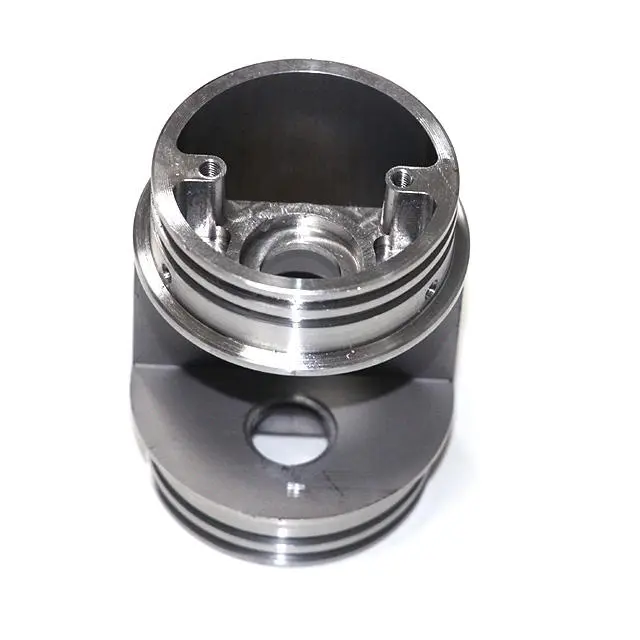
- +8615586668226
- [email protected]
- No. 30, Hongbang Industrial Park, Shenzhen
A rivet is a permanent mechanical fastener consisting of a smooth, cylindrical shaft with a head on one end. The rivet is inserted through holes in the materials being joined, and then the tail end is deformed or compressed to create a second head, securing the materials together. This process creates a strong and reliable joint, making rivets ideal for a wide range of applications.
Rivets are similar to bolts and screws but differ in their installation method and permanence. Unlike bolts and screws, which can be easily removed and reused, rivets are permanently installed. This makes them suitable for applications where a tamper-proof or vibration-resistant joint is required.
Rivets offer several advantages over other types of fasteners. They are cost-effective, especially for high-volume applications. They are also quick to install, even in hard-to-reach areas, often requiring only access to one side of the joint. CNC Machining can be used in conjunction with rivets for complex parts. Furthermore, rivets are highly reliable and durable, providing excellent shear and tensile strength. Fabrication Services frequently employ rivets for their robust nature.
In industries like aerospace and automotive, where safety and reliability are critical, rivets are the preferred choice. Their ability to withstand high stress and vibration makes them ideal for joining critical components. This is why Aerospace and Automotive industries utilize rivets extensively.
There are many types of rivets available, each designed for specific applications and materials. Six of the most common rivet types include:
Blind Rivets: Also known as pop rivets, these are versatile and easy to install, requiring access to only one side of the joint. CNC Solutions often involve blind rivets.
Solid Rivets: These are heavy-duty rivets offering exceptional strength and are typically used in structural applications.
Tubular Rivets: These rivets have a hollow shaft, making them lighter and easier to deform than solid rivets. They are often used in applications where high strength is not required.
Split Rivets: These rivets have a split tail that expands when hammered, creating a second head. They are often used for securing thin materials like sheet metal.
Drive Rivets: These rivets have a short, tapered shank that is driven into a pre-drilled hole.
Self-Piercing Rivets: These rivets pierce their own holes, eliminating the need for pre-drilling, commonly used in automotive assembly.
Rivet Type | Description | Applications |
Blind Rivet | Single-side installation | Sheet metal, electronics |
Solid Rivet | High strength | Structural steel, heavy machinery |
Tubular Rivet | Lightweight, easy to deform | Light assemblies, fabrics |
Split Rivet | Securing thin materials | Leather, signage |
Drive Rivet | Short tapered shank | Soft materials, hobby projects |
Self-Piercing Rivet | Pierces own hole | Automotive assembly, appliances |
Blind rivets are installed using a special tool called a rivet gun. The rivet gun inserts a mandrel through the rivet and pulls it tight, deforming the tail end and creating a second head. Once the joint is secure, the mandrel breaks off, leaving a flush finish.
Blind rivets are often used in applications where access to only one side of the joint is possible. They are particularly useful in sheet metal work, electronics, and other assemblies where traditional rivets would be difficult or impossible to install. Sheet Metal Fabrication processes often leverage blind rivets.
Rivets are made from a variety of different materials, including aluminum, steel, stainless steel, copper, brass, and various alloys. The choice of rivet material depends on the specific application requirements, such as strength, corrosion resistance, and conductivity. Aluminum rivets are lightweight and corrosion-resistant, while stainless steel rivets offer excellent strength and durability. Materials used for rivets must be carefully chosen for optimal results.
Stainless steel is often chosen for applications requiring high strength and corrosion resistance, particularly in harsh environments like marine or chemical processing. Aluminum rivets are preferred for their lightweight properties in the aerospace industry.
Solid rivets are known for their exceptional strength and are used in structural applications where high load-bearing capacity is essential. They are commonly found in bridges, buildings, and heavy machinery. Solid rivets require access to both sides of the joint for installation, as the tail end must be hammered or pressed to form the second head.
Solid rivets provide a permanent, tamper-proof joint that can withstand extreme forces. Their robustness makes them ideal for critical applications where failure could have catastrophic consequences.
Tubular rivets are similar to solid rivets but have a hollow shaft, making them lighter and easier to deform. Tubular rivets are popular for applications where high strength isn’t critical, such as securing lightweight materials or decorative elements. They are often used in clothing, leather goods, and electronics.
Tubular rivets are also commonly used in semi-structural applications where weight reduction is important. Their hollow shaft reduces the overall weight of the assembly without significantly compromising its strength.
Self-piercing rivets are a specialized type of rivet that pierce their own holes, eliminating the need for pre-drilling. This significantly speeds up the assembly process and reduces manufacturing costs. Self-piercing rivets are often used in the automotive industry for joining sheet metal components.
Self-piercing rivets offer a strong and reliable joint, comparable to traditional rivets, while simplifying the assembly process. Their use is particularly beneficial in high-volume production environments.
Selecting the appropriate rivet type depends on several factors, including the materials being joined, the strength requirements of the joint, the accessibility for installation, and the overall cost considerations. Consulting with a CNC Machining expert can help you determine the best rivet for your specific application.
Consider the environment the rivet will be exposed to. If corrosion is a concern, stainless steel rivets are the best choice. For lightweight applications, aluminum rivets might be sufficient.
The rivet industry continues to evolve, with ongoing research and development focused on new materials, improved installation methods, and specialized rivet designs. Innovations like friction stir riveting and self-piercing rivets are changing the landscape of fastening technology. Rapid Prototyping plays a crucial role in the advancement of rivet technology.
Expect to see advancements in rivet materials that offer even greater strength and corrosion resistance. New installation techniques will likely further automate the process, improving efficiency and reducing production time.
What is the difference between a rivet and a screw? A rivet is a permanent fastener, while a screw can be removed and reused.
Can rivets be used on plastic? Yes, special types of rivets are designed for use with plastics.
How do I remove a rivet? Rivets are designed to be permanent. Removal usually involves drilling out the rivet head.
What is the strongest type of rivet? Solid rivets are generally considered the strongest type.
What is a blind rivet used for? Blind rivets are used when you only have access to one side of the material.
Are rivets waterproof? Certain materials, like stainless steel, offer excellent corrosion resistance and can be considered for waterproof applications.
Rivets are permanent mechanical fasteners ideal for a variety of applications.
Different rivet types exist, each suited to specific needs and materials.
Material selection is crucial, considering factors like strength and corrosion resistance.
Blind rivets are excellent for single-sided access applications.
Solid rivets offer superior strength for structural projects.
Self-piercing rivets streamline the assembly process.
Consulting experts can optimize your rivet selection process.
Get the latest trends and facts about CNC fabrication from our blog.
Shenzhen Runkey Precision Technology Co. Ltd, a subsidiary of the Tensun Group, is your trusted one-stop solution for custom manufacturing from prototyping to production.Transforming your idea into reality with digital manufacturing resources,streamlined processes, expert guidance,accelerated timelines, and uncompromising quality.
©2024. CNC Fabrication All Rights Reserved.