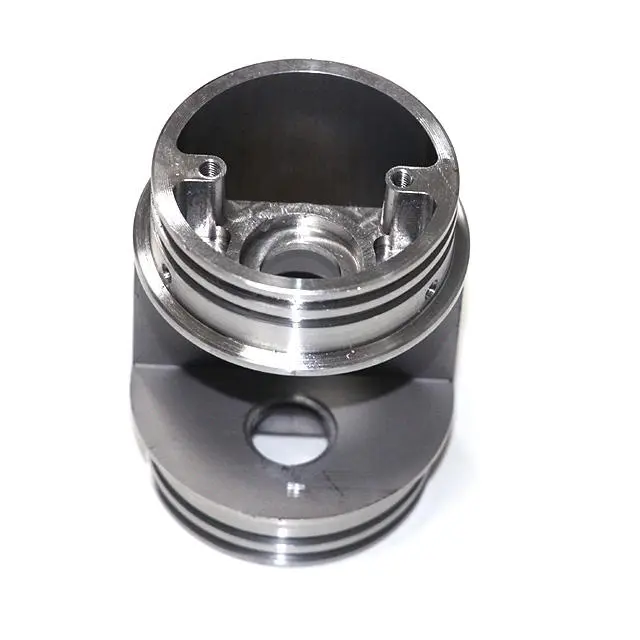
- +8615586668226
- [email protected]
- No. 30, Промышленный парк Хунбан, Шэньчжэнь
As someone deeply involved in Производство с ЧПУ services, I can’t stress enough the importance of accurately calculating CNC machine cycle time. Cycle time is the foundation upon which we build our production schedules, cost estimates, and delivery timelines. It directly impacts our ability to meet customer expectations and maintain profitability. For instance, underestimating cycle time can lead to missed deadlines and increased costs, while overestimating it can make our bids less competitive.
Moreover, understanding cycle time allows us to identify bottlenecks in our процесс обработки and optimize our operations. By analyzing each component of the cycle time calculation, we can pinpoint areas where we can improve efficiency. For example, we might discover that investing in faster машины or optimizing our tool change time can significantly reduce the overall cycle time. This knowledge is invaluable for continuous improvement and staying ahead in the competitive landscape of Услуги по обработке на станках с ЧПУ.
The data shown in the table below illustrates the impact of reducing cycle time on production output.
Cycle Time (minutes) | Parts per Hour | Increase in Production (%) |
10 | 6 | – |
9 | 6.67 | 11.1 |
8 | 7.5 | 25.0 |
7 | 8.57 | 42.9 |
6 | 10 | 66.7 |
Примечание: This table assumes continuous operation with no downtime.
In simple terms, cycle time в Обработка на станках с ЧПУ refers to the total время it takes to complete one full операция обработки on a part, from start to finish. This includes everything from loading the workpiece onto the машина to unloading the finished part. Think of it as the heartbeat of your станок с ЧПУ – a measure of how quickly it can produce.
Однако, cycle time isn’t just about the actual cutting or время обработки. It encompasses various other elements, such as tool change time, rapid traverse movements, and any delays between operations. Understanding these components is crucial for accurately calculating and optimizing cycle time. В качестве Производство с ЧПУ expert, I always emphasize that cycle time is a holistic measure of a машина productivity, not just its cutting speed.
The basic formula for calculating CNC machining time is straightforward:
Machining Time = (Total Length of Cut) / (Скорость подачи x Number of Passes)
Let’s break this down:
Total Length of Cut: This is the total distance the инструмент travels while cutting the material.
Скорость подачи: This is the speed at which the инструмент moves across the workpiece, usually measured in inches per minute or millimeters per minute.
Number of Passes: This is the number of times the инструмент needs to pass over the same area to achieve the desired depth or finish.
Это formula provides a starting point for estimating время обработки. However, it’s important to remember that this is a simplified version and doesn’t account for all the factors that can affect cycle time.
To get a more accurate cycle time calculation, we need to consider several components:
Cutting Time: This is the actual время сайт инструмент is engaged in cutting the material. It can be calculated using the formula mentioned earlier.
Tool Change Time: This is the время it takes to change from one инструмент to another. It can vary depending on the машина and the complexity of the инструмент change process.
Rapid Traverse Time: This is the время сайт машина spends moving the инструмент between different cutting locations without cutting.
Время установки: This includes the время to load and unload the workpiece, as well as any время spent on programming or setting up the машина.
Idle Time: This is any время сайт машина is not actively working due to delays, maintenance, or other issues.
By calculating each of these components separately and adding them together, we can get a more accurate estimate of the total cycle time.
Several factors can influence CNC machining cycle time:
Твердость материала: Harder materials generally require slower скорости подачи and more passes, increasing cycle time.
Tool Geometry: The shape and size of the инструмент can affect cutting efficiency and, consequently, cycle time.
Machine Capabilities: The speed and power of the станок с ЧПУ play a crucial role. High-speed CNC machines can significantly reduce cycle time.
Cutting Parameters: Скорость подачи, depth of cut, and cutting speed all impact cycle time.
Part Complexity: Complex parts with intricate features often require more operations and инструмент changes, increasing cycle time.
Coolant Usage: Proper coolant application can improve инструмент life and allow for higher cutting speeds, reducing cycle time.
Токарная обработка с ЧПУ это процесс обработки used to create cylindrical parts. To estimate the time для Токарная обработка с ЧПУ, we need to consider the following:
Calculate the cutting time: Use the formula: Cutting Time = (Length of Cut) / (Скорость подачи x Spindle Speed).
Estimate the tool change time: This depends on the complexity of the part and the number of инструменты требуется.
Add the rapid traverse time: This is the время сайт машина spends moving the инструмент between cuts.
Include the setup time: This includes loading and unloading the workpiece.
By summing up these components, we can get a good estimation из turning cycle time.
Фрезерование с ЧПУ универсальный процесс обработки used to create a wide range of shapes. To calculate the time необходимый для Фрезерование с ЧПУ, follow these steps:
Determine the cutting time: Use the basic machining time formula, considering the length of cut, скорость подачи, and number of passes.
Estimate the tool change time: This depends on the complexity of the part and the number of инструменты needed.
Calculate the rapid traverse time: This is the время сайт машина spends moving the инструмент between different cutting locations.
Add the setup time: This includes loading and unloading the workpiece and any programming время.
By adding these components together, we can calculate the total time it takes for Фрезерование с ЧПУ.
Уменьшение cycle time is crucial for improving productivity and profitability. Here are some strategies:
Optimize Cutting Parameters: Fine-tuning скорости подачи, cutting speeds, and depths of cut can significantly reduce время резки.
Use High-Performance Tooling: Investing in advanced оснастка can allow for faster cutting speeds and longer инструмент life.
Implement High-Speed Machining Techniques: Techniques like trochoidal milling and adaptive clearing can reduce cycle time by maintaining a constant инструмент engagement.
Reduce Tool Changes: Designing parts with fewer инструмент changes in mind can minimize tool change time.
Automate Processes: Implementing automation for part loading, unloading, and инструмент changes can reduce non-cutting время.
Оптимизация Обработка на станках с ЧПУ operations involves more than just reducing cutting время. It’s about minimizing all forms of wasted время:
Streamline Setup Processes: Standardizing setup procedures and using quick-change fixtures can reduce время установки.
Optimize Tool Paths: Using CAM software to generate efficient инструмент paths can minimize rapid traverse время.
Implement Predictive Maintenance: Regular maintenance can prevent unexpected downtime and keep машины running at peak performance.
Improve Workflow: Optimizing the flow of materials and information can reduce delays between operations.
Train Operators: Well-trained operators can set up and run машины more efficiently, reducing errors and downtime.
Точный cycle time estimation is the cornerstone of successful Обработка на станках с ЧПУ projects. It allows us to:
Provide Accurate Quotes: By accurately estimating cycle time, we can provide competitive and realistic quotes to our clients.
Plan Production Effectively: Знание cycle time allows us to schedule production efficiently and meet delivery deadlines.
Optimize Resource Allocation: Точный cycle time data helps us allocate машины and personnel effectively.
Identify Bottlenecks: By comparing estimated cycle time with actual cycle time, we can identify areas for improvement.
Improve Profitability: Оптимизируя cycle time, we can increase throughput and reduce costs, ultimately improving profitability.
What is the difference between cycle time and lead time in CNC machining?
Cycle time относится к время it takes to complete one обработка operation on a single part. Время выполнения refers to the total время it takes to fulfill an order, from order placement to delivery. Время выполнения includes cycle time as well as other factors like order processing, material procurement, and shipping.
How can I calculate the feed rate for a CNC machining operation?
На calculate the feed rate, you need to know the spindle speed (in revolutions per minute) and the chip load (the amount of material removed by each tooth of the инструмент per revolution). The formula is: Скорость подачи = Spindle Speed x Chip Load x Number of Teeth on the Инструмент.
What is the impact of tool wear on CNC machining cycle time?
Инструмент wear can significantly impact cycle time. В качестве инструмент wears, it becomes less efficient, requiring slower cutting speeds and potentially more passes to achieve the desired result. This increases the overall cycle time. Regular инструмент monitoring and replacement are essential for maintaining optimal cycle times.
How does the complexity of a part affect CNC machining cycle time?
Part complexity has a direct impact on cycle time. More complex parts often require multiple operations, different инструменты, and more intricate инструмент paths. This increases both время резки and non-cutting время (such as tool change time and rapid traverse время), resulting in a longer overall cycle time.
Can cycle time be reduced by using multiple tools simultaneously?
Yes, in some cases, using multiple инструменты simultaneously, such as in multi-spindle or multi-turret машиныможет значительно уменьшить cycle time. This allows for multiple operations to be performed concurrently, reducing the overall время to complete the part.
How important is coolant in optimizing CNC machining cycle time?
Coolant plays a crucial role in optimizing cycle time. Proper coolant application helps to dissipate heat, reduce инструмент wear, and improve chip evacuation. This allows for higher cutting speeds and скорости подачи, ultimately reducing cycle time. Coolant also helps to improve surface finish, which can reduce the need for secondary operations.
Cycle time calculation is essential for optimizing Обработка на станках с ЧПУ операции.
Understanding the components of cycle time allows for accurate estimation and identification of areas for improvement.
Factors like material, оснастка, машина capabilities, and cutting parameters significantly affect cycle time.
Токарная обработка с ЧПУ и Фрезерование с ЧПУ have specific considerations for cycle time calculation.
Strategies like optimizing cutting parameters, using high-performance оснастка, and implementing high-speed machining techniques can reduce cycle time.
Minimizing wasted время through streamlined setups, optimized инструмент paths, and predictive maintenance is crucial.
Точный cycle time estimation is vital for providing accurate quotes, planning production, optimizing resource allocation, and improving profitability.
Continuous improvement through data analysis and process optimization is key to staying competitive in the Обработка на станках с ЧПУ промышленность.
В нашем Производство с ЧПУ plants, we leverage our extensive experience and advanced technology to provide top-notch Услуги по обработке на заказ с ЧПУ. С сайта аэрокосмические компоненты на медицинские приборы и прецизионная обработка, we deliver high-quality parts with optimized cycle times. Our expertise in various processes, including Фрезерование с ЧПУ, Токарная обработка с ЧПУ, и производство листового металла, ensures we meet the diverse needs of industries like automotive, electronics, robotics, and more. We’re committed to continuous improvement and customer satisfaction, making us your ideal partner for all your Обработка на станках с ЧПУ needs. Contact us today to learn how we can optimize your production and help you achieve your manufacturing goals.
Адрес
No.30, Hongbang Industry Park, Шэньчжэнь
Электронная почта
[email protected]
Телефон
+86 15586668226
Узнайте о последних тенденциях и фактах в области производства с ЧПУ из нашего блога.
Shenzhen Runkey Precision Technology Co. Ltd, дочерняя компания Tensun Group, является вашим надежным универсальным решением для производства на заказ от прототипа до производства. Превращение вашей идеи в реальность с помощью цифровых производственных ресурсов, оптимизированных процессов, экспертного руководства, ускоренных сроков и бескомпромиссного качества.
©2024. CNC Fabrication Все права защищены.