온디맨드 CNC 서비스 제조업체
10년 이상 탁월한 CNC 서비스를 제공해 온 온디맨드 제조 분야의 신뢰할 수 있는 리더인 당사에 오신 것을 환영합니다. 우수성을 향한 당사의 노력은 최첨단 기술과 고객의 고유한 제조 요구 사항을 충족하기 위해 헌신하는 고도로 전문적인 팀에 의해 뒷받침됩니다. 당사는 업계 표준을 충족할 뿐만 아니라 고객의 기대를 뛰어넘는 고품질 제품을 제공하는 데 자부심을 가지고 있습니다. 신속한 프로토타이핑, 정밀 가공 또는 맞춤형 솔루션이 필요한지 여부에 관계없이 프로젝트를 제시간에 완벽하게 실행할 수 있도록 도와드립니다. 온디맨드 제조 분야에서 최고의 서비스와 신뢰성을 제공하는 파트너와 함께하세요.
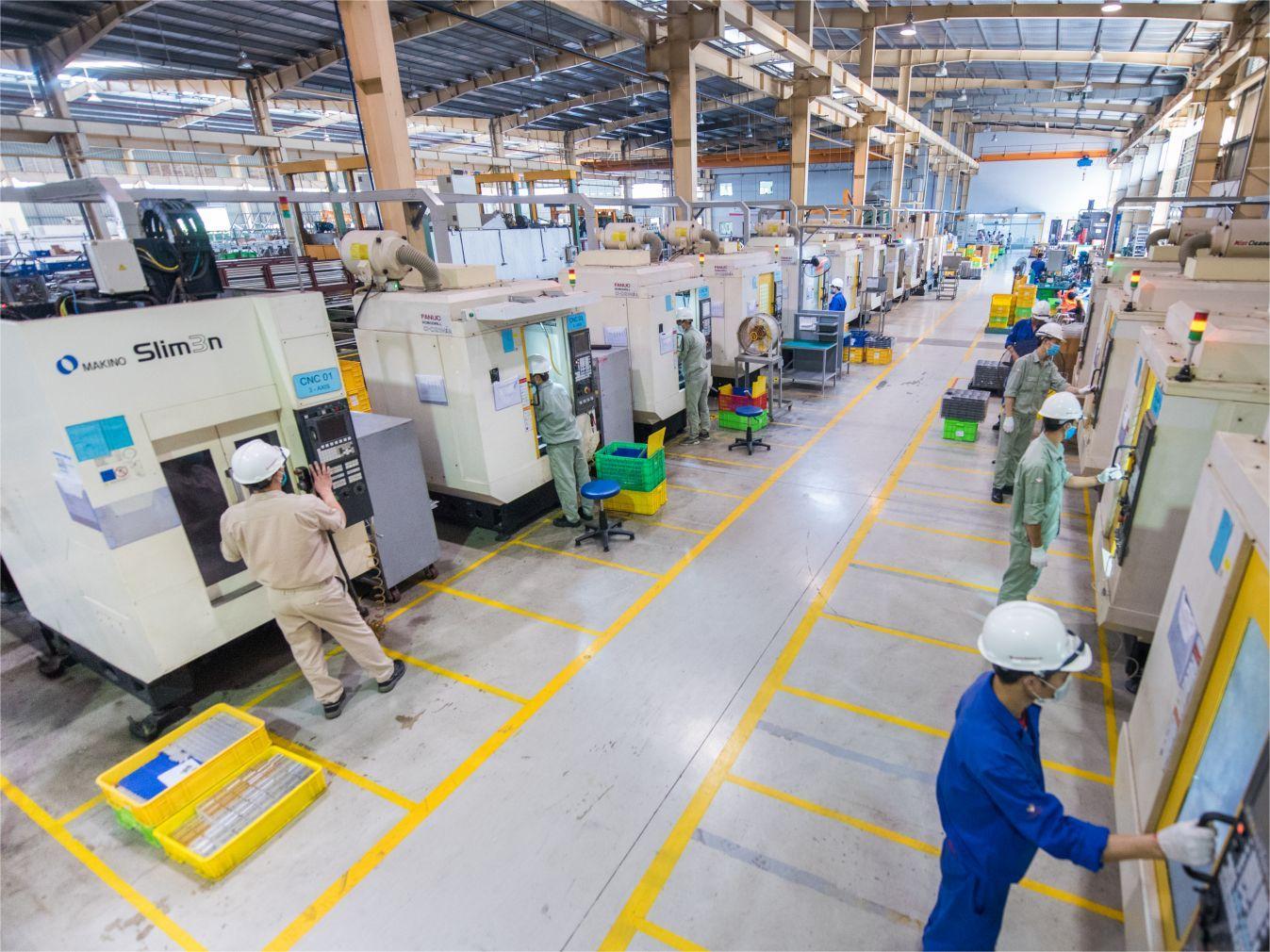
온디맨드 제조란?
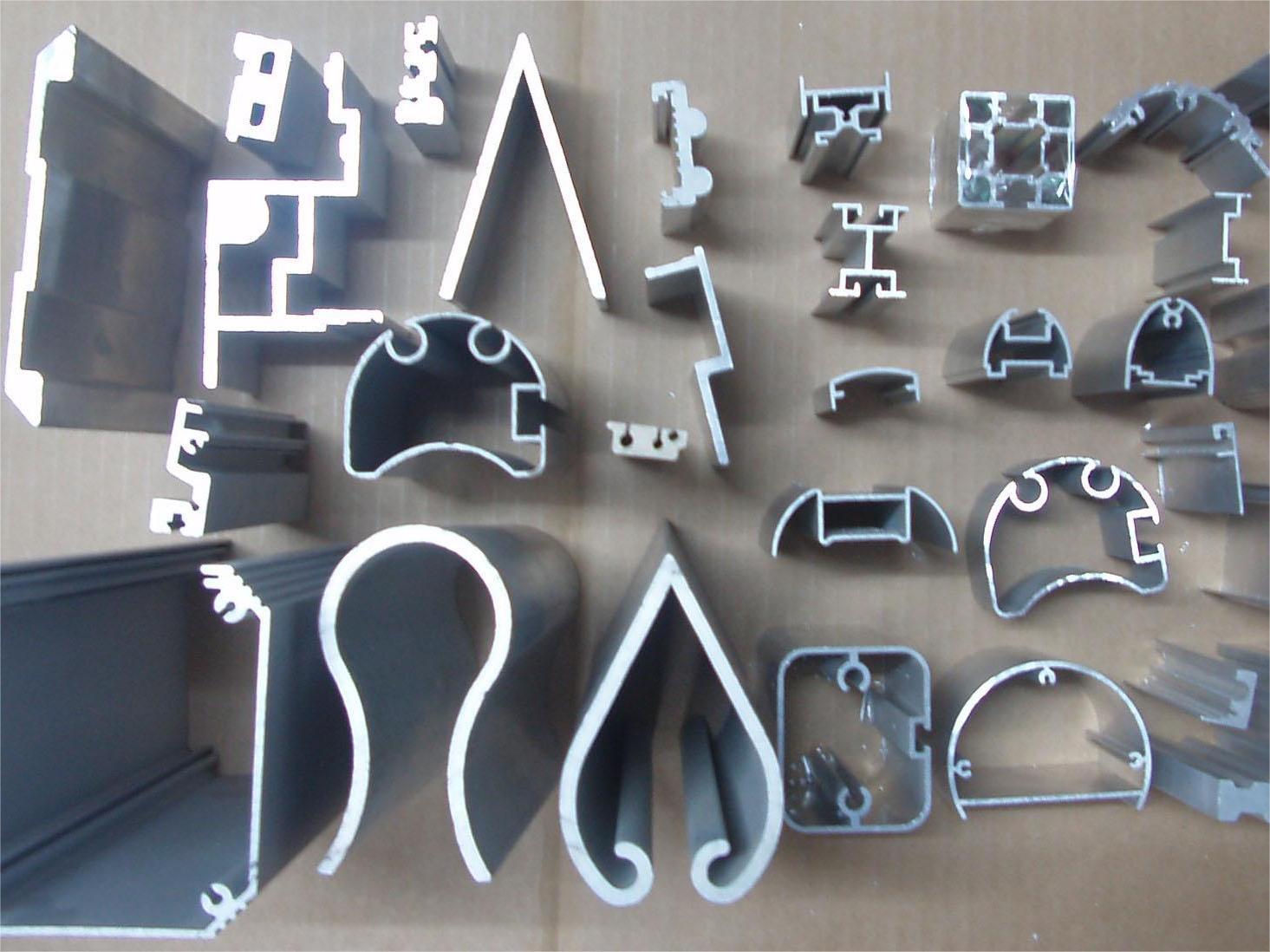
온디맨드 제조는 제품을 대량으로 생산하여 재고로 보관하지 않고 필요한 만큼만 생산하는 생산 프로세스를 말합니다. 이 방식을 통해 기업은 고객의 요구에 신속하게 대응하고 과잉 생산 및 재고 과잉과 관련된 위험을 줄일 수 있으며, 온디맨드 제조의 주요 특징은 다음과 같습니다:
맞춤화: 특정 고객 요구 사항을 충족하도록 제품을 맞춤화할 수 있어 유연성과 개인화가 향상됩니다.
효율성: 필요한 만큼만 생산함으로써 기업은 낭비를 최소화하고 보관 및 미판매 재고와 관련된 비용을 절감할 수 있습니다.
속도: 온디맨드 제조에는 신속한 프로토타이핑과 빠른 처리 시간이 필요한 경우가 많으므로 기업은 제품을 더 빨리 시장에 출시할 수 있습니다.
기술 통합: CNC 가공, 3D 프린팅, 자동화된 워크플로와 같은 고급 기술은 일반적으로 제조 공정을 간소화하고 정밀도를 향상시키는 데 사용됩니다.
지속 가능성: 이 모델은 과잉 생산과 낭비를 줄여 지속 가능한 관행에 부합하므로 더욱 환경 친화적일 수 있습니다.
소니의 온디맨드 프로덕션 서비스
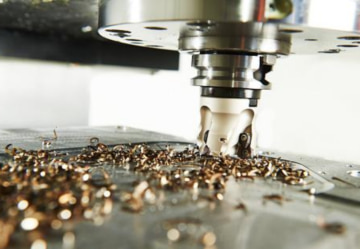
CNC 가공
컴퓨터 제어 도구를 사용하여 다양한 재료로 복잡한 부품을 제작하는 정밀 제조.
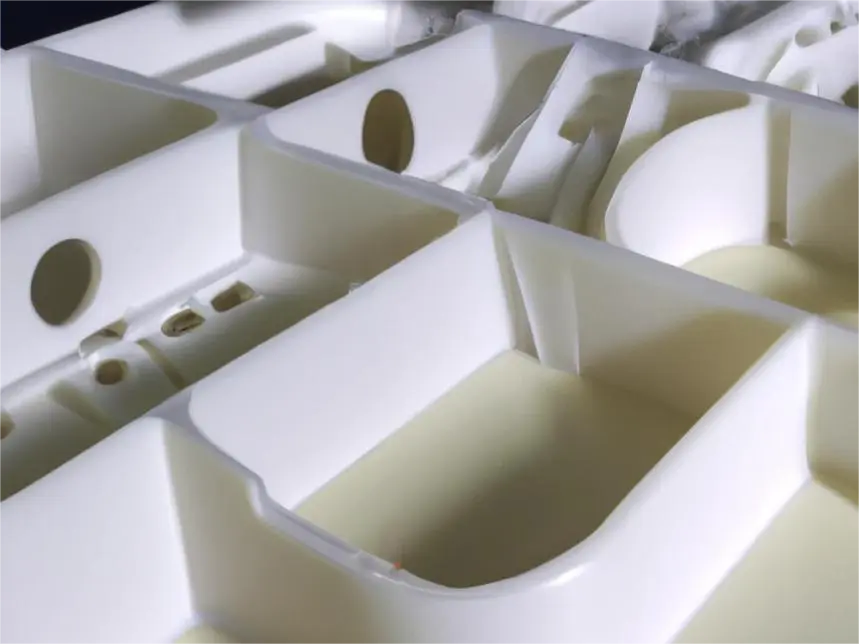
플라스틱 사출 성형
용융된 플라스틱을 금형에 주입하여 플라스틱 부품을 효율적으로 생산할 수 있어 대량 생산에 이상적입니다.
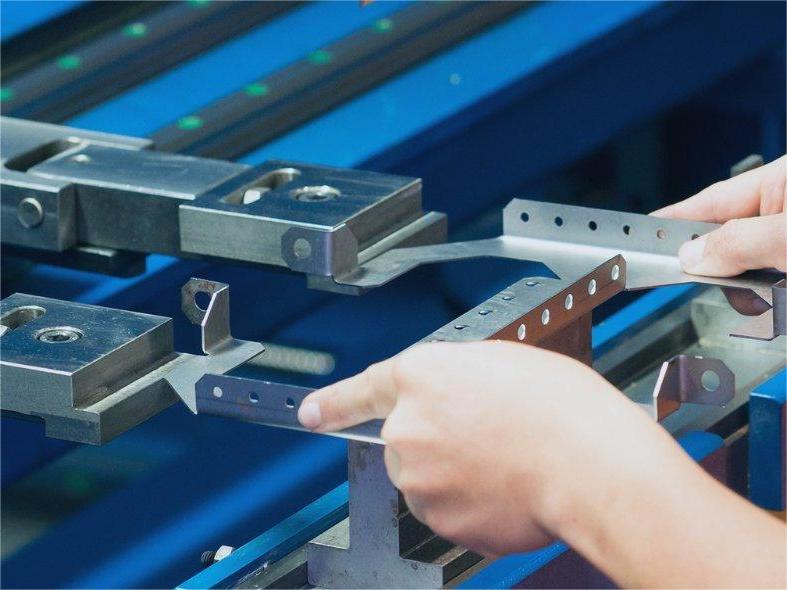
판금 가공
절단 및 절곡과 같은 기술을 통해 다양한 애플리케이션에 적합한 내구성 있는 판금 부품을 제작할 수 있습니다.
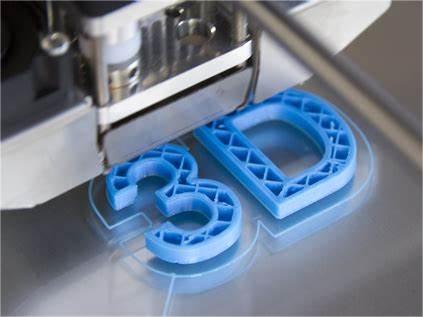
3D 프린팅
부품을 레이어별로 제작하는 적층 제조는 신속한 프로토타입 제작과 복잡한 디자인에 적합합니다.
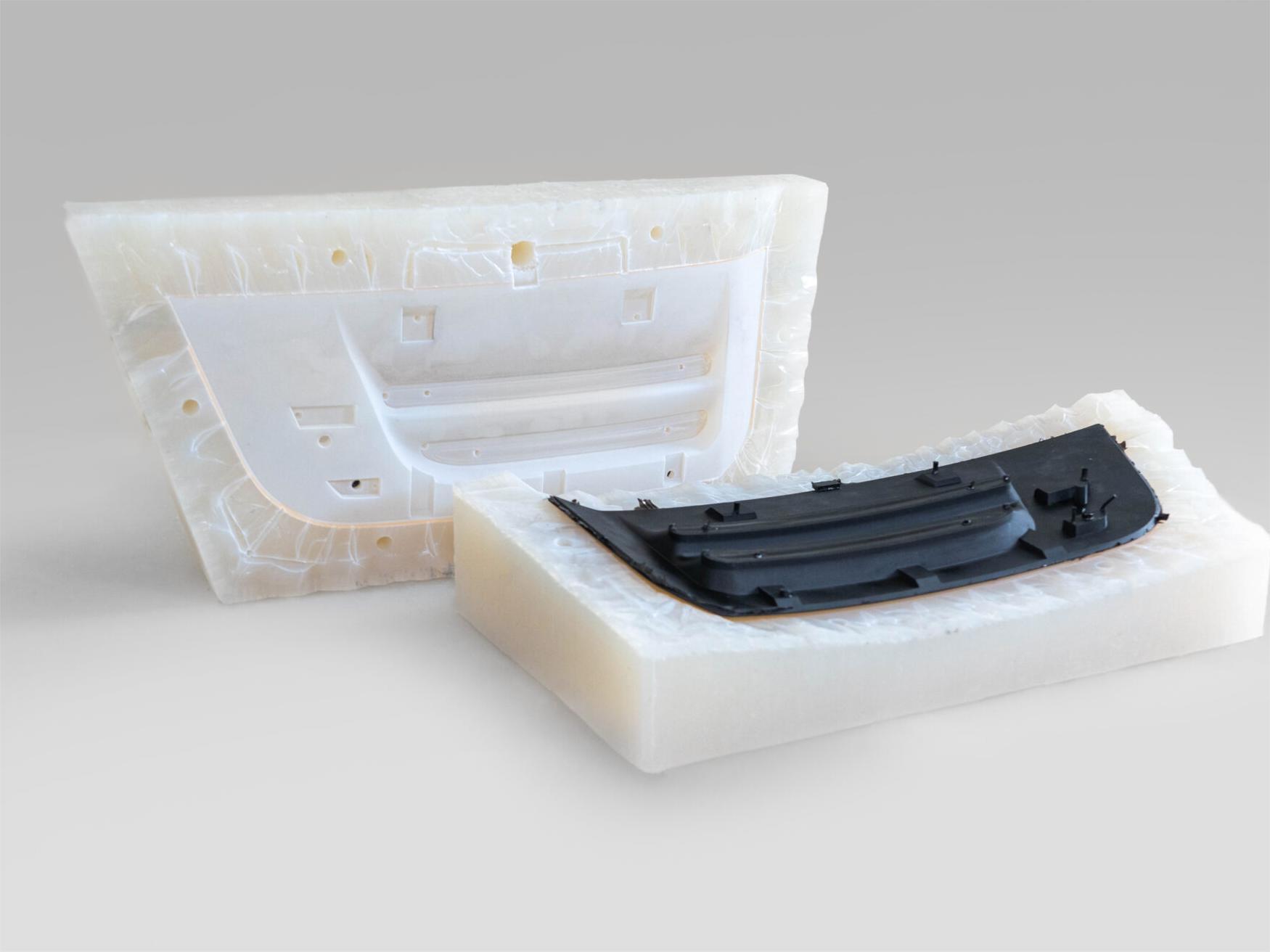
진공 주조
소량 생산이 가능한 고품질 실리콘 몰드로, 섬세한 디테일의 프로토타입 제작에 이상적입니다.
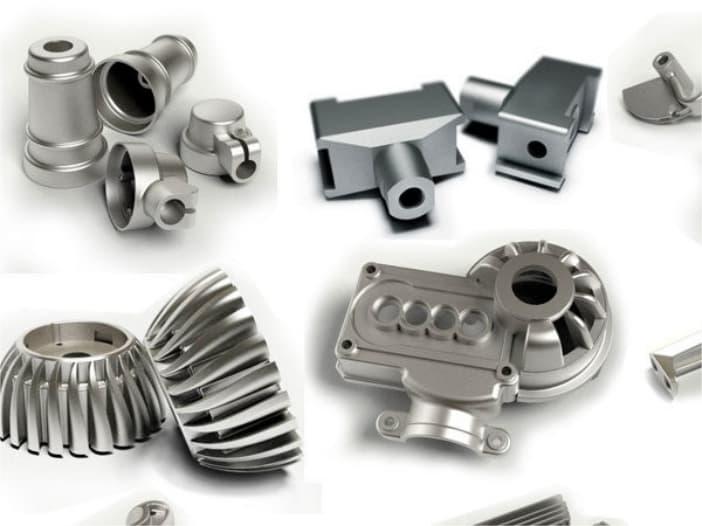
다이 캐스팅
용융 금속을 금형에 고압 사출하여 다양한 산업 분야에 필요한 정밀하고 복잡한 금속 부품을 제작합니다.
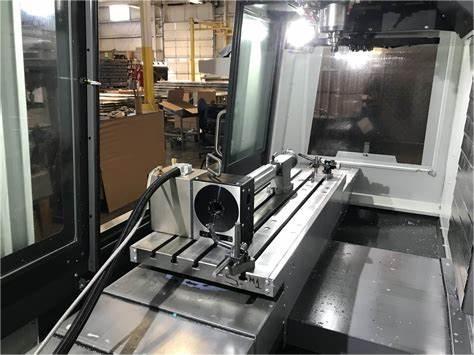
압출
파이프와 프로파일에 일반적으로 사용되는 금형을 통해 재료를 강제로 성형하는 연속 제조 공정입니다.
CNC 가공
CNC 가공 또는 컴퓨터 수치 제어 가공은 다양하고 복잡한 기계를 정밀하게 제어하는 정교한 제조 공정입니다. 고급 소프트웨어와 사전 프로그래밍된 코드를 활용하는 CNC 가공은 생산 장비의 움직임을 전문적으로 관리하여 제조의 높은 정확도와 일관성을 보장합니다.
주요 사양:
선형 치수:
고품질 부품 생산에 이상적인 ±0.025mm(±0.001인치)의 공차로 탁월한 정밀도를 달성할 수 있습니다.
구멍 지름(비 리밍):
구멍 직경이 ±0.025mm(±0.001인치)의 허용 오차를 준수하여 정확도를 유지하여 안정적인 성능을 보장합니다.
샤프트 직경:
공차 ±0.025mm(±0.001인치) 이내의 정밀한 샤프트 직경을 제공하여 엄격한 엔지니어링 요구 사항을 충족합니다.
부품 크기 제한:
당사의 CNC 가공 기능은 최대 950 x 550 x 480mm(37.0 x 21.5 x 18.5인치) 크기의 부품을 수용할 수 있어 다양한 응용 분야에 적합합니다.
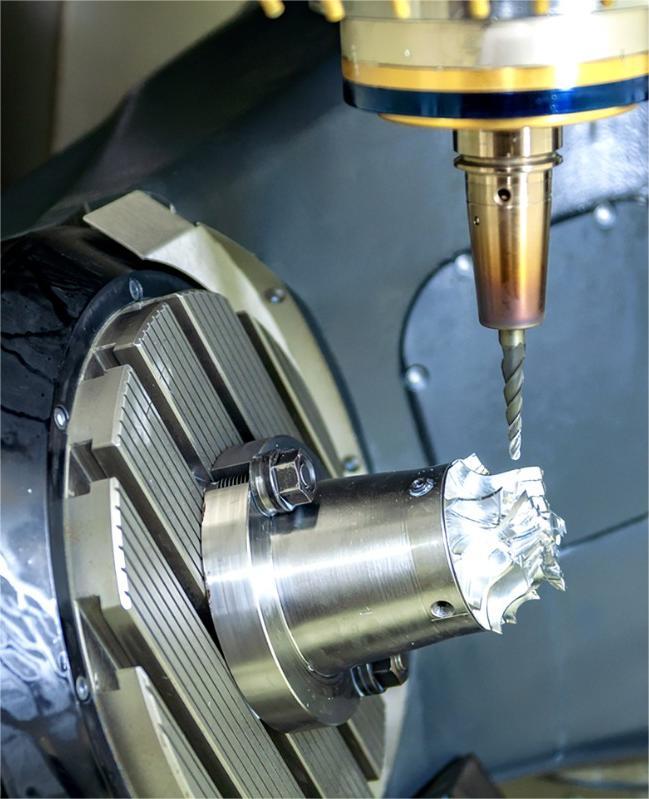
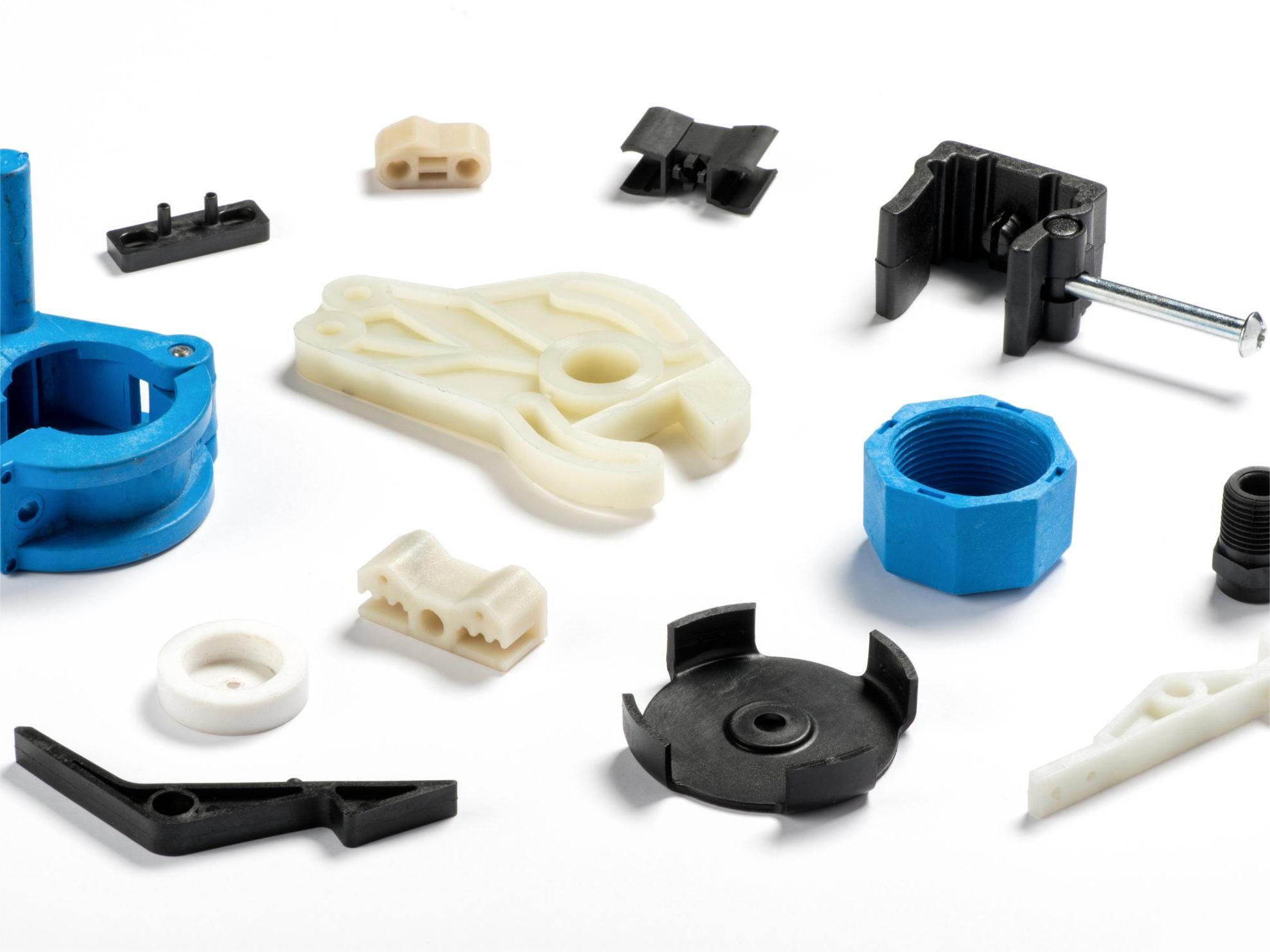
플라스틱 사출 성형
플라스틱 사출 성형은 열경화성 및 열가소성 폴리머 등 플라스틱 수지를 녹여 금형 캐비티에 압력을 가해 주입하는 매우 효율적인 제조 공정입니다. 이 공정을 통해 용융된 플라스틱이 캐비티를 채우고 정밀도와 내구성을 갖춘 최종 제품으로 굳어집니다.
표준 기능:
몰드 캐비티 공차:
0.05mm의 금형 캐비티 공차로 탁월한 정확도를 달성하여 고품질 생산을 보장합니다.
표준 리드 타임:
플라스틱 사출 성형의 표준 리드 타임은 영업일 기준 15일 이내이므로 프로젝트를 신속하게 처리할 수 있습니다.
부품 간 반복성:
부품 간 ±0.1mm의 반복성으로 일관된 품질을 경험하고 각 부품이 고객의 사양을 충족하도록 보장합니다.
프로덕션 등급:
다양한 애플리케이션에 적합한 당사의 생산 능력은 1~10만 사이클 범위로, 소규모 및 대규모 생산 실행을 모두 수용합니다.
판금 제작
판금 제작은 평평한 강철 또는 알루미늄 시트를 내구성 있는 금속 구조물 및 제품으로 변형하는 다목적 제조 공정입니다. 이 공정에는 절단, 펀칭, 접기, 조립 등 다양한 기술이 포함되므로 특정 요구 사항에 맞는 맞춤형 솔루션을 제공할 수 있습니다.
치수 세부 정보:
가장자리 간 / 단일 표면 공차:
가장자리 간, 가장자리와 구멍 간, 구멍과 구멍 간 구성에 대해 ±0.005인치의 허용 오차로 정밀한 측정을 수행합니다.
가장자리/홀 공차까지 굽힘:
벤드 투 엣지 및 벤드 투 홀 공차가 ±0.010인치로 정확도를 유지하여 고품질의 벤드 및 접힘을 보장합니다.
에지 대 피처/다중 표면 공차:
여러 표면에 대해 ±0.030인치의 가장자리-기능 간 공차를 허용하여 복잡한 디자인과 기능을 수용할 수 있습니다.
굽힘 각도 허용 오차:
1°의 굽힘 각도 허용 오차로 정밀한 굽힘을 보장하여 구조적 무결성을 유지하면서 설계의 유연성을 제공합니다.
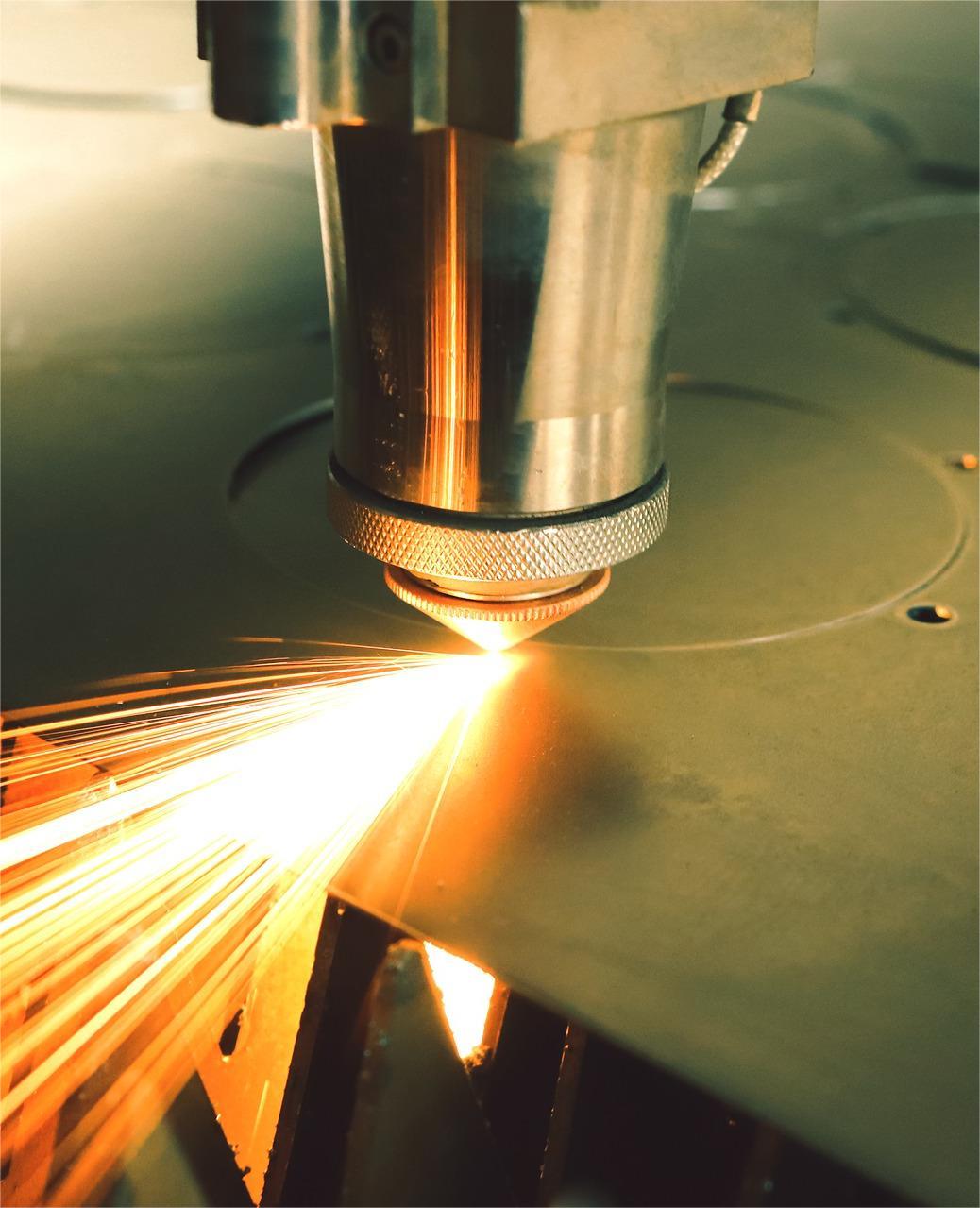
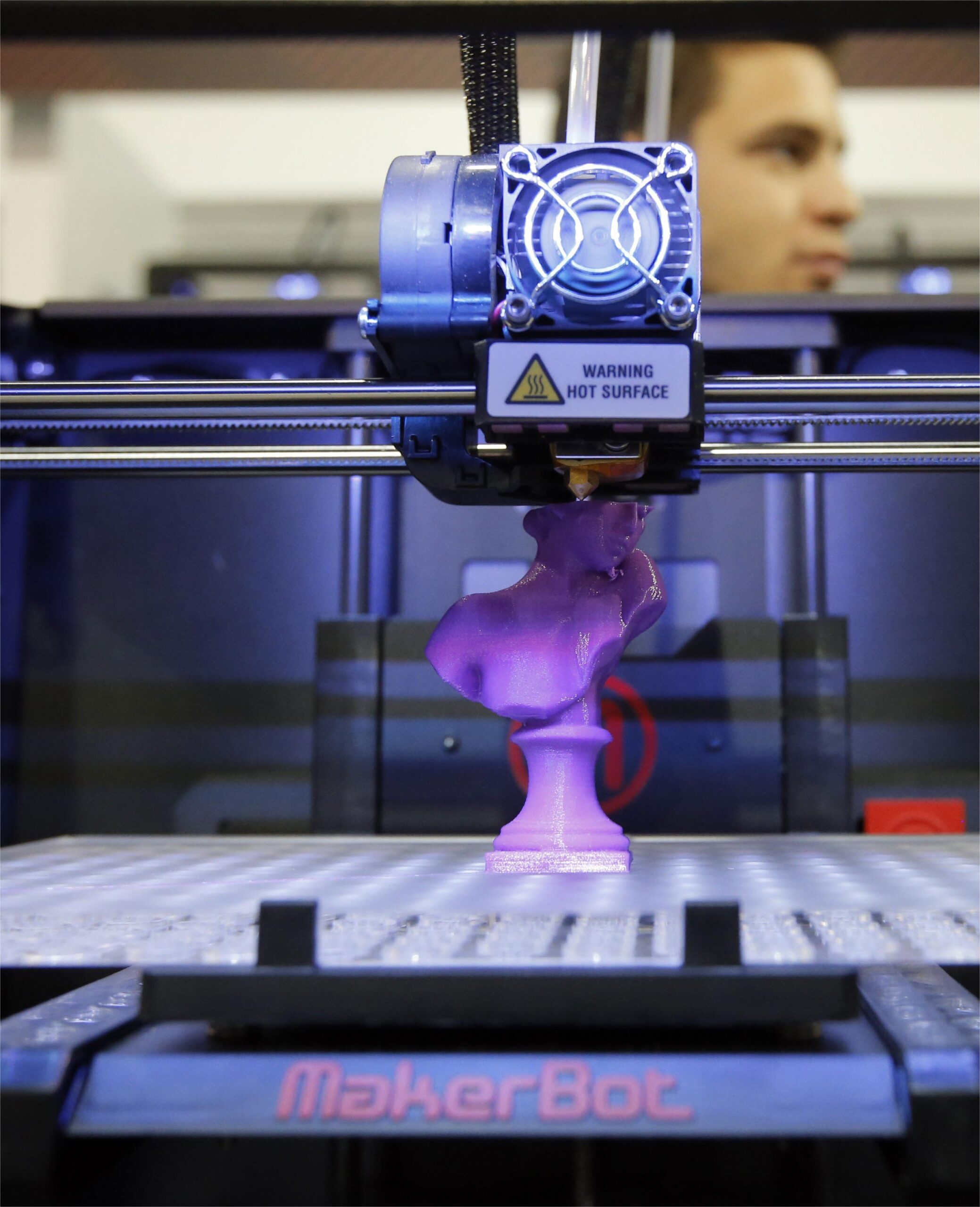
3D 프린팅
적층 제조라고도 하는 3D 프린팅은 디지털 3D 또는 CAD 모델에서 3차원 물체를 만드는 혁신적인 프로세스입니다. 이 다목적 기술을 사용하면 프로토타입을 신속하게 제작하고 복잡한 디자인을 높은 정밀도로 제작할 수 있습니다.
표준 기능:
최대 빌드 크기:
3D 프린팅 서비스는 FDM의 경우 최대 900 x 600 x 900mm, SLA의 경우 최대 1500 x 750 x 500mm, SLS의 경우 750 x 550 x 550mm 등 다양한 제작 크기를 지원하므로 다양한 응용 분야에 활용할 수 있습니다.
표준 리드 타임:
7일 이내에 최대 50개의 부품을 제작할 수 있는 빠른 처리 시간을 경험하고 프로젝트의 적시 납품을 보장하세요.
치수 공차:
0.1mm의 치수 공차로 높은 정확도를 달성하여 각 부품이 고객의 사양을 충족하도록 보장합니다.
벽 두께 공차:
당사의 벽 두께 허용 오차는 FDM의 경우 ±1mm, SLA의 경우 ±0.2mm, SLS의 경우 ±0.7mm로 방식에 따라 다르므로 설계 및 기능에 유연성을 부여할 수 있습니다.
프로덕션 등급:
50개 이상의 부품을 효율적으로 생산할 수 있으므로 3D 프린팅 서비스는 소규모 및 대규모 제조 요구사항에 모두 적합합니다.
진공 주조
진공 주조는 실리콘 몰드와 진공을 활용하여 복잡한 생산 부품을 생산하는 고급 제조 공정입니다. 이 기술을 사용하면 매우 섬세하고 복잡한 부품을 제작할 수 있으므로 프로토타입 제작 및 소량 생산에 이상적입니다.
표준 기능:
최대 빌드 크기:
0.025mm(±0.001인치)의 공차로 정밀한 치수를 구현하여 주조 요구 사항에 맞는 고품질의 결과물을 보장합니다.
표준 리드 타임:
진공 주조 서비스는 최대 20개의 부품을 15일 이내에 납품할 수 있어 프로젝트에 효율적인 처리 시간을 제공합니다.
치수 정확도:
허용 오차 ±0.05mm의 뛰어난 치수 정확도로 각 부품이 정확한 사양을 충족하도록 보장합니다.
레이어 두께:
당사의 진공 주조 공정은 1.5mm에서 2.5mm에 이르는 층 두께를 허용하여 다양한 디자인 요구 사항을 수용합니다.
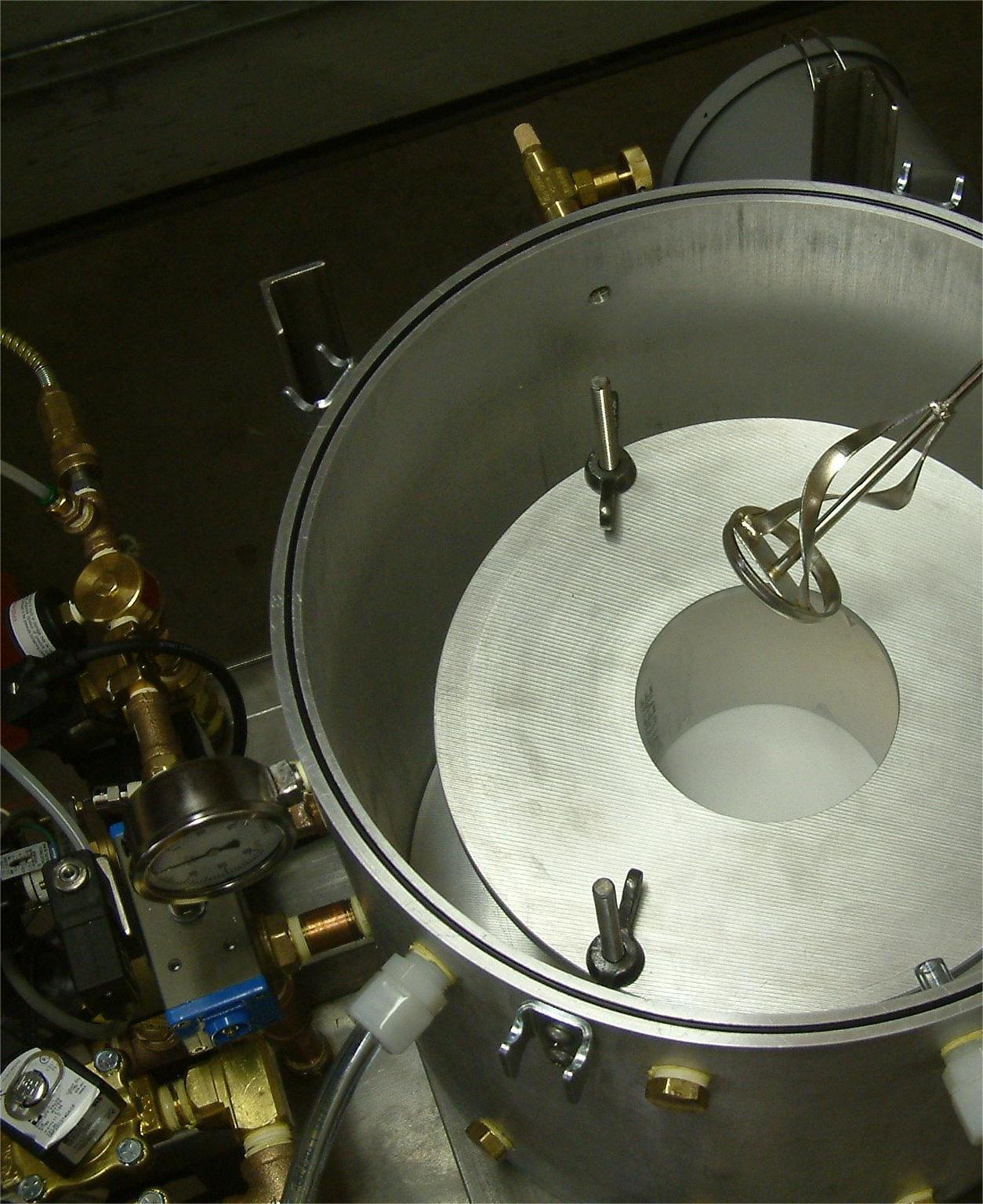
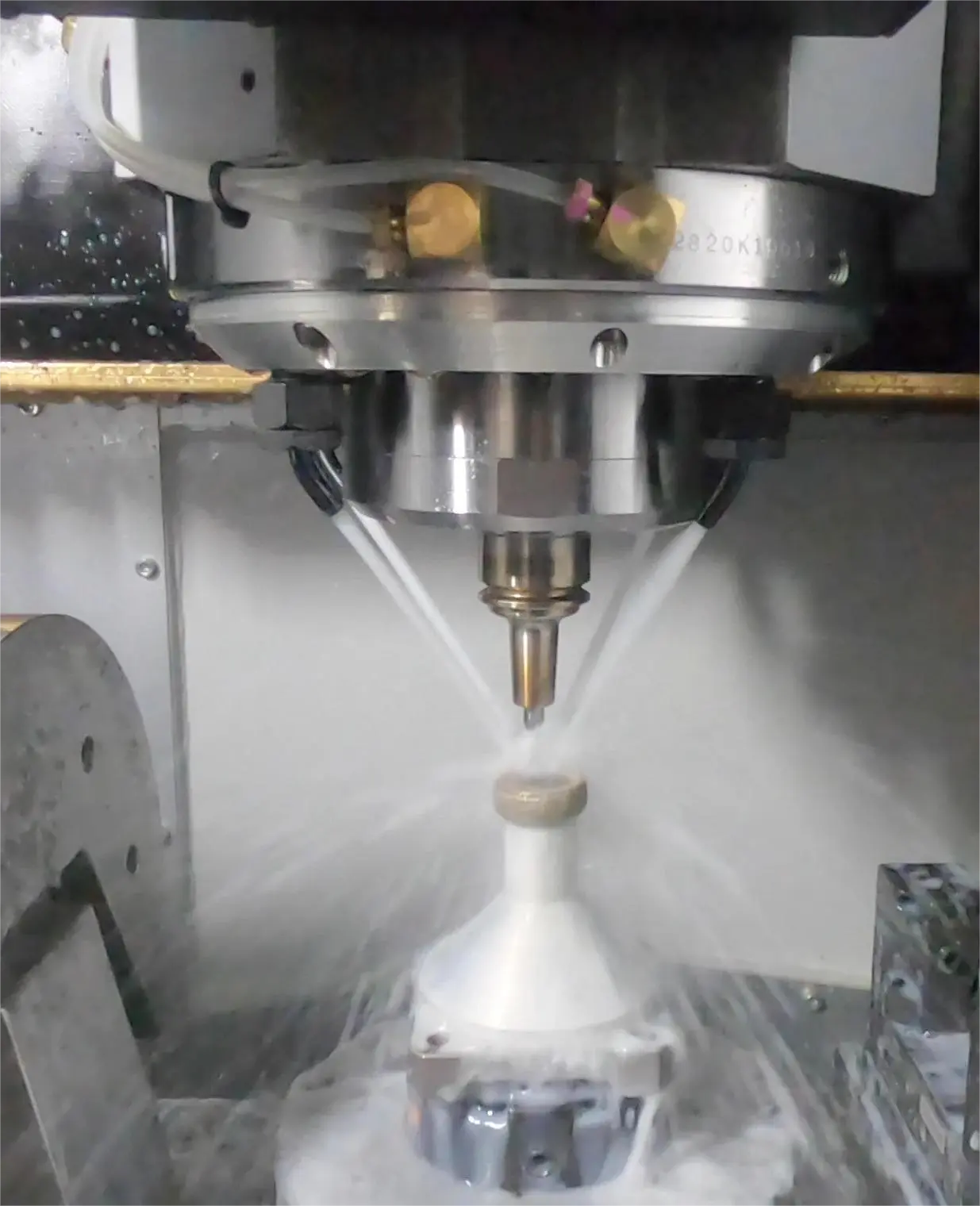
다이 캐스팅
다이캐스팅은 용융 금속을 강철 주형에 붓거나 강제로 주입하여 내구성이 뛰어나고 정밀한 다양한 부품을 만드는 매우 효율적인 제조 공정입니다. 이 방법은 표면 마감과 치수 정확도가 뛰어난 복잡한 형상을 제작하는 데 이상적입니다.
표준 기능:
최대 빌드 크기:
다이캐스팅 서비스는 최대 300mm × 650mm의 제작 크기를 수용할 수 있어 고객의 사양에 맞는 다양한 부품을 제작할 수 있습니다.
표준 리드 타임:
최대 20개의 부품을 15일 이내에 배송할 수 있으므로 제작 기한을 맞출 수 있도록 신속하게 처리할 수 있습니다.
치수 정확도:
±0.05mm의 치수 정확도로 높은 정밀도를 달성하여 각 부품이 설계 요구 사항에 완벽하게 맞도록 보장합니다.
레이어 두께:
당사의 다이캐스팅 공정은 1.5mm에서 2.5mm의 레이어 두께를 지원하므로 다양한 애플리케이션에 적합합니다.
압출
압출은 소성 변형을 통해 복잡한 부품을 성형하는 다목적 제조 공정입니다. 이 과정에서 재료는 다이 또는 오리피스를 통해 강제로 흐르게 되어 특정 애플리케이션에 맞는 맞춤형 프로파일과 모양이 만들어집니다.
표준 기능:
크기를 누릅니다:
당사의 압출 서비스는 다양한 생산 요구 사항을 수용하는 450T에서 3000T에 이르는 프레스 크기를 활용합니다.
표준 리드 타임:
작은 금형의 경우 2주, 큰 금형의 경우 4주의 표준 리드 타임을 제공하여 프로젝트의 적시 납기를 보장합니다.
최소 주문량:
최소 주문량은 소형 기계의 경우 알루미늄 0.5톤, 대형 기계의 경우 6063 알루미늄 1.0톤으로, 다양한 생산 요구에 유연하게 대응할 수 있습니다.
후처리 서비스:
당사는 CNC 절단, 나사 가공, 슬롯 가공, 페이스 밀링 등 포괄적인 후가공 옵션을 제공하여 압출 부품의 기능성과 정밀도를 향상시킵니다.
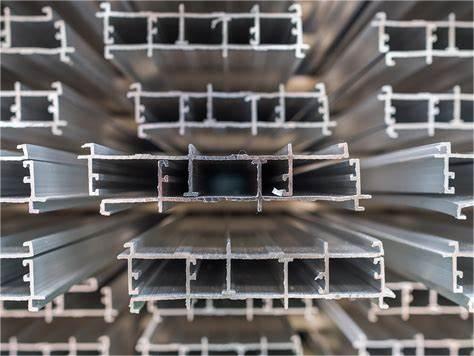
온디맨드 제조를 특별하게 만드는 특징
맞춤형 솔루션
당사는 고객의 특정 요구 사항을 충족하는 맞춤형 제조를 전문으로 하며, 모든 제품이 고객의 고유한 사양과 선호도에 맞게 설계되도록 보장합니다.
신속한 처리
당사의 첨단 생산 역량을 통해 고품질의 제품을 신속하게 제공할 수 있습니다. 당사는 시장의 긴급성을 이해하고 품질 저하 없이 리드 타임을 최소화하기 위해 노력하고 있습니다.
최첨단 기술
당사는 CNC 가공 및 3D 프린팅을 비롯한 최신 제조 기술을 활용하여 정밀도와 효율성을 높이고 복잡한 디자인을 쉽게 제작할 수 있습니다.
품질 보증
전문가로 구성된 전담 팀이 제조 공정의 모든 단계에서 엄격한 품질 검사를 실시하여 업계 표준을 충족하는 최고 품질의 제품만을 제공합니다.
온디맨드 제조 서비스 FAQ
온디맨드 제조는 필요할 때만 제품을 생산하는 생산 모델로, 고객 맞춤화가 가능하고 과잉 재고를 줄일 수 있습니다. 이 접근 방식은 기업이 낭비를 최소화하면서 고객의 요구에 신속하게 대응하는 데 도움이 됩니다.
온디맨드 제조는 필요한 만큼만 생산하기 때문에 판매되지 않은 재고를 보관하는 데 드는 비용을 절감할 수 있습니다. 또한 생산 프로세스를 간소화하여 인건비와 재료비를 절감할 수 있습니다.
예! 온디맨드 제조의 주요 이점 중 하나는 특정 요구 사항에 따라 제품을 맞춤화할 수 있다는 점입니다. 각 제품이 고객의 고유한 사양을 충족할 수 있도록 고객과 긴밀히 협력합니다.
리드 타임은 주문의 복잡성과 수량에 따라 달라질 수 있습니다. 하지만 첨단 생산 역량을 통해 고품질의 제품을 몇 주가 아닌 며칠 내에 신속하게 배송할 수 있습니다.
당사는 설계 및 생산 계획을 위해 CNC 가공, 3D 프린팅, 고급 소프트웨어와 같은 첨단 기술을 활용합니다. 이를 통해 제조 공정에서 높은 정밀도와 효율성을 달성할 수 있습니다.
품질 보증 을 최우선으로 생각합니다. 모든 제품이 업계 표준과 고객의 기대치를 충족할 수 있도록 각 단계의 검사 및 테스트를 포함하여 제조 공정 전반에 걸쳐 엄격한 품질 관리 조치를 시행합니다.
온디맨드 제조에 관한 블로그
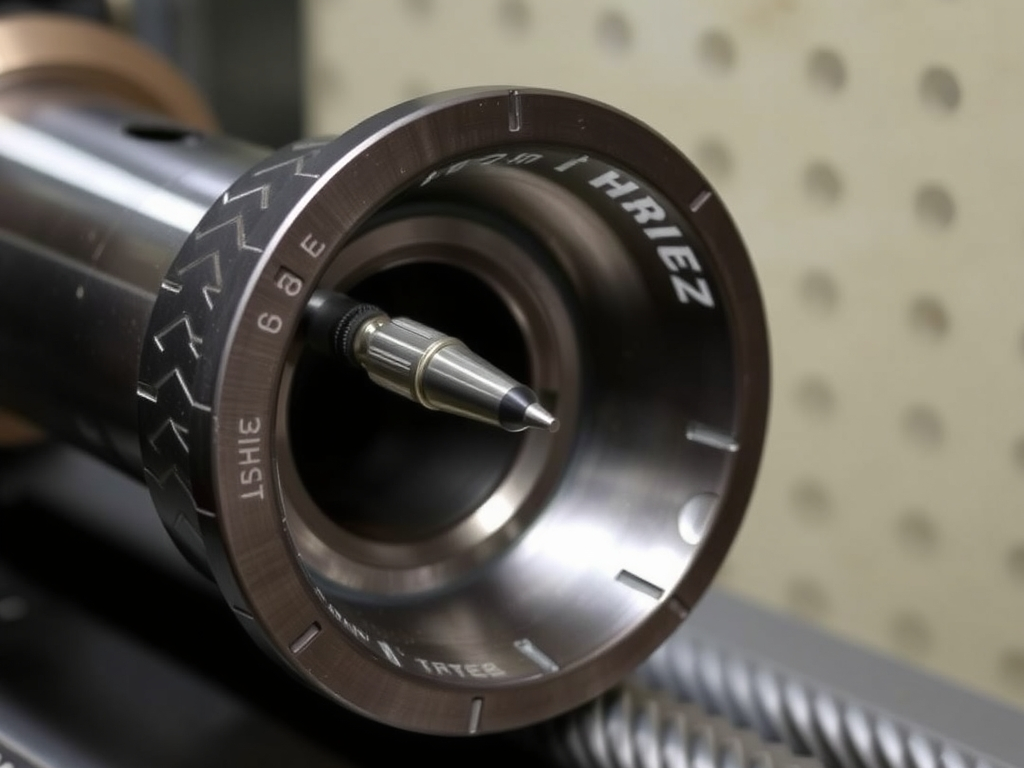
리밍 기술 마스터하기: 정밀 가공에 대한 종합 가이드
이 문서에서는 정밀한 홀 크기와 우수한 표면 마감을 얻기 위한 중요한 가공 작업인 리밍의 복잡성에 대해 자세히 설명합니다. 이 가이드는 숙련된 기계 기술자든 이 분야를 처음 접하는 사람이든 상관없이 올바른 리머 선택, 다양한 리머 유형 이해, 최적의 결과를 위한 리밍 프로세스 숙달에 대한 귀중한 통찰력을 제공합니다.
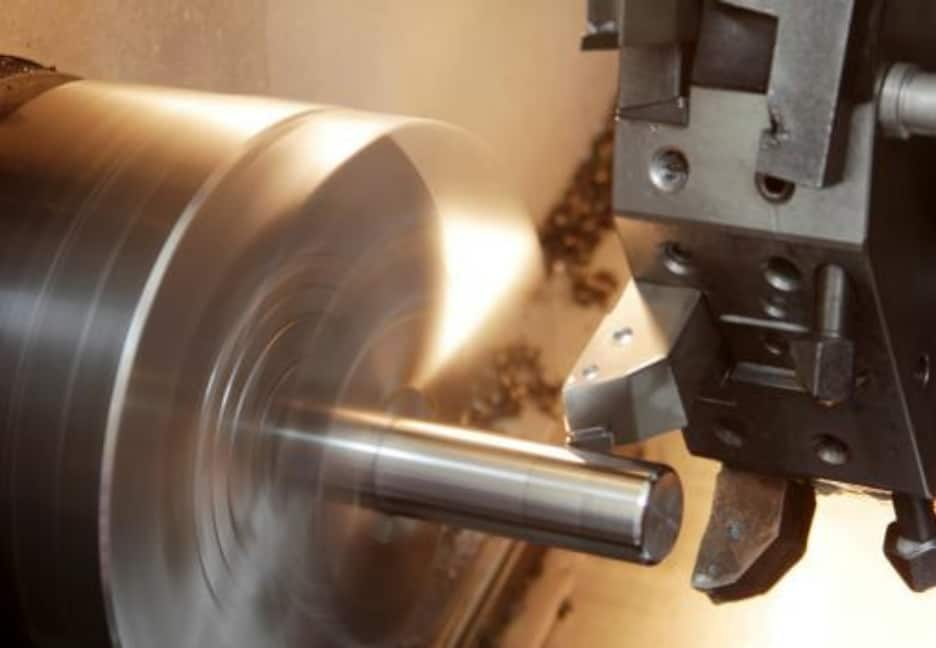
CNC 기계: 최신 제조에 대해 알아야 할 모든 것
제조업의 세계는 CNC 기계의 등장으로 혁명을 맞이했습니다. 컴퓨터 수치 제어의 약자인 이 놀라운 엔지니어링 기술은 작은 전자 부품부터 거대한 항공우주 부품까지 모든 것을 만드는 방식을 변화시켰습니다. 이 글에서는 CNC 가공의 역사, 다양한 유형의 기계, 관련 프로세스, 현대 제조업에서 CNC 가공이 중요한 이유에 대해 알아보는 복잡한 여정을 안내합니다. 물건이 어떻게 만들어지는지 궁금하거나 기계 가공 업계에서 경력을 쌓고 싶다면 꼭 읽어보시기 바랍니다.
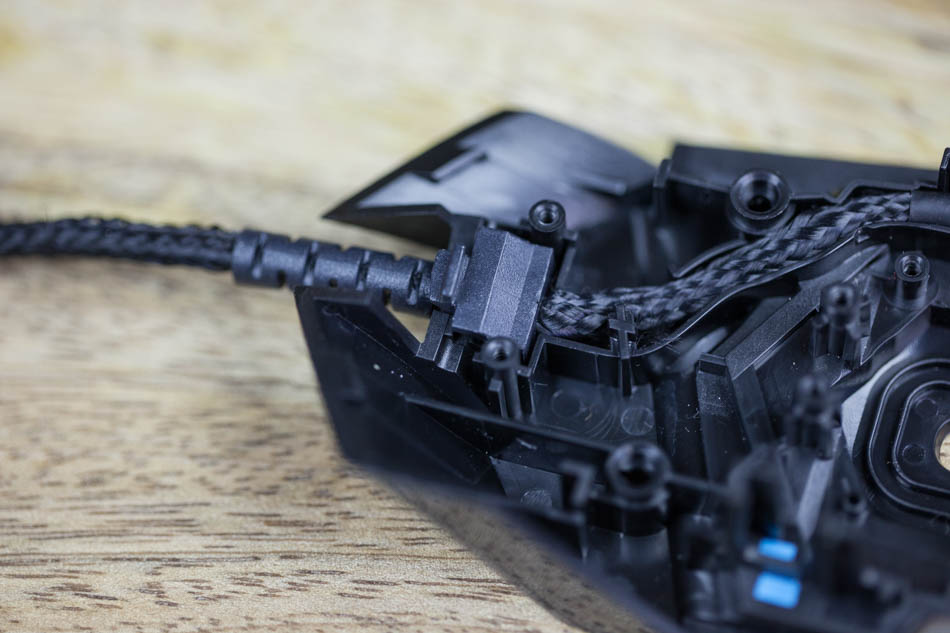
케이블 디자인 마스터하기: 내구성 및 심미적 매력을 위한 팁
기술이 넘쳐나는 세상에서 내구성과 미적 매력을 겸비한 케이블을 디자인하는 것은 모든 산업에 필수적입니다. 항공우주, 가전제품, 로봇 공학 등 어떤 분야에서든 견고하고 시각적으로 매력적인 케이블을 만들면 제품 품질을 크게 향상시킬 수 있습니다. 이 포괄적인 가이드는 케이블을 견고하고 보기 좋게 만들기 위한 설계 팁과 전략을 안내합니다.