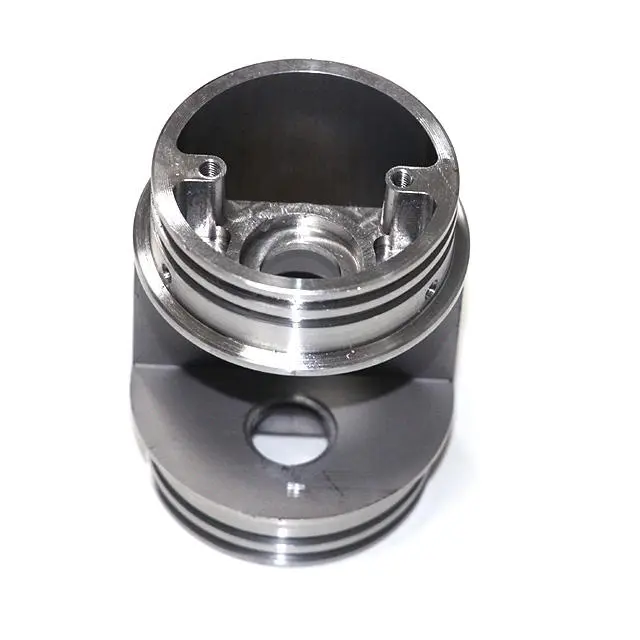
- +8615586668226
- [email protected]
- No. 30, Hongbang Industrial Park, Shenzhen
One of the biggest hurdles in CNC machining is the initial investment required for advanced machinery and software. High-end CNC machines and CAD/CAM software licensing can be prohibitive for small to medium-sized enterprises (SMEs).
Operating CNC machines requires specialized skills, and the shortage of qualified operators is a growing concern.
Choosing the right material is critical for CNC machining success. Different materials present unique challenges, such as tool wear, heat resistance, and deformation.
Material | Provocare | Soluție |
---|---|---|
Aluminiu | Sticking to cutting tools | Use lubricants and slower feed rates. |
Oțel inoxidabil | Rapid tool wear | Opt for carbide or diamond-coated tools. |
Titan | Heat resistance | Employ specialized coolants and strategies. |
Regularly update your team on advancements in material science to stay ahead of industry trends [[4]].
Design constraints can limit the capabilities of CNC machines. Complex geometries, tight tolerances, and thin walls are common challenges.
Tool wear is inevitable but manageable with the right strategies.
Programming errors can lead to costly downtime and defective products.
Quality control ensures that every part meets precise specifications.
Machining small parts requires precision and innovation.
Large parts present logistical and technical challenges.
High-volume production demands efficiency without compromising quality.
Cum pot reduce costurile de prelucrare CNC?
Invest in automation, optimize material usage, and seek leasing options for equipment.
What causes CNC program failures?
Software compatibility issues, data input errors, and improper tool settings are common culprits.
How do I choose the right material for CNC machining?
Consider the end-use requirements, material properties, and machining capabilities.
What are the benefits of advanced CAD/CAM software?
It simplifies programming, reduces errors, and enables simulations for better planning.
How can I improve CNC machining precision?
Regularly calibrate machines, use high-quality tools, and optimize cutting parameters.
For more insights, explore our resources on Prelucrare CNC, Prelucrare de precizie, și Prelucrare CNC cu 5 axe.
Obțineți cele mai recente tendințe și fapte despre fabricarea CNC de pe blogul nostru.
Shenzhen Runkey Precision Technology Co. Ltd, o filială a Tensun Group, este soluția dvs. unică de încredere pentru producția personalizată, de la prototipuri la producție.Transformarea ideii dvs. în realitate cu resurse de producție digitale, procese raționalizate, îndrumare de specialitate, termene accelerate și calitate fără compromisuri.
©2024. CNC Fabrication Toate drepturile rezervate.