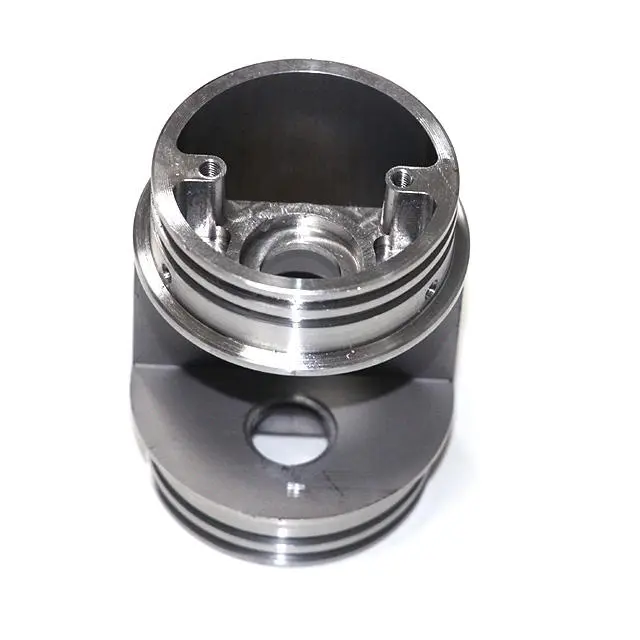
- +8615586668226
- [email protected]
- No. 30, Hongbang Industrial Park, Shenzhen
An end mill is a type of milling tool used in CNC milling applications to shape and cut various materials. Unlike a drill bit, which only cuts axially, an end mill can cut both axially and laterally. As a CNC fabrication service provider, we understand that end mills are essential tools in the milling process, and the right choice can significantly affect the quality, efficiency, and cost-effectiveness of your project.
End mills are crucial because they offer versatility and precision. For example, our plant utilizes various end mills to produce parts for industries such as aerospace, automotive, and medical devices. Mills are used in milling machines to perform a wide range of milling operations, from simple slotting to complex contouring. The specific type of end mill you choose will depend on factors like the material you are cutting, the desired surface finish, and the complexity of the part. Understanding these factors helps us optimize our processes and deliver high-quality products to our clients.
The number of flutes on an end mill significantly influences its performance and application. Flutes are the helical grooves that run along the cutting edge of the mill. Each flute acts as a cutting surface, and the number of flutes determines how the end mill interacts with the material being cut.
2 flute end mills are common in our CNC machining operations. These mills are used for general milling applications where chip evacuation is critical. For example, when working with aluminum or other soft materials, fewer flutes are best because they provide more space for chip removal, preventing clogging and overheating. On the other hand, end mills with more flutes are preferred for harder materials like steel, as they provide a smoother surface finish and distribute the cutting load more evenly. In our experience, using four or more flute end mills on steel can significantly improve tool life and surface quality.
End mill shapes vary widely, each designed for specific applications. Understanding these shapes is crucial for selecting the right tool for your project.
End mill coatings play a critical role in extending tool life and improving cutting performance. Coatings provide a protective layer that reduces friction, enhances heat resistance, and increases wear resistance.
For instance, titanium nitride (TiN) is a popular coating that adds a hard, smooth surface to the end mill. This coating is particularly effective in reducing wear and improving chip flow. In our operations, TiN-coated end mills are used extensively when machining abrasive materials or when high precision is required. Another example is aluminum titanium nitride (AlTiN), which offers superior heat resistance, making it ideal for high-speed machining. Using coated end mills not only improves the quality of the finished product but also reduces downtime and tool replacement costs.
Choosing between carbide and high-speed steel (HSS) end mills depends on the specific application and material being machined. Each material has its advantages and ideal use cases.
Carbide end mills are made from a composite material consisting of tungsten carbide and cobalt. They are significantly harder and more durable than high-speed steel end mills, making them ideal for cutting tough materials like stainless steel, titanium, and hardened steel. At our plant, we use solid carbide end mill for demanding applications where tool life and precision are critical. On the other hand, HSS end mills are less expensive and more forgiving when it comes to minor misalignments or vibrations. We often recommend HSS end mills for softer materials or less demanding applications where cost is a primary concern. HSS end mills are generally more affordable than carbide end mills.
Selecting the right end mill for your CNC machining project is crucial for achieving the desired results. Several factors should be considered when making this decision.
Firstly, identify the material you will be machining. Different materials require different end mill types. For soft materials like aluminum, 2 flute end mills with ample chip clearance are suitable. For harder materials like steel, carbide end mills with four or more flutes are recommended. Secondly, consider the specific milling operations you will be performing. For example, if you are creating complex 3D shapes, a ball nose end mill would be ideal. For general-purpose tasks like slotting or profiling, square end mills are appropriate. In our facility, we provide detailed consultations to help clients choose the right end mill for their specific needs, ensuring optimal results.
Square end mills are characterized by their flat cutting end, making them suitable for creating flat surfaces, slots, and pockets. They are a staple in many CNC machining operations.
Square end mills are used in a wide range of applications, from roughing out large amounts of material to finishing operations that require precision. For instance, when creating parts for the automotive industry, square end mills are used to machine flat surfaces and create precise slots for component assembly. In our experience, square end mills offer a balance of versatility and performance, making them a go-to choice for many general milling tasks. CNC machining involves using square end mills to cut and shape various materials.
Roughing end mills, also known as hog mills, are designed for removing large amounts of material quickly and efficiently. They feature a serrated cutting edge that breaks chips into smaller pieces, reducing cutting forces and heat generation.
We utilize roughing end mills in our initial machining stages to quickly remove excess material before moving on to finishing operations. This approach significantly reduces machining time and increases productivity. For example, when producing large components for industrial equipment, roughing end mills are used to quickly shape the raw material, leaving a small amount for the finishing pass. This not only speeds up the process but also extends the life of our finishing end mills. Roughing end mills are essential for quickly removing material.
Ball nose end mills are essential tools for creating complex, curved surfaces. They feature a hemispherical cutting end that allows for smooth, contoured cuts.
Ball nose end mills are commonly used in mold making, die sinking, and creating 3D profiles. For instance, in the medical devices industry, ball nose end mills are used to produce intricate parts with smooth, organic shapes. We also use them to create prototypes and custom parts that require precise contouring. The ability of ball nose end mills to produce smooth, curved surfaces makes them invaluable in applications where aesthetics and functionality are equally important. Using CNC milling with ball nose end mills allows for intricate 3D shapes.
Corner radius end mills feature a slight radius at the corner of the cutting edge. This design reduces the risk of chipping and extends tool life, making them suitable for a variety of milling applications.
In our experience, corner radius end mills are particularly beneficial when machining materials that are prone to chipping, such as hardened steels or composites. The rounded corner distributes cutting forces more evenly, reducing stress on the tool and the workpiece. We use corner radius end mills in applications where edge integrity is crucial, such as in the aerospace and defense industries. By reducing the risk of damage to the end mill and the workpiece, corner radius end mills help us maintain high-quality standards and reduce scrap rates. These mills are used to prevent chipping and extend tool life.
End Mill Type | Material | Application | Flutes | Coating |
---|---|---|---|---|
Square End Mill | Aluminum | Slotting, Profiling | 2 | Uncoated |
Ball Nose End Mill | Stainless Steel | Contouring, 3D Profiling | 4 | AlTiN |
Corner Radius End Mill | Hardened Steel | Edge Finishing, Reducing Chipping | 4 | TiN |
Roughing End Mill | Titanium | Rapid Material Removal | 3 | TiAlN |
High-Speed Steel End Mill | Plastic | General Milling, Cost-Effective | 2 | Uncoated |
Carbide End Mill | Composite | High Precision, Durability | 6 | Diamond-like |
Tapered End Mill | Wood | Engraving, Detailing | 2 | Uncoated |
Drill Mill | Various | Drilling and Milling in a Single Operation | 2 | TiCN |
What is the difference between an end mill and a drill bit?
An end mill is designed to cut both axially and laterally, making it suitable for milling operations such as slotting, profiling, and contouring. A drill bit, on the other hand, is designed to cut only axially, making it ideal for creating holes. End mills provide versatility in cutting directions, unlike drill bits.
How do I choose the right number of flutes for my end mill?
The number of flutes depends on the material and the specific application. For soft materials, fewer flutes (2-3) are preferred for better chip evacuation. For hard materials, more flutes (4 or more) provide a smoother surface finish and better tool life.
What are the benefits of using coated end mills?
Coated end mills offer several benefits, including reduced friction, increased heat resistance, and improved wear resistance. Coatings like TiN and AlTiN can significantly extend tool life and enhance cutting performance, especially in demanding applications.
When should I use a carbide end mill instead of a high-speed steel end mill?
Carbide end mills are ideal for cutting hard materials like stainless steel and titanium due to their superior hardness and durability. High-speed steel end mills are more cost-effective and suitable for softer materials or less demanding applications. Carbide end mills provide longer tool life compared to HSS end mills.
What is the purpose of a corner radius on an end mill?
A corner radius helps reduce the risk of chipping and extends tool life by distributing cutting forces more evenly. Corner radius end mills are particularly useful when machining materials that are prone to chipping or when edge integrity is crucial.
How does feed rate affect end mill performance?
Feed rate is the speed at which the end mill moves through the material. The correct feed rate is crucial for achieving optimal tool life and surface finish. Too high a feed rate can cause tool breakage, while too low a feed rate can lead to rubbing and excessive heat generation.
For more detailed information or to discuss your specific project needs, please contact us. Our experienced team is ready to assist you with all your CNC machining requirements, ensuring you get the best results from your end mill selection.
Get the latest trends and facts about CNC fabrication from our blog.
Shenzhen Runkey Precision Technology Co. Ltd, a subsidiary of the Tensun Group, is your trusted one-stop solution for custom manufacturing from prototyping to production.Transforming your idea into reality with digital manufacturing resources,streamlined processes, expert guidance,accelerated timelines, and uncompromising quality.
©2024. CNC Fabrication All Rights Reserved.