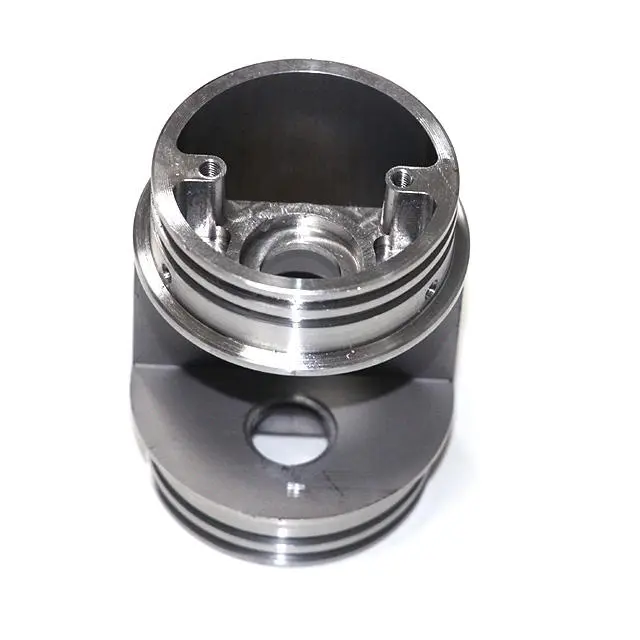
- +8615586668226
- [email protected]
- No. 30, Промышленный парк Хунбан, Шэньчжэнь
Machining parameters are the settings that control the cutting conditions during the CNC machining process. Think of them like the ingredients and instructions in a recipe. Just as the right ingredients and cooking methods determine the taste and quality of a dish, the correct machining parameters determine the quality, precision, and efficiency of your manufactured parts.
Incorrect parameters can lead to:
By mastering these parameters, you can achieve:
Let’s explore the essential CNC machining parameters and how they impact your manufacturing process.
Cutting speed is the speed at which the cutting tool moves across the surface of the material. It’s like the speed of a car on a highway. It’s measured in feet per minute (FPM) or meters per minute (MPM).
Calculating Cutting Speed (Cs):
Cs = π × d × n
Где:
Spindle speed is the rotational speed of the cutting tool (or the workpiece in turning operations). It’s measured in revolutions per minute (RPM). It’s like the speed at which a drill bit spins.
Calculating Spindle Speed (n):
n = (Cs × 1000) / (π × d)
Где:
Feed rate is the distance the cutting tool travels during one revolution of the spindle (or workpiece). It’s measured in inches per minute (IPM) or millimeters per minute (MM/min). Think of it as how quickly you feed wood into a saw.
Calculating Feed Rate (F):
F = f × n
Где:
Depth of cut is the thickness of the material removed by the cutting tool in a single pass. It’s measured in millimeters or inches. It’s like how deep a plow digs into the soil.
There’s no single formula, but here are some general guidelines:
SFM is another way to express cutting speed, specifically at the point where the tool contacts the workpiece. It’s vital for efficiency and surface quality.
Calculating SFM:
SFM = (π × D × RPM) / 12
Где:
This is very similar to the depth of cut, but it specifically refers to each individual pass the tool makes. Keeping this consistent helps ensure even material removal.
Plunge rate is how fast the tool moves down into the material, especially important for drilling or pocketing operations. It’s also measured in IPM or MM/min.
Calculating Plunge Rate:
Plunge Rate = Feed per Tooth × Number of Flutes × Spindle Speed
Chip load is the thickness of the material removed by each cutting edge of the tool during one revolution. It’s a key factor in tool life and surface finish. Proper chip load prevents:
The size of your cutting tool significantly impacts the machining process.
The tool path is the route the cutting tool takes to remove material. Efficient tool paths are critical for:
Wall thickness, the minimum thickness of a part’s walls, is a crucial design consideration.
The ideal wall thickness depends on:
Here’s a straightforward process for setting your CNC machine parameters:
The table below provides starting point recommendations. Always consult tooling manufacturer data for precise values.
Материал | Скорость вращения шпинделя (об/мин) | Cutting Speed (ft/min) | Feed Rate (IPT) | Depth of Cut (inches) | Примечания |
---|---|---|---|---|---|
Алюминий | 3000-6000 | 600-1000 | 0.002-0.005 | 0.04-0.10 | Use sharp tools, good cooling. We specialize in Экструзия алюминия. |
Сталь | 1500-3000 | 100-400 | 0.001-0.004 | 0.02-0.08 | Use robust tools (HSS or carbide). |
Нержавеющая сталь | 1000-2000 | 50-150 | 0.001-0.003 | 0.01-0.05 | Tough material, use coated tools. |
Титан | 500-1500 | 30-100 | 0.0005-0.002 | 0.01-0.04 | Very difficult to machine, requires careful control. |
Softwood/Plywood | 10,000-18,000 | 800-1200 (m/min) | 0.004-0.006 | 0.10-0.25 | |
Твердая древесина | 8000-12,000 | 600-1000 (m/min) | 0.003-0.005 | 0.08-0.20 | |
Акрил | 10,000-16,000 | 100-300 (m/min) | 0.002-0.004 | 0.02-0.10 | High speed, low feed, good cooling to prevent melting. |
Поликарбонат | 8000-12,000 | 150-400 (m/min) | 0.002-0.005 | 0.02-0.08 | Control heat to prevent deformation. |
PVC | 8000-14,000 | 200-500 (m/min) | 0.002-0.004 | 0.02-0.06 | |
Композиты | 12,000-18,000 | 100-300 (m/min) | 0.001-0.004 | 0.01-0.08 | Requires specialized tooling and techniques. We offer expertise in machining composites for various industries, including Аэрокосмическая промышленность. |
Superalloys | 1000-4000 | 30-60(m/min) | 0.001-0.003 | 0.01-0.05 | Require lower spindle speeds and cutting speeds |
Керамика | 8000-16,000 | 100-200(m/min) | 0.002-0.004 | 0.005-0.02 | Ceramics require high spindle speeds and low feed rates |
High-Performance Polymers | 6000-12,000 | 150-400(m/min) | 0.002-0.006 | 0.01-0.05 | Parameters for high-performance polymers |
The cutting tool you choose is directly linked to the parameters you set. Here’s what to consider:
Here’s how to fine-tune your CNC parameters for the best results:
Here are some telltale signs that your parameters need adjustment:
Correctly setting your parameters can significantly reduce your manufacturing costs:
What if I’m unsure about the right parameters for my material?
Start with conservative settings (lower speeds and feeds) and gradually increase them while monitoring the process. Consult tooling manufacturer data and material guides.
How often should I check my CNC machine parameters?
Regularly check parameters, especially when changing materials, tools, or job types.
What’s the difference between cutting speed and spindle speed?
Cutting speed is the speed of the tool across the material’s surface. Spindle speed is the rotational speed of the tool (or workpiece).
Can I use the same parameters for different CNC machines?
Not necessarily. Machine capabilities (power, rigidity) vary, so parameters may need adjustment.
What role does coolant play in parameter optimization?
Coolant reduces heat, extends tool life, and improves surface finish. Proper coolant flow is crucial, especially with harder materials. We offer a variety of Отделка поверхности options to enhance your parts.
Where can I get help with complex CNC machining projects?
Contact us! As a CNC Manufacturing Service and Product Manufacturing Factory, we have the expertise and equipment to handle projects across various industries, including Медицинские приборы, Электроника, Оборона и военное дело, and more. We also offer Быстрое прототипирование услуги.
By understanding and applying these principles, you can achieve superior results in your CNC machining operations. We are here to help you every step of the way, from prototype to production. Contact us today to discuss your project!
Адрес
No.30, Hongbang Industry Park, Шэньчжэнь
Электронная почта
[email protected]
Телефон
+86 15586668226
Узнайте о последних тенденциях и фактах в области производства с ЧПУ из нашего блога.
Shenzhen Runkey Precision Technology Co. Ltd, дочерняя компания Tensun Group, является вашим надежным универсальным решением для производства на заказ от прототипа до производства. Превращение вашей идеи в реальность с помощью цифровых производственных ресурсов, оптимизированных процессов, экспертного руководства, ускоренных сроков и бескомпромиссного качества.
©2024. CNC Fabrication Все права защищены.