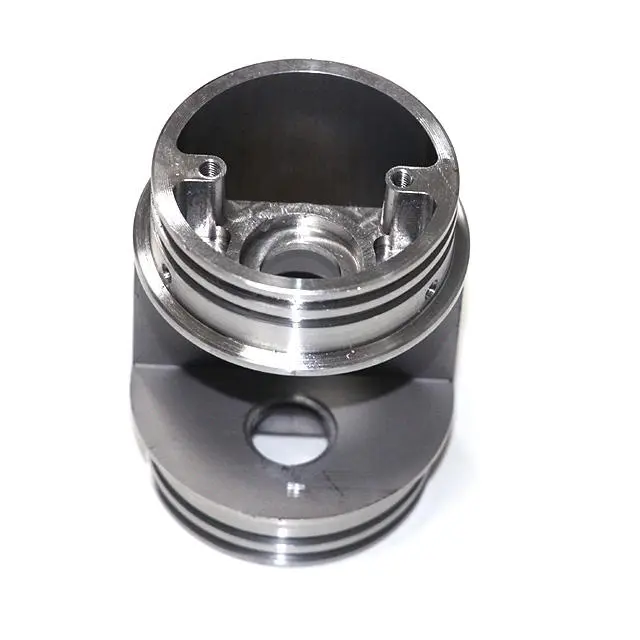
- +8615586668226
- [email protected]
- No. 30, Hongbang Industrial Park, Shenzhen
Milling isn’t just cutting metal—it’s about maximizing performance. The choice between climb (down) and conventional (up) milling impacts:
With industries like aeroespacial, automóvele dispositivos médicos demanding micron-level precision, selecting the optimal method is non-negotiable.
Climb milling, or down milling, involves the cutter rotating in the same direction as the workpiece feed. This method starts with maximum chip thickness, reducing friction and heat for smoother cuts.
In conventional (up) milling, the cutter rotates against the feed direction. It’s ideal for rough surfaces, castings, and manual machines.
Fator | Climb Milling | Conventional Milling |
---|---|---|
Chip Thickness | Starts thick, tapers to zero | Starts thin, increases gradually |
Vida útil da ferramenta | Longer (less heat) | Shorter (more friction) |
Workpiece Forces | Downward (stabilizing) | Upward (requires strong clamping) |
Melhor para | Soft metals, finishing passes | Hard materials, roughing |
A manufacturer of aerospace brackets switched to climb milling on a 5-axis CNC machine, achieving:
Which method is better for titanium alloys?
Climb milling is preferred for titanium’s low thermal conductivity, minimizing heat buildup.
Can I use climb milling on a manual machine?
Avoid it—backlash risks tool pull-in. Stick to conventional milling for safety.
How does material thickness affect the choice?
Thin materials (<6 mm) benefit from climb milling’s stabilizing forces.
Is conventional milling outdated?
No—it’s indispensable for roughing cast iron or Equipamento pesado peças.
Ready to optimize your CNC operations? Contactar-nos for tailored machining solutions!
Endereço
No.30, Hongbang Industry Park, Shenzhen
Correio eletrónico
[email protected]
Telefone
+86 15586668226
Obtenha as últimas tendências e factos sobre o fabrico CNC no nosso blogue.
A Shenzhen Runkey Precision Technology Co. Ltd, uma subsidiária do Grupo Tensun, é a sua solução única e fiável para o fabrico personalizado, desde a criação de protótipos até à produção, transformando a sua ideia em realidade com recursos de fabrico digital, processos simplificados, orientação especializada, prazos acelerados e qualidade sem compromissos.
©2024. CNC Fabrication Todos os direitos reservados.