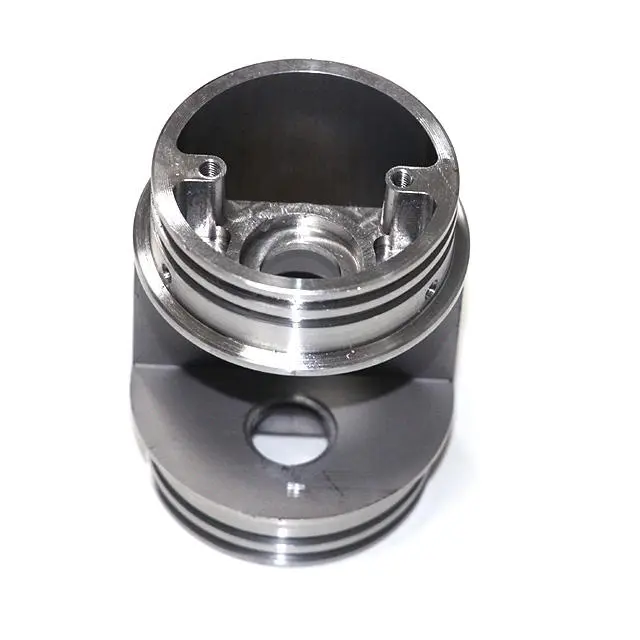
沉孔放电加工与线切割放电加工:选择正确工艺的综合指南
目录
导言
了解沉降片放电加工和线切割放电加工的关键区别、应用和特定行业的优势。
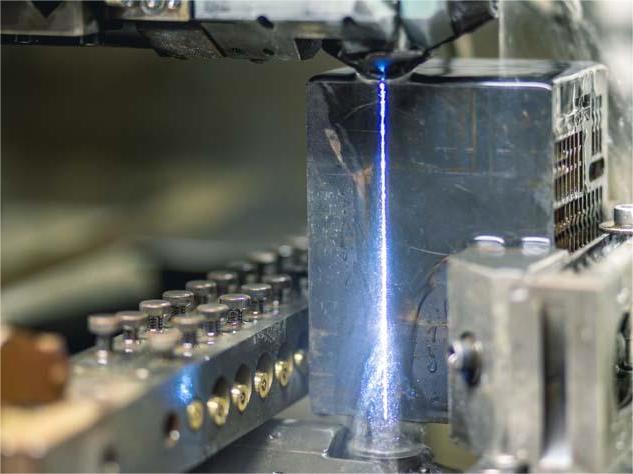
了解放电加工 (EDM)
放电加工(EDM)通过使用受控电火花侵蚀材料,彻底改变了金属加工工艺。与传统方法不同,放电加工无需物理接触,因此非常适合加工钛或淬火钢等超硬金属。
电火花加工的主要优势:
- 可处理硬度高达 90 HRC 的材料
- 实现最小公差 ±0.005毫米
- 消除易损部件上的机械应力
- 非常适合复杂的几何形状
电火花加工是如何工作的?火花背后的科学
EDM 依赖于三个核心组件:
- 电极:工具(沉降片)或金属丝会产生火花。
- 绝缘液:冲洗碎片并冷却工件(油或去离子水)。
- 电源:产生快速放电(高达每秒 100,000 次火花)。
案例研究:一家医疗设备制造商使用线切割放电加工技术加工钛合金手术工具,将零件变形量减少了 40%。
沉降片放电加工:精确加工复杂型腔
沉降片电火花加工(又称 拉姆放电加工 或 模具下沉)使用预先成型的电极来制造模具、冲模和复杂的型腔。
典型工作流程:
- 设计一个石墨/铜电极,镜像所需的空腔。
- 将工件浸入碳氢化合物油中。
- 降低电极,通过受控火花侵蚀材料。
最适合
- 注塑模具
- 尖锐的内角(如涡轮叶片冷却通道)
- 淬硬钢盲孔
沉孔放电加工机床在现代工业中的主要应用
行业 | 使用案例 |
---|---|
航空航天 | 具有复杂内部通道的燃油系统组件 |
医疗 | 具有微米级精度的种植体模具 |
汽车 | 传动齿轮模具 |
探索我们的 精密加工 类似项目的能力。
线切割放电加工:精密切割,实现复杂设计
线切割放电加工使用细黄铜线(直径 0.02-0.33 毫米)切割导电材料。金属丝从不接触工件,确保边缘无毛刺。
为什么选择线切割放电加工?
- 切割厚度可达 300 毫米
- 表面粗糙度可达 Ra 0.1 微米
- 适用于需要最少后期处理的原型机
了解我们如何 线切割放电加工 服务简化生产流程。
线切割机床的优势:特定行业的应用案例
- 电子产品:为 5G 设备切割铜散热器
- 国防:制造具有严格公差的装甲钢板
- 能源:用镍合金生产涡轮叶片
统计:78% 汽车模具制造商使用线切割放电加工机床制造冲裁冲头。
正面比较:沉降片与线切割
系数 | 沉降片放电加工 | 线切割放电加工 |
---|---|---|
工具类型 | 定制形状电极 | 细铜丝 |
轴运动 | 主要是垂直(Z 轴) | 多轴(X/Y/Z) |
材料去除率 | 200-400 毫米³/分钟 | 50-150 毫米³/分钟 |
成本效益 | 更高的模具成本 | 降低小批量生产的设置成本 |
对于大批量项目,请考虑我们的 压铸 解决方案
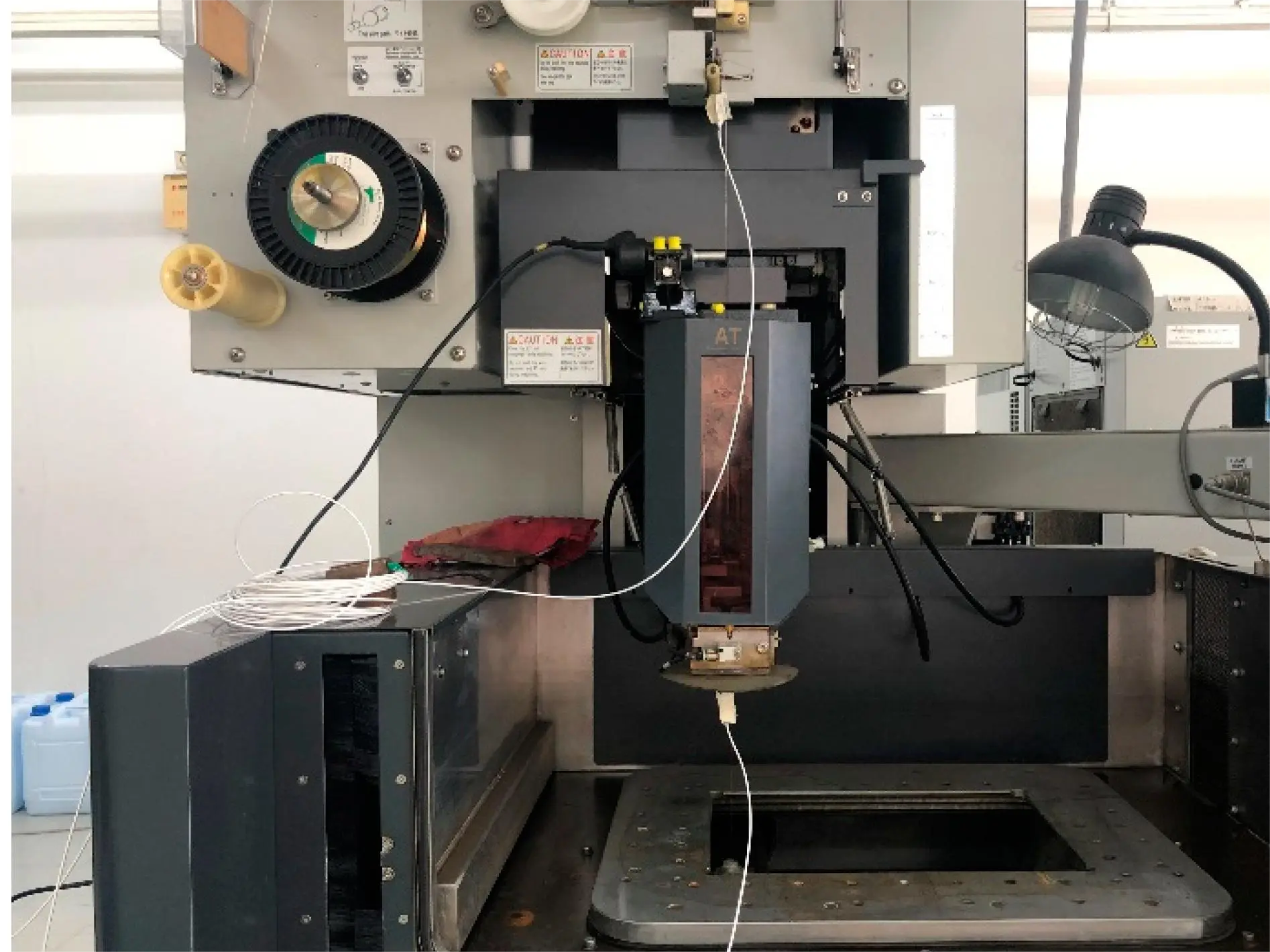
为您的项目选择合适的电火花加工工艺
选择 Sinker EDM 时:
- 您需要三维空腔或深肋。
- 材料厚度大于 150 毫米。
- 锐利的内角至关重要。
选择线切割放电加工用于:
- 二维轮廓或贯穿切割。
- 薄而脆弱的部件容易变形。
- 精度要求 ±0.005 毫米的项目。
还不确定?我们的 数控解决方案 团队提供免费咨询。
为什么要与我们合作提供放电加工解决方案?
客户故事:一家机器人公司利用我们的 5 轴系统将交货时间缩短了 30% 数控加工 和线切割加工组合。
常见问题:EDM 问题解答
哪种放电加工方法更适合小批量生产?
线切割加工对于原型和小批量加工而言,安装成本通常较低。
电火花加工可以处理非金属材料吗?
No-EDM 只适用于钢、钛或硬质合金等导电材料。
与数控铣床相比,电火花加工的精度如何?
电火花加工的细节更精细(±0.005 毫米,而铣削加工为 ±0.025 毫米),但速度较慢。
哪些行业最受益于电火花加工?
航空航天、医疗和汽车行业的关键部件都依赖于电火花加工。
主要收获
- 沉降片放电加工 在 3D 型腔和模具制造方面表现出色。
- 线切割放电加工 是超精密二维切割的理想选择。
- 这两种方法都能消除硬质材料上的机械应力。
- 与经过认证的专家合作,以获得最佳效果。
准备好开始您的项目了吗? 申请免费报价 今天!
评论
出色的产品案例
标签
相关博客
从我们的博客中获取有关 CNC 加工的最新趋势和事实。