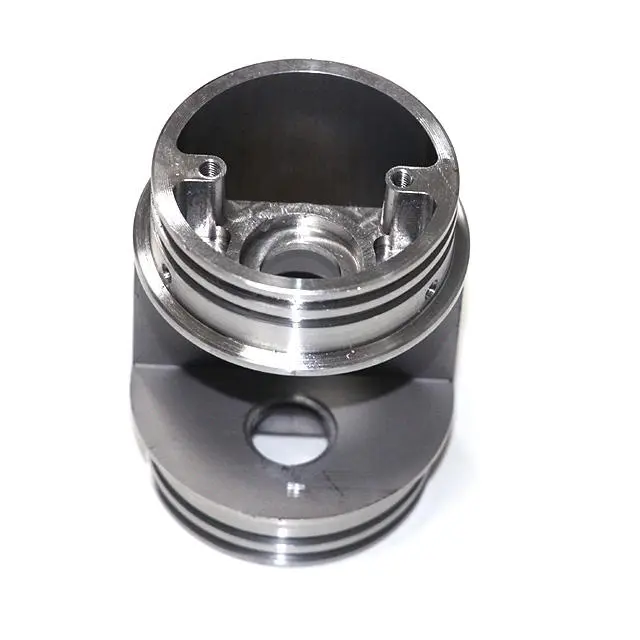
- +8615586668226
- [email protected]
- No. 30, Hongbang Industrial Park, Shenzhen
At its core, sheet metal forming is a manufacturing process that involves applying force to a sheet of metal, causing it to bend, stretch, or deform into a desired shape without fracturing. This process leverages the plasticity of metals, their ability to undergo permanent deformation under stress. The methods employed in sheet metal forming can range from simple bending operations to complex deep drawing and incremental forming techniques.
Why is Sheet Metal Forming Important?
Sheet metal forming encompasses a variety of techniques, each tailored to specific geometries and material properties. Here’s a breakdown of the primary categories:
Deep drawing is a widely used sheet metal forming process that deserves special attention. It’s a critical process in industries like automotive, where complex shapes are often required. This process involves several key stages:
Key Considerations in Deep Drawing:
The success of sheet metal forming hinges on understanding the mechanical properties of the materials being used. Here are some key properties to consider:
Friction plays a significant role in sheet metal forming. It affects the forces required for forming, the quality of the finished part, and the lifespan of tooling. Effective lubrication is crucial to minimize friction and ensure smooth, efficient forming.
Types of Lubricants:
Lubrication Mechanisms:
Incremental and hybrid forming represent the cutting edge of sheet metal forming technology. These processes offer greater flexibility and control, enabling the creation of complex shapes that were previously impossible or impractical to produce.
Incremental Forming:
Hybrid Forming:
Presses are the workhorses of sheet metal forming, providing the force necessary to deform the metal. There are two main types of presses used in sheet metal forming:
Mechanical Presses:
Hydraulic Presses:
Servo-presses represent a significant advancement in press technology. These presses use servomotors to control the motion of the ram, offering several advantages over conventional mechanical and hydraulic presses:
Cushion systems play a crucial role in sheet metal forming, particularly in deep drawing. They provide a controlled force that opposes the punch force, helping to prevent wrinkling and tearing.
Types of Cushion Systems:
Sheet metal forming finds applications in a wide array of industries, including:
Industrie | Aplicații |
---|---|
Industria aerospațială și aviație | Aircraft fuselages, wings, engine components, interior panels. |
Automobile | Body panels, chassis components, fuel tanks, exhaust systems. |
Dispozitive medicale | Surgical instruments, implants, diagnostic equipment enclosures. |
Electronică | Computer cases, server racks, electronic enclosures. |
Apărare și armată | Vehicle armor, weapon components, ammunition casings. |
Echipamente industriale | Machinery housings, control panels, conveyor systems. |
Produse de larg consum | Appliances, cookware, furniture, lighting fixtures. |
Energie și energie regenerabilă | Solar panel frames, wind turbine components, battery enclosures. |
Robotică | Robot arms, end effectors, structural components. |
Construcții | Roofing, cladding, structural elements. |
Telecomunicații | Antennas, satellite dishes, communication equipment enclosures. |
Ambalaje | Cans, containers, closures. |
Artă și design | Sculptures, decorative panels, architectural elements. |
Scule și matrițe | Components for manufacturing tools and dies. |
Produse alimentare și ambalaje | Food processing equipment, packaging machinery. |
Produse farmaceutice | Pharmaceutical manufacturing equipment, medical device components. |
Echipamente grele | Construction machinery, agricultural equipment, mining equipment. |
Proiecte personalizate/Prototipuri | Unique parts for research, development, and custom applications. As a provider of Soluții CNC we specialize in creating prototypes for many industries. |
Case Study 1: Automotive Body Panels
A major automotive manufacturer needed to produce complex body panels for a new vehicle model. By utilizing desen profund și avansate servo-press technology, they were able to achieve the desired shape with high precision and efficiency. The use of high-strength steel allowed for thinner panels, reducing vehicle weight and improving fuel efficiency.
Case Study 2: Medical Device Enclosures
A medical device company required intricate enclosures for a new diagnostic device. Using incremental forming, they were able to create prototypes quickly and cost-effectively. The flexibility of incremental forming allowed for design iterations without the need for expensive tooling changes. Once the design was finalized, they transitioned to traditional forming methods for mass production.
Case Study 3: Aerospace Components
An aerospace company needed to produce lightweight, high-strength components for an aircraft. By using stretch forming and advanced aluminum alloys, they were able to create complex shapes that met the stringent requirements of the aerospace industry. The use of Prelucrare CNC cu 5 axe ensured that the components were formed to precise tolerances.
What is the difference between cold forming and hot forming?
Cold forming is performed at room temperature, while hot forming is performed at elevated temperatures. Hot forming is typically used for thicker materials or materials with low ductility at room temperature.
What is springback, and how can it be compensated for?
Springback is the elastic recovery of a material after it has been formed. It can be compensated for by overbending the material or by using special tooling.
What is the role of simulation in sheet metal forming?
Computer simulation is used to predict the behavior of materials during forming. It can help optimize process parameters, reduce trial-and-error, and improve part quality.
What are the advantages of using CNC machining in sheet metal forming?
CNC machining offers high precision, repeatability, and automation. It can be used for blank preparation, trimming, and other secondary operations. CNC machining is one of the servicii de prelucrare we excel at.
What are the limitations of sheet metal forming?
Sheet metal forming is generally limited to relatively thin materials. It may not be suitable for creating very thick parts or parts with very sharp corners.
How do I choose the right sheet metal forming process for my application?
The choice of process depends on factors such as part geometry, material properties, production volume, and cost considerations.
Sheet metal forming is a dynamic field, constantly evolving with new technologies and materials. As a leader in Servicii de fabricare CNC, we are committed to staying at the forefront of these advancements, offering our clients the most innovative and efficient manufacturing solutions. Whether you need prototipuri rapide, high-volume production, or specialized forming techniques, we have the expertise and resources to meet your needs.
By embracing the power of sheet metal forming, businesses across a wide range of industries can unlock new levels of precision, efficiency, and innovation. As we continue to push the boundaries of what’s possible, we invite you to join us on this journey, shaping the future of manufacturing together.
Ready to transform your ideas into reality? Contact us today to discuss your sheet metal forming needs and discover how our expertise can help you achieve your manufacturing goals.
Obțineți cele mai recente tendințe și fapte despre fabricarea CNC de pe blogul nostru.
Shenzhen Runkey Precision Technology Co. Ltd, o filială a Tensun Group, este soluția dvs. unică de încredere pentru producția personalizată, de la prototipuri la producție.Transformarea ideii dvs. în realitate cu resurse de producție digitale, procese raționalizate, îndrumare de specialitate, termene accelerate și calitate fără compromisuri.
©2024. CNC Fabrication Toate drepturile rezervate.