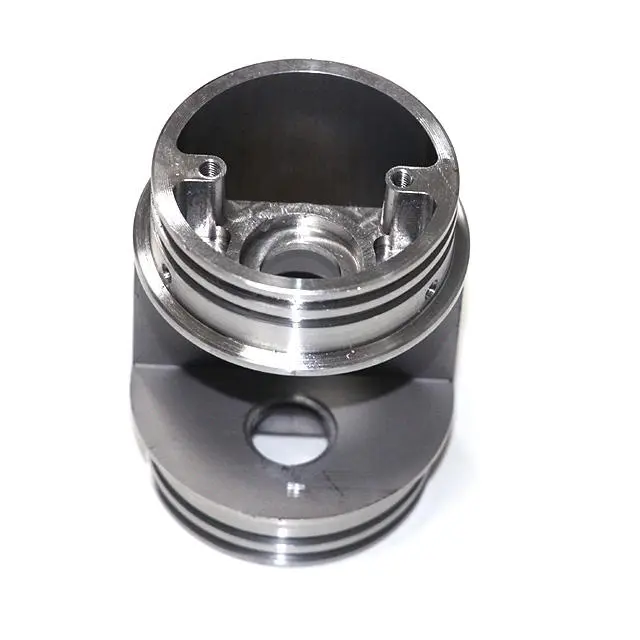
- +8615586668226
- [email protected]
- No. 30, Hongbang Endüstri Parkı, Shenzhen
1018 çelik düşük karbonlu veya hafif bir Çelikmükemmel işlenebilirliği ve kaynaklanabilirliği ile bilinir. Lider bir tedarikçi olarak CNC imalat hizmetlerisık sık tavsiye ediyoruz 1018 çelik şekillendirilebilirlik, mukavemet ve maliyet etkinliği dengesi gerektiren projeler için uygundur. 1018 çelik çok yönlülüğü ve işleme kolaylığı nedeniyle otomotiv parçalarından inşaat bileşenlerine kadar çeşitli uygulamalarda yaygın olarak kullanılmaktadır.
1018 çelik bir karbon çeliği sünekliğine ve tokluğuna katkıda bulunan yaklaşık 0,18% karbon içerir. Genellikle yüksek mukavemet gerektirmeyen parçalarda kullanılır. güç ancak iyi şekillendirilebilirlikten yararlanır. Bu tip Çelik gerektiren uygulamalar için idealdir. CNC işleme delme, tornalama ve frezeleme gibi işlemler. Üretim tesisimiz şunları kullanır 1018 çelik çeşitli endüstriler için yüksek kaliteli bileşenler oluşturmak, her parçada hassasiyet ve tutarlılık sağlamak. Sıklıkla karşılaştığımız 1018 çelik Kaliteden ödün vermeden uygun maliyetli çözümlerin çok önemli olduğu projelerde.
4140 çelik bir alaşımlı çelik yüksek kalitesi ile ünlü güç, sertlikve dayanıklılığı, onu zorlu uygulamaların gözdesi haline getiriyor. Benim görevimde CNC imalat hizmetleriGördüm. 4140 çelik havacılık, otomotiv ve ağır ekipman endüstrilerinde yaygın olarak kullanılmaktadır. Üstün özellikleri mekani̇k özelli̇kler içeren benzersiz bileşiminden kaynaklanmaktadır. krom ve molibdensertleşebilirliğini ve aşınma direncini arttırır.
4140 çelik bir alaşımlı çelik yaklaşık 1% krom, 0,2% molibden ve 0,4% karbon içerir. Bu bileşim ona üstünlük kazandırır güç ve sertlik ile karşılaştırıldığında 1018 çelik. Isıl işlem uygulandığında, 4140 çelik olağanüstü tokluk ve dayanıklılık sunarak yüksek gerilimli uygulamalar için uygun hale getirir. Bu bir Brinell sertliği Isıl işleme bağlı olarak 197 ila 241 arasında değişir. Üretim tesisimizde şunları kullanıyoruz 4140 çelik Dişliler, şaftlar ve akslar gibi yüksek dayanıklılık gerektiren bileşenler için. Bu Çelik sağlam ve güvenilir malzemeler gerektiren sektörler için çok önemlidir. Biz kullanıyoruz 4140 çelik Aşırı koşullar altında üstün performans gerektiren bileşenler için.
Karşılaştırma yaparken 1018 ve 4140 çeliktemel farklılıklar bileşimlerinde yatmaktadır, mekani̇k özelli̇klerve amaçlanan uygulamalar. 1018 çelikdüşük karbonlu olmak Çelikmükemmel işlenebilirlik ve kaynaklanabilirlik sunar, ancak daha düşük güç daha 4140 çelik. Bu işle yakından ilgilenen biri olarak CNC imalat hizmetleriBu farklılıkları anlamanın, her proje için doğru malzemeyi seçmek açısından çok önemli olduğunu düşünüyorum.
İşte temel farklılıkları özetleyen bir tablo:
Özellik | 1018 Çelik | 4140 Çelik |
Karbon İçeriği | Düşük (yaklaşık 0,18%) | Orta (yaklaşık 0,40%) |
Alaşım Elemanları | Minimal | Krom, Molibden |
Güç | Orta düzeyde | Yüksek |
Sertlik | Daha düşük | Daha yüksek |
İşlenebilirlik | Mükemmel | İyi, ancak 1018'den az |
Kaynaklanabilirlik | Mükemmel | İyi, ancak ön ısıtma ve son ısıtma gerektirebilir |
Maliyet | Daha düşük | Daha yüksek |
Tipik Kullanımlar | Genel imalat, düşük gerilimli bileşenler | Yüksek gerilimli bileşenler, aletler, makine parçaları |
Isıl İşlem | Tipik olarak ısıl işlem görmemiş | Gelişmiş özellikler için genellikle ısıl işlem görmüş |
4140 çelikdiğer taraftan, bir alaşımlı çelik gibi daha yüksek karbon içeriğine ve alaşım elementlerine sahip krom ve molibden. Bu bileşim ona üstün güç ve sertlikBu da onu yüksek stresli uygulamalar için ideal hale getirir. Bizim CNC imalat hizmetlerisık sık tavsiye ediyoruz 4140 çelik olağanüstü dayanıklılık ve aşınma direnci gerektiren parçalar için. İçindeki alaşım elementleri 4140 çelik gelişmiş sertleşebilirlik sağlayarak ağır yüklere ve zorlu ortamlara maruz kalan bileşenler için tercih edilen bir seçim haline getirir.
Bu mekani̇k özelli̇kler . 1018 ve 4140 çelik önemli ölçüde farklılık göstermekte ve çeşitli uygulamalar için uygunluklarını etkilemektedir. 1018 çelik daha düşük bir gerilime sahiptir güç ve sertlik ile karşılaştırıldığında 4140 çelikAncak süneklik ve tokluk açısından üstündür. Bu özellikler 1018 çelik Çatlama olmadan bükme, şekillendirme veya kaynak gerektiren parçalar için idealdir.
4140 çelik daha yüksek gerilme sağlar güç ve sertliközellikle ısıl işlem uygulandığında. Eklenmesi krom ve molibden aşınma direncini ve tokluğunu artırarak yüksek stres ve sürtünmeye maruz kalan dişliler, miller ve akslar gibi bileşenler için uygun hale getirir. Deneyimlerimize göre CNC imalat hizmetleribulduk ki 4140 çelik üstün mekani̇k özelli̇kler zorlu endüstriyel uygulamalar için güvenilir bir seçim haline getirir. Bu Brinell sertliği . 4140 çelik ısıl işleme bağlı olarak 241'e kadar ulaşabilir ve mükemmel aşınma direnci sağlar.
İşlenebilirlik seçerken çok önemli bir faktördür Çelik üretim süreçleri için. 1018 çelik düşük karbon içeriği ve minimum alaşım elementleri nedeniyle mükemmel işlenebilirliği ile ünlüdür. Bu da kesmeyi, delmeyi ve şekillendirmeyi kolaylaştırarak takım aşınmasını azaltır ve üretim verimliliğini artırır. Bizim CNC imalat hizmetlerisık sık kullandığımız 1018 çelik Daha hızlı işleme ve daha düşük üretim maliyetleri sağladığından, kapsamlı işleme operasyonları gerektiren parçalar için.
4140 çelikhala işlenebilir olsa da, aşağıdakilere kıyasla daha fazla zorluk sunar 1018 çelik. Yüksek karbon ve alaşım içeriği, özellikle krom ve molibdenartırmak sertlik ve güçBu da takım aşınmasının artmasına ve işleme hızının düşmesine neden olur. Bununla birlikte, doğru kesici takımlar ve tekniklerle, 4140 çelik etkili bir şekilde işlenebilir. Deneyimlerimiz, karbür takımların kullanılmasının ve kesme parametrelerinin optimize edilmesinin işlenebilirlik . 4140 çelikyüksek kaliteli bitmiş parçalar sağlar. Ön ısıtma ve son ısıtma yapmak çok önemlidir 4140 çelik Çatlamayı önlemek için kaynak sırasında.
Kaynaklanabilirlik, aşağıdakiler arasında seçim yaparken dikkate alınması gereken bir diğer kritik husustur 1018 ve 4140 çelik. 1018 çelik düşük karbon içeriği sayesinde mükemmel kaynaklanabilirliği ile bilinir. Özel ön ısıtma veya son ısıtma prosedürleri gerektirmeden MIG, TIG ve çubuk kaynağı dahil olmak üzere çeşitli yöntemler kullanılarak kolayca kaynak yapılabilir. Bu sayede 1018 çelik kaynak içeren imalat projeleri için popüler bir seçimdir.
4140 çelikyüksek karbon ve alaşım içeriği nedeniyle daha dikkatli kaynak teknikleri gerektirir. Çatlamayı önlemek ve güçlü bir kaynak sağlamak için genellikle ön ısıtma ve son ısıtma gereklidir. Süre 4140 çelik başarılı bir şekilde kaynaklanabilir, daha fazla uzmanlık ve detaylara dikkat gerektirir. Bizim CNC imalat hizmetleriiçin özel kaynak protokolleri geliştirdik. 4140 çelik Kaynaklı bileşenlerin bütünlüğünü ve dayanıklılığını sağlamak için. Kaynak yaparken 4140 çelikÇatlama riskini en aza indirmek için uygun dolgu malzemelerinin kullanılması ve ısı girdisinin kontrol edilmesi çok önemlidir. Eklenmesi 4140 çelikte krom kaynaklanabilirliğini etkileyebilir ve kaynak işlemi sırasında dikkatli olunmasını gerektirir.
Seçmek sağ çelik Projeniz için gereken miktar da dahil olmak üzere çeşitli faktörlere bağlıdır. güç, sertlikişlenebilirlik, kaynaklanabilirlik ve maliyet. 1018 çelik imalat kolaylığı ve maliyet etkinliğine öncelik veren uygulamalar için mükemmel bir seçimdir. Üstün işlenebilirliği ve kaynaklanabilirliği, onu çok çeşitli genel amaçlı bileşenler için uygun hale getirir.
4140 çelik yüksek olduğunda daha iyi bir seçenektir güç ve sertlik çok önemlidir. Geliştirilmiş mekani̇k özelli̇kler'nin eklenmesi sayesinde krom ve molibdenYüksek gerilime, aşınmaya ve darbeye maruz kalan parçalar için idealdir. Bizim CNC imalat hizmetlerien uygun çözümü belirlemek için her projenin özel gereksinimlerini dikkatle değerlendiriyoruz Çelik derece. Çalışma ortamı, yük koşulları ve bileşenlerin istenen kullanım ömrü gibi faktörleri göz önünde bulunduruyoruz.
İşte karar verirken kendinize sormanız gereken bazı sorular:
Ne düzeyde güç ve sertlik uygulama ne gerektiriyor?
İşlenebilirlik ve imalat kolaylığı ne kadar önemli?
Parça kaynak işlemine tabi tutulacak mı?
Malzeme maliyetleri için bütçe nedir?
Parçanın karşılaşacağı çevresel koşullar nelerdir?
Korozyon direnci önemli bir faktör müdür?
Bileşenin beklenen kullanım ömrü nedir?
Dikkate alınması gereken sektöre özgü standartlar veya düzenlemeler var mı?
Bitmiş parçanın ağırlığı ne kadar kritik?
Bileşen istenen özelliklere ulaşmak için ısıl işlem gerektirecek mi?
1018 çelik mükemmel işlenebilirliği, kaynaklanabilirliği ve maliyet etkinliği nedeniyle çeşitli endüstrilerde çok sayıda uygulamada kullanılmaktadır. Bizim CNC imalat hizmetlerisıkça kullandığımız 1018 çelik gibi parçaların üretimi için kullanılır:
Otomotiv bileşenleri: Braketler, ara parçalar ve kritik olmayan yapısal parçalar
İnşaat malzemeleri: Sac metal imalatı parçalar, plakalar ve yapısal şekiller
Makine parçaları: Pimler, çubuklar ve düşük gerilimli bileşenler
Tüketici ürünleri: Mobilya çerçeveleri, cihaz parçaları ve dekoratif eşyalar
Tarım ekipmanları: Yük taşımayan parçalar ve yapısal elemanlar
Çok yönlülüğü 1018 çelik performans ve uygun fiyat dengesi gerektiren projeler için popüler bir seçimdir. Kolayca şekillendirilebilme ve kaynaklanabilme özelliği, karmaşık şekillerin ve yapıların oluşturulmasına olanak tanır.
4140 çelik yüksek performanslı uygulamalarda kendine yer bulur. güç, sertlikve aşınma direnci çok önemlidir. Bizim CNC imalat hizmetlerisık sık tavsiye ediyoruz 4140 çelik gibi zorlu koşullara maruz kalan bileşenler için uygundur:
Havacılık ve uzay parçaları: İniş takımı bileşenleri, yapısal elemanlar ve bağlantı elemanları
Otomotiv bileşenleri: Akslar, krank milleri, dişliler ve bağlantı çubukları
Ağır ekipman: Basınçlı dökümmadencilik makine parçaları ve inşaat ekipmanı bileşenleri
Takımlar ve kalıplar: Kalıplar, kalıplar ve yüksek aşınmalı aletler
Petrol ve gaz endüstrisi: Matkap bilezikleri, takım bağlantıları ve diğer yüksek gerilimli parçalar
Ateşli silah bileşenleri: Namlular, gövdeler ve diğer kritik parçalar
Üstün mekani̇k özelli̇kler . 4140 çelik bu zorlu uygulamalar için uygun hale getirir. Yüksek yüklere dayanma, aşınmaya direnme ve aşırı koşullar altında bütünlüğünü koruma yeteneği, kritik bileşenlerin uzun ömürlü ve güvenilir olmasını sağlar.
Uygun olanın seçilmesi Çelik Herhangi bir projenin başarısı için kalite çok önemlidir. Arasındaki seçim 1018 ve 4140 çelikveya başka herhangi bir sınıf, nihai ürünün performansını, dayanıklılığını ve maliyet etkinliğini doğrudan etkiler. Gözetim tecrübelerime göre CNC imalat hizmetleriDoğru malzeme seçiminin bir projeyi nasıl değiştirebileceğine ya da bozabileceğine ilk elden tanık oldum.
Yanlış kullanım Çelik erken arızalara, bakım maliyetlerinin artmasına ve hatta güvenlik tehlikelerine yol açabilir. Örneğin, aşağıdakileri kullanmak 1018 çelik gerektiren bir uygulamada güç . 4140 çelik stres altında bileşen kırılmasına neden olabilir. Tersine, kullanmak 4140 çelik nerede 1018 çelik yeterli olacağını düşünmek gereksiz masraflara ve potansiyel üretim zorluklarına yol açabilir. Bilinçli bir karar vermek, seçilen ürünün Çelik hem performansı hem de maliyeti optimize ederek projenin özel ihtiyaçlarıyla uyumludur.
1018 ve 4140 çelikleri arasındaki temel fark nedir?
Temel fark, bileşimlerinde ve ortaya çıkan özelliklerinde yatmaktadır. 1018 çelik düşük karbonlu bir Çelik mükemmel işlenebilirlik ve kaynaklanabilirliğe sahip ancak daha düşük güç. 4140 çelik bir alaşımlı çelik içeren krom ve molibden, daha yüksek teklif güç, sertlikve aşınma direnci.
Yüksek gerilimli uygulamalar için hangi çelik daha iyidir, 1018 mi 4140 mı?
4140 çelik üstün özellikleri nedeniyle yüksek stresli uygulamalar için daha uygundur. güç ve sertlik. Alaşım elementleri, krom ve molibdenağır yüklere dayanma ve aşınmaya direnç gösterme kabiliyetini artırır. 4140 çelik sağlam ve güvenilir malzemelere ihtiyaç duyan endüstriler için çok önemlidir.
1018 çeliğin işlenmesi 4140 çeliğe göre daha mı kolaydır?
Evet, 1018 çelik genellikle işlenmesi aşağıdakilerden daha kolaydır 4140 çelik. Düşük karbon içeriği ve önemli alaşım elementleri içermemesi, daha az takım aşınması ve daha yüksek işleme hızları sağlar. Kullanım 1018 çelik için hassas i̇şleme iyi bir seçimdir.
Hem 1018 hem de 4140 çelik kaynaklanabilir mi?
Evet, ikisi de kaynaklanabilir, ancak 1018 çelik düşük karbon içeriği nedeniyle daha iyi kaynaklanabilirlik sunar. 4140 çelik kaynak sırasında çatlamayı önlemek için ön ısıtma ve son ısıtma gerektirebilir.
Hangi çelik daha pahalıdır, 1018 mi 4140 mı?
4140 çelik genellikle aşağıdakilerden daha pahalıdır 1018 çelik daha yüksek alaşım içeriği ve üstün mekani̇k özelli̇kler.
4140 çeliği yaygın olarak hangi sektörlerde kullanılır?
4140 çelik havacılık ve uzay, otomotiv, ağır ekipman, petrol ve gaz ve kalıplama gibi endüstrilerde yaygın olarak kullanılmaktadır. güç ve dayanıklılık gereklidir.
İşte temel çıkarımların bir özeti:
1018 çelik düşük karbonlu bir Çelik mükemmel işlenebilirliği, kaynaklanabilirliği ve uygun fiyatıyla bilinir.
4140 çelik bir alaşımlı çelik daha yüksek güç, sertlikilavesi sayesinde aşınma direncine sahiptir. krom ve molibden.
1018 çelik genel imalat ve yüksek performans gerektirmeyen bileşenler için idealdir. güç.
4140 çelik yüksek gerilimli uygulamalar ve ağır aşınmaya maruz kalan parçalar için tercih edilir.
Seçmek sağ çelik sınıf, performans, dayanıklılık ve maliyeti etkileyerek proje başarısı için çok önemlidir.
Aşağıdaki gibi faktörleri göz önünde bulundurun güç, sertlikarasında seçim yaparken işlenebilirlik, kaynaklanabilirlik ve maliyet 1018 ve 4140 çelik.
Bizim CNC imalat hizmetleri uzmanlık, optimum sonuçlar için doğru malzemenin seçilmesini sağlar.
Aralarındaki farkları anlamak Çelik 1018 ve 4140 gibi kaliteler, üretimde bilinçli karar verme sürecini güçlendirir.
1018 çelik bir şekillendirilebilirlik dengesi sunar, güçve maliyet etkinliği sayesinde geniş bir uygulama yelpazesi için uygundur.
Üstün mekani̇k özelli̇kler . 4140 çelikyüksek gerilimi de dahil olmak üzere güç ve Brinell sertliğiBu da onu zorlu endüstriyel bileşenler için güvenilir bir seçim haline getirir.
Unutmayın, seçme sağ çelik sadece teknik özellikleri karşılamakla ilgili değildir; performansı optimize etmek, uzun ömürlülüğü sağlamak ve maliyet etkinliği elde etmekle ilgilidir. Bu alanda bir lider olarak CNC imalat hizmetlerimüşterilerimize bu kritik karar verme sürecinde rehberlik etmeye ve projelerinin başarılı olmasını sağlamaya kararlıyız. İster çok yönlülüğe ihtiyacınız olsun 1018 çelik veya sağlamlığı 4140 çelikuzmanlığımız ve son teknoloji üretim tesisimiz, özel ihtiyaçlarınıza göre uyarlanmış yüksek kaliteli bileşenler sunmak için burada. Projenizi görüşmek için bugün bizimle iletişime geçin ve CNC imalat hizmetleri tasarımlarınızı hassasiyet ve verimlilikle hayata geçirebilir. Biz bir dizi sunuyoruz CNC çözümleri Müşterilerimizin farklı ihtiyaçlarını karşılamak için.
Blogumuzdan CNC imalatı ile ilgili en son trendleri ve gerçekleri öğrenin.
©2024. CNC İmalat Tüm Hakları Saklıdır.