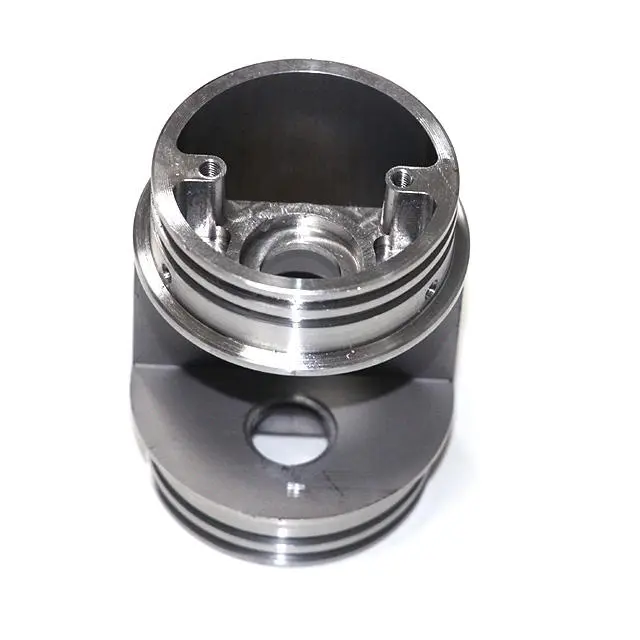
- +8615586668226
- [email protected]
- No. 30, Hongbang Industrial Park, Shenzhen
In the aerospace industry, where safety and reliability are paramount, every component, no matter how small, plays a vital role. Fasteners, such as bolts, rivets, and screws, are the unsung heroes that hold aircraft structures together, withstanding extreme forces, temperatures, and environmental conditions. We’ve seen firsthand how the right fastener can make all the difference in a project. Whether it’s ensuring the integrity of a fuselage or securing critical components in a medical device, the principles of selecting and using fasteners effectively remain the same.
Designing an aircraft involves a complex interplay of factors, including structural safety, longevity, weight, fuel efficiency, and cost. With over 120,000 materials to choose from, aerospace engineers must carefully select those that meet the stringent requirements of aircraft construction. Typically, less than 100 materials are deemed suitable for most aerospace structures due to the need for lightweight, stiff, strong, fatigue-resistant, tough, damage-tolerant, durable, easily manufactured, and cost-effective materials. Here at [Your Company Name], we specialize in working with many of these materials, offering services like Maquinação CNC e Fabrico de chapas metálicas to bring your designs to life.
The selection of fasteners is a crucial aspect of aircraft design. Factors such as material compatibility, load requirements, environmental conditions, and ease of assembly must be carefully considered. Aluminum rivets, for instance, are commonly used to join aluminum components due to their lightweight nature and resistance to corrosion. However, they are not suitable for high-tensile applications, where bolts designed to clamp materials together are preferred.
Caraterística | Parafusos | Rebites |
---|---|---|
Loading | Tension and shear | Primarily shear |
Aplicação | Clamping materials together | Joining materials permanently |
Reusability | Reusable | Not reusable |
Força | Elevada resistência à tração | Lower tensile strength, high shear strength |
Installation | Requires access to both sides of the joint | Can be installed from one side (blind rivets) |
Bolts are designed to withstand both tensile and shear forces, making them suitable for applications where high clamping forces are required. Rivets, on the other hand, are primarily used in shear applications and are permanently installed. The choice between bolts and rivets depends on the specific requirements of the joint and the overall design of the aircraft.
The increasing use of composite materials in aircraft construction presents unique challenges for fastener selection. Drilling holes into composites can damage the fibers, create stress concentrations, and provide entry points for moisture. Additionally, the contact between aluminum fasteners and carbon fibers can lead to galvanic corrosion. To mitigate these issues, titanium alloy (Ti-6Al-4V) fasteners are often used in composite joints due to their superior compatibility and strength.
In recent years, welding has emerged as a viable alternative to traditional fasteners in certain aircraft applications. Laser beam welding (LBW) and friction stir welding (FSW) offer several advantages, including reduced cracking, porosity, and improved joint properties. These welding techniques also reduce the heat-affected zone, minimize residual stresses, and eliminate the need for rivets and adhesives in some cases. This can result in significant weight and cost savings, as well as improved fatigue resistance.
Galvanic corrosion is a significant concern in aircraft construction, particularly when dissimilar metals are in contact. The use of aluminum fasteners in carbon fiber-reinforced composites can lead to severe corrosion due to the large difference in electrical potential between the two materials. To prevent this, titanium fasteners or insulating materials such as glass fabric are used to separate the aluminum from the carbon fibers.
The selection of materials for aerospace fasteners is driven by the need to meet stringent performance requirements. High-strength aluminum alloys, titanium alloys, and stainless steel are commonly used due to their excellent strength-to-weight ratio, corrosion resistance, and fatigue properties. The choice of material depends on the specific application, load requirements, and environmental conditions.
Fasteners used in aerospace applications often require protective coatings or platings to enhance their corrosion resistance and durability. Cadmium plating is a popular choice for steel fasteners, providing excellent corrosion protection and resistance to hydrogen embrittlement. Other coatings, such as zinc and phosphate, are also used depending on the specific application and environmental conditions.
Proper preloading and torque are essential for ensuring the structural integrity of bolted joints. Preloading involves applying a specific tension to the bolt before the joint is subjected to external loads. This creates a clamping force that helps to prevent loosening and fatigue failure. The amount of preload required depends on the stiffness of the bolt and the materials being joined, as well as the expected operating loads.
Bolts can fail in several ways, including tensile failure, shear failure, and fatigue failure. Tensile failure occurs when the bolt is subjected to a tensile load that exceeds its ultimate tensile strength. Shear failure occurs when the bolt is subjected to a shear load that exceeds its shear strength. Fatigue failure occurs when the bolt is subjected to repeated cyclic loading, leading to crack initiation and propagation.
Regular inspection and maintenance are crucial for ensuring the continued airworthiness of aircraft. Fasteners should be inspected for signs of corrosion, damage, and loosening. Any damaged or corroded fasteners should be replaced immediately to prevent catastrophic failure. Proper maintenance practices, including regular cleaning and lubrication, can help to extend the life of fasteners and prevent premature failure. We understand that your needs might extend beyond just aerospace. That’s why we offer a wide range of services, including Prototipagem rápida e Montagem, to support your projects from start to finish.
The Aloha Airlines incident in 1988 serves as a stark reminder of the importance of proper fastener maintenance and inspection. The incident, which involved the catastrophic failure of a section of the fuselage, was attributed to a combination of factors, including corrosion, fatigue cracking, and inadequate maintenance practices. The investigation revealed that the failure originated at a lap joint where rivets had been used to join aluminum skin panels. Corrosion in the joint had weakened the rivets, leading to fatigue cracking and ultimately, the separation of the skin panels.
The main types of fasteners used in aerospace applications include bolts, rivets, and screws. Each type has its own unique characteristics and is suited for different applications.
Galvanic corrosion is a concern because it can occur when dissimilar metals are in contact, particularly in the presence of an electrolyte such as saltwater. This can lead to the accelerated corrosion of the less noble metal, weakening the joint and potentially leading to catastrophic failure.
Galvanic corrosion can be prevented by using compatible materials, such as titanium fasteners in carbon fiber composites, or by using insulating materials to separate dissimilar metals.
LBW uses a high-power laser to melt and fuse materials together, while FSW uses a rotating tool to generate frictional heat and create a solid-state weld. Both techniques offer advantages over traditional fastening methods in certain applications.
Welding can offer several advantages over fasteners, including reduced weight, improved fatigue resistance, and the elimination of stress concentrations associated with holes.
Regular inspection and maintenance are important to ensure the continued airworthiness of aircraft. Fasteners can become corroded, damaged, or loose over time, and any issues should be addressed immediately to prevent catastrophic failure.
One question we often get is about the materials we work with. Our expertise covers a wide range of Materiais, from aluminum and titanium to more exotic alloys.
As aircraft technology continues to evolve, so too will the demands placed on fasteners. The development of new materials, such as advanced composites and high-temperature alloys, will require innovative fastening solutions. Research into new joining techniques, such as adhesive bonding and hybrid joining methods, is also ongoing. The future of aerospace fasteners promises to be one of continuous innovation and improvement, driven by the need for lighter, stronger, and more efficient aircraft.
At [Your Company Name], we’re not just about manufacturing; we’re about providing comprehensive solutions. Our Fabrico a pedido services are designed to meet your specific needs, whether you’re in the Robótica industry or developing Produtos de consumo. And with our commitment to quality Acabamento de superfícies, you can be sure that your parts will not only perform well but also look great.
Further Considerations on Fastener Use in Structural Applications
In our extensive experience providing Serviços de fabrico CNC, we’ve encountered a wide range of challenges and considerations related to fastener use in structural applications. Beyond the basics of material selection and joining techniques, several other factors play a critical role in ensuring the long-term integrity and performance of fastened joints.
Hygrothermal Effects on Composites
One area that often requires special attention is the impact of hygrothermal effects on composite materials. Changes in temperature and moisture levels can significantly affect the mechanical properties of composites. This is particularly relevant in aerospace applications where aircraft are exposed to extreme temperature fluctuations and varying humidity levels during flight. Understanding how these environmental factors influence the behavior of composites and, consequently, the performance of fasteners within these materials is crucial for designing reliable and durable structures. In our work with clients in the Aeroespacial e aviação sector, we’ve developed specialized techniques to address these challenges, ensuring that our fabricated components maintain their integrity under diverse operating conditions.
Stress Concentration and Fatigue Life
Stress concentration around fastener holes is another critical consideration. Even in well-designed joints, the presence of a hole inherently creates a region of increased stress. This can significantly impact the fatigue life of the component, especially under cyclic loading conditions. Our team utilizes advanced simulation and analysis tools to model stress distribution patterns and optimize fastener placement to minimize stress concentrations. By carefully considering factors such as hole size, edge distance, and fastener spacing, we can significantly enhance the fatigue resistance of the joint and extend the overall service life of the component.
Design for Manufacturability and Assembly
From a practical standpoint, design for manufacturability and assembly (DFMA) is paramount. We work closely with our clients, including those in the Automóvel, Dispositivos médicose Equipamento industrial industries, to ensure that fastener selection and joint design are optimized for efficient and cost-effective production. This includes considering factors such as accessibility for tooling, ease of installation, and the potential for automation. By collaborating early in the design process, we can help identify potential manufacturing challenges and develop solutions that streamline production and reduce overall costs.
Advanced Joining Techniques
While traditional mechanical fastening methods remain prevalent, advanced joining techniques are gaining traction in various industries. Adhesive bonding, for instance, offers several advantages over mechanical fastening, including improved stress distribution, reduced weight, and enhanced sealing capabilities. We’ve seen a growing interest in hybrid joining methods that combine the benefits of both adhesive bonding and mechanical fastening. These hybrid approaches can offer superior performance characteristics, particularly in applications requiring high strength, fatigue resistance, and damage tolerance.
Quality Control and Assurance
Throughout the entire fabrication process, rigorous quality control and assurance measures are essential. We employ a comprehensive range of inspection techniques, including non-destructive testing (NDT), to ensure that every fastener and every joint meets the highest quality standards. Our commitment to quality extends beyond the manufacturing floor. We work closely with our clients to develop customized quality plans that address their specific requirements and industry regulations.
Looking Ahead
As we look to the future, the field of fastening technology continues to evolve at a rapid pace. New materials, advanced joining techniques, and sophisticated simulation tools are constantly emerging, pushing the boundaries of what’s possible in structural design. At [Your Company Name], we’re committed to staying at the forefront of these advancements. We invest heavily in research and development, continuously exploring new technologies and processes to provide our clients with the most innovative and effective solutions for their fastening needs.
Conclusão
In conclusion, the world of aerospace fasteners is complex and multifaceted. It requires a deep understanding of materials science, mechanics, and manufacturing processes. At [Your Company Name], we pride ourselves on our ability to navigate this complexity and deliver precision-engineered components that meet the most demanding requirements. Whether you’re in the aerospace, automotive, medical, or any other industry that relies on high-performance fasteners, we have the expertise and experience to help you succeed.
We invite you to contact us today to discuss your specific needs and learn more about how our CNC fabrication services can benefit your next project. Let us be your trusted partner in bringing your innovative designs to life. We’re confident that together, we can achieve great things. Don’t hesitate to reach out – we’re here to help you every step of the way.
Endereço
No.30, Hongbang Industry Park, Shenzhen
Correio eletrónico
[email protected]
Telefone
+86 15586668226
Obtenha as últimas tendências e factos sobre o fabrico CNC no nosso blogue.
A Shenzhen Runkey Precision Technology Co. Ltd, uma subsidiária do Grupo Tensun, é a sua solução única e fiável para o fabrico personalizado, desde a criação de protótipos até à produção, transformando a sua ideia em realidade com recursos de fabrico digital, processos simplificados, orientação especializada, prazos acelerados e qualidade sem compromissos.
©2024. CNC Fabrication Todos os direitos reservados.