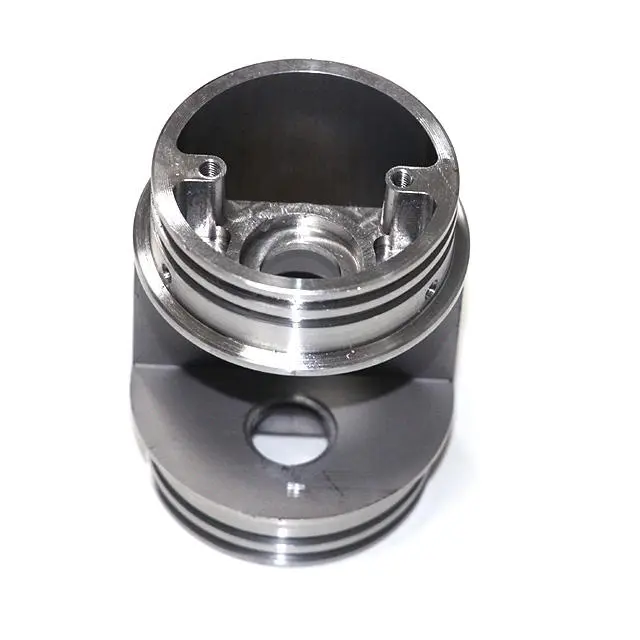
- +8615586668226
- [email protected]
- Nr 30, Hongbang Industrial Park, Shenzhen
Tłoczenie is a cold-forming proces produkcji który używa prasa tłocząca oraz stamping die przekształcać blacha w pożądany kształt. This process is essential for creating a wide array of elementy metalowe, from simple brackets to złożone części używany w komponenty motoryzacyjne and electronic devices. Tłoczenie is a highly efficient and versatile process that offers precision, repeatability, and cost-effectiveness. As a usługi produkcyjne cnc provider, I have witnessed firsthand how critical tłoczenie is to our operations and to fulfilling the diverse needs of our clients in industries like Aerospace and Aviation, Automotive, Medical Devices, Electronics, Defense and Military, Industrial Equipment, Consumer Products, Energy and Renewable Energy, Robotics, Construction and Architecture, Tooling and Dies, Food and Packaging, Pharmaceuticals, Heavy Equipment, Custom Projects/Prototyping, Art and Design, Telecommunications, Packaging.
Znaczenie tłoczenie lies in its ability to produkować części with high precision and consistency. Metal stamping is capable to create intricate designs and shapes that would be difficult or impossible to achieve with other methods. For instance, in the motoryzacja przemysł, tłoczenie is used to produce body panels, brackets, and other structural components. In elektronika, it helps create connectors, enclosures, and various other small, detailed parts. The ability of tłoczenie to work with a variety of metals, including steel, aluminum, and copper, further enhances its importance in manufacturing. Our experience in usługi produkcyjne cnc has shown us that tłoczenie remains a go-to method for producing reliable and durable części metalowe.
Progresywne tłoczenie matrycowe is an advanced formowanie metalu technique within the broader tłoczenie metali process, utilizing a series of tłoczenie stations within a single die set. Each station performs a specific operation, such as wykrawanie, bending, or coining, on the taśma metalowa jak to advances through the die. Jako usługi produkcyjne cnc provider, we use progresywne tłoczenie matrycowe to efficiently produce complex parts with high precision and consistency. This process involves feeding surowy metal przez progressive stamping diegdzie metal is progressively shaped until it reaches its final form. Progresywne tłoczenie matrycowe is especially useful for high-volume production runs and intricate parts.
Progressive dies are designed to handle multiple operations, making them ideal for complex geometries and high-precision requirements. Each station in a progressive die performs a specific task, and as the taśma metalowa moves through, it is gradually formed into the pożądany kształt. This method is perfect for creating components for the Aerospace and Aviation, Automotive, and Medical Devices industries, where precision is paramount. The progressive die stamping process allows for the creation of features like holes, notches, and bends in a single setup, significantly reducing production time and costs. Progresywne tłoczenie matrycowe is a highly efficient and cost-effective method for producing elementy metalowe. It allows for high-speed production while maintaining tight tolerances and consistent quality.
The progressive die stamping process begins with a coil of blacha that is fed into a prasa tłocząca. The press posiada die set, which consists of multiple stations. Each station performs a specific operation on the metal as it moves through the umierać. For example, the first station might cios a hole, the second might create a bend, and so on. As the taśma metalowa progresses, each operation builds upon the previous one until the część metalowa reaches its final form. Our expertise in usługi produkcyjne cnc has allowed us to optimize this process, ensuring each step is executed with precision.
The tłoczenie progresywne process is continuous, meaning that as one część metalowa is completed, the next one is already being formed. This continuous operation is what makes progresywne tłoczenie matrycowe so efficient. The taśma metalowa jest podawany do press automatically, and the części tłoczone are ejected at the end of the process. Die maintenance is crucial to ensure the longevity and performance of the stamping die. Regular inspections and maintenance by die maintenance technicians help maintain the quality of the części tłoczone. As a company specializing in usługi produkcyjne cnc, we understand the importance of maintaining our equipment to deliver high-quality results consistently.
Advantages of progressive die stamping include its high efficiency, precision, and cost-effectiveness. Progresywne tłoczenie matrycowe allows for the rapid production of złożone części with tight tolerances. This is particularly important for industries like Aerospace and Aviation, Automotive, and Medical Devices, where precision is critical. The ability to perform multiple operations within a single die set reduces the need for multiple setups and handling, leading to lower production costs. Additionally, tłoczenie progresywne minimizes material waste, as the taśma metalowa is used efficiently.
Another key advantage is the ability to create intricate designs and features in a single tłoczenie cycle. This capability is vital for producing niestandardowy metal components that meet specific design requirements. Progresywne tłoczenie matrycowe can also handle a wide range of materials, making it a versatile choice for various applications. In our experience providing usługi produkcyjne cnc, we have found that progresywne tłoczenie matrycowe is particularly beneficial for high-volume production runs where consistency and quality are paramount. The process allows for the creation of features like holes, bends, and notches with high precision. The ability to produce complex parts makes it ideal for many stamping applications.
Istnieją różne types of stamping presses używany w tłoczenie metali, each designed for specific applications. Mechanical presses are commonly used for progresywne tłoczenie matrycowe due to their speed and power. These presses use a motor-driven flywheel to store energy, which is then transferred to the ram to perform the tłoczenie operation. Hydraulic presses, on the other hand, use fluid pressure to generate force. They are often used for deep drawing and other forming operations that require high force over a longer stroke.
Servo presses are a more advanced type of prasa tłocząca that offers precise control over the ram’s speed and position. This control is particularly useful for complex tłoczenie operations and for working with delicate materials. In our usługi produkcyjne cncwykorzystujemy różnorodne presses to meet the diverse needs of our clients. The choice of press depends on factors such as the material being wytłoczony, the complexity of the part, and the required production volume. Servo presses are becoming increasingly popular due to their flexibility and precision. Different types of presses offer various benefits depending on the specific requirements of the tłoczenie operation.
Types of stamping dies include single-station dies, compound dies, and progressive dies. Single-station dies perform one operation per stroke and are used for simpler parts. Compound dies perform multiple operations on a single station, making them more efficient than single-station dies but less so than progressive dies. Progressive dies, as discussed earlier, perform a series of operations across multiple stations, making them ideal for complex and high-volume production. Transfer dies are used for larger parts that need to be moved from one station to another.
Każdy typ umierać has its own advantages and is chosen based on the specific requirements of the tłoczenie operation. For example, line dies are used in a series of presses where each umierać performs a single operation. Progressive dies are preferred for their ability to produce intricate parts efficiently. In our usługi produkcyjne cncczęsto używamy progressive dies for their versatility and efficiency. They are particularly useful for creating elementy metalowe for industries like Motoryzacja oraz Elektronika, where intricate designs are common.
W tłoczenie progresywne, many die types can be utilized within a single die set. Each station in a progressive die can perform a different operation, such as wykrawanie, bending, coining, or drawing. The number of stations depends on the complexity of the part being produced. A simple part may require only a few stations, while a complex part may require a dozen or more. The ability to combine multiple operations in one umierać is what makes progresywne tłoczenie matrycowe so efficient.
Każdy die type within a progressive die set is carefully designed and manufactured to ensure precise operation. Stal narzędziowa is commonly used for making die components due to its hardness and durability. Die design jest krytycznym aspektem tłoczenie progresywne, and it requires expertise in both formowanie metalu oraz tool and die making. As a provider of usługi produkcyjne cnc, we work closely with our clients to design and manufacture dies that meet their specific needs. The use of multiple die types w tłoczenie progresywne allows us to create highly detailed and accurate parts.
A stamping die consists of several key components, each playing a crucial role in the tłoczenie process. The die set is the foundation of the umierać and provides a rigid structure for the other components. It typically consists of an upper and lower shoe, guide pins, and bushings. The cios jest częścią umierać that performs the cutting or shaping operation on the metal. It is usually made of stal narzędziowa and is designed to withstand the high forces involved in tłoczenie.
The umierać block holds the cios i inne die components and provides the necessary support and alignment. Other important components include strippers, pilots, and gauges, which help to control the movement of the taśma metalowa and ensure accurate positioning. In our usługi produkcyjne cnc, we pay close attention to the design and construction of each die component to ensure optimal performance and longevity. Proper die maintenance is also essential to maintain the quality of the części tłoczone. The key parts of the die work together to ensure precise and efficient tłoczenie operacje.
There are several common stamping methods używany w obróbka metali, each with its own unique characteristics and applications. Blanking is a method where a cios is used to cut a piece of metal from a larger sheet. This pusty is then used for further tłoczenie operations. Piercing is similar to blanking but involves cutting holes or other shapes within the blacha. Bending involves shaping the metal by applying force along a straight axis.
Coining is a tłoczenie method where the metal is compressed between the cios oraz umierać to create a specific shape or pattern. Drawing is used to form cup-shaped or box-shaped parts by stretching the metal over a umierać. Embossing creates raised or recessed designs on the metal surface. In our usługi produkcyjne cnc, we utilize these stamping methods individually or in combination to create a wide range of elementy metalowe. Each method offers specific advantages and is chosen based on the desired outcome.
Progresywne tłoczenie matrycowe is used across a szeroki zakres branż due to its versatility and efficiency. The Lotnictwo i kosmonautyka przemysł opiera się na progresywne tłoczenie matrycowe to produce lightweight, high-strength components. In the Motoryzacja industry, it is used to create body panels, brackets, and other structural parts. The Urządzenia medyczne industry benefits from the precision and repeatability of progresywne tłoczenie matrycowe for manufacturing surgical instruments and implants.
The Elektronika zastosowania przemysłowe progresywne tłoczenie matrycowe to produce connectors, enclosures, and other small, intricate parts. The Obrona i wojsko sector utilizes this technology for creating durable and reliable components. Other industries, such as Industrial Equipment, Consumer Products, Energy and Renewable Energy, Robotics, Construction and Architecture, Tooling and Dies, Food and Packaging, Pharmaceuticals, Heavy Equipment, Custom Projects/Prototyping, Art and Design, Telecommunications, Packaging, also benefit from progresywne tłoczenie matrycowe. As a provider of usługi produkcyjne cnc, we have experience serving all these industries, delivering high-quality części tłoczone that meet their specific needs. Our expertise in obróbka cnc oraz cięcie laserowe further enhances our ability to provide comprehensive solutions.
What is the difference between progressive die stamping and transfer die stamping?
Progresywne tłoczenie matrycowe involves multiple stations within a single die set, with the taśma metalowa advancing through each station sequentially. Transfer die stamping involves moving the part from one umierać to another using a mechanical transfer system. Progresywne tłoczenie matrycowe is generally more efficient for high-volume production of complex parts.
How do I choose the right stamping method for my project?
Wybór tłoczenie method depends on factors such as the complexity of the part, the material being wytłoczony, the required production volume, and the desired precision. Consulting with a usługi produkcyjne cnc provider like us can help you determine the most suitable method for your specific needs.
What materials can be used in progressive die stamping?
Szeroki zakres materiałów może być stosowany w progresywne tłoczenie matrycowe, including steel, stainless steel, aluminum, copper, brass, and various alloys. The choice of material depends on the application and the desired properties of the finished part.
What are the tolerances that can be achieved with progressive die stamping?
Progresywne tłoczenie matrycowe can achieve very tight tolerances, often within a few thousandths of an inch. The exact tolerances depend on factors such as the die design, the material being wytłoczony, and the condition of the prasa tłocząca.
What is the typical lead time for a progressive die stamping project?
Czas realizacji dla progresywne tłoczenie matrycowe projekt różni się w zależności od złożoności umierać, the availability of materials, and the production volume. It is best to discuss your specific requirements with a usługi produkcyjne cnc provider to get an accurate estimate.
How does die maintenance affect the quality of stamped parts?
Die maintenance is crucial for ensuring the quality and consistency of części tłoczone. Regular inspections, cleaning, and sharpening of die components help prevent defects and extend the life of the umierać.
Tłoczenie is a vital obróbka metali process used across many industries.
Progresywne tłoczenie matrycowe offers high efficiency, precision, and cost-effectiveness.
Różne types of stamping presses and dies cater to various applications.
Key components of a stamping die zawierać die set, ciosoraz umierać block.
Wspólny stamping methods include blanking, piercing, bending, coining, drawing, and embossing.
Branże takie jak Aerospace and Aviation, Automotive, Medical Devices, and Electronics extensively use progresywne tłoczenie matrycowe.
Właściwy die maintenance is essential for maintaining the quality of części tłoczone.
Consulting with a usługi produkcyjne cnc provider can help you choose the right tłoczenie method for your project.
Poprzez zrozumienie zawiłości progresywne tłoczenie matrycowe and its applications, you can make informed decisions for your manufacturing needs. Whether you require precyzyjna obróbka skrawaniem, produkcja blachlub Produkcja na żądanie, our expertise in usługi produkcyjne cnc ensures that we deliver high-quality solutions tailored to your specific requirements. We invite you to contact us to explore how our services, including montaż and creating detailed Wykończenia powierzchni, can benefit your projects.
Poznaj najnowsze trendy i fakty dotyczące produkcji CNC na naszym blogu.
Shenzhen Runkey Precision Technology Co. Ltd, spółka zależna Tensun Group, jest zaufanym, kompleksowym rozwiązaniem w zakresie niestandardowej produkcji, od prototypowania po produkcję. Przekształcenie pomysłu w rzeczywistość dzięki cyfrowym zasobom produkcyjnym, usprawnionym procesom, wskazówkom ekspertów, przyspieszonym terminom i bezkompromisowej jakości.
©2024. CNC Fabrication Wszelkie prawa zastrzeżone.