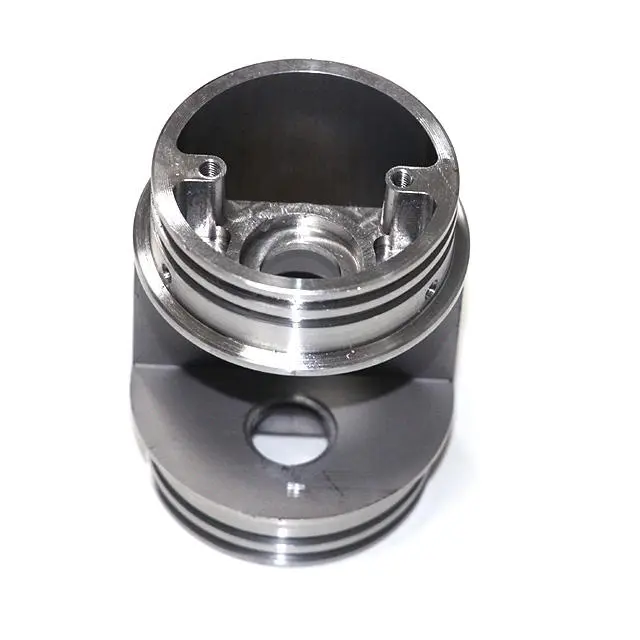
- +8615586668226
- [email protected]
- No. 30, Hongbang Endüstri Parkı, Shenzhen
Wall thickness isn’t just a number—it’s the backbone of part performance. Whether you’re crafting lightweight drones or heavy-duty industrial gear, this parameter impacts structural integrity, material efficiency, and machining costs.
Wall thickness measures the distance between two parallel surfaces of a part. Think of it as the “skeleton” that holds your design together. Too thin, and parts risk warping; too thick, and you’ll waste material and inflate costs.
Key Factors Influencing Wall Thickness:
For instance, aerospace brackets often use 0.5–1.5 mm aluminum walls to balance strength and weight, while medical housings might require 1–3 mm stainless steel for sterilization durability.
Thin walls save weight but challenge stability. Here’s how thickness impacts outcomes:
Issue | Thin Walls | Thick Walls |
---|---|---|
Yapısal Bütünlük | Risk of deformation | Over-engineered, heavy |
Machining Cost | Higher precision needed | More material consumed |
Thermal Stability | Warps under heat | Resists distortion |
“A 0.1 mm deviation in wall thickness can reduce a turbine blade’s lifespan by 20%.” – Aerospace Manufacturing Journal
Not all materials handle thin walls equally.
Örnek Olay İncelemesi: A robotics firm reduced part weight by 30% using 0.8 mm carbon fiber walls (Robotik) while maintaining load capacity.
Use this cheat sheet for design decisions:
Malzeme | Min Thickness | Max Thickness |
---|---|---|
Alüminyum | 0.5 mm | 10 mm |
Paslanmaz Çelik | 1 mm | 15 mm |
ABS Plastik | 0.3 mm | 8 mm |
Titanyum | 1 mm | 20 mm |
Profesyonel İpucu: For high-stress applications like Havacılık ve Uzay, pair titanium’s 20 mm max thickness with 5 Eksenli CNC İşleme for complex geometries.
Thinner walls = trickier machining. Here’s how to adapt:
A defense contractor slashed machining time by 25% using Hassas İşleme for 0.6 mm brass components.
Precision tools prevent costly errors:
Did You Know? X-ray CT scans are used in Tıbbi Cihazlar to verify 0.4 mm titanium walls without disassembly.
8 Rules for Success:
For prototypes, Hızlı Prototipleme lets you test 0.5 mm walls cost-effectively.
Stay compliant, stay competitive:
Pitfalls to Dodge:
How thin can aluminum walls be?
0.5 mm is achievable with CNC Freze, but design supports to prevent bending.
What’s the minimum wall for 3D printing?
0.4 mm nozzle? Aim for 0.8 mm (two extrusion lines).
Does wall thickness affect cost?
Yes! Thick walls use 30% more material on average.
How to measure internal walls?
Ultrasonic gauges or CT scans for non-destructive testing.
Ready to Optimize Your Next Project? Bize Ulaşın for CNC solutions tailored to your industry.
Blogumuzdan CNC imalatı ile ilgili en son trendleri ve gerçekleri öğrenin.
©2024. CNC İmalat Tüm Hakları Saklıdır.