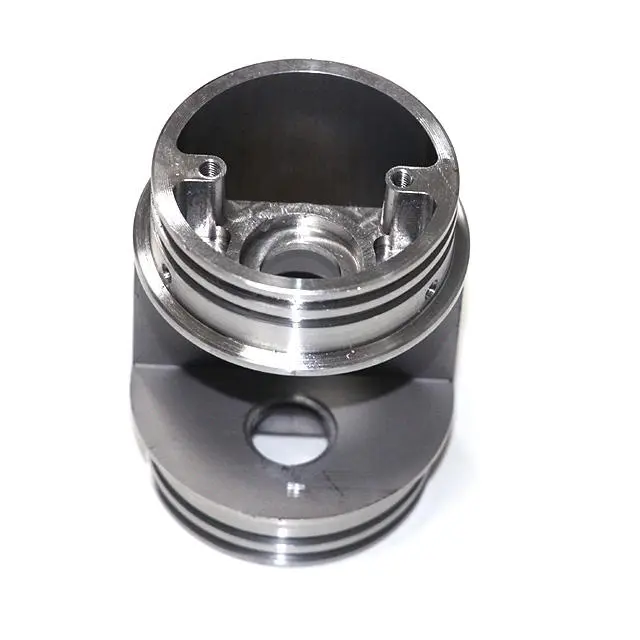
爬行铣削与传统铣削:选择最佳数控加工方法
目录
导言
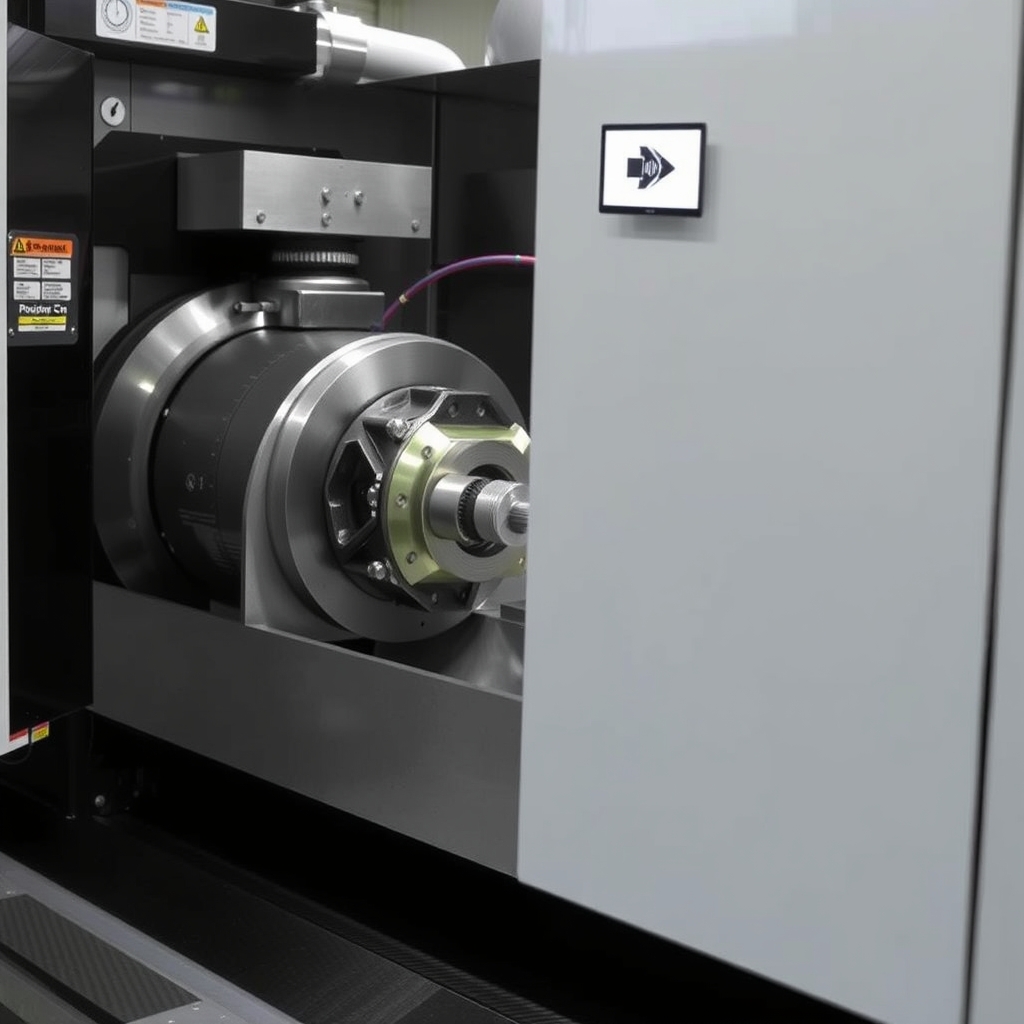
Why Milling Direction Matters in Modern Manufacturing
Milling isn’t just cutting metal—it’s about maximizing performance. The choice between climb (down) and conventional (up) milling impacts:
- Surface finish quality
- Tool longevity
- Machining speed
- Workpiece stability
With industries like 航天, 车载和 医疗器械 demanding micron-level precision, selecting the optimal method is non-negotiable.
Understanding Climb Milling: Precision Meets Efficiency
What is Climb Milling?
Climb milling, or down milling, involves the cutter rotating in the same direction as the workpiece feed. This method starts with maximum chip thickness, reducing friction and heat for smoother cuts.
Key Advantages of Climb Milling
- Superior surface finishes: Ideal for visible components in 消费品.
- 50% longer tool life: Reduced heat and friction.
- Faster feed rates: Boosts productivity in high-volume projects like 汽车 零件
- Efficient chip evacuation: Prevents recutting.
Limitations to Watch For
- Requires 现代数控机床 with backlash control.
- Unsuitable for rough or uneven surfaces.
- Risk of tool pull-in on older equipment.
Conventional Milling: Stability for Tough Materials
How Conventional Milling Works
In conventional (up) milling, the cutter rotates against the feed direction. It’s ideal for rough surfaces, castings, and manual machines.
Why Choose Conventional Milling?
- Handles hardened materials: Perfect for 工业设备 组件
- Safer for manual machines: No tool pull-in risk.
- Better for deep cuts: Up to 1x cutter diameter.
Drawbacks to Consider
- Poorer surface finish due to chip recutting.
- Higher tool wear from friction.
Climb vs. Conventional Milling: Head-to-Head Comparison
系数 | Climb Milling | Conventional Milling |
---|---|---|
Chip Thickness | Starts thick, tapers to zero | Starts thin, increases gradually |
工具寿命 | Longer (less heat) | Shorter (more friction) |
Workpiece Forces | Downward (stabilizing) | Upward (requires strong clamping) |
最适合 | Soft metals, finishing passes | Hard materials, roughing |
7 Factors to Determine Your Milling Strategy
- 材料硬度: Soft metals (e.g., aluminum) favor climb; hardened steels need conventional.
- 机器类型: Modern CNC vs. manual (数控解决方案).
- Surface Finish Needs: Climb for 医疗设备; conventional for rough castings.
- 切割深度: Shallow (climb) vs. deep (conventional).
- Chip Evacuation: Critical for heat-sensitive materials.
- 刀具偏差: Climb requires rigid setups.
- 生产速度: Climb enables faster cycles.
Case Study: Aerospace Component Machining
A manufacturer of aerospace brackets switched to climb milling on a 5-axis CNC machine, achieving:
- 20% faster cycle times.
- Ra 0.4 µm surface finish (vs. Ra 1.6 µm with conventional).
- 30% reduction in tool replacement costs.
FAQs: Your Milling Questions Answered
Which method is better for titanium alloys?
Climb milling is preferred for titanium’s low thermal conductivity, minimizing heat buildup.
Can I use climb milling on a manual machine?
Avoid it—backlash risks tool pull-in. Stick to conventional milling for safety.
How does material thickness affect the choice?
Thin materials (<6 mm) benefit from climb milling’s stabilizing forces.
Is conventional milling outdated?
No—it’s indispensable for roughing cast iron or 重型设备 零件
主要收获
- Climb milling excels in precision, speed, and finish quality.
- Conventional milling offers control for hard materials and older machines.
- Match the method to your 材料, 机械和 production goals.
Ready to optimize your CNC operations? 联系我们 for tailored machining solutions!
评论
出色的产品案例
标签
相关博客
从我们的博客中获取有关 CNC 加工的最新趋势和事实。