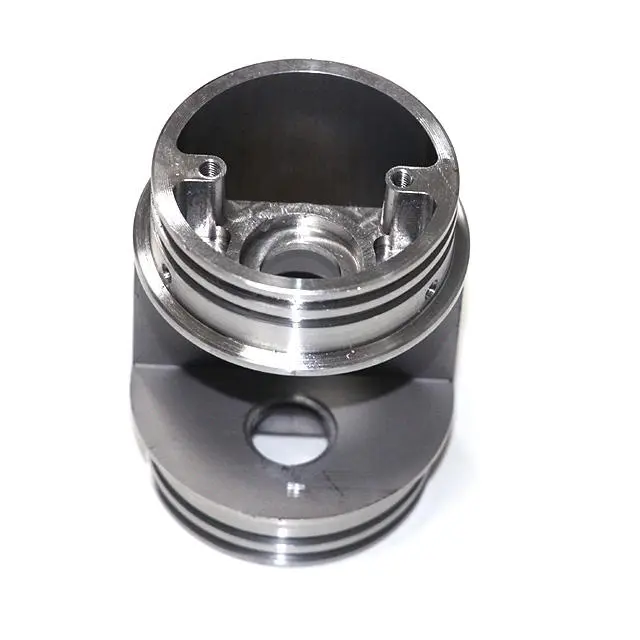
- +8615586668226
- [email protected]
- No. 30, Hongbang Industrial Park, Shenzhen
Tolerancia na stránke CNC obrábanie refers to the permissible variation for a specific dimension of a obrábaný diel. It defines the acceptable range of deviation from the nominal dimension, usually represented as a plus or minus value. For instance, if a dimension is specified as 10 mm s tolerancia of ±0.1 mm, the actual dimension can range from 9.9 mm to 10.1 mm. As a representative of a Výroba CNC services manufacturing plant, I can attest to the critical role tolerancia plays. It’s the backbone of precision in our industry.
Prečo tolerancia matter? Imagine assembling a complex machine like an aircraft engine. Every component must fit perfectly to ensure optimal performance and safety. Prísne tolerancie are crucial in such cases. If the parts don’t fit within the specified tolerancia, the entire assembly can fail. This is why, at our CNC obrábanie service plant, we emphasize the importance of machining s vysokou presnosť. Podľa mojich skúseností, tighter tolerances often translate to higher quality, but they also come with increased costs and production time. A tolerancia of ±0.001″ is incredibly tight and requires specialized equipment and expertise. Striking the right balance between cost and quality is a key aspect of our job.
Standard machining tolerances are predefined tolerancia values typically used when a dimension doesn’t have a specified tolerancia. Tieto stránky standard tolerances are based on the International Organization for Standardization (ISO) standards, such as ISO 2768, and provide a general guideline for obrábanie. Standard tolerance values are categorized into different classes, such as “fine,” “medium,” and “coarse,” based on the tolerancia range and the dimension’s nominal size. When I first started in the industry, understanding these classifications was crucial.
Vplyv standard machining tolerances on your projects can be significant. Using standard tolerance values can simplify the design process, as they provide a ready-made tolerancia framework. However, relying solely on standard tolerances might not be suitable for all applications. For instance, if you’re designing a critical component for a medical device, you might need tighter tolerances than what the “fine” class under ISO 2768 offers. This requires deeper collaboration between engineers and CNC experts to achieve the right level of precision. At our plant, we often engage in detailed discussions with clients to understand their specific needs and guide them toward the most appropriate tolerancia choices. Understanding the tolerancia needs from the outset can save time and resources. The American Society of Mechanical Engineers provides useful guidelines in these situations.
In the world of CNC obrábanie, understanding the different types of tolerances is fundamental. Tolerancia defines the allowable variation in a dimension, and it can be expressed in three main ways: jednostranná tolerancia, bilaterálna toleranciaa limit tolerance. Each type serves a distinct purpose and impacts the design and manufacturing process differently.
Jednostranná tolerancia umožňuje odchýlku len v jeden smer from the nominal size. For example, if a dimension is specified as 10 mm s jednostranná tolerancia of +0.1 mm, the actual dimension can range from 10 mm to 10.1 mm, but not below 10 mm. This type of tolerancia is often used when a part needs to fit into a specific space or mate with another component in a particular way. We often recommend jednostranná tolerancia in designs where clearance or interference fits are critical.
Bilateral tolerances allow variation in both directions from the nominal size. A common example is a dimension specified as 10 mm ±0.1 mm. This means the actual dimension can range from 9.9 mm to 10.1 mm. Bilaterálna tolerancia is versatile and commonly used in general CNC obrábanie applications. They offer a balanced approach to dimensional control, making them a popular choice in many projects.
Limit tolerance určuje horné a dolné limity of a dimension directly. For instance, a limit tolerance might be expressed as 9.9 mm to 10.1 mm. This method clearly defines the allowable range without needing a nominal size and a plus/minus value. We often use limit tolerance v našom Výroba CNC plant when the absolute limits are critical, and the nominal size is less important.
Výber správneho typu tolerancia závisí od konkrétnych požiadaviek vášho projektu. Jednostranné tolerancie are ideal for ensuring a part fits in one specific direction, while bilateral tolerances offer a more balanced approach. Limit tolerances provide clear, direct limits that can be crucial for certain applications. It is dôležité to be clear when you specify these.
Typical machining tolerances sa líšia v závislosti od proces obrábania used. For example, CNC frézovanie typically achieves a standard tolerance of around ±0.1 mm (±0.004 inches). However, with specialized equipment and skilled operators, tighter tolerances down to ±0.025 mm (±0.001 inches) or even better can be achieved. When customers approach us with requirements for vysoká presnosť, we often suggest presné obrábanie techniques combined with processes like grinding or lapping to meet those needs.
CNC sústruženie, on the other hand, generally offers slightly tighter tolerances compared to milling. A standard tolerance pre CNC sústruženie is around ±0.05 mm (±0.002 inches), and with extra care, tolerances as tight as ±0.01 mm (±0.0004 inches) are achievable. In our strojárska dielňa, we’ve successfully delivered parts with even tighter tolerances for specialized applications, such as in the aerospace industry. It’s important to remember that achieving these prísne tolerancie often requires multiple passes, specialized rezné nástroje, and careful monitoring of the proces obrábania.
Iné obrábanie methods, such as drilling or boring, have their own typical tolerancia ranges. Drilling usually has a wider tolerancia, around ±0.2 mm (±0.008 inches), while boring can achieve tolerancie podobne ako CNC sústruženie. Grinding is a process known for its presnosť, often used to achieve very prísne tolerancie, in the range of ±0.005 mm (±0.0002 inches) or better. Each obrábanie method has its strengths and limitations when it comes to tolerancia, and understanding these nuances is crucial for selecting the right process for your project. It is important to know the tolerančné pásmo that you need. Materials and machining go hand in hand for these projects.
Specifying tolerancie accurately is crucial for ensuring that your CNC obrábané diely meet the required specifications. The first step is to identify the critical dimensions and features of your part. Consider which dimensions directly affect the part’s functionality, fit, and assembly with other components. Once you’ve identified these critical dimensions, you can start assigning appropriate tolerancie. A good starting point is to consider standard machining tolerances based on ISO standards like ISO 2768. However, always evaluate whether these standard tolerances are sufficient for your specific application.
When specifying tolerancie, use clear and unambiguous notation. For bilateral tolerances, use the ± symbol followed by the tolerancia value. For example, 20 mm ±0.1 mm indicates that the dimension can vary from 19.9 mm to 20.1 mm. Pre jednostranné tolerancie, specify the direction of the allowable variation, such as 20 mm +0.1 mm/-0 mm. This means the dimension can range from 20 mm to 20.1 mm but cannot be smaller than 20 mm. Limit tolerances are specified by providing the maximum and minimum allowable dimensions, for example, 19.9 mm – 20.1 mm.
It’s also essential to consider the tolerancia stack-up in assemblies. Tolerancia stack-up refers to the cumulative effect of tolerancie when multiple parts are assembled. Each part’s tolerancia contributes to the overall variation in the assembly. To minimize tolerancia stack-up issues, carefully analyze how the tolerancie of individual parts interact and affect the final assembly dimensions. In our Výroba CNC plant, we often use advanced simulation tools to predict and manage tolerancia stack-up, ensuring that the final product meets the required specifications. When you are dealing with multiple part tolerances it is easy for errors to occur.
Geometric Dimensioning and Tolerancing (GD&T) is a symbolic language used to define a part’s geometry and its allowable variation. It goes beyond basic dimensional tolerancie by specifying the geometric characteristics of features, such as form, orientation, location, and runout. GD&T uses a set of standardized symbols and rules defined by the American Society of Mechanical Engineers (ASME) Y14.5 standard or ISO equivalents.
GD&T plays a crucial role in modern CNC obrábanie by providing a more comprehensive and precise way to define a part’s requirements. For example, GD&T can specify the true position of a hole, which not only controls its location but also its perpendicularity to a surface. This level of control is often necessary for parts that need to interface precisely with other components. In my experience, GD&T helps to have better communication between design and manufacturing.
One of the key benefits of GD&T is that it defines the function and relationship of features, rather than just their size and location. For instance, profile tolerances can control the shape of a complex surface, ensuring that it fits correctly with a mating part. GD&T tolerances can be more complex to learn, but they offer much greater control over the final part. At our Výroba CNC plant, we’ve found that using GD&T reduces ambiguity and misinterpretation, leading to fewer errors and higher-quality parts. GD&T is particularly useful for complex parts with tight požiadavky na toleranciu, such as those used in aerospace, medical devices, and other vysoko presné aplikácie.
Dosiahnutie prísna tolerancia na stránke CNC obrábanie requires a combination of factors, including the right equipment, skilled operators, and a well-defined process. Prísne tolerancie refer to very small allowable variations, often in the range of ±0.01 mm (±0.0004 inches) or even tighter. One of the first considerations is the CNC stroj itself. High-presnosť machines with advanced features like linear motors, high-resolution encoders, and thermal stabilization are essential for achieving prísne tolerancie. Regular maintenance and calibration of these machines are also critical.
Another crucial factor is the choice of rezné nástroje. High-quality, sharp rezné nástroje designed for specific materials and operations can significantly impact the achievable tolerancia. Tool wear must be monitored closely, as worn tools can lead to dimensional inaccuracies. In our strojárska dielňa, we use advanced tool management systems to track tool life and ensure that tools are replaced or sharpened before they affect part quality. CNC screw machining also plays a role here.
Stránka obrábanie process itself also plays a vital role. Techniques like using multiple finishing passes, optimizing cutting parameters (speed, feed, depth of cut), and employing advanced strategies like high-speed obrábanie or trochoidal milling can help achieve tighter tolerances. Additionally, using specialized techniques like grinding, lapping, or honing as secondary processes can further refine dimensions and achieve extremely prísne tolerancie. It’s also important to consider the material being machined, as some materials are more challenging to machine to prísne tolerancie than others. This is where working with experienced machinists can make a big difference.
International standards for machining tolerances provide a common framework for specifying and interpreting tolerancie globally. The most widely recognized standards are those published by the International Organization for Standardization (ISO). ISO 2768 is a commonly used standard that defines general tolerancie for linear and angular dimensions. It specifies four tolerancia classes: f (fine), m (medium), c (coarse), and v (very coarse). Each class defines a tolerance range based on the nominal size of the dimension. These types of standardized tolerances make understanding requirements much simpler.
Another important ISO standard is ISO 286, which defines a system of limits and fits. It specifies tolerancia grades (IT grades) that define the tolerancia range for holes and shafts. IT grades range from IT01 to IT18, with lower numbers indicating tighter tolerances. For example, IT6 is a common tolerancia grade for precision fits, while IT11 might be used for looser clearance fits. These engineering tolerances are essential for anyone in the machining industry.
In addition to ISO standards, some industries use standards published by other organizations. For instance, the aerospace industry often uses standards developed by SAE International. These standards often build upon ISO standards but may include additional requirements or stricter tolerancie specific to aerospace applications. When working with international clients, we often encounter various standards. Being familiar with these different standards helps ensure that we meet all specified requirements. Understanding and adhering to these international standards is essential for ensuring consistency, quality, and interoperability in CNC obrábanie across different countries and industries.
The choice of material significantly impacts the achievable tolerancia na stránke CNC obrábanie. Different materials have varying properties, such as hardness, thermal expansion, and machinability, which can affect dimensional stability and the presnosť z proces obrábania. For example, softer materials like aluminum and brass are generally easier to machine and can achieve tighter tolerances compared to harder materials like stainless steel or titanium. This is something we always discuss with clients during the material selection phase.
Harder materials often require more robust rezné nástroje, slower cutting speeds, and more frequent tool changes, which can impact the achievable tolerancia. Additionally, some materials are more prone to thermal expansion or contraction during obrábanie, which can affect dimensional accuracy. In our Výroba CNC plant, we work with a wide range of materials and have developed specific strategies for each to ensure optimal tolerancia control. For instance, when obrábanie stainless steel, we often use specialized coolant systems to manage heat and maintain dimensional stability. We also consider plating and finishes in this stage.
Stránka spôsob obrábania itself also influences the achievable tolerancia. As mentioned earlier, processes like CNC frézovanie a CNC sústruženie have different typical tolerancia ranges. Presné obrábanie techniques, such as grinding or honing, can achieve much tighter tolerances compared to conventional obrábanie methods. The choice of spôsob obrábania závisí od konkrétneho požiadavky na toleranciu, the complexity of the part, and the material being machined. We often combine different obrábanie methods to achieve the desired results. For example, we might start with CNC frézovanie to remove most of the material and then use grinding to achieve the final dimensions and prísne tolerancie.
Determining tolerances is a critical aspect of the design process that requires careful consideration of various factors. One of the first steps is to understand the function of the part and how it interacts with other components in an assembly. This will help identify the critical dimensions that require prísne tolerancie and those that can have looser tolerancie. It’s also essential to consider the manufacturing process that will be used to produce the part. Different obrábanie methods have varying capabilities when it comes to achieving tolerancie, so it’s crucial to choose a process that can meet the required presnosť.
Another best practice is to use standard tolerances whenever possible. Standards like ISO 2768 provide a good starting point for assigning tolerancie to non-critical dimensions. This can simplify the design process and reduce the risk of errors. However, always evaluate whether these standard tolerances are sufficient for your specific application. For critical dimensions, it’s often necessary to perform a detailed tolerancia analysis, considering factors like tolerancia stack-up, material properties, and environmental conditions.
Collaboration between designers, engineers, and machinists is also crucial for determining tolerances. Designers should consult with experienced machinists to understand the capabilities and limitations of the obrábanie process. This can help avoid specifying tolerancie that are unnecessarily tight or difficult to achieve, which can increase costs and lead times. In our Výroba CNC plant, we encourage early collaboration between our clients’ design teams and our obrábanie experts. This collaborative approach helps ensure that the specified tolerancie are realistic, achievable, and cost-effective. Finding the right tolerance for each project is essential.
Here is a simple table to illustrate some key points:
Aspekt | Popis |
Tolerancia | Permissible variation in dimension. Essential for part functionality and assembly. |
Standard Tolerance | Predefined values (e.g., ISO 2768) simplify design but may not suit all applications. |
Tight Tolerance | Very small allowable variations, often ±0.01 mm or better. Requires specialized equipment and processes. |
GD&T | Geometric Dimensioning and Tolerancing. Provides comprehensive control over part geometry beyond basic dimensional tolerancie. |
Material Impact | Material properties affect achievable tolerancia. Softer materials generally allow for tighter tolerances than harder ones. |
Process Impact | Rôzne obrábanie methods have varying tolerancia schopnosti. Presnosť techniques like grinding offer the najprísnejšie tolerancie. |
What is the difference between unilateral and bilateral tolerance?
Jednostranná tolerancia allows variation in only one direction from the nominal size, while bilaterálna tolerancia allows variation in both directions. For example, a jednostranná tolerancia might be 10 mm +0.1 mm/-0 mm, zatiaľ čo a bilaterálna tolerancia would be 10 mm ±0.1 mm. Choosing between them depends on how a part needs to fit or function within an assembly.
How tight of a tolerance can CNC machining achieve?
CNC obrábanie can achieve very prísne tolerancie, often down to ±0.01 mm (±0.0004 inches) or even better with specialized equipment and processes. High-precision machines, specialized rezné nástroje, and techniques like grinding or honing can further refine dimensions to achieve extremely prísne tolerancie, sometimes in the range of ±0.005 mm (±0.0002 inches) or less.
What is a standard tolerance in CNC machining?
A standard tolerance na stránke CNC obrábanie refers to predefined tolerancia values that are commonly used when a dimension doesn’t have a specified tolerancia. Tieto stránky standard tolerances are often based on international standards like ISO 2768, which defines general tolerances for linear and angular dimensions. They are categorized into different classes like “fine,” “medium,” and “coarse,” providing a general guideline for obrábanie. Používanie stránky standard machining tolerances can greatly simplify the process.
How does material choice affect machining tolerance?
Material choice significantly impacts achievable tolerancia. Softer materials like aluminum and brass are generally easier to machine and can achieve tighter tolerances compared to harder materials like stainless steel or titanium. Material properties such as hardness, thermal expansion, and machinability all play a role in determining how precisely a part can be machined.
What is GD&T, and why is it important?
Geometric Dimensioning and Tolerancing (GD&T) is a system for defining and communicating engineering tolerancie. It uses a symbolic language to specify the allowable variation in part geometry, including form, orientation, location, and runout. GD&T is important because it provides a more comprehensive and precise way to define a part’s requirements compared to using only basic dimensional tolerancie. It helps ensure that parts fit and function correctly in an assembly, especially for complex components with prísna tolerancia požiadavky. GD&T also helps reduce ambiguity and misinterpretation between design and manufacturing.
How can I ensure my CNC machined parts meet the specified tolerances?
To ensure your CNC obrábané diely meet the specified tolerancie, it’s essential to work with an experienced CNC obrábanie service provider that has the right equipment, skilled operators, and a robust quality control process. Clearly communicate your požiadavky na toleranciu, use appropriate tolerancia notations, and consider using GD&T for critical dimensions. Regular communication between your design team and the obrábanie experts can also help ensure that everyone understands the requirements and that the parts are produced to the correct specifications.
Tolerancia is the permissible variation in a dimension and is crucial for part functionality and assembly.
Standard machining tolerances, based on standards like ISO 2768, provide a general guideline but may need adjustment for specific applications.
Unilateral, bilaterálnea limit tolerances offer different ways to specify allowable variation, each with its own use cases.
Prísne tolerancie require specialized equipment, rezné nástrojea obrábanie procesy.
GD&T provides a comprehensive way to define part geometry and tolerancie, going beyond basic dimensional tolerancie.
Material choice and obrábanie method significantly influence achievable tolerancia.
Collaboration between designers and machinists is essential for determining realistic and cost-effective tolerancie.
Adhering to international standards for machining tolerances ensures consistency and quality in global manufacturing.
As an experienced professional in the Výroba CNC industry, I’ve seen firsthand how crucial understanding machining tolerances is for producing high-quality parts. Whether you’re designing a simple bracket or a complex aerospace component, paying attention to tolerancie can make the difference between success and failure. I hope this comprehensive guide has provided you with valuable insights into the world of CNC machining tolerances. Remember, presnosť is not just about hitting the numbers; it’s about ensuring that every part fits perfectly, functions flawlessly, and contributes to the overall success of your project. If you have a project requiring Výroba na požiadanie, contact us today, we are experts in CNC obrábanie and will be able to assist you with your needs. Our Výrobné služby are second to none, utilizing Výroba plechov a Vytláčanie hliníka. Naše odborné znalosti sa vzťahujú na Povrchová úprava, ensuring every project meets the highest standards of quality and precision.
Získajte najnovšie trendy a fakty o výrobe CNC z nášho blogu.
Shenzhen Runkey Precision Technology Co. Ltd, dcérska spoločnosť skupiny Tensun Group, je dôveryhodným komplexným riešením pre zákazkovú výrobu od prototypov až po výrobu.Transformuje váš nápad na realitu pomocou digitálnych výrobných zdrojov, zefektívnených procesov, odborného poradenstva, zrýchlených termínov a nekompromisnej kvality.
©2024. Všetky práva vyhradené.