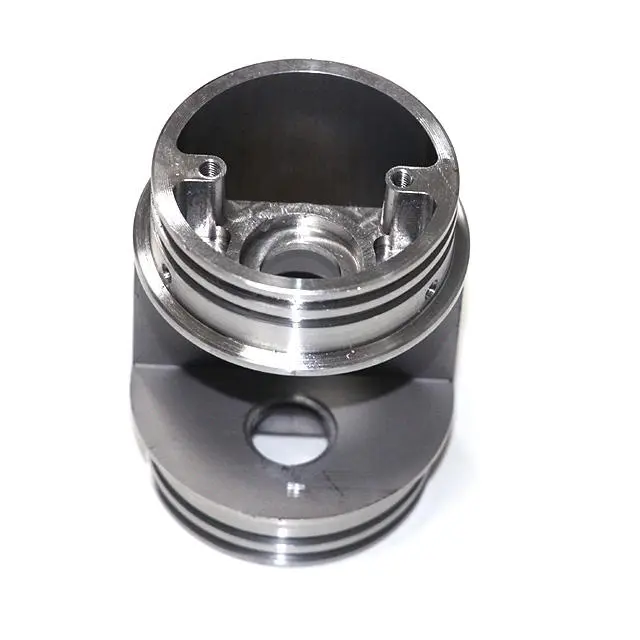
优化数控速度和进给,实现精密加工
目录
导言
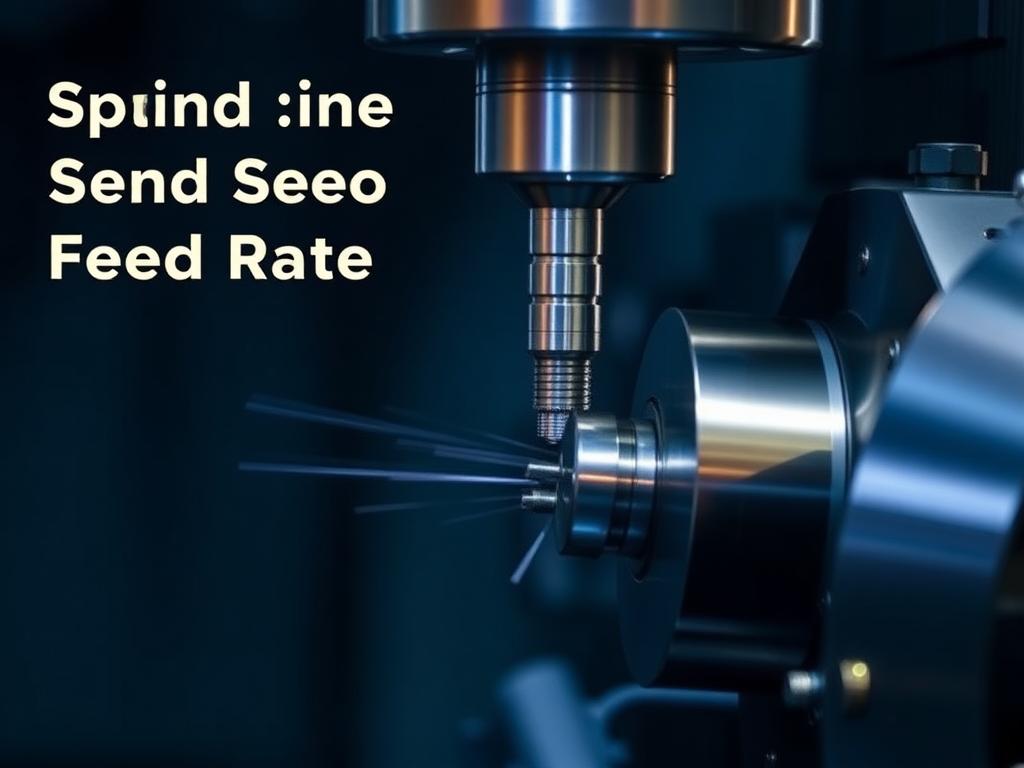
What is Feed Rate in CNC Machining?
进料速度 in CNC machining refers to the speed at which the cutting tool moves along the workpiece. More specifically, it’s the rate at which the tool advances into the material during each revolution of the spindle. As a representative of a 数控加工服务 company, I’ve seen firsthand how crucial this parameter is. For instance, a higher 进料速度 can significantly reduce machining time, but if not properly managed, it can lead to tool breakage or a poor 表面处理.
在我们的 机械 shop, we typically measure 喂食 in units like inches per minute (IPM) or millimeters per minute (mm/min). The optimal 进料速度 取决于以下因素 material you’re cutting的类型 刀具 used, and the desired 表面处理. For example, when working with soft materials like aluminum, we can often use a higher 进料速度 compared to harder materials like steel. Our experience with 数控加工服务 has shown that a well-calibrated 进料速度 is essential for maximizing 加工效率 while maintaining high-quality results. Our experience has shown that finding the optimal 喂食 和 速度 settings for each job can significantly reduce cycle times and improve part quality.
How Does Spindle Speed Influence CNC Machining?
Spindle speed in CNC machining refers to the rotational speed of the 机器的 spindle, which holds the cutting tool. It is typically measured in revolutions per minute (RPM). The 主轴转速 is a critical factor that affects the cutting process in several ways. For instance, in our experience with 数控解决方案, we have found that higher spindle speeds generally result in a better 表面处理, especially when working with non-ferrous materials like aluminum. This is because the increased speed helps to reduce the formation of built-up edge on the 刀具.
However, it is important to note that 主轴转速 must be carefully balanced with the 进料速度. As a general rule, higher spindle speeds require a corresponding increase in 进料速度 to maintain proper chip load. For example, when working with hard materials like stainless steel, we often use lower spindle speeds to prevent excessive heat generation and 工具 wear. Our 数控加工服务 experience has shown that selecting the appropriate 主轴转速 for each 机加工 operation is crucial for achieving optimal results.
What is the Relationship Between Cutting Speed and Feed Rate?
切割速度 和 进料速度 are two of the most important parameters in CNC machining. 切割速度 refers to the speed at which the cutting edge of the 工具 moves past the cutting material, while 进料速度 的速度。 刀具 moves along the workpiece. These two parameters are closely related and must be carefully balanced to achieve optimal 机加工 results. Our experience in providing 机械加工服务 has taught us that the correct combination of cutting speed and feed rate can significantly affect 工具寿命, 表面处理, and overall 加工效率.
For example, a higher 切割速度 generally allows for faster material removal but can also lead to increased 工具 wear and heat generation. On the other hand, a higher 进料速度 can reduce machining time but may result in a rougher 表面处理 甚至 工具 breakage if not properly managed. In our 数控加工服务 shop, we often use specialized software to calculate the optimal cutting speed and feed rate for each job, taking into account factors like the material being machined, the type of 刀具 used, and the desired 表面处理.
How to Optimize Feed Rate and Spindle Speed for Different Materials?
优化 进料速度 和 主轴转速 is crucial for achieving efficient and high-quality results in 数控加工工艺. The optimal settings vary depending on the 材料 being machined. For instance, softer materials like aluminum can typically be machined at higher spindle speeds 和 喂料速率 compared to harder materials like steel.
在我们的 数控加工服务 company, we maintain a comprehensive database of recommended speeds 和 feeds for various materials. Here’s a simplified example in a table:
材料 | Spindle Speed (RPM) | Feed Rate (IPM) |
铝 6061 | 4000-6000 | 20-40 |
Stainless Steel 304 | 1500-2500 | 5-15 |
低碳钢 | 2000-3000 | 10-25 |
黄铜 | 3000-4500 | 15-35 |
These values are just starting points, and the optimal settings for a specific application may vary depending on factors like the specific alloy, 工具 geometry, and desired 表面处理.例如,当 机加工 a thin-walled aluminum part, we might use a lower 进料速度 to prevent distortion, even though the material allows for higher speeds. This is one of the many insights that come from the many years we have been in business as a 数控加工服务 company.
What Role Does Chip Load Play in Determining Optimal Feed?
Chip load又称 feed per tooth, is a critical factor in determining the optimal 进料速度 对于 数控加工. It refers to the thickness of the 材料 removed by each cutting edge of the 工具 during one revolution of the 转轴. Maintaining the correct chip load is essential for achieving good 工具寿命, 表面处理, and overall 加工效率.
在我们的 数控加工服务 shop, we often use the following formula to calculate the 进料速度 based on the desired chip load:
Feed Rate (IPM) = Chip Load x Number of Teeth x Spindle Speed (RPM)
For example, if we’re using a 4-flute end mill to 机械 aluminum with a recommended chip load of 0.002 inches per tooth and a 主轴转速 of 5000 RPM, the calculated 进料速度 would be:
Feed Rate = 0.002 in/tooth x 4 teeth x 5000 RPM = 40 IPM
It’s important to note that the optimal chip load varies depending on the 材料 being machined and the type of 刀具 used. For instance, roughing operations typically require a higher chip load compared to finishing operations. In our experience, maintaining the correct chip load is crucial for preventing 工具 rubbing, which can lead to poor 表面处理 and reduced 工具寿命.
How Can I Improve Tool Life Through Optimized Speed and Feed?
优化 速度和进料 is not only crucial for achieving high-quality 机加工 results but also for extending 工具寿命. As a leading provider of 数控加工服务, we’ve found that using the correct 速度和进料 settings can significantly reduce 工具 wear and prevent premature 工具 failure. One of the key factors in improving 工具寿命 is to avoid excessive heat generation during the 切割过程. Higher speeds 和 feeds can generate more heat, which can accelerate 工具 穿。
By optimizing the 切割速度 和 进料速度, we can minimize heat buildup and distribute wear more evenly across the cutting edges of the 工具. For example, using a lower cutting speed and a higher 进料速度 can often reduce heat while maintaining a reasonable material removal rate. Additionally, using coolant or lubricant can help dissipate heat and reduce friction, further extending 工具寿命.
What are the Best Machining Techniques for High-Speed CNC Machining?
High-speed machining (HSM) is a technique that involves using higher spindle speeds 和 喂料速率 to achieve faster material removal rates and improve 加工效率. In our 数控加工服务 company, we often employ HSM techniques for applications that require high productivity, such as 快速成型 或 按需制造. One of the key aspects of HSM is the use of specialized 刀具 designed to withstand the higher speeds 和 feeds involved. These 工具 often feature advanced coatings and geometries that help to reduce heat and wear.
Another important technique in HSM is the use of trochoidal milling, which involves programming the 工具 to move in a series of circular or spiral motions rather than straight lines. This technique helps to maintain a constant chip load 并减少 工具 engagement, which can significantly improve 工具寿命 和 表面处理 at higher speeds.
How Does Depth of Cut Affect Feed Rate and Cutting Speed?
"(《世界人权宣言》) 切割深度 is another critical parameter that affects 进料速度 和 切割速度 于 数控加工. It refers to the amount of 材料 removed in a single pass of the 刀具. In our experience with 数控加工服务, we’ve found that the 切割深度 has a significant impact on the optimal 速度和进料 settings.
Generally, a deeper 切割深度 requires a lower 进料速度 to maintain proper chip load and prevent 工具 breakage. For example, when performing roughing operations, we typically use a larger 切割深度 and a lower 进料速度 去掉 材料 quickly. Conversely, for finishing operations, we use a smaller 切割深度 and a higher 进料速度 to achieve a better 表面处理.
Here’s a table illustrating how 切割深度 can affect 进料速度 for a typical milling operation on mild steel:
Depth of Cut (in) | Feed Rate (IPM) |
0.100 | 20 |
0.050 | 30 |
0.025 | 40 |
It’s important to note that the optimal 切割深度 also depends on the rigidity of the 机械 and the workpiece setup. A less rigid setup may require a smaller 切割深度 to prevent chatter and vibration, which can negatively affect 工具寿命 和 表面处理.
What are Common Mistakes to Avoid When Adjusting Speed and Feed?
Adjusting 速度和进料 是 数控加工, and even experienced machinists can make mistakes that can lead to poor results or 工具 damage. In our 数控加工服务 company, we’ve identified several common mistakes that machinists should avoid when adjusting 速度和进料:
Ignoring Manufacturer Recommendations: One of the most common mistakes is ignoring the 速度和进料 recommendations provided by the 刀具 manufacturer. These recommendations are based on extensive testing and are usually the best starting point for optimizing 机加工 参数
Using Excessive Speed: Another common mistake is using a 主轴转速 that is too high for the 材料 或 工具 being used. While higher speeds can improve productivity, excessive speed can lead to increased heat, 工具 wear, and poor 表面处理.
Using Insufficient Feed:使用 进料速度 that is too low can be just as detrimental as using one that is too high. A low feed rate can cause the 工具 to rub against the workpiece, generating excessive heat and leading to 工具 failure.
How to Achieve the Best Surface Finish by Balancing Speed and Feed?
Achieving a good 表面处理 is often a top priority in 数控加工, especially for parts that require tight tolerances or have aesthetic requirements. As a provider of 数控加工服务, we understand the importance of achieving the desired 表面处理 for our customers. The 表面处理 is primarily influenced by the 进料速度, 主轴转速, and the condition of the 刀具.
Generally, a higher 进料速度 results in a rougher 表面处理, while a lower 进料速度 produces a smoother finish. However, using a 进料速度 that is too low can cause the 工具 to rub against the workpiece, leading to a poor 表面处理 and reduced 工具寿命.
To achieve the best 表面处理, it’s important to find the right balance between 速度和进料. For finishing operations, we typically use a higher 主轴转速 and a lower 进料速度 compared to roughing operations. This combination helps to minimize 工具 deflection and vibration, resulting in a smoother 表面处理.
Here’s a table illustrating how 速度和进料 can be adjusted to achieve different 表面处理:
Surface Finish (Ra) | Spindle Speed (RPM) | Feed Rate (IPM) |
63 | 3000 | 20 |
32 | 4000 | 15 |
16 | 5000 | 10 |
It’s important to note that these values are just examples and the optimal settings may vary depending on the specific application. Other factors that can affect 表面处理 包括 工具 geometry, coolant usage, and 机械 rigidity.
常见问题
What is the difference between cutting speed and feed rate?
切割速度 refers to the speed at which the cutting edge of the 工具 moves past the cutting material, typically measured in surface feet per minute (SFM) or meters per minute (m/min). 进料速度, on the other hand, is the speed at which the 刀具 moves along the workpiece, usually measured in inches per minute (IPM) or millimeters per minute (mm/min).
How do I determine the optimal feed rate for a specific material?
The optimal 进料速度 取决于几个因素,包括 材料 being machined, the type of 刀具 used, the 主轴转速, and the desired 表面处理. A good starting point is to consult the 工具 manufacturer’s recommendations for the specific 材料 和 工具 正在使用。
Can I use the same speed and feed settings for all materials?
不 速度和进料 settings should be adjusted for each 材料 being machined. Different materials have different machining characteristics, and using the wrong settings can lead to poor results, 工具 damage, or even safety hazards.
What should I do if I experience tool breakage or poor surface finish?
If you experience 工具 breakage or poor 表面处理, you should first check your 速度和进料 settings. Make sure you’re using the correct settings for the 材料 和 工具 being used. You may also need to adjust other parameters, such as the 切割深度 or coolant usage.
How does chip load affect tool life?
Chip load has a significant impact on 工具寿命.如果 chip load is too high, it can cause excessive 工具 wear or even 工具 breakage. If the chip load is too low, it can cause the 工具 to rub against the workpiece, generating heat and leading to premature 工具 failure. Maintaining the correct chip load is essential for achieving optimal 工具寿命.
What is the role of coolant in optimizing speed and feed?
Coolant plays a crucial role in 数控加工 by reducing heat, lubricating the cutting zone, and flushing away chips. Proper coolant usage can allow for higher speeds 和 feeds while maintaining good 工具寿命 和 表面处理. It’s important to use the right type of coolant for the 材料 being machined and to ensure proper coolant concentration and flow rate.
摘要
优化 速度和进料 is crucial for achieving efficient and high-quality results in 数控加工.
进料速度 是指 速度 at which the 刀具 moves along the workpiece, while 主轴转速 refers to the rotational 速度 的 机器的 spindle.
之间的关系 cutting speed and feed rate must be carefully balanced to achieve optimal 机加工 results.
The optimal 进料速度 和 主轴转速 根据 材料 being machined.
Chip load plays a critical role in determining the optimal 喂食 and has a significant impact on 工具寿命.
Optimized 速度和进料 can improve 工具寿命 by reducing heat generation and distributing wear evenly.
High-speed machining involves using higher spindle speeds 和 喂料速率 to achieve faster material removal rates.
"(《世界人权宣言》) 切割深度 影响 进料速度 和 切割速度, with deeper cuts generally requiring lower 喂料速率.
Common mistakes to avoid when adjusting 速度和进料 include ignoring manufacturer recommendations, using excessive 速度, and using insufficient 喂食.
Achieving the best 表面处理 requires finding the right balance between 速度和进料, with higher spindle speeds 及以下 喂料速率 generally producing smoother finishes.
By understanding and applying the principles discussed in this article, machinists and programmers can optimize their 数控加工 processes, improve productivity, and achieve superior results. As a leading provider of 数控加工服务, we’re committed to helping our customers achieve their manufacturing goals through the application of advanced machining techniques and expertise.
联系我们 today to learn more about how our 数控加工服务 can benefit your business. We offer a wide range of 机械加工服务包括 数控铣床, turning, and 5 轴数控加工. We also specialize in 制造服务 例如 钣金加工 和 激光切割.
Sources
Sandvik Coromant. “Optimizing Milling Process Parameters.” Sandvik Coromant, https://www.sandvik.coromant.com/en-us/knowledge/milling/pages/optimizing-milling-process-parameters.aspx
Haas Automation, Inc. “CNC Mill Programming Workbook.” Haas Automation, Inc., https://diy.haascnc.com/sites/default/files/2021-07/Mill_Programming_Workbook_2020_EDITION.pdf
Kennametal Inc. “Machining Parameter Optimization.” Kennametal Inc., https://www.kennametal.com/us/en/resources/engineering-calculators/milling/machining-parameter-optimization.html
Harvey Performance Company. “Speeds and Feeds Guide.” Harvey Tool, https://www.harveytool.com/in-the-loupe/speeds-and-feeds-guide/
ISCAR. “Technical Guide – Speeds and Feeds.” ISCAR, https://www.iscar.com/eCatalog/Family.aspx?fnum=1625&mapp=ML&app=65
Tooling U-SME. “Fundamentals of CNC Machining.” Tooling U-SME, https://www.toolingu.com/classes/sample/102511
Disclaimer: The information provided in this article is intended for general guidance only and may not be applicable to all situations. Always consult with a qualified professional before making decisions about specific machining processes or parameters.
评论
出色的产品案例
标签
相关博客
从我们的博客中获取有关 CNC 加工的最新趋势和事实。