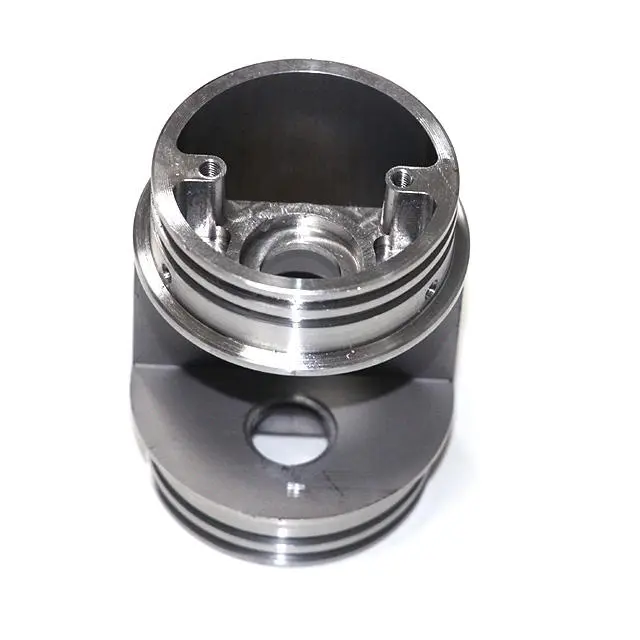
- +8615586668226
- [email protected]
- No. 30, Промышленный парк Хунбан, Шэньчжэнь
Использование lightweight metal in manufacturing offers numerous advantages, especially in industries where weight reduction is critical. From my experience, one of the most significant benefits is the improved fuel efficiency in the automotive and аэрокосмическая промышленность sectors. For instance, using lightweight alloys in car bodies can drastically reduce the overall weight, leading to lower fuel consumption and emissions. Similarly, in аэрокосмические приложения, lightweight materials contribute to higher payload capacities and reduced operational costs. The соотношение прочности и веса of these materials is exceptional, making them ideal for applications where both strength and lightness are paramount.
Another critical advantage is enhanced performance. In the аэрокосмическая промышленность industry, reducing the weight of an aircraft by just a few kilograms can significantly improve its maneuverability and speed. Furthermore, the коррозионная стойкость of many lightweight metal alloys, such as титан and certain types of Aluminum is one of the three metals commonly used in lightweight products. alloy, extends the lifespan of products and reduces maintenance costs. The теплопроводность of these materials is also noteworthy. For example, магний имеет отличную thermal and electrical проводимость, making it suitable for heat sinks and electronic housings.
Определение best lightweight metal for high-strength applications depends on specific requirements, but титан and its alloys often stand out. Titanium alloy offers an impressive combination of high прочность на разрыв, low плотность, and excellent коррозионная стойкость. This makes it ideal for demanding environments, such as those found in аэрокосмическая промышленность and marine applications. However, magnesium alloys also deserve consideration. They are the lightest structural металл available, with a плотность significantly lower than that of сталь и алюминий.
В то время как магний might not match the прочность на разрыв из титан, it provides a substantial соотношение прочности и веса, making it suitable for applications where weight is a primary concern. For example, in the automotive industry, magnesium alloy components can significantly reduce vehicle weight, improving fuel efficiency. For high-performance Легкий structural components in the аэрокосмическая промышленность and military sectors, the high прочность на разрыв и коррозионная стойкость из titanium and titanium alloys make them the preferred choice.
Magnesium alloys are commonly used in military applications. are renowned for their extremely light weight, being about 33% lighter than алюминий and 75% lighter than сталь. This makes them particularly attractive for applications where weight reduction is crucial. From a personal standpoint, I’ve found that magnesium’s machinability is superior to many other metals, allowing for intricate and precise designs. Обработка с ЧПУ is often more efficient with магний, leading to cost savings in production.
По сравнению с алюминиевый сплав, magnesium alloy offers better damping capacity and electromagnetic shielding. However, алюминиевые сплавы generally have superior коррозионная стойкость and are more широко используемый in structural applications due to their higher strength. Титан, on the other hand, surpasses both магний и алюминий in terms of strength and коррозионная стойкость, but it is significantly more expensive. The choice between these metal alloys often depends on the specific application and budget constraints. The inherent преимущества, like the low weight of magnesium alloys, make them an attractive choice in various applications.
Despite their many advantages, magnesium alloys do have some drawbacks. One notable недостаток is their susceptibility to corrosion, particularly in the presence of salt water or other corrosive agents. This can limit their use in marine and certain промышленное применение unless protective coatings are applied. Another concern is their relatively low melting point and potential flammability, which can be a safety issue in высокотемпературные среды.
Additionally, while магний offers a good соотношение прочности и веса, it generally has lower absolute strength compared to титан and certain алюминиевые сплавы. This can be a limiting factor in applications that require extremely высокая прочность. Disadvantages of magnesium alloys also include their lower теплопроводность по сравнению с алюминий, which can be a concern in heat dissipation applications. Despite these limitations, advancements in alloying and surface treatments are continually improving the performance and applicability of магний в различных отраслях промышленности.
Титан‘s exceptional properties make it a preferred choice in both the аэрокосмическая промышленность and medical industries. In аэрокосмическая промышленность, its high соотношение прочности и веса, отличный коррозионная стойкость, and ability to withstand высокие температуры are invaluable. Titanium alloy components are used in aircraft engines, airframes, and other critical parts where reliability and performance are non-negotiable. Its lightweight properties also contribute to fuel efficiency and overall aircraft performance.
In the medical field, титан‘s biocompatibility is a major advantage. It is non-toxic and does not react with the human body, making it ideal for implants, surgical instruments, and medical devices. Its коррозионная стойкость ensures longevity and safety in medical applications. Moreover, титан‘s strength and durability provide the necessary support and stability for orthopedic implants. The combination of these properties makes титан a vital material in both аэрокосмическая промышленность and medical applications.
Aluminum and steel have long been staple materials in various industries, but modern lightweight alloys are increasingly challenging their dominance. Алюминий, known for its lightness and коррозионная стойкость, is about one-third the density of steel. It offers good thermal and electrical проводимость, making it suitable for a wide range of applications, including automotive parts, packaging, and construction. However, compared to титан and some advanced magnesium alloys, алюминий has lower прочность на разрыв These alloys may not be suitable for high-stress environments, especially in engineering applications.
Стальв частности углеродистая сталь и high-strength steel, is valued for its strength, durability, and cost-effectiveness. It remains a primary material in construction, automotive, and heavy machinery. However, its high плотность makes it less desirable in applications where weight is a critical factor. Modern lightweight materials, такие как magnesium and titanium alloys, offer significant weight reductions without compromising strength, making them increasingly popular in аэрокосмическая промышленность, automotive, and other industries focused on efficiency and performance. Using the aforementioned металлы as alternatives for сталь provides numerous benefits.
Lightweight materials play a crucial role in defense applications, where reducing weight can enhance mobility, speed, and fuel efficiency. In military vehicles, using lightweight alloys например, титан и продвинутый алюминиевые сплавы can improve maneuverability and reduce fuel consumption. Additionally, lightweight Composites made of lightweight materials are increasingly popular in various applications. are used in body armor to provide protection without adding excessive weight, enhancing soldier mobility and endurance. Lightweight materials for defense applications also include materials used in aircraft, drones, and naval vessels.
Использование lightweight materials in body armor is particularly noteworthy. Advanced композиты и lightweight alloys provide high levels of protection while minimizing the burden on soldiers. Similarly, Легкий projectiles and missile radomes benefit from these materials, offering improved performance and range. Lightweight materials are essential for modernizing defense equipment and ensuring operational effectiveness. Recent research on сплавы и металл matrices has focused on developing new lightweight composites.
Lightweight design in engineering involves selecting materials and optimizing structures to minimize weight while maintaining or improving performance. Key considerations include the соотношение прочности и веса, коррозионная стойкость, и thermal properties of the materials used. Engineers must also consider the specific requirements of the application, such as the operating environment, load conditions, and expected lifespan of the product. As a company specializing in Услуги по изготовлению изделий с ЧПУ, we understand the intricacies of working with different металлы и сплавы. Наш опыт в Прецизионная обработка allows us to create high-quality, Легкий components tailored to our clients’ needs.
Another important aspect of lightweight design is the use of advanced manufacturing techniques, such as Фрезерование с ЧПУ и Токарная обработка с ЧПУ. These methods allow for the creation of complex shapes and precise components from lightweight metals и сплавы. Additionally, simulation and modeling tools are used to predict the behavior of Легкий structures under various conditions, ensuring their reliability and safety. Integrating these considerations into the design process is essential for achieving optimal Легкий решения.
Advanced lightweight materials are revolutionizing промышленное применение by enabling the development of more efficient, durable, and sustainable products. These materials, including advanced сплавы, композиты, and hybrid materials, offer enhanced properties such as improved соотношение прочности и веса, коррозионная стойкость, и thermal management. The use of graphene as reinforcements in металл matrices is an example of cutting-edge research aimed at creating futuristic materials with exceptional properties.
В автомобильной промышленности, advanced lightweight materials are used to manufacture Легкий vehicles with improved fuel efficiency and reduced emissions. In аэрокосмическая промышленность, these materials are essential for creating lighter, more fuel-efficient aircraft. The construction industry benefits from Легкий materials that simplify installation and reduce structural loads. Even in consumer products, Легкий materials enhance portability and performance. The ongoing development and adoption of lightweight materials are transforming engineering applications. advanced lightweight materials are driving innovation and shaping the future of various industries.
Lightweight metals например, алюминий, магний, и титан are significantly lighter than сталь due to their lower densities. For instance, алюминий is about one-third the density of steelв то время как магний is even lighter. Despite their lower weight, these металлы can offer comparable or even superior strength when properly alloyed and processed. The key lies in their atomic structure and the ability to form strong bonds within the сплав.
Титан, for example, has a very high соотношение прочности и веса due to its strong metallic bonds and the ability to form сплавы Alloys are often combined with other elements that further enhance their strength compared to traditional materials. Magnesium alloys, while not as strong as титан, can be engineered to provide sufficient strength for many applications while maintaining their Легкий advantage. The development of advanced сплавы and processing techniques continues to improve the strength and performance of lightweight metals, making them viable alternatives to сталь во многих приложениях.
What makes magnesium alloys suitable for electronic applications?
Magnesium alloys are excellent for electronic applications due to their superior electromagnetic shielding properties and good теплопроводность. They effectively dissipate heat, making them ideal for components like heat sinks and electronic housings.
How do titanium alloys benefit the aerospace industry?
Титановые сплавы are crucial in the аэрокосмическая промышленность industry due to their high соотношение прочности и веса, отличный коррозионная стойкость, and ability to withstand extreme temperatures. These properties enhance aircraft performance, fuel efficiency, and longevity.
What are the main challenges in using lightweight materials for defense?
The main challenges include ensuring sufficient protection, durability, and resistance to environmental factors. Balancing weight reduction with the need for robust performance under harsh conditions is also critical.
Can lightweight metals replace steel in construction?
Да, lightweight metals например, алюминий и продвинутый композиты can replace сталь in certain construction applications. They offer benefits such as reduced structural load, ease of installation, and коррозионная стойкость, although the specific application requirements must be considered.
What is the future of lightweight materials in automotive manufacturing?
The future looks promising, with ongoing advancements in lightweight alloys и композиты leading to more fuel-efficient and environmentally friendly vehicles. Innovations in materials like магний и титановые сплавы will further enhance vehicle performance and reduce emissions.
Why are lightweight materials important for renewable energy technologies?
Lightweight materials are vital for renewable energy technologies because they improve the efficiency and performance of devices like wind turbines and solar panels. Reducing the weight of these components makes them easier to install and more cost-effective, contributing to the overall sustainability of renewable energy solutions.
Lightweight metal alloys offer significant advantages in various industries, including improved fuel efficiency, enhanced performance, and excellent коррозионная стойкость.
Титан и magnesium alloys are among the best lightweight metals for high-strength applications, each with unique properties suited to different needs.
Magnesium alloys provide exceptional lightness and machinability but have limitations in corrosion resistance and absolute strength.
Титан is preferred in аэрокосмическая промышленность and medical fields due to its high соотношение прочности и веса, biocompatibility, and коррозионная стойкость.
Lightweight materials play a crucial role in defense applications, enhancing mobility, protection, and operational effectiveness.
Lightweight design requires careful consideration of material properties, manufacturing techniques, and application requirements.
Advanced lightweight materials are shaping the future of промышленное применение, driving innovation and sustainability.
Lightweight metals can match or exceed the strength of сталь while being significantly lighter due to their atomic structure and alloying capabilities.
Ongoing research and development continue to improve the properties and applications of lightweight materials, ensuring their growing importance in modern manufacturing.
Наш опыт в Отделка поверхности ensures that the final product meets the highest standards of quality and durability.
Понимание преимущества и недостатки of different lightweight metal alloys and staying informed about the latest advancements, industries can leverage these materials to create innovative, efficient, and high-performance products. At Изготовление с ЧПУ, we are dedicated to providing top-notch Услуги по изготовлению изделий с ЧПУ to meet the diverse needs of our clients across various sectors. Whether you need prototypes through our Быстрое прототипирование service or large-scale production through Производство по требованию, we have the expertise and technology to deliver exceptional results.
As we look to the future, the continued development and adoption of lightweight materials will undoubtedly play a pivotal role in advancing technology and improving the quality of products across numerous industries.
Адрес
No.30, Hongbang Industry Park, Шэньчжэнь
Электронная почта
[email protected]
Телефон
+86 15586668226
Узнайте о последних тенденциях и фактах в области производства с ЧПУ из нашего блога.
Shenzhen Runkey Precision Technology Co. Ltd, дочерняя компания Tensun Group, является вашим надежным универсальным решением для производства на заказ от прототипа до производства. Превращение вашей идеи в реальность с помощью цифровых производственных ресурсов, оптимизированных процессов, экспертного руководства, ускоренных сроков и бескомпромиссного качества.
©2024. CNC Fabrication Все права защищены.