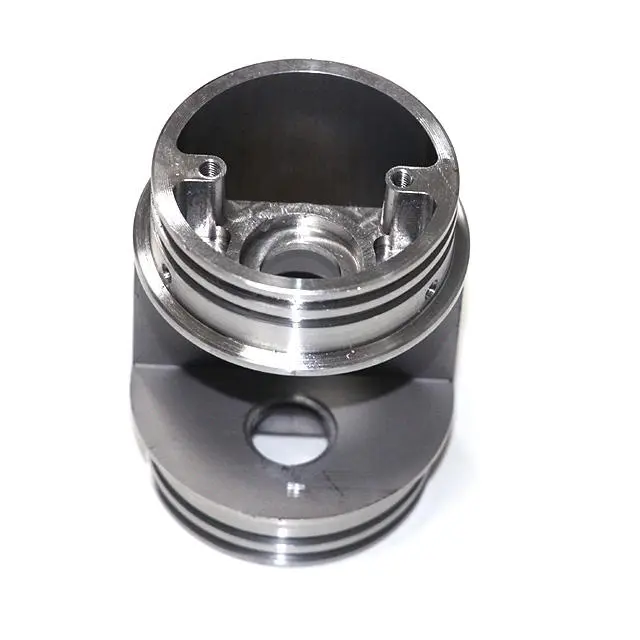
- +8615586668226
- [email protected]
- No. 30, Hongbang Industrial Park, Shenzhen
Galvanizarea la cald este un proces de fabricație prin care se aplică un strat protector de zinc pe oțel sau fier pentru a preveni rugina și coroziunea. Această metodă presupune scufundarea metalului într-o baie de zinc topit, de obicei la aproximativ 449°C (840°F). Prima istorie înregistrată a galvanizării datează din 1742, când chimistul francez P.J. Malouin a descoperit procesul electrochimic. În calitate de companie specializată în servicii de fabricație CNC, am văzut pe propria piele impactul transformator al galvanizării asupra durabilității produselor.
Procesul creează o legătură metalurgică între zinc și metalul de bază, formând o acoperire robustă, multistratificată. Această legătură este esențială, deoarece asigură faptul că zincul nu rămâne doar la suprafață, ci devine parte integrantă a metalului însuși. Oțelul de bază este astfel protejat chiar dacă acoperirea este zgâriată. În calitate de experți în acest domeniu, subliniem importanța pregătirii corespunzătoare a suprafeței înainte de galvanizare, deoarece aceasta are un impact direct asupra calității legăturii și a eficienței protecției împotriva coroziunii.
Galvanizarea joacă un rol esențial în prelungirea duratei de viață a produselor metalice. Fără aceasta, multe dintre structurile din fier și oțel pe care ne bazăm zilnic ar ceda rapid în fața efectelor dăunătoare ale coroziunii. Scopul principal al galvanizării este de a preveni coroziunea, ceea ce prelungește semnificativ durata de viață a componentelor metalice.
Din experiența noastră, metalul galvanizat poate rezista zeci de ani în medii dificile, în timp ce oțelul netratat poate necesita înlocuirea mult mai devreme. Acoperirea cu zinc acționează ca un anod sacrificial, ceea ce înseamnă că se corodează preferențial față de oțelul de bază, oferind o rezistență superioară la coroziune. Acest lucru este deosebit de important în industrii precum construcțiile, industria auto și agricultura, unde piesele metalice sunt expuse în mod constant la elemente. De exemplu industria auto se bazează în mare măsură pe oțelul galvanizat pentru caroserii, asigurându-se că acestea pot rezista la ani de expunere la diferite condiții meteorologice.
Procesul de galvanizare la cald este o procedură meticuloasă care implică mai mulți pași cheie. În primul rând, oțelul sau fierul este curățat temeinic pentru a îndepărta orice murdărie, grăsime sau calcar. Acest lucru implică de obicei degresarea, decaparea (folosind o soluție acidă pentru a îndepărta calcarul și rugina) și fluxarea, care implică scufundarea metalului într-o soluție de clorură de zinc și amoniu pentru a preveni oxidarea și a ajuta zincul să adere la oțel. În cadrul operațiunilor noastre, ne asigurăm că fiecare etapă este atent monitorizată pentru a garanta cele mai bune rezultate.
Apoi, metalul este scufundat într-o baie de zinc topit, unde are loc reacția metalurgică. Fierul din oțel reacționează cu zincul topit pentru a forma o serie de straturi de aliaj zinc-fier, acoperite cu un strat de zinc pur. Grosimea acestui strat de zinc variază de obicei între 50 și 150 microni. Odată ce metalul este scos din baia de zinc și se răcește, acoperirea se solidifică, creând o barieră de protecție. În calitate de experți în fabricarea tablelor metalice, înțelegem importanța controlului timpului și temperaturii de imersie pentru a obține grosimea de acoperire dorită.
Deși oțelul și fierul sunt cele două metale cel mai frecvent galvanizate, pot fi galvanizate și alte metale feroase. În activitatea noastră, am galvanizat diferite tipuri de oțel, inclusiv oțel moale, oțel slab aliat cu rezistență ridicată și fontă. Cu toate acestea, este important să rețineți că este posibil ca procesul de galvanizare să trebuiască să fie ajustat în funcție de metalul specific și de utilizarea acestuia.
Metalele cu niveluri ridicate de siliciu sau fosfor pot cauza formarea unui strat mai gros și mai fragil, care ar putea să nu fie potrivit pentru anumite aplicații. Acest lucru necesită expertiza unui specialist cu experiență în selectarea materialelor metalice. Este esențial să vă consultați cu experți ca noi, care înțeleg nuanțele diferitelor metale și modul în care acestea reacționează la procesul de galvanizare. De exemplu, unele oțeluri speciale pot necesita preîncălzire înainte de galvanizare pentru a preveni crăparea. Această abordare nuanțată asigură faptul că materialele galvanizate sunt utilizate pe scară largă în multe domenii, datorită durabilității lor sporite.
Da, există mai multe tipuri de galvanizare, fiecare cu un proces și o aplicație unice. Galvanizarea la cald este cea mai comună și cea mai utilizată formă datorită protecției excelente împotriva coroziunii și rentabilității sale. Cu toate acestea, există și alte metode, cum ar fi electro-galvanizarea, pre-galvanizarea și sherardizarea.
Electro-galvanizarea presupune aplicarea unui strat de zinc printr-un proces de galvanizare. Această metodă are ca rezultat o acoperire mai subțire, dar mai uniformă în comparație cu galvanizarea la cald. Pre-galvanizarea, pe de altă parte, se realizează pe foi sau bobine de oțel la uzină înainte ca acestea să fie scufundate într-o baie de zinc topit și transformate în produse. Din experiența noastră, fiecare tip are avantajele și dezavantajele sale, iar alegerea depinde de factori precum utilizarea preconizată, grosimea de acoperire necesară și preferințele estetice. De exemplu, recomandăm adesea galvanizarea la cald pentru structurile de exterior datorită protecției superioare împotriva coroziunii, în timp ce galvanizarea electrolitică ar putea fi preferată pentru produsele care necesită un finisaj mai neted, mai plăcut din punct de vedere estetic, cum ar fi articolele care necesită prelucrare de precizie.
Oțelul galvanizat oferă numeroase avantaje față de oțelul netratat, ceea ce îl face alegerea preferată în multe industrii. În primul rând, acesta oferă o protecție excepțională împotriva coroziunii, prelungind semnificativ durata de viață a produselor din oțel. Un studiu realizat de Asociația Americană a Galvanizatorilor a constatat că oțelul galvanizat la cald poate rezista peste 70 de ani în mediul rural și 20-25 de ani în cazul expunerii urbane sau costiere severe, datorită stratului protector de zinc.
În al doilea rând, oțelul galvanizat este foarte durabil și poate rezista la deteriorări mecanice în timpul manipulării, transportului și instalării. Legătura metalurgică dintre zinc și oțel face ca acoperirea să fie incredibil de dură și rezistentă la abraziune. În plus, oțelul galvanizat este rentabil pe termen lung. În timp ce costul inițial poate fi ușor mai mare, durata de viață extinsă și cerințele reduse de întreținere duc la economii semnificative în timp. În proiectele noastre, am observat în mod constant că utilizarea oțelului galvanizat minimizează nevoia de reparații și înlocuiri costisitoare.
Beneficii | Descriere |
Protecția împotriva coroziunii | Acoperirea cu zinc acționează ca o barieră și un anod sacrificial, prevenind rugina și coroziunea. |
Durabilitate | Legătura metalurgică dintre zinc și oțel creează un strat dur, rezistent la abraziune. |
Longevitate | Oțelul galvanizat poate rezista zeci de ani, chiar și în medii dificile. |
Cost-eficacitate | Cost redus al ciclului de viață datorită duratei de viață prelungite și a întreținerii reduse. |
Sustenabilitate | Zincul este un element natural și este 100% reciclabil. Oțelul galvanizat poate fi regalvanizat de mai multe ori, prelungindu-i și mai mult durata de viață. |
Ușurința inspecției | Acoperirile galvanizate sunt ușor de inspectat vizual. Aspectul uniform facilitează identificarea oricăror probleme potențiale. |
Acoperire completă | Galvanizarea la cald asigură o acoperire completă, inclusiv marginile, colțurile și adânciturile, oferind o protecție completă. |
Proces rapid | Galvanizarea la cald este un proces relativ rapid, permițând realizarea mai rapidă a proiectelor în comparație cu alte metode de acoperire, cum ar fi vopsirea. |
Apelul estetic | Oțelul galvanizat are o estetică unică, industrială, care este favorizată în multe aplicații arhitecturale și de design. Acesta poate fi, de asemenea, vopsit sau acoperit cu pulbere. |
Deși galvanizarea este o metodă excelentă de protejare a metalului, nu este singura opțiune. Alte metode includ vopsirea, acoperirea cu pulbere și utilizarea oțelului inoxidabil. Fiecare metodă are punctele sale forte și slabe, iar cea mai bună alegere depinde de aplicația specifică și de condițiile de mediu.
Comparativ cu vopsirea sau acoperirea cu pulbere, galvanizarea oferă o protecție superioară împotriva coroziunii datorită legăturii metalurgice pe care o formează cu oțelul. Vopselele și acoperirea cu pulbere se pot ciobi sau desprinde, expunând metalul de bază la coroziune. În schimb, stratul de zinc din metalul galvanizat acționează ca un anod sacrificial, continuând să protejeze oțelul chiar dacă stratul este zgâriat. Oțelul inoxidabil, deși foarte rezistent la coroziune, este semnificativ mai scump decât oțelul galvanizat, ceea ce îl face mai puțin rentabil pentru multe aplicații. Îi sfătuim adesea pe clienții noștri să ia în considerare costurile și beneficiile pe termen lung atunci când aleg o metodă de protecție a metalului și, în multe cazuri, galvanizarea iese învingătoare.
Metalul galvanizat este utilizat într-o gamă largă de industrii datorită durabilității și rezistenței sale la coroziune. Industria construcțiilor este unul dintre cei mai mari consumatori de oțel galvanizat, utilizându-l pentru componente structurale, acoperișuri și placări. Mii de tone de oțel galvanizat pentru construcții sunt utilizate în fiecare an numai în acest sector. La comunicare industria alimentară se bazează pe oțelul galvanizat pentru turnuri și infrastructură. Sectorul agricol îl utilizează pentru garduri, adăposturi pentru animale și echipamente.
În industria auto, oțelul galvanizat este utilizat pentru caroserii și piese auto, asigurându-se că acestea pot rezista la ani de expunere la intemperii. Sectorul energetic, inclusiv proiectele de energie regenerabilă, cum ar fi fermele solare și eoliene, utilizează metalul galvanizat pentru durabilitatea și longevitatea sa în medii dificile. Chiar și în specialitatea noastră, Prelucrare CNC, vedem utilizarea de componente galvanizate în diverse mașini și echipamente.
Galvanizarea este considerată un proces ecologic, mai ales în comparație cu alte metode de protecție a metalelor. Zincul, componenta principală în galvanizare, este un element natural și este 100% reciclabil. Oțelul galvanizat, care este supus procesului de galvanizare, poate fi reciclat în mod repetat fără a-și pierde proprietățile, ceea ce îl face o alegere durabilă.
În plus, durata lungă de viață a oțelului galvanizat reduce nevoia de înlocuiri frecvente, conservând resursele și reducând deșeurile. Procesul de galvanizare la cald în sine este, de asemenea, conceput pentru a minimiza impactul asupra mediului, asigurându-se că metalul este galvanizat eficient. Fabricile moderne de galvanizare, precum a noastră, utilizează sisteme cu circuit închis care reciclează și refolosesc materialele, reducând deșeurile și emisiile. Este important pentru noi ca procesele noastre de producție să fie nu numai eficiente, ci și responsabile față de mediu. În plus, industria britanică de galvanizare este angajată față de sustenabilitate și lucrează continuu pentru a-și îmbunătăți performanța de mediu, ceea ce o face o alegere responsabilă pentru diverse industrii.
Asigurarea calității produselor metalice galvanizate începe cu alegerea unui furnizor de galvanizare cu reputație și experiență. Căutați companii cu un istoric dovedit, certificări precum ISO 9001 și un angajament față de controlul calității. În cadrul operațiunilor noastre, aderăm la standarde stricte de calitate în fiecare etapă a procesului, de la selectarea materialului la inspecția finală.
De asemenea, este important să pregătiți corect suprafața metalică înainte de galvanizare, deoarece acest lucru are un impact direct asupra calității stratului de acoperire. Inspecțiile regulate în timpul și după procesul de galvanizare pot ajuta la identificarea și abordarea oricăror probleme potențiale. În plus, specificarea grosimii corecte a stratului de acoperire pentru aplicația dorită este esențială. Acoperirile mai groase oferă o protecție mai mare, dar s-ar putea să nu fie necesare pentru toate aplicațiile. Prin colaborarea strânsă cu un furnizor bine informat, vă puteți asigura că produsele dvs. metalice galvanizate îndeplinesc standardele necesare și funcționează conform așteptărilor.
Care este cauza aspectului cu paiete pe unele tipuri de oțel galvanizat?
Aspectul cu paiete, adesea observat pe oțelul galvanizat la cald, este rezultatul structurii cristalelor de zinc care se formează în timpul procesului de răcire. Dimensiunea și forma acestor cristale pot varia în funcție de factori precum rata de răcire și compoziția băii de zinc. Deși este o caracteristică naturală a galvanizării la cald, aceasta nu afectează protecția împotriva coroziunii.
Metalul galvanizat poate fi sudat?
Da, metalul galvanizat poate fi sudat, dar necesită precauții speciale. Sudarea poate deteriora stratul de zinc, creând nevoia de reparații pentru a menține protecția împotriva coroziunii. De asemenea, sudarea oțelului galvanizat produce vapori de oxid de zinc, care pot fi nocivi dacă sunt inhalați. Ventilația adecvată și echipamentul individual de protecție sunt esențiale. În calitate de experți în fabricarea metalelor, vă recomandăm să utilizați tehnici precum galvanizarea înainte de sudare sau metode de retușare după sudare pentru a asigura integritatea stratului de acoperire.
Cât timp durează galvanizarea?
Durata de viață a galvanizării depinde de mai mulți factori, inclusiv grosimea stratului de zinc, mediul la care este expus și tipul de metal utilizat. În medii blânde, oțelul galvanizat la cald poate rezista peste 70 de ani fără coroziune semnificativă. În medii mai agresive, cum ar fi zonele industriale sau de coastă, acesta poate dura 20-50 de ani sau mai mult. Inspecțiile și întreținerea regulate pot contribui la prelungirea duratei de viață și mai mult.
Este oțelul galvanizat potrivit pentru aplicații care intră în contact cu alimentele?
În general, oțelul galvanizat nu este recomandat pentru aplicații care intră în contact direct cu alimentele, în special cu alimentele acide. Deși stratul de zinc în sine nu este toxic, acesta poate reacționa cu anumite alimente, putând duce la levigarea zincului. Cu toate acestea, oțelul galvanizat poate fi utilizat în medii de prelucrare a alimentelor pentru componente structurale și echipamente care nu intră în contact direct cu alimentele. Ne sfătuim întotdeauna clienții să consulte reglementările și standardele relevante atunci când iau în considerare utilizarea oțelului galvanizat în aplicații legate de alimente.
Oțelul galvanizat poate fi vopsit sau acoperit cu pulbere?
Da, oțelul galvanizat poate fi vopsit sau acoperit cu pulbere pentru protecție suplimentară sau în scopuri estetice. Cu toate acestea, pregătirea corespunzătoare a suprafeței este esențială pentru a asigura o aderență bună atunci când metalul este galvanizat. Aceasta implică, de obicei, curățarea și aplicarea unui grund adecvat conceput pentru suprafețele galvanizate. Vopsirea sau acoperirea cu pulbere poate prelungi și mai mult durata de viață a oțelului galvanizat și poate oferi o gamă mai largă de opțiuni de culoare. Recomandăm adesea această abordare pentru proiectele în care sunt importante atât durabilitatea sporită, cât și cerințele estetice specifice, de exemplu în procesul de aplicare a unui strat de zinc. fabricarea tablei metalice pentru elemente externe.
Care sunt diferitele standarde asociate cu oțelul galvanizat?
Mai multe standarde internaționale reglementează procesul de galvanizare și calitatea oțelului galvanizat. Unele dintre cele mai recunoscute standarde includ ASTM A123/A123M pentru galvanizarea la cald a produselor din fier și oțel, ISO 1461 pentru acoperiri galvanizate la cald pe articole fabricate din fier și oțel și ASTM A153/A153M pentru acoperirea cu zinc (la cald) a feroneriei din fier și oțel. Aceste standarde specifică cerințele privind grosimea acoperirii, aspectul, aderența și metodele de testare. În calitate de furnizor de renume de servicii de fabricație CNC, ne asigurăm că procesele noastre de galvanizare respectă aceste standarde industriale pentru a oferi clienților noștri produse de înaltă calitate.
Iată principalele informații despre galvanizare:
Galvanizarea, în special galvanizarea la cald, este un proces crucial pentru protejarea oțelului și fierului împotriva coroziunii.
Procesul implică scufundarea metalului în zinc topit, creând un strat durabil, lipit metalurgic.
Metalul galvanizat oferă o rezistență excepțională la coroziune, prelungind semnificativ durata de viață a produselor.
Deși oțelul și fierul sunt cele mai comune, pot fi galvanizate și alte metale feroase.
Există diferite tipuri de galvanizare, fiecare cu propriile avantaje și aplicații.
Oțelul galvanizat este rentabil pe termen lung datorită necesităților reduse de întreținere și înlocuire, deoarece stratul de zinc protejează împotriva coroziunii.
Este o alegere durabilă, deoarece zincul este reciclabil, iar durata lungă de viață a produselor galvanizate conservă resursele.
Industrii precum construcțiile, industria auto, agricultura și energia se bazează foarte mult pe metalul galvanizat, inclusiv principalele noastre grupuri de clienți din Industria aerospațială și aviație, automobile, dispozitive medicale și sectorul electronic.
Alegerea unui furnizor de galvanizare de renume și respectarea standardelor de calitate este esențială pentru obținerea unor rezultate optime.
Galvanizarea este, în general, un proces ecologic, în special atunci când sunt respectate cele mai bune practici.
Metalul galvanizat, care este acoperit cu un strat de zinc, poate fi sudat, vopsit sau acoperit cu pulbere, cu precauții și tehnici adecvate.
Înțelegerea nuanțelor galvanizării poate ajuta întreprinderile să ia decizii în cunoștință de cauză cu privire la protecția metalelor.
În calitate de servicii de fabricație CNC specializate în fabrici de producție pentru produse, am fost martorii puterii de transformare a galvanizării. Nu este vorba doar despre prevenirea ruginii; este vorba despre asigurarea longevității, fiabilității și durabilității produselor metalice din diverse industrii. Prin înțelegerea complexității acestui proces, întreprinderile pot lua decizii în cunoștință de cauză care să conducă la produse mai bune, costuri reduse și o amprentă mai mică asupra mediului. Indiferent dacă lucrați în construcții, industria auto sau în orice alt domeniu care se bazează pe metal, galvanizarea este un proces care merită luat în considerare.
Obțineți cele mai recente tendințe și fapte despre fabricarea CNC de pe blogul nostru.
Shenzhen Runkey Precision Technology Co. Ltd, o filială a Tensun Group, este soluția dvs. unică de încredere pentru producția personalizată, de la prototipuri la producție.Transformarea ideii dvs. în realitate cu resurse de producție digitale, procese raționalizate, îndrumare de specialitate, termene accelerate și calitate fără compromisuri.
©2024. CNC Fabrication Toate drepturile rezervate.