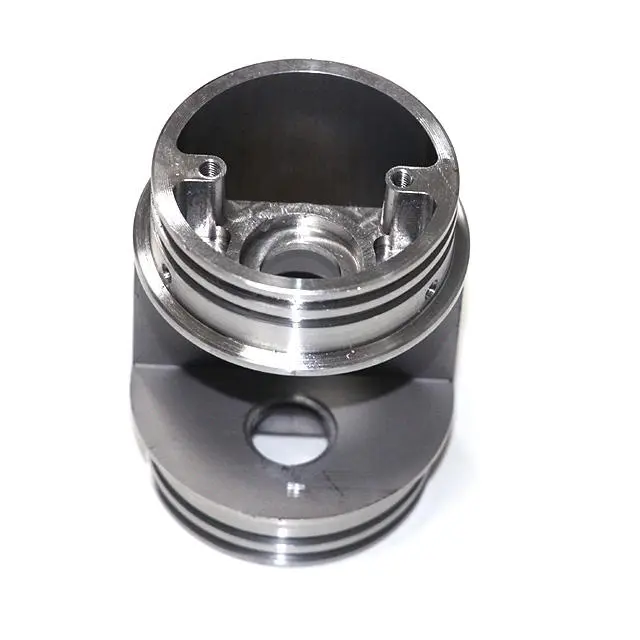
- +8615586668226
- [email protected]
- Nr. 30, Hongbang industripark, Shenzhen
Wire EDM, eller elektrisk utladningsbearbeiding med tråd, er en maskineringsprosess som bruker en tynn, enkelttrådet metalltråd, vanligvis av messing, sammen med avionisert vann for å skjære gjennom ledende materiale. De trådelektrode mates kontinuerlig fra en spole og styres langs en programmert bane. Som en ledende leverandør av CNC-fabrikasjonstjenester vil jeg understreke at denne prosessen er utrolig presis. Den maskin genererer en serie raske elektriske gnister mellom ledningen og arbeidsstykke. Disse gnister eroderer materialet og skaper et presist kutt langs den ønskede banen. Det avioniserte vannet fungerer som et dielektrikum og kontrollerer gnist og spyler bort de eroderte partiklene.
Den Wire EDM-prosess er spesielt effektiv for å skape komplekse former og intrikate design med ekstremt stramme toleranser. Det er en populær metode for produksjonsdeler som krever høy nøyaktighet, og den kan til og med håndtere harde materialer som kan være utfordrende for konvensjonelle skjæreverktøy. For eksempel kan vår Wire EDM-tjenester har vært avgjørende i produksjonen av komponenter til romfartsindustrien, der presisjon er et ufravikelig krav.
Wire EDM kan gi oss mange fordeler, for eksempel:
Høy presisjon: Wire EDM oppnår eksepsjonell nøyaktighet, med toleranser helt ned til ±0,0001 tommer.
Komplekse former: Prosessen kan skape intrikate og detaljerte geometrier som er vanskelige eller umulige å oppnå med tradisjonelle maskineringsmetoder.
Harde materialer: Wire EDM kan enkelt skjære gjennom herdet stål, titan og andre tøffe materialer.
Et av de bemerkelsesverdige aspektene ved wire EDM er dens allsidighet når det gjelder å håndtere et bredt spekter av ledende materialer. Som spesialist på dette feltet har jeg sett med egne øyne hvordan denne teknologien effektivt kan bearbeide alt fra vanlige metaller til eksotiske legeringer.
Her er en detaljert oversikt over noen av materialene som kan bearbeides ved hjelp av wire EDM:
Stål: Alle typer stål, inkludert verktøystål, rustfritt stål og hurtigstål, er egnet for wire EDM. Dette gjør den ideell til å lage verktøy, matriser og støpeformer.
Aluminium: Selv om aluminium er mykere enn stål, kan det likevel bearbeides effektivt med wire EDM, spesielt for kompliserte deler.
Titan: Dette lette, men likevel sterke materialet, som ofte brukes i romfartsindustrien, er en perfekt kandidat for wire EDM på grunn av sitt høye smeltepunkt og hardhet.
Kobber og messing: Disse ledende materialer brukes ofte i elektriske komponenter og er enkle å bearbeide ved hjelp av wire EDM.
Karbid: Karbid er kjent for sin ekstreme hardhet og brukes ofte i skjæreverktøy og slitesterke deler. Wire EDM er en av de få metodene som effektivt kan bearbeide dette tøffe materialet.
Superlegeringer: Materialer som Inconel og Hastelloy, som brukes i høytemperatur- og korrosive miljøer, kan skjæres nøyaktig ved hjelp av wire EDM.
Evnen til wire EDM til å håndtere et så bredt spekter av materialer, uavhengig av hardhet, gjør den til et uvurderlig verktøy i mange bransjer.
Wire EDM har en rekke fordeler som gjør det til et foretrukket valg for mange produksjonsapplikasjoner. Ut fra min erfaring er fordelene med wire EDM strekker seg lenger enn bare presisjon. Denne teknologien tilbyr en unik kombinasjon av egenskaper som er vanskelig å matche med andre maskinering metoder.
Wire EDM har mange fordeler, og nedenfor finner du en liste over dem:
Ingen skjærekrefter: I motsetning til konvensjonell maskinering, wire EDM innebærer ingen fysisk kontakt mellom skjæreverktøy og arbeidsstykke, eliminere skjærekrefter og risikoen for forvrengning, noe som er spesielt viktig for ømfintlige deler. Dette stressfri maskinering er ideell for produksjon av ømfintlige eller tynnveggede deler.
Gratfrie kutt: Den Wire EDM-prosess gir rene, gratfrie kanter, noe som reduserer eller eliminerer behovet for sekundær etterbehandling, noe som sparer oss for både tid og penger!
Eksepsjonell overflatefinish: Med wire EDMkan du oppnå en jevn overflatefinishog eliminerer ofte behovet for ytterligere polering eller sliping.
Allsidighet: Som nevnt tidligere, wire EDM kan håndtere et bredt spekter av ledende materialer, inkludert herdet stål, eksotiske legeringer og til og med stablede materialer.
Automatisering: Moderne trådgnistmaskiner er svært automatiserte og kan kjøre uten tilsyn i lengre perioder, noe som øker produktiviteten og reduserer lønnskostnadene.
Komplekse geometrier: Prosessen er utmerket til å skape intrikate former, skarpe hjørner og komplekse innvendige funksjoner som ville vært utfordrende eller umulig med konvensjonelle metoder.
Trange toleranser: Wire EDM kan konsekvent oppnå toleranser helt ned til ±0,0001 tommer, noe som gjør den ideell for presisjonskomponenter.
Mens wire EDM er en form for elektrisk utladningsbearbeiding, men skiller seg vesentlig fra konvensjonell EDM (også kjent som sinker EDM eller ram EDM). Forståelsen av disse forskjellene, samt hvordan wire EDM sammenlignes med andre maskinering teknikker som laserskjæringer avgjørende for å velge riktig prosess for en spesifikk applikasjon.
Her er en sammenligningstabell for å fremheve de viktigste forskjellene:
Funksjon | Wire EDM | Sinker EDM | Laserskjæring |
Skjæreverktøy | Tynn trådelektrode | Formet elektrode, vanligvis av grafitt eller kobber | Fokusert laserstråle |
Prosess | Erosjon av materiale med gnister mellom en tråd som mates kontinuerlig og arbeidsstykket | Erosjon av materiale med gnister mellom en formet elektrode og arbeidsstykket | Smelter, brenner eller fordamper materiale ved hjelp av en kraftig laser |
Former | Brukes først og fremst til 2D- og enkle 3D-figurer, men utmerker seg ved å skape intrikate konturer og profiler og skjære gjennom deler | Skaper komplekse 3D-former, hulrom og blinde funksjoner, som ofte brukes til støping og til å skape komplekse innvendige funksjoner | Brukes vanligvis til skjæring av metallplater, men kan skape komplekse 2D-figurer |
Fjerning av materiale | Lavere materialfjerningshastighet sammenlignet med sinker EDM | Raskere materialfjerning, spesielt ved grovbearbeiding | Kan ha en høy materialfjerningshastighet for tynne materialer, men kan være langsommere for tykkere seksjoner |
Overflatebehandling | Gir vanligvis en bedre overflatefinish | Kan gi en god overflatefinish, men kan kreve flere etterbehandlingstrinn | Gir et relativt rent snitt, men den varmepåvirkede sonen kan i noen tilfeller kreve etterbehandling |
Materialutvalg | Kun ledende materialer | Kun ledende materialer | Bredt utvalg av materialer, inkludert ikke-ledende materialer som plast og tre, men kan ha begrensninger med metaller |
Toleranse | Ekstremt små toleranser, vanligvis ±0,0001 tommer | Trange toleranser, men generelt ikke like presise som ved trådgnist, typisk ±0,001 tommer | Gode toleranser, men kanskje ikke like presise som EDM for svært fine detaljer |
Slitasje på verktøy | Minimal slitasje på ledningen | Slitasjen på elektrodene kan være betydelig, og det kan være nødvendig å skifte dem ut | Minimal slitasje på verktøyet |
Bruksområder | Skjæring av kompliserte former, stanser, matriser, ekstruderingsformer, romfartskomponenter, medisinsk utstyr | Lage støpeformer, matriser, komplekse hulrom og funksjoner i herdede materialer | Skjæring av metallplater, gravering, merking, prototyping |
Kostnader | Generelt høyere initialinvestering, men kan være kostnadseffektivt for komplekse deler og små til mellomstore produksjonsserier | Kan være rimeligere enn trådgnistring for enklere former, men elektrodekostnadene kan være betydelige | Kan være kostnadseffektivt for produksjon av store volumer, men den innledende investeringen kan være høy |
Automatisering | Svært automatisert, kan kjøre uten tilsyn i lengre perioder | Kan automatiseres, men kan kreve mer inngripen fra operatøren ved elektrodebytter | Høyautomatisert, egnet for kontinuerlig produksjon |
Begrensninger | Begrenset til ledende materialer, lavere materialfjerningshastighet | Elektrodeslitasje og -kostnader, begrenset til ledende materialer, kan kreve sekundær etterbehandling | Begrenset til 2D-figurer, varmepåvirket sone, kan ha problemer med reflekterende eller tykke materialer |
De unike egenskapene til wire EDM gjør den til en ideell løsning for en rekke bruksområder i mange bransjer. I min rolle har jeg sett denne teknologien bli brukt i alt fra å skape komplekse deler for romfart til produksjon av komplisert medisinsk utstyr.
Her er noen av de vanligste bruksområdene for wire EDM:
Verktøy- og formfremstilling: Wire EDM brukes i stor utstrekning til å lage presisjonsstempler, matriser og støpeformer til ulike produksjonsprosesser.
Luft- og romfartskomponenter: Evnen til å bearbeide harde materialer med høy presisjon gjør wire EDM perfekt for produksjon av kompliserte deler til fly og romfartøy.
Medisinsk utstyr: Wire EDM brukes til å lage små, komplekse komponenter til medisinske implantater, instrumenter og diagnostisk utstyr. Hos CNC Fabrication har vi produsert medisinske komponenter, som du kan lese mer om på vår Medisinsk utstyr side.
Elektronikk: Wire EDM kan produsere kompliserte deler til kontakter, kjøleribber og andre elektroniske komponenter.
Utvikling av prototyper: Wire EDM brukes ofte til å lage prototyper for testing og designvalidering på en rask og nøyaktig måte.
Mikrobearbeiding: Prosessen gjør det mulig å lage ekstremt små detaljer og deler, noe som gjør den egnet for mikrobearbeiding.
Girskjæring: Wire EDM kan produsere tannhjul med høy presisjon og komplekse tannprofiler.
Bruken av avionisert vann i wire EDM er et kritisk aspekt av prosessen, og det er noe som ofte vekker nysgjerrighet. Av erfaring kan jeg fortelle deg at vannets renhet spiller en avgjørende rolle for hvor vellykket EDM-operasjon.
Her er hvorfor avionisert vann er avgjørende:
Dielektriske egenskaper: Avionisert vann fungerer som en dielektrisk væske, noe som betyr at den er en dårlig leder av elektrisitet under normale omstendigheter. Dette gjør at spenningen kan bygge seg opp mellom ledningen og arbeidsstykke inntil en gnist kan hoppe over gapet.
Kontrollert gnistdannelse: Vannets dielektriske egenskaper bidrar til å kontrollere gnistdannelsesprosess ved å sørge for en jevn gjennombruddsspenning. Dette sikrer at gnister skjer på en forutsigbar måte og med ønsket intensitet.
Flushing: Ettersom gnister eroderer materialet, og avionisert vann fungerer som et spylemiddel som fører bort de mikroskopiske partiklene som dannes under skjæreprosessen. Dette holder skjæresonen ren og forhindrer at rusk forstyrrer skjæreprosessen. gnistdannelsesprosess.
Kjøling: Vannet fungerer også som kjølevæske, og leder bort varmen som genereres av gnister og forhindrer termisk skade på arbeidsstykke og ledningen.
Vannets renhet er avgjørende fordi eventuelle urenheter eller oppløste mineraler kan endre de dielektriske egenskapene, noe som kan føre til inkonsekvente gnistdannende og potensielt påvirke kvaliteten på kuttet. Det er derfor trådgnistmaskiner har vanligvis sofistikerte vannfiltrerings- og deioniseringssystemer for å opprettholde den nødvendige vannrenheten.
A trådgnistmaskin er et komplekst stykke utstyr med mange komponenter som jobber sammen for å oppnå presise kutt. Jeg kan trygt si at det å forstå disse komponentene er avgjørende for alle som bruker eller vedlikeholder en trådgnistmaskin.
Her er de viktigste komponentene:
Wire Feed System: Dette systemet lagrer og mates kontinuerlig med trådelektrode fra en spole gjennom maskin.
Wire Guides: Disse presisjonsføringene sørger for at wiren er nøyaktig posisjonert og opprettholder riktig spenning når den beveger seg gjennom arbeidsstykke.
Strømforsyning: Strømforsyningen genererer de elektriske høyspenningspulsene som skaper gnister mellom ledningen og arbeidsstykke.
Dielektrisk system: Dette systemet filtrerer, avioniserer og sirkulerer avionisert vann brukt i skjæreprosessen.
Arbeidsbord: Den arbeidsstykke er montert på arbeidsbordet, som kan beveges i flere akser for å skape den ønskede skjærebanen.
CNC-kontrollenhet: Hjernen til maskin, den CNC kontrollenhet, leser de programmerte instruksjonene og styrer alle aspekter av maskineringsprosess, inkludert trådbevegelse, gnist produksjon og vannføring.
Automatisk trådtrekking (AWT): Mange moderne trådgnistmaskiner AWT-funksjonen, som automatisk trer ledningen gjennom arbeidsstykke, noe som reduserer installasjonstiden og øker effektiviteten.
CNC (Computer Numerical Control) spiller en sentral rolle i moderne wire EDM operasjoner. Jeg vil faktisk si at CNC teknologien har revolusjonert wire EDMfra en manuell prosess til en svært automatisert og presis prosess. maskinering metode.
Slik gjør du det CNC er integrert i wire EDM:
Stiprogrammering: CNC gjør det mulig for operatørene å programmere komplekse skjærebaner ved hjelp av CAD/CAM-programvare. Disse programmene definerer de nøyaktige bevegelsene til tråden og arbeidsstykkesom gjør det mulig å skape intrikate former og funksjoner.
Bevegelseskontroll: Den CNC Kontrollenheten styrer nøyaktig bevegelsen til arbeidsbordet og trådmatesystemet, og sørger for at tråden følger den programmerte banen med ekstrem nøyaktighet.
Spark Control: CNC styrer også strømforsyningen, og justerer spenning, strøm og pulsvarighet for å optimalisere gnistdannelsesprosess for ulike materialer og skjæreforhold.
Automatisering: CNC muliggjør en høy grad av automatisering i wire EDM. Når programmet er lastet inn og arbeidsstykke er satt opp, vil maskin kan kjøre uten tilsyn i lengre perioder, noe som øker produktiviteten betydelig.
Adaptiv kontroll: Noen avanserte CNC-trådgnistmaskiner har adaptiv kontroll, som automatisk justerer skjæreparametrene i sanntid basert på forholdene i skjæresonen. Dette bidrar til å optimalisere skjærehastigheten, nøyaktigheten og trådlevetiden.
Integreringen av CNC teknologien har gjort wire EDM en mer effektiv, presis og pålitelig prosess som er i stand til å produsere svært komplekse deler med minimal inngripen fra operatøren.
Ved å velge riktig trådelektrode er en kritisk beslutning i wire EDMDet er et spørsmål som jeg alltid råder kundene til å vurdere nøye. Valget av tråd kan ha stor innvirkning på skjærehastighet og nøyaktighet, overflatefinishog totale kostnader.
Her er noen faktorer du bør ta hensyn til når du velger en trådelektrode:
Materiale: Messing er det vanligste trådmaterialet på grunn av den gode balansen mellom ledningsevne, strekkfasthet og pris. Andre materialer, som f.eks. belagte tråder (sinkbelagt, diffusjonsglødd), brukes imidlertid til spesifikke bruksområder. Belagte tråder kan gi raskere skjærehastigheter og bedre overflatefinish.
Diameter: Den tråddiameter varierer vanligvis fra 0,004 til 0,012 tommer. Tråder med mindre diameter gir finere kutt og trangere hjørner, men kan ha lavere skjærehastigheter.
Strekkfasthet: Tråder med høyere strekkfasthet er mer motstandsdyktige mot brudd, spesielt ved kutting av tykke materialer eller ved bruk av aggressive skjæreparametere.
Konduktivitet: Ledningens ledningsevne påvirker effektiviteten til gnistdannelsesprosess. Høyere ledningsevne fører generelt til høyere skjærehastigheter.
Søknad: Det spesifikke bruksområdet og materialet som skal kappes, vil også påvirke valget av tråd. For eksempel kan harde materialer kreve en tråd med høyere strekkfasthet, mens kutting av tykke seksjoner kan ha nytte av en belagt tråd for raskere kutting.
Valg av riktig ledning innebærer ofte en avveining av ulike faktorer, og det kan kreve litt eksperimentering for å finne den optimale ledningen for et bestemt bruksområde.
Wire EDM teknologien fortsetter å utvikle seg, drevet av kravet om stadig større presisjon, effektivitet og automatisering. Som en som er dypt involvert i dette feltet, er jeg begeistret over fremskrittene som former fremtiden for wire EDM.
Her er noen viktige trender å følge med på:
Økt automatisering: Vi kan forvente å se enda større grad av automatisering i wire EDMmed funksjoner som automatisk trådbytte, avansert prosessovervåking og integrering med robotsystemer.
Forbedret skjærehastighet: Den pågående forskningen på nye trådmaterialer, belegg og strømforsyningsteknologier fører til høyere skjærehastigheter uten at det går på bekostning av nøyaktigheten.
Forbedret presisjon: Kravet om enda strammere toleranser og finere funksjoner driver frem forbedringer i maskin design, bevegelseskontroll og gnist generasjon.
Mikro-EDM: Miniatyriseringstrenden driver utviklingen av mikroEDM-maskiner i stand til å lage utrolig små funksjoner og deler.
Hybrid maskinering: Kombinere wire EDM med andre prosesser, som fresing eller sliping, i en og samme maskin blir stadig vanligere, noe som gir større fleksibilitet og effektivitet.
Kunstig intelligens (AI): AI og maskinlæring begynner å bli brukt i wire EDM for prosessoptimalisering, prediktivt vedlikehold og adaptiv kontroll.
Industri 4.0-integrasjon: Wire EDM-maskiner blir i økende grad integrert i smarte fabrikker, med datatilkobling og overvåkingsfunksjoner i sanntid.
Disse fremskrittene lover å gjøre wire EDM en enda kraftigere og mer allsidig maskinering Vi har utviklet en metode som kan møte de stadig nye behovene til bransjer som krever de høyeste presisjons- og kvalitetsnivåene. Vi utforsker for eksempel muligheten for å integrere 5-akset wire EDM for å utvide mulighetene våre til å produsere komplekse geometrier ytterligere. Du kan lære mer om denne avanserte teknikken på vår 5-akset CNC-maskinering side.
Hva er det minste hullet som kan bores ved hjelp av wire EDM?
Med spesialiserte hullboring EDM eller EDM for små hull Teknikken gjør det mulig å lage hull helt ned til 0,004 tommer (0,1 mm) i diameter. Denne muligheten er spesielt nyttig ved mikrobearbeiding og for å skape intrikate detaljer i små deler.
Kan trådgnist skjære i ikke-ledende materialer?
Nei, wire EDM er spesielt utviklet for ledende materialer. Prosessen baserer seg på den elektriske ledningsevnen til arbeidsstykke for å fullføre den elektriske kretsen og generere gnister nødvendig for fjerning av materiale. For ikke-ledende materialer kan andre metoder som laserskjæring kan være mer passende.
Hvor lang tid tar en trådgnistprosess vanligvis?
Varigheten av en Wire EDM-prosess varierer sterkt avhengig av faktorer som materialet som skjæres, tykkelsen på arbeidsstykke, formens kompleksitet og ønsket nøyaktighet. Enkle kutt i tynne materialer kan ta minutter, mens komplekse deler i tykke, harde materialer kan ta flere timer eller til og med dager. Vi fullførte nylig et prosjekt med kompliserte komponenter til romfartsindustriensom tok flere dager med kontinuerlig wire EDM drift for å sikre høyeste presisjonsnivå.
Er wire EDM en kostbar prosess?
Kostnaden for wire EDM kan være høyere enn noen konvensjonelle maskinering metoder, spesielt for enkle deler. Men for komplekse former, harde materialer og krav til høy presisjon, wire EDM kan være svært kostnadseffektivt. Muligheten til å lage intrikate detaljer uten behov for dyre verktøy, kombinert med den høye automatiseringsgraden, resulterer ofte i lavere totalkostnader sammenlignet med alternative metoder.
Hvordan påvirker trådgnistingen materialegenskapene til arbeidsstykket?
Wire EDM er en termisk prosess, så den skaper en varmepåvirket sone (HAZ) nær skjæreflaten. Den varmepåvirkede sonen i wire EDM er vanligvis svært liten sammenlignet med andre termiske skjæreprosesser som laser- eller plasmaskjæring. Bruken av avionisert vann som kjølevæske bidrar til å minimere HAZ. I de fleste tilfeller er effekten på materialegenskapene ubetydelig, men for enkelte kritiske bruksområder kan det være nødvendig med etterbehandling eller varmebehandling. Som eksperter på CNC-fabrikasjon kan vi gi råd om hva som er den beste tilnærmingen for ditt spesifikke materiale og bruksområde.
Hva slags vedlikehold krever en trådgnistmaskin?
Wire EDM-maskiner krever regelmessig vedlikehold for å sikre optimal ytelse og lang levetid. Dette inkluderer rengjøring av maskinfilter, kontroll og justering av trådspenning og overvåking av kvaliteten på avionisert vann. De CNC kontrollenhet og andre elektroniske komponenter kan også kreve periodiske kontroller og oppdateringer. Riktig vedlikehold er avgjørende for å oppnå konsistente resultater og forhindre kostbar nedetid.
Wire EDM er en svært presis maskineringsprosess som bruker en tynn ledning og elektrisk gnister for å kutte ledende materialer.
Den utmerker seg ved å skape komplekse former, intrikate detaljer og små toleranser i et bredt spekter av materialer, inkludert herdet stål og eksotiske legeringer.
Wire EDM har mange fordeler i forhold til konvensjonelle maskinering metoder, inkludert ingen skjærekrefter, gratfrie kutt og eksepsjonelle overflatefinish.
CNC teknologi spiller en avgjørende rolle i wire EDMsom muliggjør automatisering, presis bevegelseskontroll og kompleks baneprogrammering.
Bruken av avionisert vann er avgjørende for å kontrollere gnistdannelsesprosessspyler bort rusk og kjøler ned arbeidsstykke.
Wire EDM er mye brukt i bransjer som romfart, medisinsk utstyr, verktøy- og formfremstilling og elektronikk. Se hvordan vi bruker wire EDM i bilindustrien.
Stadige fremskritt innen wire EDM teknologi, inkludert økt automatisering, høyere skjærehastigheter og forbedret presisjon, utvider mulighetene og bruksområdene.
Jeg håper denne omfattende guiden har gitt deg verdifull innsikt i den fascinerende verdenen av wire EDM. Som en ledende leverandør av CNC-fabrikasjonstjenester, inkludert produksjon av metallplater, presisjonsbearbeiding, og CNC-maskineringVi er opptatt av å utnytte den nyeste teknologien for å levere eksepsjonelle resultater for kundene våre. Hvis du har ytterligere spørsmål eller ønsker å diskutere hvordan wire EDM kan være til nytte for ditt neste prosjekt, ikke nøl med å kontakte oss. Vi er alltid ivrige etter å dele vår ekspertise og hjelpe deg med å nå dine produksjonsmål.
Få de nyeste trendene og fakta om CNC-fabrikasjon fra bloggen vår.
Shenzhen Runkey Precision Technology Co. Ltd, et datterselskap av Tensun Group, er din pålitelige one-stop-løsning for tilpasset produksjon fra prototyping til produksjon. Forvandle ideen din til virkelighet med digitale produksjonsressurser, strømlinjeformede prosesser, ekspertveiledning, akselererte tidslinjer og kompromissløs kvalitet.
©2024. CNC Fabrication Alle rettigheter forbeholdt.