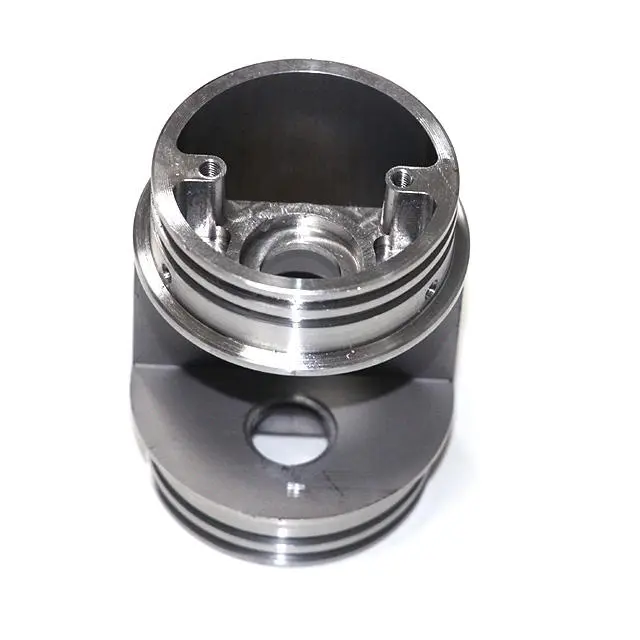
- +8615586668226
- [email protected]
- No. 30, Hongbang Industrial Park, Shenzhen
Both 4130 steel and 4140 steel are low alloy steel grades, known for their excellent balance of strength, toughness, and machinability. These steel materials are widely used in various industries due to their versatility and reliable performance. The “41” in their names indicates that they are chromium-molybdenum steel alloys, which are known for their enhanced hardenability and resistance to fatigue. 4130 steel is often chosen when a good balance of toughness and weldability is required, while 4140 steel provides higher strength and hardness, often used when those properties are paramount. These two types of steel are part of the large family of steel products we work with here at cnc fabrication serive Manufacturing plants for products.
As a manufacturing company specializing in CNC machining and fabrication, we encounter a broad range of materials daily. The use of 4130 and 4140 steel is common due to their specific properties. 4130 steel is often favored for components that require good weldability and toughness, such as aircraft parts, while 4140 steel may be preferred for components that require higher strength, such as gears and shafts. Understanding the subtle yet crucial differences between 4130 and 4140 is vital to the success of any manufacturing project. The flexibility of steel allows us to offer a variety of services like CNC Machining, Sheet Metal Fabrication, and even Rapid Prototyping.
4130 steel exhibits a range of mechanical properties that make it a popular choice in various applications. Its tensile strength typically ranges from 65,000 to 85,000 psi (450 to 586 MPa), while its yield strength falls within the range of 40,000 to 60,000 psi (276 to 414 MPa). The strength of 4130 steel is good, and it boasts excellent toughness, meaning it can absorb significant energy before fracturing. This steel also has a relatively high fatigue strength, allowing it to withstand repeated stress cycles, as well as good weldability, which makes it suitable for applications where welding is required.
4130 steel also has a high impact resistance, and it is more resistant to stress corrosion cracking compared to some other types of steel. These characteristics make it a good fit for aerospace, automotive, and even some industrial components. The 4130 steel exhibits a good balance between these mechanical properties, which often makes it a versatile material that can be used in different designs. The tensile strength of 4130 steel can vary depending on the heat treatment applied, but it generally offers a good middle ground between strength and toughness.
4140 steel has a higher strength and hardness compared to 4130 steel. The typical tensile strength is in the range of 90,000 to 120,000 psi (621 to 827 MPa), with a yield strength between 60,000 and 90,000 psi (414 to 621 MPa). The strength of 4140 steel is notably higher than 4130, and this results in a higher wear resistance and a greater ability to withstand higher loads. This steel also exhibits good fatigue strength, making it suitable for applications involving cyclic stress. This steel is a versatile option for high-stress applications.
While 4140 steel has a higher strength, it is not as tough as 4130 steel, meaning it might be more prone to fracture under certain high-impact conditions. Also, 4140 steel is relatively less weldable than 4130. Due to its higher hardness, 4140 steel also makes it more difficult to machine compared to 4130. Despite these differences, 4140 steel boasts a higher level of performance where strength and wear resistance are most needed. Making 4140 steel parts requires a careful approach, but our experienced team at cnc fabrication serive Manufacturing plants for products are equipped to handle this material.
The key differences between these two steel grades primarily stem from their chemical compositions, specifically the carbon content in 4140 steel. 4140 steel contains slightly higher carbon content, around 0.38-0.43%, compared to 4130 steel, which has a carbon content of about 0.28-0.33%. This difference in carbon content in 4140 steel leads to the higher strength and hardness of 4140 steel and also its relative decrease in weldability and toughness. 4140 steel exhibits good fatigue strength, which is essential for many industrial uses.
The 4140 and 4130 steel differ in their performance in different environments. 4130 steel has a higher degree of ductility, making it more resistant to fracture under stress, while 4140 steel is more susceptible to cracking under impact. However, if higher strength and wear resistance are paramount, 4140 steel is the better choice. When comparing 4140 vs 4130 we must always consider the specific needs of the project. This difference in carbon content is why 4140 has a higher carbon. The right choice depends entirely on what your application needs.
4130 steel has excellent weldability due to its lower carbon content. It is less prone to cracking after welding, and it can be readily joined using various welding techniques. This makes it a better choice for applications that require welding, such as structural supports or components requiring assembly via welding. Because of it’s good weldability, 4130 steel is also more commonly used in aerospace than 4140 steel. The excellent weldability of this material is important as it allows for a seamless integration of different parts.
On the other hand, 4140 steel is relatively more challenging to weld due to its higher carbon content. When welded improperly, 4140 steel can form a hard, brittle zone around the weld which might lead to cracking. This means that preheating, precise temperature control, and post-weld heat treatments are usually necessary for 4140 steel. Therefore, when welding is a critical process in your project, 4130 steel would be a better choice. At cnc fabrication serive Manufacturing plants for products, we carefully assess this factor and advise our clients on best practices. The superior weldability of 4130 steel is critical for many applications.
Choosing between 4130 steel and 4140 steel comes down to your specific application needs. If toughness, good weldability, and moderate strength are your primary requirements, then 4130 steel is likely the better choice. 4130 steel is also more resistant to corrosion compared to 4140. We often suggest this steel for components that may see impact and require being welded together. 4130 steel is widely used in applications requiring fatigue and wear resistance too.
However, if your application needs higher strength, hardness, and wear resistance, and welding is not as critical, then 4140 steel is probably a better fit. It is also a good option for parts that will see significant loads and high stress conditions, such as gears, shafts, and axles. 4140 steel has higher strength and provides a more durable part when strength and wear resistance are paramount. 4140 is typically more readily available than 4130. The final decision depends on a complete 4140 vs 4130 analysis, as well as the overall project needs.
The carbon content in 4140 steel is primarily responsible for its increased strength and hardness, and how that property compares in 4140 vs 4130. With a carbon content range of 0.38-0.43%, 4140 steel can be hardened to a greater degree than 4130 steel, which has a lower carbon content in 4140 steel. This higher carbon percentage allows it to form a harder martensitic structure during heat treatment, resulting in a stronger and more wear-resistant steel. The carbon also helps the steel resist deformation.
However, the higher carbon content also leads to increased brittleness and decreased weldability. This is because the higher carbon content makes the steel more prone to cracking during welding or in high-impact applications. It can also affect machining processes. When you choose the right one, knowing these differences is vital. When making 4140, we must take these considerations into account. When it comes to manufacturing, the carbon content in 4140 steel is one of the key differences we focus on during the manufacturing process.
When making a 4140 vs 4130 steel decision, you need to consider multiple factors. Your choice must align with the operational requirements of the part, the method of manufacturing and other specific needs. Firstly, what is more important for your component: strength, or toughness and weldability? If strength is more important than weldability then 4140 steel might be the better choice. Alternatively, if the part will be welded or will require impact resistance, 4130 steel may be the better option. We offer insights based on the 4140 vs debate to assist you in your decision.
The cost of material, the cost of additional heat treatment, and the machinability are other critical factors. While both steel grades are cost-effective, 4140 steel usually requires more careful machining and heat treatment procedures due to its hardness, which could result in added costs. 4140 steel is the better option, depending on your criteria. We always advise our customers based on a thorough evaluation of their specifications, making sure the right material is selected and that it meets all requirements. If 4130 steel is chosen, its 4130 steel properties may be a good fit for your project, but we always consider many factors.
Machining 4140 and 4130 steel involves considerations about the quality 4140 and 4130 steel you use, including tool selection, cutting speeds, and cooling methods. Since 4140 steel has a higher strength and hardness, it generally requires more robust tooling and lower cutting speeds compared to 4130 steel. The heat generated during machining is also higher for 4140 steel, and using suitable cooling techniques is crucial to prevent excessive tool wear and damage to the part. 4140 steel machining requires more precision and a different approach than 4130.
When machining 4130 steel, the same careful considerations must be used, although its easier to machine compared to 4140 steel. The lower carbon content of 4130 steel makes it less likely to cause tool wear and the machining is much more straightforward. Regardless of the type of steel, precision and accuracy during the machining process are crucial for ensuring high-quality parts. Here at cnc fabrication serive Manufacturing plants for products, we are experts in both 4140 and 4130 steel machining, and all steel materials.
4140 steel is a popular choice in the manufacturing process due to its balance of strength, toughness, and wear resistance, allowing it to use 4140 in certain situations. If your project needs a material that withstands high loads, wear, and high-stress situations, then 4140 steel may be the correct option for you. The higher tensile and yield strength make this a reliable option for many industrial components. 4140 steel has high durability and is perfect for high performance environments.
Also, in 4140 vs 4130 debates, the ease of finding 4140 is something to consider too. The steel is available relatively easily, 4140 is not as corrosion-resistant as other alloys but is easy to process for many applications. When it comes to applications that require strength, and when toughness and weldability are not a priority, 4140 steel is an excellent material for your manufacturing needs. 4140 steel reaches a temperature at which it can be heat treated to improve performance. When we use 4140 in our projects, we make sure to choose it when these conditions are met.
The primary difference lies in their carbon content, with 4140 steel having a higher carbon level than 4130 steel. This results in 4140 steel having higher strength and hardness, while 4130 steel offers better toughness and weldability.
4130 steel is more weldable than 4140 steel due to its lower carbon content. It is less prone to cracking after welding and requires fewer precautions, like preheating, compared to 4140 steel.
4130 steel is best suited for applications requiring a good balance of toughness, weldability, and moderate strength, such as aircraft components, structural parts, and high-fatigue components.
4140 steel is preferred when higher strength and hardness are needed, such as in gears, shafts, axles, and high-stress mechanical components, especially if weldability is not a primary concern.
4140 steel has higher tensile strength, yield strength, and hardness compared to 4130 steel, while 4130 steel has a higher level of toughness, impact resistance, and fatigue resistance.
Yes, both 4130 and 4140 steel are commonly used steel alloys and are widely available, however, 4140 is typically more readily found.
Choosing between 4130 steel and 4140 steel requires a comprehensive understanding of their unique characteristics. At cnc fabrication serive Manufacturing plants for products, we have extensive experience with both steel grades, working with different projects, such as Aerospace, Automotive, Medical Devices, and Industrial Equipment. We are adept at handling complex manufacturing needs, ensuring your project uses the right material for each specific application. Our services extend from CNC Machining to Rapid Prototyping. We encourage you to reach out to us so we can help you choose the right steel for your needs. We offer a wide range of solutions, including Surface Finishing, and Assembly. Our commitment to quality and precision makes us your ideal partner in manufacturing.
Get the latest trends and facts about CNC fabrication from our blog.
Shenzhen Runkey Precision Technology Co. Ltd, a subsidiary of the Tensun Group, is your trusted one-stop solution for custom manufacturing from prototyping to production.Transforming your idea into reality with digital manufacturing resources,streamlined processes, expert guidance,accelerated timelines, and uncompromising quality.
©2024. CNC Fabrication All Rights Reserved.