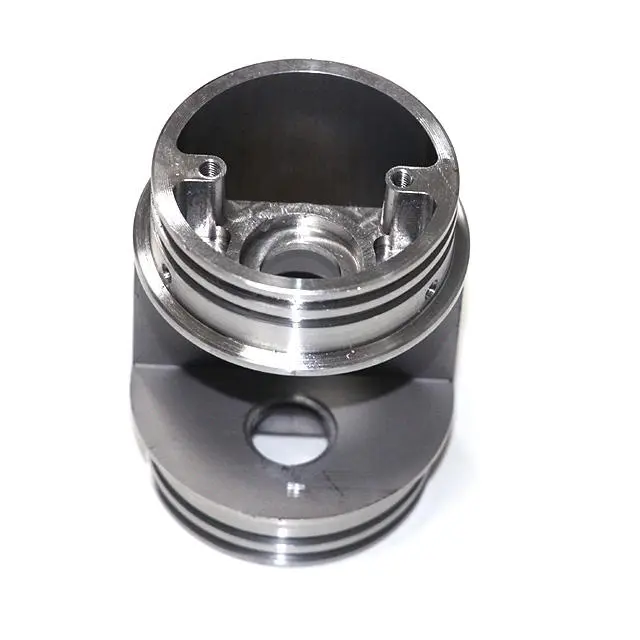
- +8615586668226
- [email protected]
- No. 30, Hongbang Industrial Park, Shenzhen
ABS plastic, short for acrylonitrile butadiene styrene, is a type of thermoplastic polymer that’s widely used in manufacturing due to its unique combination of properties. It’s not just any plastic, it is an engineering plastic, a robust material formed by polymerizing styrene and acrylonitrile in the presence of polybutadiene. The result? A material that is strong and durable, offering good impact strength and impact resistance that other materials simply cannot match. We can’t stress enough how widely abs plastics are used!
The significance of ABS plastic lies in its versatility. It’s not brittle like some other plastic materials; instead, it strikes a balance between stiffness and flexibility. This means it can withstand machine work, injection molding processes, and other fabrication methods without easily cracking or breaking. This versatility opens up a world of possibilities for designers and engineers to create a wide range of complex and durable products. From small electronic components to large automotive parts, ABS has proven itself.
Yes, ABS plastic is indeed a thermoplastic. Understanding this is crucial because it defines how the material behaves when heated. Thermoplastics, unlike thermosets, can be repeatedly melted and reshaped without undergoing a change in their chemical properties. This means that ABS scrap from injection molding or fabrication can be recycled and reused, making it an environmentally conscious material choice.
The thermoplastic nature of ABS makes it ideal for processes like injection molding, extrusion, and even 3D printing. This ability to be injection molded allows for mass production of complex ABS parts with consistent quality and precision. When heated, it becomes pliable and can be shaped into the desired form; when cooled, it solidifies, retaining the new shape. This recyclability and ease of forming makes it a favorite of manufacturers, who frequently use injection molded and extruded abs polymers to create an endless amount of items.
Several key properties of ABS contribute to its wide acceptance in diverse fields. One of the most notable is its impact strength. Unlike other plastic materials, ABS offers exceptional impact resistance, meaning it can withstand significant force without breaking or fracturing. This makes it particularly valuable in products that are expected to undergo a lot of wear and tear. ABS also displays good electrical insulating properties, making it suitable for electrical components and enclosures.
ABS offers high tensile strength, meaning it can withstand a significant amount of pulling force before breaking. It’s also relatively hard and rigid, which is useful for parts that need to maintain their shape under pressure. Furthermore, ABS plastic boasts chemical resistance, meaning it’s not easily damaged by various chemicals. While not as chemically resistant as some specialty plastics, its chemical resistance is more than sufficient for a wide range of applications. The combination of these physical properties, mechanical properties, and material properties contributes to the durability of this popular plastic.
When we compare ABS plastic with other plastic materials, it’s clear where it stands out. For example, while acrylic offers good clarity and weather resistance, it lacks the impact resistance of ABS. In comparison to polystyrene, ABS has superior impact strength and durability, although polystyrene is known for its lower cost. Even when stacked up against acrylic sheet it lacks the same high impact-resistance. ABS essentially offers a great middle ground, balancing toughness, impact resistance, and ease of processing.
Compared to more exotic engineering plastics, ABS is often more cost-effective while still offering a robust set of performance characteristics. This makes it an ideal choice for many applications where extreme performance is not necessary. It bridges the gap between cost and performance, making it an excellent choice when you don’t need the properties of high performance plastics. That’s why it’s such a popular plastic choice. It is readily available, and if you look in the correct category on amazon you are likely to find abs plastic sheet ready for you to use abs on your next project.
The applications of ABS are vast and varied, showcasing its versatility. In the automotive industry, ABS is used to create instrument panels, door panels, and even exterior parts, due to its impact strength and resistance to uv degradation. In the electronics sector, you’ll find it used in computer keyboard housings, keyboard keycaps, and other enclosures, leveraging its electrical insulating properties and durability.
Consumer goods benefit immensely from ABS as well. Lego bricks are famously made from ABS due to the material’s ability to withstand repetitive use. Other products made from it range from kitchen utensils and protective headgear, to luggage and small appliances. In recent years we’ve seen it used in 3d printing as well and is a favorite of people using 3d printers. Across various industries, we can clearly see abs is one of the most useful and frequently used plastic items. You can make plastic with it and it comes in an abs sheet ready to be used. ABS plastics are used for all sorts of reasons.
ABS plastic sheet is indeed a common form in which this material is used, providing a versatile platform for many fabrication methods. Sheets of abs allow for easy cutting, shaping, and forming, making it ideal for prototyping and mass-production. If you’re trying to make abs parts, having them arrive in sheet form means you can begin fabrication right away. Whether you need a black abs plastic sheet 12 x 12 or a more custom size, ABS sheet is an easy place to start.
ABS plastic sheet is useful when working with thermoplastic materials because you can manipulate it by heating it. The material can be easily shaped using a heat gun. This is also a major factor in the ease of fabrication. Black plastic sheet is a popular request and the black abs plastic sheet is a great material for creating many plastic panels. The fact it comes in sheets means it can be easily manipulated and it is readily available in the category on amazon. You’ll likely find everything you need, even if you are looking for something specific like inch thick 8 or x 16, or even something like x 0.06.
Yes, ABS plastic parts can be easily machined and fabricated, adding to its versatility. Its toughness makes it possible to be easily machined with standard tools, while its thermoplastic nature allows it to be shaped through various methods. From CNC machining, to laser cutting, the applications are endless.
ABS plastic is a great material for injection molding which makes it well-suited for mass production of consistent and precise parts. ABS can also be shaped through techniques like thermoforming and extrusion, further adding to the flexibility in its fabrication. These capabilities mean that abs provides options for a whole range of projects, whether it’s a quick prototype or large-scale manufacturing runs. With the correct machine and skill, you’ll be making a wide range of abs plastic parts easily.
While ABS offers a multitude of benefits, it does have a few disadvantages. One of the primary drawbacks is its relatively low melting point. This means that abs plastic is not ideal for applications that require high heat resistance. Additionally, ABS is susceptible to degradation when exposed to UV light for prolonged periods which is why many abs parts are coated or painted.
Despite these limitations, the benefits of using ABS plastic often outweigh the minor inconveniences. For applications where high heat is a concern, other plastic materials with higher heat tolerances can be considered. For items exposed to sunlight, ABS parts can be treated with UV protectant coatings to extend their lifespan. It’s all about understanding the material properties and matching the right material to the right job.
As CNC, we are experts in bringing your ABS ideas to life. CNC machining allows us to create precision parts with tight tolerances from ABS. Our state-of-the-art equipment and highly skilled team can manufacture a wide range of abs parts, whether you need a few prototypes or a large production run. We can manipulate a block of material into a perfect replica of what you need.
Our processes ensure consistent part quality, so you can rely on our services to deliver outstanding components. CNC Fabrication utilizes advanced techniques to make sure every part meets your exact specifications. From intricate injection molding to large scale production of products, we can help with anything. We bring our experience in plastics industry to provide efficient and cost effective solutions. This means your abs plastic parts will be of the highest quality and be completed quickly. When you need any kind of plastic sheeting, reach out to us and we can get you started right away. We have the knowledge of material properties to make sure you get what you need every time.
ABS is such a strong and durable option due to the specific blend of its properties. Its impact strength and high durability make it suitable for an extremely wide range of applications. The fact it is able to withstand high levels of wear and tear, and can be easily shaped using various methods, are all contributing factors to it’s popularity. The fact that it can also be easily recycled is a major bonus too. The combination of being strong and durable makes it a favorite for people in the plastics industry.
Whether it’s for the intricate details of computer keyboard components or the robust exterior of a vehicle, ABS stands out. Its good impact strength, chemical resistance, and the ability to be used in diverse manufacturing processes make it an ideal solution. ABS is commonly used in products, and many of these are used every day by people around the globe. The fact that abs comes in many forms including sheet stock, pellets, and more, makes it one of the most useful plastic materials available today. It is clear abs is one of the most popular materials on the market today.
How can ABS plastic be used in 3D printing?
ABS plastic is a popular material for 3d printing due to its durability and impact resistance. You will find 3d printers that have been specifically made to utilize abs as their print material. It can be easily extruded in filament form and used to print a wide range of 3d printed objects.
Is ABS plastic suitable for outdoor use?
ABS plastic is not the best choice for long term outdoor use. Prolonged exposure to UV radiation can cause it to degrade. However, the degradation process can be slowed with UV protectant coatings and proper maintenance.
Can ABS plastic be painted and finished?
Yes, ABS plastic is very suitable for painting and finishing. The surfaces can be easily prepared by sanding and priming. This ensures that any desired color, texture or look can be easily applied to any abs parts.
What products are commonly made from ABS?
Products made from abs plastic include many of the things you use every day. You’ll find things like lego bricks, kitchen utensils, computer keyboard components, and instrument panels in automobiles. In addition, many items are created with abs plastic parts which are not visible to the naked eye, further increasing the scope of its use. ABS is one of the most useful and common materials across all sectors.
What is the difference between ABS and acrylic plastic?
ABS is known for its durability and impact resistance, making it suitable for load bearing applications. Acrylic is valued for its optical clarity and weather resistance and is often used in windows and other see-through applications. They are both useful plastics, but they are useful in completely different ways.
What is ABS plastic made from?
ABS is made out of abs, a type of thermoplastic polymer. It is created by polymerizing styrene and acrylonitrile in the presence of polybutadiene. This process gives it its unique set of properties including it’s high impact strength, and high durability making it such a useful material properties. ABS is frequently cited as a common engineering plastic.
Let us help you bring your ABS project to life. Contact us today to learn more about our CNC machining and fabrication capabilities, and how we can help you create a strong and durable solution.
Machining Services
Fabrication Services
CNC Solutions
Precision Machining
Rapid Prototyping
On Demand Manufacturing
Get the latest trends and facts about CNC fabrication from our blog.
Shenzhen Runkey Precision Technology Co. Ltd, a subsidiary of the Tensun Group, is your trusted one-stop solution for custom manufacturing from prototyping to production.Transforming your idea into reality with digital manufacturing resources,streamlined processes, expert guidance,accelerated timelines, and uncompromising quality.
©2024. CNC Fabrication All Rights Reserved.