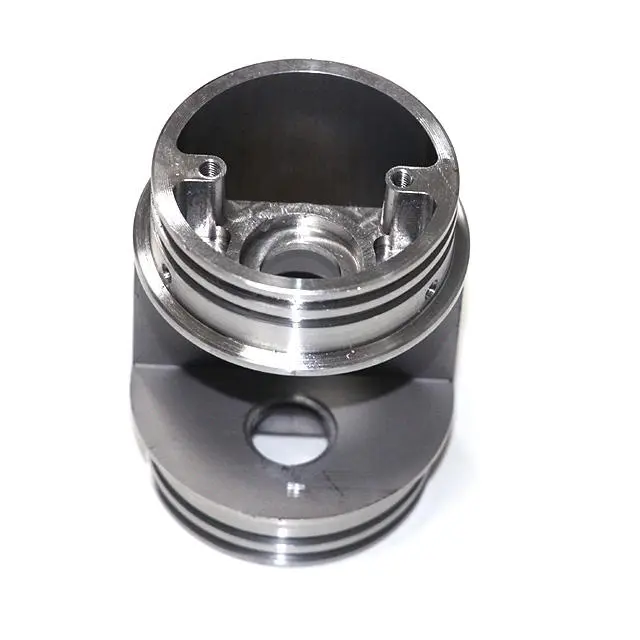
- +8615586668226
- [email protected]
- No. 30, Hongbang Endüstri Parkı, Shenzhen
A PAH bir açılı kenar iki yüzeyi, tipik olarak 45°'lik bir açıyla birleştiren açıAncak 30° veya 60° gibi başka açılar da kullanılabilir. İçinde maki̇ne mühendi̇sli̇ği̇, a PAH birden fazla amaca hizmet eder. İlk olarak, ortadan kaldırır keskin kenarlargüvenliği ve kullanımı artırır. İkincisi, bir PAH genellikle parçaların montajını kolaylaştırmak için kullanılır, örneğin bir pimi bir delikle hizalamak gibi.
Pahlar filetolara kıyasla genellikle daha kolay ve daha hızlı işlenir. A tek araç oluşturabilir PAH farklı derinlik ve açılarda. İnşaat sırasında bir özellik olarak eklenebilirler. CNC işleme önemli ölçüde artırmadan süreç işleme süresi. Bu da bir PAH birçok uygulama için uygun maliyetli bir çözümdür. Örneğin, CNC İmalat Hizmetleri'ndeki deneyimlerimize göre, bir PAH otomotiv endüstrisi veya tüketici ürünleri gibi parçaların sık sık monte ve demonte edilmesi gereken uygulamalarda sıklıkla tercih edilir. Pah basitliği ve verimliliği nedeniyle seçilmiştir. Bu eğim tasarım gereksinimlerine göre özelleştirmeye izin vererek de değişebilir. Hızlı bir şekilde ihtiyacım olduğunda birçok kez kullandım, eğimli kenar montaj amaçları için.
A fileto bir yuvarlatılmış köşe veya kenararasında geçiş yapan içbükey ya da dışbükey iki yüzey. Farklı olarak PAHki bu bir açılı kenar, a fileto pürüzsüz bir görünüm sağlar, kavisli kenar. Mühendislik tasarımında, filetolar stres yoğunluğunu azaltmak için çok önemlidir. A keskin köşe yük altında potansiyel arızaya yol açan bir stres yükseltici olarak hareket edebilir. A fileto yardımcı olur dağıtmak daha geniş bir alanda stres yaratır, böylece yük taşıma kapasitesi bir parçanın.
Fileto tasarım sırasında daha dikkatli bir değerlendirme gerektirir. üretim süreci. Oluşturma fileto genellikle belirli bir kesici alet ile istenen yarıçap. Fileto ekleyebilir işleme süresi ve maliyet, özellikle de özel bir alet gerekiyorsa. Buna rağmen, bir alet kullanmanın faydaları fileto yapısal bütünlük açısından çoğu zaman ilave karmaşıklıktan daha ağır basmaktadır. Fileto dayanıklılığın kritik olduğu havacılık ve uzay bileşenlerinde yaygın olarak kullanılır. Örneğin, yüksek gerilime maruz kalan parçalarda fileto çatlamayı önlemek için çok önemlidir, havacılık endüstrisi için bir proje hatırlıyorum. fileto kenarları yüksek stres altında yapısal bütünlüğü korumak için.
Birincil fileto ve pah arasındaki fark geometrilerinde ve stres dağılımını nasıl etkilediklerinde yatmaktadır. A fileto sağlar yuvarlatılmış köşeiki yüzey arasında yumuşak geçişler yaparak stresi azaltmak konsantrasyon. Bu da filetolar Yüksek yüklere veya döngüsel strese maruz kalan parçalar için idealdir. Buna karşılık, bir PAH bir açılı kenar. Bir yandan da PAH azaltılmasına yardımcı olabilir keskin köşelerdeğil dağıtmak kadar etkili bir şekilde stres fileto.
Bir diğer önemli fark ise üretim yöntemidir. Diğer fileto arasındaki fark ve bir PAH farklı nedenlerle kullanılıyor olmalarıdır. Fileto genellikle aşağıdakiler için kullanılır stresi azaltmak konsantrasyonları ve chamfers genellikle çapak almak veya bir parçayı diğerine yerleştirmeyi kolaylaştırmak için kullanılır. Pahlar standart işleme takımlarıyla üretilmesi genellikle daha kolaydır, bu da onları birçok uygulama için daha uygun maliyetli bir seçenek haline getirir. Ancak, bir fileto Tasarım, malzemenin yorulmasını ve arızalanmasını önlemek için gerilim yoğunlaşmasını en aza indirmeyi gerektirdiğinde gerekli olabilir. Örneğin, ağır ekipman için bileşenler tasarlarken, her zaman aşağıdakilerin kullanımını vurgularım filetolar Üstün gerilim dağılımı özellikleri için.
Pahlar çeşitli senaryolarda oldukça etkilidir. Yaygın kullanım alanlarından biri keskin kenarlarBu sayede parçaların taşınması daha güvenli hale gelir ve montaj veya kullanım sırasında yaralanma riski azalır. Pahlar aynı zamanda bir parçanın estetiğini iyileştirerek ona daha bitmiş bir görünüm kazandırabilir. Bir diğer önemli uygulama da montaj sırasında parçaların yönlendirilmesi ve hizalanmasıdır. Örneğin, bir yivli kenar bir milin yatak veya deliğe daha kolay kaymasına yardımcı olabilir. Bu sadece montaj süresini kısaltmakla kalmaz, aynı zamanda ilgili parçaların hasar görmesini de önler.
Montaj avantajlarına ek olarak, chamfers oluşturmak için kullanılabilir. açı kaynak hazırlıkları için veya dağıtmak yükleri bir bağlantı boyunca daha eşit bir şekilde taşır. Sac metal imalatında, bir PAH malzemenin bükülürken çatlamasını önleyebilir. Sac metal imalatı ayrıca kullanır chamfers parça dayanıklılığını artırmak için. Örneğin, parçaların aşınma ve yıpranmaya maruz kaldığı endüstriyel ekipmanlarda PAH kenar ufalanması olasılığını azaltarak parçanın ömrünü uzatabilir. Bunun özellikle hassasiyet ve dayanıklılığın kritik önem taşıdığı karmaşık robotik parçaların üretiminde geçerli olduğunu gördüm, örneğin 60° PAH kaynak işlemine yardımcı olabilirken, 45° PAH genellikle estetik amaçlar için kullanılır.
Fileto özellikle gerilim yoğunlaşması ile uğraşırken ve bir parçanın genel mukavemetini artırırken faydalıdır. A fileto's yuvarlatılmış kenar stresi daha eşit bir şekilde dağıtmaya yardımcı olur, bu da onu yüksek yüklere veya döngüsel strese maruz kalan bileşenler için ideal hale getirir. Örneğin, parçaların aşırı kuvvetlere ve titreşimlere dayanması gereken havacılık ve uzay uygulamalarında, filetolar yapısal bütünlüğün sağlanması için gereklidir. A fileto bir parçanın farklı bölümleri arasında yumuşak bir geçiş oluşturmak için de kullanılabilir ve stres yükselmelerine yol açabilecek ani değişikliklerin olasılığını azaltır.
Mekanik faydalara ek olarak, filetolar belirli uygulamalarda sıvıların veya malzemelerin akışını iyileştirebilir. Örneğin, kalıp tasarımında bir fileto erimiş malzemenin sorunsuz bir şekilde akmasını sağlayarak kusur riskini azaltmaya yardımcı olabilir. Fileto ergonomi ve estetiği geliştirmek, daha rahat ve görsel olarak çekici bir tasarım sağlamak için tüketici ürünlerinde de kullanılmaktadır. Benim deneyimlerime göre filetolar tıbbi cihaz tasarımlarında sadece güvenliği artırmakla kalmaz, aynı zamanda cihazları daha kullanıcı dostu hale getirir.
CNC işleme kullanılıp kullanılmayacağının belirlenmesinde önemli bir rol oynar. fileto ya da PAH. Pahlar standart kesme takımları kullanılarak işlenmesi genellikle daha kolaydır, bu da onları birçok durumda daha uygun maliyetli bir seçenek haline getirir. A PAH genellikle tek bir geçişle oluşturulabilir. kesici aletgenel olarak azaltılması işleme süresi. Bu, verimliliğin çok önemli olduğu yüksek hacimli üretimde özellikle avantajlıdır.
FiletoÖte yandan, istenen sonuca ulaşmak için özel aletler veya birden fazla geçiş gerekebilir. yarıçaphem karmaşıklığını hem de maliyetini artırmaktadır. üretim süreci. Bununla birlikte, modern CNC işleme gelişmiş yeteneklere sahip merkezler karmaşık işlerin üstesinden gelebilir fileto yüksek hassasiyete sahip geometriler. Bu, tasarımda daha fazla esneklik sağlar ve aşağıdakilerin kullanılmasına olanak tanır filetolar performans nedenleriyle en çok ihtiyaç duyulan yerlerde. Tesisimizde, aşağıdaki unsurları kullanmaya yönelik bir eğilim gördük filetolar gelişmeler sayesinde kritik bileşenlerde CNC işleme.
Gerilme konsantrasyonu mekanik tasarımda kritik bir faktördür ve hem fileto ve PAH yönetiminde önemli roller oynamaktadır. A keskin köşe veya kenar yük altında erken arızaya yol açabilecek yüksek stres yoğunlaşma noktası oluşturur. A fileto stresi daha geniş bir alana dağıtan kademeli bir geçiş sağlayarak bunu hafifletmeye yardımcı olur ve böylece tepe stresini azaltır. İşte bu yüzden filetolar genellikle dayanıklılık ve güvenilirliğin çok önemli olduğu kritik uygulamalarda kullanılır.
Pahlar'den daha az etkili olsa da filetolar stres yoğunluğunu azaltmada hâlâ bazı faydalar sunmaktadır. A PAH kaldırır keskin kenarBu da çatlak başlama olasılığını azaltabilir. Bununla birlikte açılı kenar bir PAH kadar düzgün bir şekilde dağıtmaz. yuvarlatılmış kenar bir fileto. Bu nedenle, yüksek stresli uygulamalarda fileto genellikle tercih edilir. Pratikte gözlemlediğim kadarıyla filetolar olanlara kıyasla yoğun kullanım altında daha uzun ömürlü olma eğilimindedir. chamfers. Ayrıca şunu da bilmelisiniz ki PAH her zaman aynı düzeyde stres azaltma sağlamaz.
Arasında seçim yapmak fileto ve bir PAH özel uygulama, gerilim gereksinimleri, üretim kabiliyetleri ve maliyet hususları dahil olmak üzere çeşitli faktörlere bağlıdır. Birincil endişe ortadan kaldırmaksa keskin kenarlar ve montajı kolaylaştırmak, bir PAH yeterli olabilir. Bununla birlikte, tasarım yüksek stres veya döngüsel yükleme içeriyorsa, bir fileto muhtemelen daha iyi bir seçimdir. Fileto veya PAH farklı nedenlerden dolayı iyi seçimlerdir. Ayrıca, aşağıdakilere karar verirken PAH veya fileto tasarımında, parçanın nasıl kullanılacağını düşünmelisiniz.
Üretimle ilgili sonuçları da göz önünde bulundurmak önemlidir. Pahlar genellikle daha kolay ve daha hızlı üretilir, bu da maliyete duyarlı projelerde avantajlı olabilir. Fileto daha karmaşık işleme gerektirebilir, ancak yatırım, sundukları gelişmiş performans ve dayanıklılık ile haklı çıkarılabilir. Tasarım perspektifinden bakıldığında, ödünleşimleri değerlendirmek ve projenin genel gereksinimlerini en iyi karşılayan özelliği seçmek çok önemlidir. Örneğin, aşağıdakileri içeren projelerde hızlı prototipleme, chamfers basitliği ve hızı nedeniyle sıklıkla kullanılır.
Evet, her ikisini de kullanmak mümkün ve bazen avantajlıdır fileto ve PAH tek bir tasarımda. Bu özelliklerin birleştirilmesi, tasarımcıların bir parçanın farklı alanlarında her birinin avantajlarından yararlanmasına olanak tanır. Örneğin, bir PAH montajı kolaylaştırmak için dış kenarlarda kullanılabilirken filetolar stres konsantrasyonunu azaltmak için iç köşelere uygulanır. Bu hibrit yaklaşım, parçanın hem işlevselliğini hem de üretilebilirliğini optimize edebilir.
Bir kombinasyon kullanarak fileto ve PAH maliyet ve performans arasında bir denge de sağlayabilir. Stratejik olarak uygulayarak chamfers en etkili oldukları yerlerde ve filetolar Kritik alanlar için tasarımcılar hem sağlam hem de ekonomik bir tasarım elde edebilirler. Bu yaklaşım, dikkatli bir planlama ve her bir özelliğin güçlü yönlerinin ve sınırlamalarının iyi anlaşılmasını gerektirir. Deneyimlerime göre, bu karma yöntem genellikle sıkı performans kriterlerini karşılayan ve aynı zamanda uygun maliyetli yenilikçi çözümlere yol açmaktadır.
Maliyet, her üretim projesinde önemli bir husustur ve aşağıdakiler arasında seçim yapmak gerekir fileto ve PAH kayda değer sonuçlar doğurabilir. Pahlar daha basit geometrileri ve standart kesici takımlarla uyumlulukları nedeniyle üretilmeleri genellikle daha ucuzdur. Bu da onları maliyetin öncelikli olduğu uygulamalar için cazip bir seçenek haline getirmektedir. Ek olarak, daha hızlı işleme süresi ile ilişkili chamfers üretim maliyetlerini daha da düşürebilir.
FiletoÖte yandan, özel aletlere ihtiyaç duyulması ve potansiyel olarak daha uzun sürmesi nedeniyle daha maliyetli olabilir. işleme süresi. Bununla birlikte, ilave masraf, geliştirilmiş performans ve dayanıklılık ile haklı çıkarılabilir. filetolar sağlayın. Güvenilirlik ve uzun ömürlülüğün kritik önem taşıdığı uygulamalarda filetolar arıza olasılığını ve değiştirme ihtiyacını azaltarak uzun vadeli maliyet tasarrufu sağlayabilir. Nihayetinde karar, hem ilk üretim maliyetlerini hem de potansiyel uzun vadeli etkileri göz önünde bulunduran kapsamlı bir maliyet-fayda analizine dayanmalıdır. Örneğin, aşağıdakileri kullanmak filetolar içinde 5 eksenli CNC işleme başlangıç maliyetlerini artırabilir ancak parça performansını önemli ölçüde artırabilir.
Kullanmanın birincil avantajı fileto Yüksek gerilimli uygulamalarda, gerilimi daha geniş bir alana dağıtma, gerilme konsantrasyonunu azaltma ve parçanın dayanıklılığını artırma yeteneğidir. Bu yuvarlatılmış kenar bir fileto yüzeyler arasında yumuşak bir geçiş sağlayarak yük altında arıza riskini en aza indirir.
A PAH oluşturarak montajı kolaylaştırır. açılı kenar parçaları yönlendirmeye ve hizalamaya yardımcı olur. Bu, bir parçanın diğerine yerleştirilmesini kolaylaştırır ve montaj için gereken kuvveti azaltır. Pahlar montaj kolaylığını artırmak için miller, pimler ve delikler üzerinde yaygın olarak kullanılır.
Pahlar üretimi genellikle aşağıdakilerden daha ucuzdur filetolar Çünkü standart kesici takımlarla oluşturulabilecek daha basit bir geometriye sahiptirler. Bu, özel takım ihtiyacını azaltır ve aşağıdakileri en aza indirir işleme süresiBu da daha düşük üretim maliyetleri ile sonuçlanır.
Evet, filetolar pürüzsüz bir yapı sağlayarak kalıp tasarımında malzeme akışını iyileştirebilir, yuvarlatılmış kenar türbülansı azaltır ve eşit dolum sağlar. Bu, kusurları en aza indirmeye ve kalıplanmış parçanın kalitesini artırmaya yardımcı olabilir.
arasında seçim yaparken fileto ve bir PAHÖzel uygulamayı, gerilim gereksinimlerini, üretim kabiliyetlerini ve maliyet etkilerini göz önünde bulundurun. Öncelikli hedef ortadan kaldırmaksa keskin kenarlar ve montajı kolaylaştırmak, bir PAH yeterli olabilir. Bununla birlikte, tasarım yüksek stres veya döngüsel yükleme içeriyorsa, bir fileto muhtemelen daha iyi bir seçimdir.
Evet, her ikisini de kullanmak mümkündür ve genellikle faydalıdır fileto ve PAH aynı parça üzerinde. Bu, tasarımcıların parçanın farklı alanlarında her bir özelliğin avantajlarından yararlanmasına olanak tanıyarak hem işlevselliği hem de üretilebilirliği optimize eder.
Pahlar vardır açılı kenarlar tipik olarak kaldırmak için kullanılır keskin kenarlar ve montajı kolaylaştırır.
Fileto vardır yuvarlatılmış kenarlar bu yardım stresi azaltmak konsantrasyonunu ve parça dayanıklılığını artırır.
Pahlar ile karşılaştırıldığında genellikle daha kolay ve daha ucuzdur. filetolar.
Fileto üstün gerilme dağılımı özellikleri nedeniyle yüksek gerilimli uygulamalarda tercih edilir.
Arasında seçim yapmak fileto ve bir PAH özel uygulamaya, gerilim gereksinimlerine, üretim kabiliyetlerine ve maliyet hususlarına bağlıdır.
Birleştirme fileto ve PAH tek bir tasarımda maliyet ve performans arasında bir denge sağlayabilir.
Gelişmeler CNC işleme teknoloji, yeni teknolojilerin filetolar karmaşık tasarımlara dönüştürür.
Doğru kullanım fileto ve PAH üretilen parçaların hem güvenliğini hem de işlevselliğini artırabilir.
Yüzey bitirme ile parçaların kalitesini ve görünümünü daha da iyileştirebilir. filetolar veya chamfers.
Nüansları anlamak fileto vs pah tasarım ve üretimde bilinçli kararlar almak için çok önemlidir.
Dikkatli değerlendirme fileto ve PAH uzun vadeli maliyet tasarrufu ve gelişmiş ürün performansı sağlayabilir.
Pahlar genellikle kalıp döküm parçaların kalıplardan çıkarılmasını kolaylaştırmak için.
Doğru kullanım fileto ve PAH gibi sektörlerdeki projelerin başarısını önemli ölçüde etkileyebilir. havacılık ve uzay ve otomotiv.
CNC İmalat Hizmetleri her iki alanda da uzmanlık sunar fileto ve PAH uygulamaları, çeşitli endüstriler için optimum sonuçlar sağlar.
Unutmayın, bir PAH bir açılı kenarOysa a fileto bir yuvarlatılmış kenar.
Doğru özelliği seçmek, ister bir fileto ya da PAHprojenizin başarısı için çok önemlidir. CNC İmalat Hizmetleri olarak bu nüansları anlıyoruz ve imalat ihtiyaçlarınız için en iyi çözümleri sunmaya kararlıyız. Tasarımlarınızı optimize etmenize ve üstün sonuçlar elde etmenize nasıl yardımcı olabileceğimizi öğrenmek için bugün bize ulaşın. Havacılık, otomotiv ve tıbbi cihazlar dahil olmak üzere çeşitli sektörlerdeki uzmanlığımız, özel gereksinimlerinizi hassasiyet ve verimlilikle karşılayabilmemizi sağlar. Projelerinizi en yüksek kalite ve performans standartlarıyla hayata geçirmenize yardımcı olalım.
Blogumuzdan CNC imalatı ile ilgili en son trendleri ve gerçekleri öğrenin.
©2024. CNC İmalat Tüm Hakları Saklıdır.