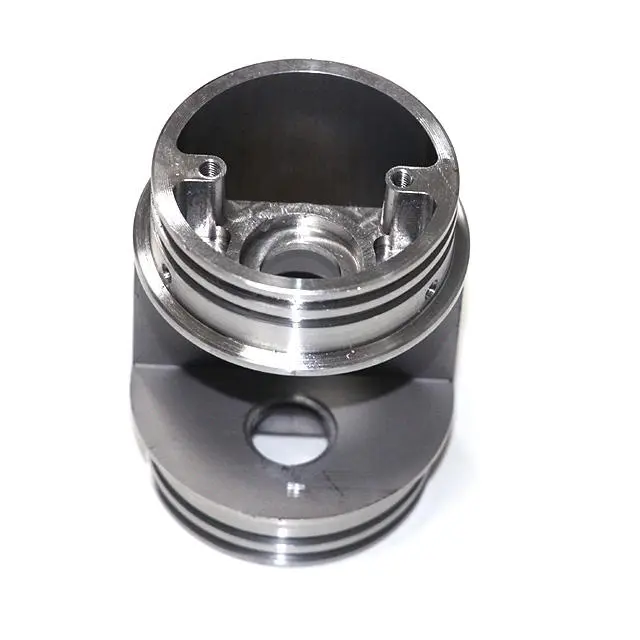
- +8615586668226
- [email protected]
- No. 30, Hongbang Endüstri Parkı, Shenzhen
Milling isn’t just cutting metal—it’s about maximizing performance. The choice between climb (down) and conventional (up) milling impacts:
With industries like havacılık ve uzay, otomotivve tibbi̇ ci̇hazlar demanding micron-level precision, selecting the optimal method is non-negotiable.
Climb milling, or down milling, involves the cutter rotating in the same direction as the workpiece feed. This method starts with maximum chip thickness, reducing friction and heat for smoother cuts.
In conventional (up) milling, the cutter rotates against the feed direction. It’s ideal for rough surfaces, castings, and manual machines.
Faktör | Climb Milling | Conventional Milling |
---|---|---|
Chip Thickness | Starts thick, tapers to zero | Starts thin, increases gradually |
Alet Ömrü | Longer (less heat) | Shorter (more friction) |
Workpiece Forces | Downward (stabilizing) | Upward (requires strong clamping) |
İçin En İyisi | Soft metals, finishing passes | Hard materials, roughing |
A manufacturer of aerospace brackets switched to climb milling on a 5-axis CNC machine, achieving:
Which method is better for titanium alloys?
Climb milling is preferred for titanium’s low thermal conductivity, minimizing heat buildup.
Can I use climb milling on a manual machine?
Avoid it—backlash risks tool pull-in. Stick to conventional milling for safety.
How does material thickness affect the choice?
Thin materials (<6 mm) benefit from climb milling’s stabilizing forces.
Is conventional milling outdated?
No—it’s indispensable for roughing cast iron or Ağır Ekipmanlar parçalar.
Ready to optimize your CNC operations? Bize ulaşın for tailored machining solutions!
Blogumuzdan CNC imalatı ile ilgili en son trendleri ve gerçekleri öğrenin.
©2024. CNC İmalat Tüm Hakları Saklıdır.