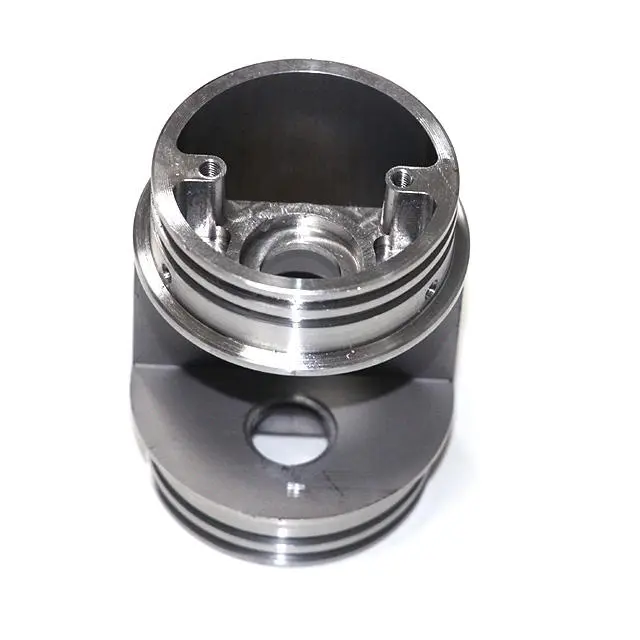
- +8615586668226
- [email protected]
- No. 30, Hongbang Industrial Park, Shenzhen
A CNC machine is a marvel of modern engineering. It’s a type of automated tool, controlled by computer software, that’s designed to perform a variety of machining operations with incredible precision. I have seen firsthand how these machines operate by following pre-programmed instructions, dictating every movement and cut. The machine starts with a block of material, known as the workpiece, and uses a range of cutting tools to shape it into the desired form. The process begins with a digital design created using CAD (Computer-Aided Design) software. This design is then translated into a set of instructions, or a programme, that the CNC machine can understand. As a business providing cnc fabrication services for products, we’ve witnessed a revolution in how we create parts; the precision and efficiency are unmatched.
The operation of a CNC machine is fascinating. Once the programme is loaded, the machine takes over, executing cuts and movements with a high degree of accuracy. This process involves removing material from the workpiece, a method known as subtractive manufacturing. Unlike manually operated machines, where a skilled operator manually guides the tool, CNC machines rely on computer instructions. This not only speeds up the machining process but also ensures consistency across every part produced. For example, in CNC milling, a rotating cutting tool moves across the workpiece, shaving off material layer by layer until the final shape is achieved. It’s remarkable how a machine can be programmed to perform such intricate tasks.
Precision is the cornerstone of quality in manufacturing, especially in industries like aerospace and medical devices. When I talk about precision, I’m referring to the ability to consistently produce parts that meet exact specifications, down to the smallest detail. In our line of work, the accuracy of a part can mean the difference between success and failure, safety and hazard. This is where CNC machines truly shine. With their computerized controls, these machines can deliver a degree of accuracy that’s nearly impossible to achieve with manual machines. In fact, CNC machines can maintain tolerances as tight as +/- 0.001 inches, ensuring that every part is virtually identical to the next.
The secret behind this precision lies in the way CNC machines are designed. They use precise motors and feedback systems to control the movement of the cutting tool. This allows the machine to follow the programmed path with exceptional fidelity, remove material from a workpiece, and create complex shapes with sharp edges and smooth surfaces. Furthermore, the use of high-quality cutting tools and the ability to control factors like speed and feed rate contribute to the overall precision of the process. Our experience with Precision Machining has shown us that the ability to achieve tight tolerances is not just about the machine itself, but also about the expertise in programming and operating it effectively.
When discussing efficiency, CNC machines are in a league of their own. As someone deeply involved in the manufacturing industry, I’ve observed that one of the main advantages of CNC machining is its ability to run 24/7. Unlike manual machines that require breaks and are prone to fatigue, CNC machines can run continuously, only stopping for maintenance or tool changes. This continuous operation significantly increases throughput. For instance, a CNC mill can work through the night, completing tasks that would take days for a human operator. This not only speeds up the production process but also ensures timely delivery, which is crucial in today’s fast-paced market.
Another aspect of efficiency is the speed at which CNC machines operate. They are much faster than manual counterparts. For example, a task that might take hours on a manual machine can be completed in minutes on a CNC machine. This speed is particularly beneficial when producing large quantities of parts. Moreover, the use of CNC machines reduces the need for constant supervision. Once the machine is programmed and set up, it can operate with minimal human intervention. This allows workers to focus on other critical tasks, further enhancing overall operational efficiency. In our operations, we’ve found that CNC technology has not just improved our production speed but also optimized our workflow significantly.
Automation is a game-changer in manufacturing, and CNC machining is a prime example of this. One of the most significant impacts of automation is the reduction in labor costs. With CNC machines, the need for a large workforce is diminished. A single skilled operator can oversee multiple machines, which dramatically reduces the number of workers required on the shop floor. This is a stark contrast to conventional machines, where each machine typically requires a dedicated operator. By minimizing the need for manual labor, businesses can significantly lower their operational expenses. In my experience, the shift to automated CNC machining has allowed us to reallocate resources more effectively, investing in areas that further enhance our capabilities.
Moreover, automation in CNC machining contributes to a reduction in material wastage. CNC machines are incredibly precise, meaning they only remove the necessary amount of material, minimizing waste. This is particularly important when working with expensive materials. Compared to manual operations, where the possibility of human error is higher, CNC machines ensure that material usage is optimized. Additionally, the consistency and repeatability of CNC machining lead to fewer defects and reworks, further reducing costs. The initial investment in a CNC machine might be higher than that of a manual machine, but the long-term savings in labor and material costs make it a cost-effective solution for many businesses.
The versatility of CNC machines in handling a wide range of materials is one of their most significant advantages. From metals like aluminum, steel, and brass to plastics, wood, and even composites, CNC machines are capable of working with a diverse array of materials. This capability opens up a world of possibilities in manufacturing. For instance, in our Sheet Metal Fabrication services, we often switch between different types of metals, each requiring specific cutting techniques and tools. CNC machines allow us to make these transitions seamlessly, without compromising on quality or precision.
This material versatility is crucial for industries that require parts made from different materials. For example, in the automotive industry, various components are made from different metals and plastics. A CNC machine can be programmed to switch between these materials, ensuring that each part is crafted to its specific requirements. Moreover, the ability to work with different materials means that manufacturers can experiment with new materials and develop innovative products. This flexibility is vital for staying competitive and meeting the evolving needs of the market. In my view, the material versatility of CNC machines is not just an advantage; it’s a necessity in today’s dynamic manufacturing landscape.
CNC milling is a cornerstone of modern manufacturing processes. As someone who has been in this field for years, I’ve seen how CNC milling machines have transformed the way we produce parts. CNC milling involves using rotating cutting tools to remove material from a workpiece. This milling process is incredibly versatile, allowing for the creation of complex shapes and designs that would be difficult, if not impossible, to achieve with manual machines. In CNC milling, the workpiece is typically held stationary while the cutting tool moves along multiple axes. This allows for intricate cuts and precise shaping of the material.
One of the key advantages of CNC milling is its ability to perform a wide range of operations. From drilling and boring to contouring and slotting, a CNC mill can handle various tasks with ease. This makes it an invaluable tool in machine shops and manufacturing facilities. For example, in our machining services, we often use CNC milling to create parts with complex geometries, such as those required in the aerospace industry. The precision and versatility of CNC milling make it an essential process for creating high-quality, intricate components. Additionally, CNC milling is often used in conjunction with other machining processes, such as turning, to produce parts with a high degree of accuracy and complexity.
While the advantages of CNC machines are numerous, it’s important to acknowledge that there are disadvantages as well. One notable disadvantage is the higher initial cost compared to manual machines. Purchasing a CNC machine represents a significant investment, which might be a barrier for small businesses or startups. Additionally, there are ongoing costs associated with maintenance, software updates, and the need for a skilled operator to program and operate the machine. While automation reduces the need for a large workforce, it also requires personnel with specialized skills in CNC programming and operation. Finding and retaining such skilled individuals can be a challenge and may involve additional training expenses.
Another potential disadvantage is the complexity of CNC machines. While they are designed to simplify the manufacturing process, they can be complex to set up and program. Errors in programming can lead to incorrect cuts, material wastage, and even damage to the machine or tools. Furthermore, while CNC machines reduce the possibility of human errors in the machining process, they are not immune to malfunctions. Mechanical failures or software glitches can occur, leading to downtime and potential delays in production. In my experience, while these issues are relatively rare, they can be disruptive when they happen. It’s crucial to have a robust maintenance plan and skilled technicians to address any technical problems promptly.
When comparing CNC machining to other manufacturing methods, such as 3D printing, it’s essential to understand their respective strengths and limitations. CNC machining is a subtractive manufacturing method, meaning it starts with a block of material and removes portions to achieve the desired shape. In contrast, 3D printing, also known as additive manufacturing, builds parts layer by layer from a digital model. One of the key differences is in the materials they can use. While CNC machines can work with a wider range of materials, including metals, plastics, and wood, 3D printing is often limited to plastics and certain metals. Additionally, CNC machining is generally better suited for creating large parts or parts that require high strength and durability.
Another significant difference is in the level of precision. CNC machining typically offers higher precision and tighter tolerances compared to 3D printing. This makes CNC machining the preferred choice for applications where accuracy is critical, such as in the aerospace and medical industries. However, 3D printing excels in creating highly complex and intricate designs that might be challenging or impossible to achieve with CNC machining. For example, 3D printing can produce parts with internal cavities and complex geometries that would require multiple setups and operations on a CNC machine. In our experience, the choice between CNC machining and 3D printing often depends on the specific requirements of the project, including the material, complexity, precision, and production volume.
The following table compares CNC machining and 3D printing.
Feature | CNC Machining | 3D Printing |
Process Type | Subtractive | Additive |
Material Range | Wide (metals, plastics, wood, composites) | Limited (mainly plastics, some metals) |
Precision | High (tight tolerances) | Moderate |
Part Size | Generally larger | Generally smaller |
Strength & Durability | High | Moderate to high, depending on material and process |
Complexity | Moderate to high | Very high (can create intricate internal structures) |
Production Volume | Medium to high | Low to medium |
Cost | Higher initial investment, lower cost per part | Lower initial investment, higher cost per part |
Speed | Faster for simple parts, slower for complex parts | Slower overall, but faster for complex geometries |
CNC machining services have become indispensable across a wide range of industries, each leveraging the unique advantages of this technology. The aerospace industry, for instance, relies heavily on CNC machining to produce high-precision components that must withstand extreme conditions. Similarly, the automotive sector uses CNC machining to manufacture parts with tight tolerances and complex geometries, ensuring the performance and safety of vehicles. In the medical field, CNC machining plays a crucial role in creating intricate and precise medical devices, from surgical instruments to implants. Our experience working with clients across various industries has shown us the versatility and adaptability of CNC Machining.
Beyond these sectors, CNC machining is also integral to industries like electronics, where it’s used to produce precise components for electronic devices, and in the energy sector, where it helps in manufacturing parts for renewable energy systems. Even in consumer products, CNC machining is employed to create high-quality, durable goods. The ability of CNC machines to work with a variety of materials and produce parts with high accuracy makes them a valuable asset in any industry that requires precision and quality. As I see it, the applications of CNC machining are vast and continue to expand as technology evolves and industries discover new ways to utilize its capabilities.
Choosing the right CNC machining services provider is a critical decision that can significantly impact the quality, cost, and timeliness of your products. One of the first things to consider is the provider’s experience and expertise. Look for a company with a proven track record in your industry and a deep understanding of the specific requirements of your project. It’s also important to assess their technological capabilities. Do they have state-of-the-art CNC machines? Can they handle the materials you need? What about their quality control processes? Ensuring that the provider has the right equipment and processes to meet your specifications is crucial. In our business, we pride ourselves on not just meeting but exceeding these expectations, offering comprehensive Machining Services tailored to our clients’ diverse needs.
Another important consideration is the provider’s capacity and scalability. Can they handle your production volume, whether it’s a small batch or a large run? And can they scale up production as your needs grow? Additionally, consider their lead times and ability to meet deadlines. Timeliness is crucial in today’s fast-paced market, and you need a partner who can deliver on time without compromising quality. Finally, don’t overlook the importance of communication and customer service. A good CNC machining provider should be responsive, transparent, and easy to work with. They should be able to provide regular updates, address any concerns promptly, and work collaboratively with you to ensure the success of your project.
What types of materials can be used in CNC machining?
CNC machining can handle a wide range of materials, including metals like aluminum, steel, brass, and titanium, as well as plastics, wood, and composites. The choice of material often depends on the specific application and the desired properties of the final product.
How accurate is CNC machining?
CNC machining is renowned for its high precision. Modern-day CNC machines can achieve tolerances as tight as +/- 0.001 inches, making them ideal for applications that require a high degree of accuracy, such as in the aerospace and medical industries.
What is the difference between CNC milling and CNC turning?
In CNC milling, the workpiece is typically held stationary while a rotating cutting tool moves across it to remove material. In CNC turning, the workpiece rotates while a stationary cutting tool shapes it. Both processes are used to create precise parts but are suited for different types of shapes and features. Here you can find more about CNC Turning.
How long does it take to program a CNC machine?
The time it takes to program a CNC machine depends on the complexity of the part and the experience of the programmer. Simple parts may only take a few minutes to program, while more complex parts can take several hours or even days.
Is CNC machining cost-effective for small production runs?
While CNC machining is highly cost-effective for medium to large production runs due to its automation and efficiency, it can also be viable for small runs, especially when high precision or complex geometries are required. The initial setup cost might be higher, but the accuracy and consistency of CNC machining can lead to cost savings in the long run.
Can CNC machines create complex shapes?
Yes, CNC machines are incredibly versatile and can create highly complex shapes and designs. With multi-axis capabilities, such as those found in 5 Axis CNC Machining, these machines can produce intricate parts with features like curves, angles, and undercuts that would be difficult or impossible to achieve with manual machines.
CNC machining offers unparalleled precision, making it essential for industries requiring tight tolerances.
Automation in CNC machining leads to significant cost savings in labor and material usage.
CNC machines can handle a wide range of materials, providing versatility in manufacturing.
CNC milling is a crucial process for creating complex shapes and designs.
While there are some disadvantages, such as higher initial costs, the benefits of CNC machining often outweigh them.
CNC machining compares favorably to other methods like 3D printing in terms of precision and material versatility.
Numerous industries, including aerospace, automotive, and medical, rely on CNC machining for high-quality parts.
Choosing the right CNC machining provider involves considering factors like experience, technology, capacity, and customer service.
The use of computerized controls and cutting tools allows CNC machines to operate with minimal manual intervention, reducing the possibility of human errors.
CNC machining is not just a manufacturing method; it’s a cornerstone of the fourth industrial revolution, driving innovation and efficiency across various sectors.
I trust this comprehensive guide has illuminated the multifaceted world of CNC machining and its pivotal role in modern manufacturing. If you have further inquiries or wish to explore how our cnc fabrication services can cater to your specific needs, please don’t hesitate to reach out. We’re here to transform your concepts into reality with precision, efficiency, and unwavering quality. Our expertise spans across various sectors, including Aerospace and Aviation, Automotive, Medical Devices, Electronics, and many more, ensuring we can meet the unique demands of your industry.
Get the latest trends and facts about CNC fabrication from our blog.
Shenzhen Runkey Precision Technology Co. Ltd, a subsidiary of the Tensun Group, is your trusted one-stop solution for custom manufacturing from prototyping to production.Transforming your idea into reality with digital manufacturing resources,streamlined processes, expert guidance,accelerated timelines, and uncompromising quality.
©2024. CNC Fabrication All Rights Reserved.