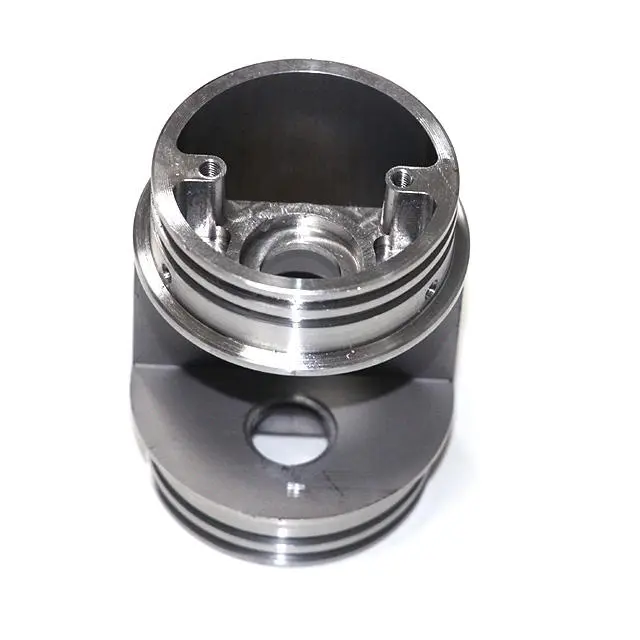
- +8615586668226
- [email protected]
- Nr. 30, Hongbang industripark, Shenzhen
Anodisere er en elektrokjemisk prosess that enhances the natural oxide layer on the surface of metals, especially aluminium. Unlike paint or plating, anodizing creates a thin, durable anodisert lag that is actually integrated into the metal itself. This process is important because it not only improves the appearance of metal parts by offering various color options, but it also increases their resistance to wear, corrosion, and abrasion. Think of anodizing to improve the longevity and performance of your aluminiumskomponenter. Essentially, it provides a protective layer that extends the life of aluminum and its alloys, which are crucial in countless applications.
Betydningen av anodisere can’t be overstated. Without it, aluminiumsdeler would be much more vulnerable to damage from everyday use and environmental factors. The anodiseringsprosessen makes aluminum suitable for a wider range of applications that require robust performance in challenging conditions. This is why anodizing is also a crucial step in many etterbehandlingsprosess for aluminiumsdeler. It is not just about looks; it is about adding real, tangible value to aluminiumskomponenter, ensuring their long-term reliability and performance.
Now, let’s focus on hard coat anodize, sometimes also referred to as hard anodizing or type III, which takes the benefits of regular anodizing to a whole new level. While both methods enhance the natural oxide layer on aluminum, hard coat anodize results in a significantly thicker, denser, and much more durable anodisert belegg. Hard anodize er ofte known as type iii anodizing and is designed for applications where extreme wear and tear resistance are required. Think of it as the “heavy-duty” version of regular anodisere.
The primary difference lies in the thickness of the coating. Regular anodizing, often referred to as type II, creates a relatively thin coating. Hard coat anodizing, on the other hand, produces a much thicker layer – usually between 0.0005 and 0.004 inches, sometimes even more. This increased beleggets tykkelse translates to enhanced hardness, superior wear resistance, better corrosion protection, and improved electrical insulation. Unlike a standard anodized surface, a hard anodic layer provides significantly greater protection and is vital when aluminiumsdeler need to withstand harsh conditions. Hard coat anodize is the go-to option for components that must perform under high stress and abrasive environments.
Den hard coat anodizing process is an intricate elektrokjemisk prosess that involves immersing aluminiumsdeler in a specially formulated anodizing bath. An electrical current is then passed through the bath, causing a controlled oxidation of the aluminiumsoverflate. This creates a dense, hard anodic layer of aluminiumoksid. The key difference lies in the specific parameters of this anodiseringsprosessen . Hard coat anodizing employs a lower temperature and higher current density compared to regular anodizing, allowing the growth of a thicker and harder anodisert lag.
Den process of hard coat anodizing is meticulously controlled to ensure consistent tykkelse and quality. The temperature of the anodizing bath, the chemical composition of the electrolyte, and the current density are all carefully monitored. This control allows for the creation of a robust, uniform coating of aluminum oxide across the entire aluminiumsdel. Hard coat anodizing is performed to create a coating that is not just on the overflaten av aluminium but rather an integral part of it, growing outward from the original metal overflate. This process is optimized to create a dense anodic coating of aluminum which provides maximum protection.
When talking about specifications of hard coat, we need to consider several key factors. The most important parameter is the tykkelse. As mentioned, hard coat anodize typically achieves a coating tykkelse of 0.0005 to 0.004 inches or more. The exact tykkelse will depend on the type of aluminum used, the specific application, and customer needs. Also, the aluminiumslegering type also influences the final results of the anodiseringsprosessen.
Another vital specification is the hardness of the anodisert lag. En typisk hard coat anodized aluminum surface will have a hardness ranging from 400 to 600 Vickers, making it exceptionally resistant to scratching and abrasion. Further, the coating’s uniformity, density, and adherence are carefully measured to ensure it meets the required performance criteria. The specifications of hard coat anodizing also address the corrosion resistance and wear properties under specific conditions. These factors are crucial in determining the overall quality of hard coat anodizing.
The exceptional durability and wear resistance of hard coat anodize make it ideal for a wide range of applications. In the aerospace industry, hard anodized aluminum is used for components like hydraulic cylinders, gears, and structural elements that need to withstand extreme temperatures, pressures, and abrasive conditions. In the automotive sector, you’ll find it used for pistons, brake components, and other parts that endure high levels of friction and heat. The applications of hard are vast and diverse, demonstrating the value of this treatment.
Dessuten.., hard coat anodizing is used extensively in the defense and military industries for weapons components, missile parts, and other critical applications. In medical devices, anodisert aluminium provides biocompatible, corrosion-resistant components. Industrial equipment benefits from hard coat anodizing to improve the longevity of wear parts, while consumer products, like high-end cookware, use it for its durability and scratch resistance. These examples illustrate how hard coat anodizing provides superior protection across various sectors and that the applications of hard coat anodizing are numerous and crucial.
Image of an aluminum part undergoing anodization
The fundamental difference between hard coat with regular anodize lies in the resulting anodisert lag. Regular anodizing is generally used for enhancing aesthetic appeal and providing a basic level of corrosion resistance. It is best suited for aluminiumsdeler that do not experience harsh wear. The anodisert lag produsert av standard anodizing is typically thin, somewhere between 0.0001 and 0.001 inches. This is why regular aluminum anodizing has limitations when it comes to handling extreme friction and demanding environments.
Motsatt, hard coat anodize aims for maximum durability and wear resistance and it is often referred to as type iii hard coat anodizing. De beleggets tykkelse achieved through this hard coat anodizing process is significantly higher. The hard coat anodizing process ensures superior corrosion and abrasion resistance making it ideal for components subjected to intense use. Also, regular anodizing offers a wider array of color options sammenlignet med hard coat anodizing. De color of aluminum after hard anodize may be more limited. In summary, think of regular anodize of aluminum as a basic protective finish while hard coat anodize is used for specialized applications requiring the highest level of performance.
Several factors can influence the effectiveness of hard coat anodizing. De type of aluminum, as well as its composition, plays a crucial role. Different aluminum alloys and the thickness av anodisert lag will react differently during the anodiseringsprosessen og annerledes aluminiumslegeringer will require slightly different anodizing parameters to get the desired beleggets tykkelse and hardness. The chemical composition of the anodizing bath is another essential factor to control. The temperature of the anodizing bath must be carefully maintained as well.
Additionally, the current density applied during the anodiseringsprosessen, as well as the duration of the anodizing process, has a major impact on the formation of the anodisert belegg. Improper control can result in inconsistent thickness, inadequate hardness, and reduced corrosion resistance. Finally, the quality of hard coat anodizing is influenced by the pre-treatment process, and proper cleaning of the aluminiumsoverflate before anodizing involves removing impurities and oxides, which is crucial for optimal results.
Den hard coat anodizing process involves multiple steps, each of which is vital to producing a high-quality coating. First, aluminiumsdeler are meticulously cleaned to remove all dirt, oil, and other contaminants. This step is crucial to ensure that the anodisert lag adheres properly. Next, the aluminiumskomponenter are placed in an anodizing bath containing a specific electrolyte. Once submerged, electrical current is applied to the aluminiumsdel.
The electrochemical reaction begins as the current flows through the bath, causing anodizing creates en aluminiumoksidlag. The temperature of the electrolyte is carefully controlled throughout the process of hard coat anodizing. This ensures the creation of a dense, hard layer of aluminum oxide on the surface. After anodisering, the parts are rinsed to remove any residual chemicals. The process often involves sealing the pores in the aluminum oxide to enhance corrosion resistance and improve the finish. This comprehensive, step-by-step approach guarantees high-quality hard coat anodizing.
Den benefits of hard coat anodizing are numerous and significant. Primarily, it provides exceptional wear and abrasion resistance. The thick and dense anodisert belegg is far less susceptible to scratching, chipping, and other forms of mechanical damage. This is a critical factor in applications where components are exposed to frequent use or harsh conditions. Moreover, hard coat anodizing offers outstanding corrosion resistance. The oxide layer acts as a barrier, preventing the underlying metal from coming into contact with corrosive elements.
Another key benefit is the enhanced electrical insulation properties, making hard anodized aluminum suitable for various electronics applications. In addition, hard coat anodizing provides a uniform, smooth surface that can improve the aesthetic appeal of aluminiumsdeler while also having excellent thermal and wear properties. Finally, the durability of the anodisert belegg extends the lifespan of aluminiumskomponenter, leading to cost savings in the long run. These are significant advantages, demonstrating why hard coat anodizing is also a crucial process.
Despite the many advantages of hard coat anodizing, there are also a few limitations to consider. Firstly, the anodizing process can be more expensive than standard anodizing due to the longer processing times and more stringent control parameters. Also, the range of colors available for hard coat anodizing is generally more limited than with regular anodisering. The thicker anodisert lag can also lead to dimensional changes that may need to be accounted for when designing parts.
Videre er effectiveness of hard coat anodizing can be affected by the type of aluminum used. Certain aluminiumslegeringer are more suitable than others for hard coating, and the desired tykkelse av anodisert lag may not be achievable with all materials. Hard coat anodizing may also result in a very slight change in surface texture. It is important to understand these limitations of hard coat anodizing to ensure it is the correct choice for your specific applications.
Here are some of our other services that might interest you:
What is the difference between type II and type III anodizing?
Type II anodizing is standard anodizing, which creates a relatively thin coating for corrosion resistance and color, whereas type III, also known as type iii, eller hard coat anodizing, produces a much thicker and harder coating for superior wear resistance.
Can hard anodizing be done on all types of aluminum?
Mens aluminum is the most commonly anodized metal, not all aluminiumslegeringer are equally suitable for hard coat anodizing. Certain type of aluminum perform better than others in terms of achieving the desired beleggets tykkelse and hardness.
Does hard anodizing change the dimensions of the part?
Ja, det anodisert lag adds to the overall dimensions of the anodisert del. De tykkelse of the coating must be accounted for in the design of the component to ensure proper fit and function.
What are the common colors available for hard anodizing?
Hard anodizing creates a much thicker layer and this limits the color choices. Common various color options include black, grey, and natural finishes.
Is hard anodizing more expensive than regular anodizing?
Ja, anodizing can be more expensive because it requires more precise controls, more electricity, longer processing times, and more stringent parameters. The cost is justified for components that need that higher degree of durability.
How do I know if I need hard coat anodizing?
If your components are exposed to abrasive environments, high levels of friction, or require superior corrosion resistance, you should consider hard coat anodizing.
Ved å forstå nyansene i hard coat anodizing, you’re now better equipped to make informed decisions about surface treatments for your aluminiumsdeler. Feel free to reach out to us to learn more about our anodisering services. Our team is ready to assist you with your next project.
Få de nyeste trendene og fakta om CNC-fabrikasjon fra bloggen vår.
Shenzhen Runkey Precision Technology Co. Ltd, et datterselskap av Tensun Group, er din pålitelige one-stop-løsning for tilpasset produksjon fra prototyping til produksjon. Forvandle ideen din til virkelighet med digitale produksjonsressurser, strømlinjeformede prosesser, ekspertveiledning, akselererte tidslinjer og kompromissløs kvalitet.
©2024. CNC Fabrication Alle rettigheter forbeholdt.