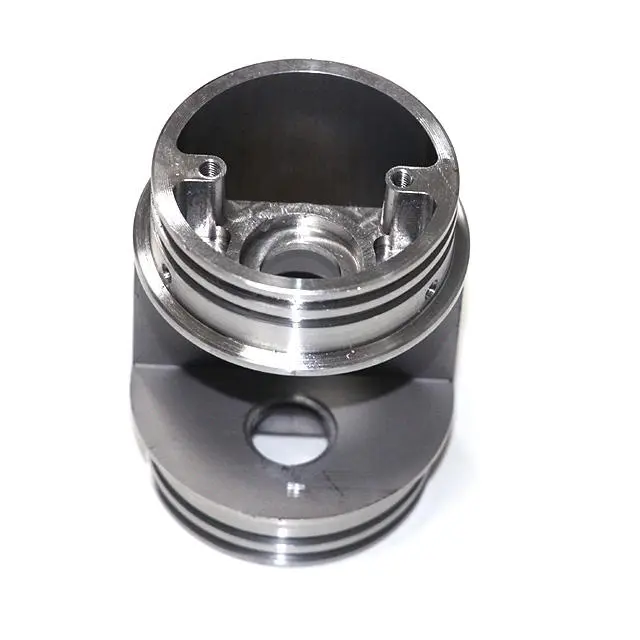
- +8615586668226
- [email protected]
- No. 30, Hongbang Industrial Park, Shenzhen
Computer Numerical Control (CNC) machining is a manufacturing process that uses pre-programmed computer software to dictate the movement of factory tools and machinery. This process can control a range of complex machines, from grinders and lathes to mills and routers. The CNC machine interprets a design from specialized software, and then uses a rotating cutting tool to remove material from a workpiece, shaping it into the desired form.
CNC machining allows for the production of highly accurate and complex parts with tight tolerances, making it ideal for various industries, including aerospace, automotive, and medical devices. It is a vital process that enables automation, reduces human error, and significantly increases production efficiency. At our CNC fabrication service, we leverage advanced CNC machines to deliver exceptional results that meet our client’s precise specifications and a great surface finish. We have also experience with cnc laser.
There are several types of CNC machines, each designed for specific tasks. CNC milling machines are the most common, utilizing rotary cutters to remove material from a workpiece. CNC lathes, on the other hand, rotate the workpiece against a cutting tool, ideal for creating cylindrical parts. CNC laser machines use a highly focused laser beam to cut through the metal, while CNC plasma machines use a plasma torch for cutting electrically conductive materials.
Other types of CNC include CNC routers, CNC grinders, and CNC water jet cutters, each offering unique machine capabilities. The choice of machine depends on the material being processed, the complexity of the design, and the required precision. Different types of CNC machines are essential for various applications, ensuring the versatility and efficiency of CNC technology. Our machine tools are top-of-the-line and help us produce high-quality products. We can help you with aluminum parts.
Aluminum is one of the most widely used materials in CNC machining due to its exceptional properties. It is lightweight yet strong, making it perfect for various applications. Aluminum also exhibits excellent corrosion resistance, machinability, and thermal conductivity. Aluminum alloy offers enhanced strength and durability, making it suitable for demanding environments.
Aluminum parts are commonly used in industries such as aerospace, automotive, and electronics due to their lightweight and robust nature. The ease of machining aluminum makes it a cost-effective choice for both prototyping and mass production, that is why is so widely used. We are experts at machining aluminum. Aluminum is an incredibly versatile metal and can be made into a variety of products.
The five common types of aluminum CNC machining processes are:
CNC Milling: CNC milling is a versatile process that uses a rotating cutting tool to remove material from a stationary workpiece. It’s ideal for creating complex shapes and designs in aluminum.
CNC Turning: CNC turning involves rotating an aluminum workpiece against a stationary cutting tool. This process is perfect for producing cylindrical aluminum parts with high precision.
CNC Drilling: Involves using a machine to drill holes in the workpiece.
5-Axis CNC Machining: 5-axis CNC machining allows for complex and intricate designs by moving the cutting tool and workpiece in five different axes simultaneously. This process is ideal for high-precision components used in aerospace and medical industries.
Precision Machining: Precision machining ensures tight tolerances and superior surface finish. It involves a combination of milling, turning, and other techniques to achieve exact specifications. Precision CNC machining is critical for applications requiring high accuracy.
CNC technology offers numerous benefits for aluminum machining. It provides high precision and repeatability, ensuring consistent quality across all parts. CNC machining allows for complex designs and intricate details that would be difficult or impossible to achieve with manual methods.
Additionally, CNC machines can operate continuously, increasing production efficiency and reducing lead times. The automation provided by CNC technology also minimizes human error, leading to higher accuracy and less material waste. Aluminum machining is vital to our business operations. Our machine capabilities are second to none.
Various tools are used in CNC machining of aluminum, each designed for specific operations. Cutting tools such as end mills, face mills, and drills are commonly used in CNC milling. These tools are made from high-speed steel or carbide to withstand the heat and stress of machining aluminum.
In CNC turning, lathe tools like turning, facing, and boring tools are employed. For precision machining, specialized tools such as reamers, taps, and dies ensure tight tolerances and a superior surface finish. Tools for machining play a crucial role in achieving the desired results. Cutting tool selection is a vital step in creating a product.
CNC machining plays a significant role in numerous industries:
Aerospace: CNC machines produce high-precision components for aircraft, ensuring safety and reliability. Aluminum alloy is favored for its lightweight and strength.
Automotive: CNC technology is used to manufacture engine parts, body panels, and other automotive components. Aluminum reduces vehicle weight, improving fuel efficiency.
Medical Devices: Precision CNC machining is essential for creating intricate medical instruments and implants. Aluminum‘s biocompatibility makes it suitable for medical applications.
Electronics: CNC machining is used to produce enclosures, connectors, and other electronic components. Aluminum‘s electrical conductivity and heat dissipation properties are advantageous.
Robotics: CNC machining helps create precise and durable parts for robots, enabling complex movements and operations.
Precision is paramount in CNC machining, particularly when working with aluminum. Precision CNC machining ensures that each part meets exact specifications, which is critical for applications where even minor deviations can compromise performance. For example, in the aerospace industry, precision components are essential for the safe operation of aircraft.
High precision also enhances the functionality and longevity of machined parts. Precision machining minimizes wear and tear, reduces the need for frequent replacements, and ensures optimal performance. Achieving high precision requires advanced CNC machines, skilled operators, and rigorous quality control processes.
CNC machining aluminum presents several challenges:
Chip Formation: Aluminum tends to form long, continuous chips that can clog machines and affect surface finish. Using chip breakers and appropriate cutting tools can mitigate this issue.
Built-Up Edge (BUE): Aluminum can adhere to the cutting tool, forming a BUE that reduces tool life and surface quality. Applying proper coolants and coatings can minimize BUE formation.
Thermal Expansion: Aluminum has a high thermal expansion coefficient, which can cause dimensional inaccuracies during machining. Controlling the machining environment temperature and using sharp cutting tools can help manage thermal expansion.
Workpiece Deformation: Thin aluminum parts may deform under machining forces. Proper fixturing and support are essential to maintain the workpiece‘s shape.
Challenge | Solution |
Chip Formation | Use chip breakers, select appropriate cutting tools |
Built-Up Edge (BUE) | Apply coolants, use coated tools |
Thermal Expansion | Control machining environment temperature, use sharp cutting tools |
Workpiece Deformation | Ensure proper fixturing and support, optimize machining parameters and processes |
Corrosion | Apply protective coatings, store in a controlled environment |
Surface Finish Imperfections | Optimize machining parameters, use appropriate finishing processes |
Choosing the right CNC machining service is crucial for the success of your project. Consider the following factors:
Expertise: Look for a service provider with extensive experience in CNC machining aluminum. They should have a deep understanding of aluminum alloys and the specific requirements of your industry.
Technology: Ensure the provider uses state-of-the-art CNC machines and tools. Advanced technology is essential for achieving high precision and efficiency.
Quality Control: A reputable CNC machining service will have rigorous quality control processes in place to ensure that every part meets your specifications.
Customer Support: Choose a provider that offers excellent customer support and communication throughout the project. They should be responsive to your needs and provide regular updates.
As a leading CNC fabrication service, we pride ourselves on our expertise, advanced technology, and commitment to quality. We have successfully completed numerous projects across various industries, delivering exceptional results that exceed our clients’ expectations.
What makes aluminum a popular choice for CNC machining?
Aluminum is popular for CNC machining due to its lightweight, strength, corrosion resistance, and excellent machinability. Its properties make it ideal for various applications across multiple industries.
How does CNC machining improve production efficiency?
CNC machining improves production efficiency by automating the machining process, reducing human error, and enabling continuous operation. This results in faster production times and higher output.
What industries benefit most from precision CNC machining?
Industries such as aerospace, automotive, medical devices, and electronics benefit significantly from precision CNC machining. These sectors require high-precision components for optimal performance and reliability.
What are the key considerations when choosing a CNC machining service?
Key considerations include the provider’s expertise, the technology they use, their quality control processes, and their customer support. Choosing a reputable and experienced provider is essential for project success.
What are the main types of CNC machines used for aluminum?
The main types of CNC machines used for aluminum include CNC milling machines, CNC lathes, 5-axis CNC machines, and precision machining centers. Each type offers specific capabilities for different machining needs.
What is the difference between CNC milling and CNC turning?
CNC milling involves using a rotating cutting tool to remove material from a stationary workpiece, while CNC turning involves rotating the workpiece against a stationary cutting tool. CNC milling is ideal for complex shapes, while CNC turning is best for cylindrical parts.
CNC machining is a versatile and efficient manufacturing process widely used across various industries.
Aluminum is a preferred material for CNC machining due to its lightweight, strength, and machinability.
Common aluminum CNC machining processes include milling, turning, drilling, 5-axis machining, and precision machining.
CNC technology offers numerous benefits, including high precision, repeatability, and increased production efficiency.
Choosing the right CNC machining service is crucial for project success, and factors such as expertise, technology, quality control, and customer support should be considered.
Proper tool selection and process optimization are essential for overcoming challenges in CNC machining aluminum.
At our CNC fabrication service, we are dedicated to providing top-notch machining services that meet the highest standards of quality and precision. Whether you need prototypes or large-scale production, we have the expertise and technology to deliver exceptional results. Our commitment to excellence and customer satisfaction sets us apart in the industry. Contact us today to discuss your project and discover how we can help you achieve your manufacturing goals.
Get the latest trends and facts about CNC fabrication from our blog.
Shenzhen Runkey Precision Technology Co. Ltd, a subsidiary of the Tensun Group, is your trusted one-stop solution for custom manufacturing from prototyping to production.Transforming your idea into reality with digital manufacturing resources,streamlined processes, expert guidance,accelerated timelines, and uncompromising quality.
©2024. CNC Fabrication All Rights Reserved.