노출되나요? 마모와 마모를 견뎌야 하나요?
미학: 외관이 중요한 경우 원하는 마감과 색상을 고려하세요. 블랙 아노다이즈 는 세련되고 현대적인 외관을 제공합니다.
예산: 유형 III 아노다이징(하드 아노다이징)은 일반적으로 유형 II 아노다이징보다 비용이 더 많이 듭니다.
허용 오차: 다음 사항에 유의하세요. 아노다이징 공정 의 레이어를 추가합니다. 알루미늄 산화물를 사용하면 부품의 치수가 약간 증가합니다. 공차가 엄격한 부품을 설계할 때는 이를 고려해야 합니다.
블랙 아노다이징의 한계는 무엇인가요?
동안 블랙 아노다이징 는 많은 이점을 제공하지만, 그 한계를 인식하는 것이 중요합니다:
색상 페이딩: 동안 검은색 염료 다음에서 사용 블랙 아노다이징 은 일반적으로 안정적이지만 장시간 자외선에 노출되면 시간이 지남에 따라 변색될 수 있습니다. 특히 직사광선에 지속적으로 노출되는 부품의 경우 더욱 그렇습니다.
스크래치 감도: 하지만 양극 산화 처리된 레이어 가 단단해도 긁힐 수 있습니다. 날카로운 물체나 연마재는 마감재를 손상시킬 수 있습니다.
비용: 블랙 아노다이징은 알루미늄 표면에 내구성이 뛰어나고 매력적인 마감을 만들어내는 공정입니다. 는 페인팅이나 파우더 코팅과 같은 다른 표면 처리보다 비용이 더 많이 들 수 있습니다.
모든 알루미늄 합금에는 적합하지 않습니다: 일부 알루미늄 합금은 아노다이징에 적합하지 않습니다. 예를 들어 고구리 합금은 아노다이징이 균일하게 이루어지지 않을 수 있습니다.
검은색 양극산화 알루미늄 부품을 관리하는 방법
적절한 유지 관리는 다음과 같은 제품의 수명을 연장하고 외관을 보존하는 데 도움이 될 수 있습니다. 블랙 아노다이징 알루미늄 부품. 다음은 몇 가지 팁입니다:
정기 청소: 순한 비누와 물로 부품을 정기적으로 청소하세요. 연마성 세제나 독한 화학 물질을 사용하지 마세요. 아노다이징 마감.
긁힘 방지: 취급 또는 설치 시 주의 블랙 알루마이트 부품 을 사용하여 긁힘을 방지하세요. 부드러운 천을 사용하고 날카로운 물체와의 접촉을 피하세요.
자외선 차단: 가능하면 직사광선에 노출되는 것을 제한하여 색이 바래는 것을 최소화하세요. 필요한 경우 자외선 차단 코팅이나 실란트 사용을 고려하세요.
재아노다이징: 경우에 따라 마모되거나 손상된 부품을 다시 아노다이징 처리하는 것이 가능할 수도 있습니다. 그러나 이는 손상 정도와 특정 합금에 따라 달라집니다.
자주 묻는 질문
아노다이징과 흑색산화물 코팅의 차이점은 무엇인가요?
아노다이징은 알루미늄 표면에 알루미늄 산화물 층을 성장시키는 전기 화학적 공정이며, 흑색산화물은 철 금속에 자철석 층을 생성하는 화학적 변환 코팅입니다. 아노다이징은 흑색산화물 코팅보다 내식성과 내마모성이 우수합니다.
모든 알루미늄 합금을 블랙 아노다이징 처리할 수 있나요?
대부분의 알루미늄 합금은 양극산화 처리가 가능하지만, 모든 알루미늄 합금에 적합한 것은 아닙니다. 블랙 아노다이징. 알루미늄 시리즈 5와 6은 아노다이징 특성이 우수하여 일반적으로 사용됩니다. 구리 함량이 높은 합금은 균일하게 아노다이징되지 않을 수 있습니다.
블랙 아노다이징의 아노다이징 층 두께는 얼마나 되나요?
두께는 양극 산화 처리된 레이어 에 따라 달라집니다. 아노다이징 유형 사용. 유형 II 아노다이징은 일반적으로 0.0002인치에서 0.001인치 사이의 층을 생성하는 반면, 유형 III(하드 아노다이징)은 최대 0.002인치 이상의 층을 생성할 수 있습니다. 아노다이징 조정 시간 및 전류 밀도를 통해 레이어 두께를 제어할 수 있습니다.
블랙 아노다이징이 부품의 치수에 영향을 미치나요?
예, 예 아노다이징 공정 의 레이어를 추가합니다. 알루미늄 산화물 를 표면에 추가하면 부품의 치수가 약간 증가합니다. 공차가 엄격한 부품을 설계할 때는 이 점을 고려해야 합니다. 일반적으로 양극 산화 처리된 레이어 양극산화 코팅은 부품의 전체 치수에 두께의 약 절반을 추가합니다.
블랙 알루마이트 처리된 알루미늄 식품은 안전한가요?
예, 양극 산화 처리된 알루미늄을 포함합니다. 블랙 아노다이징 알루미늄는 안전한 식품으로 간주됩니다. 그리고 양극 산화 처리된 레이어 양극산화 처리된 알루미늄의 표면은 불활성이고 독성이 없으며 음식과 반응하지 않습니다. 하지만, 알루미늄 표면의 아노다이징 공정 그리고 사용된 모든 염료는 관련 식품 안전 규정을 준수합니다. 아노다이징 처리된 표면은 부식을 방지하고 알루미늄이 식품으로 침출되는 것을 방지합니다.
블랙 알루마이트 처리된 알루미늄은 얼마나 오래 사용할 수 있나요?
의 수명은 블랙 아노다이징 알루미늄 의 품질 등 여러 요인에 따라 달라집니다. 아노다이징 공정의 두께는 양극 산화 처리된 레이어부품이 사용되는 환경, 부품이 얼마나 잘 관리되는지 등을 고려합니다. 적절한 관리가 필요합니다, 블랙 아노다이징 알루미늄 부품 는 다양한 애플리케이션에서 수년, 심지어 수십 년 동안 지속될 수 있습니다. 고유의 내식성과 내마모성으로 인해 양극 산화 처리된 레이어 수명에 기여합니다.
주요 내용
블랙 아노다이즈 는 전문화된 아노다이징 공정 내구성 있고 매력적이며 오래 지속되는 블랙 마감 알루미늄 부품에
이 공정에는 세척, 아노다이징, 염색 및 밀봉을 통해 단단하고 부식에 강한 표면을 만드는 과정이 포함됩니다. 알루미늄 산화물 층 와 딥 블랙 색상.
블랙 아노다이징 알루미늄 제공 표준 알루미늄에 비해 내식성, 내마모성, 방열성, 심미성이 향상되었습니다.
다양한 블랙의 종류 아노다이징에는 표준 아노다이징, 타입 II, 타입 III(하드 아노다이징) 등 다양한 유형이 있으며, 각각 고유한 특성과 용도가 있습니다.
블랙 아노다이징 은 주로 철 금속에 사용되는 흑색 산화물 코팅과 달리 부식 및 내마모성이 낮습니다.
블랙 아노다이징 알루미늄 는 항공우주, 자동차, 전자제품, 소비재, 군사용 애플리케이션 등 다양한 산업 분야에서 사용됩니다.
올바른 선택 아노다이징 공정 및 유지 관리 블랙 알루마이트 부품 를 적절히 사용하면 수명과 성능을 극대화하는 데 도움이 됩니다.
의 선도적인 제공업체로서 CNC 가공 서비스당사는 다음을 제공합니다. 정밀 가공 및 표면 마감 블랙 아노다이징을 포함한 다양한 솔루션을 제공하여 고객의 다양한 요구를 충족시키고 있습니다.
당사는 다음을 제공합니다. 신속한 프로토타이핑 및 온디맨드 제조 다양한 업계에 적합합니다.
다음과 같은 복잡한 사항을 이해함으로써 블랙 아노다이즈 알루미늄를 통해 다음 프로젝트의 재료 선택과 표면 처리에 대해 정보에 입각한 결정을 내릴 수 있습니다. 항공우주 부품에 내구성 있는 마감이 필요하든, 소비재에 미적으로 만족스러운 코팅이 필요하든 상관없습니다, 블랙 아노다이징 알루미늄 는 성능과 시각적 매력의 독특한 조합을 제공합니다.
댓글
우수 제품 사례
태그
관련 블로그
블로그에서 CNC 제작에 대한 최신 트렌드와 사실을 확인하세요.