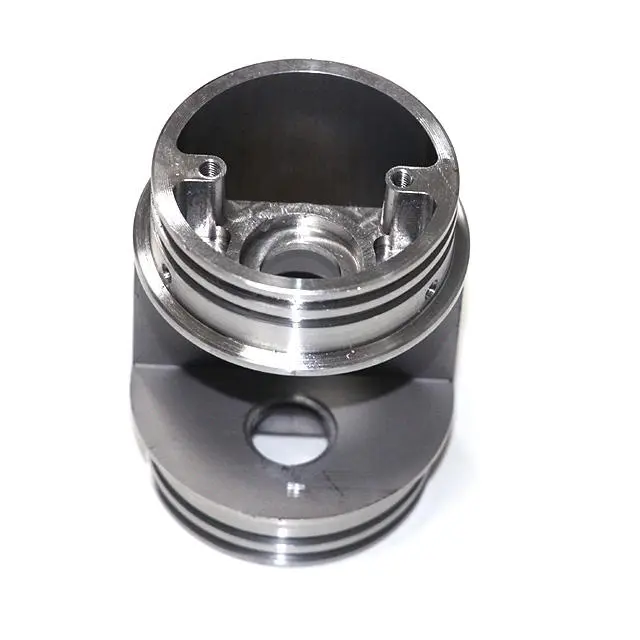
- +8615586668226
- [email protected]
- No. 30, Hongbang Industrial Park, Shenzhen
Black oxide finish, also known as black oxide coating, is a conversion coating for ferrous materials like steel and stainless steel. It’s a chemical surface treatment that converts the surface of the metal part into magnetite (Fe<sub>3</sub>O<sub>4</sub>), creating a black finish. Unlike paints or platings, the black oxide layer is integral to the metal, resulting in a durable and dimensionally stable coating.
This finishing process doesn’t significantly alter the dimensions of the machined part, making it ideal for precision components. The black oxide finish offers enhanced corrosion resistance, lubricity, and a sleek matte black appearance, making it a preferred choice in various industries like CNC Machining.
There are several types of black oxide finishes, each suited for specific applications. The most common are:
Hot Black Oxide: This hot black oxide finish involves immersing the machined part in a hot alkaline salt bath. It produces the most durable and corrosion-resistant black oxide surface.
Mid-Temperature Black Oxide: This process uses lower temperatures and is faster than the hot process. It’s a good balance between cost and performance.
Cold Black Oxide: Cold black oxide is the simplest and least expensive method, applied at room temperature. It offers less corrosion resistance than hot or mid-temperature processes.
Understanding the types of black oxide available helps in selecting the optimal type of black oxide finish for the specific requirements of your precision machined projects.
Black oxide finish for precision machined parts offers several advantages:
Enhanced Corrosion Resistance: The black oxide finish process increases the corrosion resistance of the black oxide significantly, protecting the metal part from environmental factors.
Minimal Dimensional Change: The coating process adds a very thin layer, preserving the precision of the machined part.
Improved Lubricity: Black oxide provides a slightly porous surface, which can hold lubricants, improving performance and reducing wear.
Aesthetically Pleasing: The black appearance provides a sleek and professional look, especially valuable for visible components.
These benefits make the black oxide stainless steel finish a sought-after choice in industries requiring both performance and aesthetics.
The applications of black oxide finish are vast and varied. It’s commonly used in:
Firearms: For corrosion resistance and a non-reflective surface.
Automotive: In engine components, fasteners, and other parts requiring wear resistance.
Medical Devices: Providing biocompatibility and corrosion resistance for implants and instruments.
Tooling and Dies: Enhancing durability and reducing friction.
CNC Solutions: Improving the performance and appearance of cnc machining components.
The versatility of black oxide coating offers solutions for numerous industries and applications.
The black oxide coating process typically involves the following steps:
Cleaning: Thoroughly clean the machined part to remove any oils, dirt, or contaminants.
Rinsing: Rinse the part with water to remove cleaning residue.
Black Oxide Bath: Immerse the part in the appropriate black oxide solution, depending on the desired black oxide finish.
Rinsing: Rinse the part again to remove excess black oxide.
Sealant (Optional): Apply a sealant, such as oil or wax, to further enhance corrosion resistance.
Understanding the process of applying black oxide ensures a successful and high-quality finish.
Pros | Cons |
Increased corrosion resistance | Not as corrosion resistant as other coatings like chrome |
Minimal dimensional change | Can rub off with excessive abrasion |
Improved lubricity | Not suitable for all metals |
Enhanced appearance (black color) | Can be difficult to apply evenly |
Cost-effective | Can be susceptible to chipping if not properly sealed |
Understanding the pros and cons of black oxide will help determine its suitability for your specific machined part.
Several tests can evaluate the quality of a black oxide finish:
Salt Spray Test: Assesses corrosion resistance.
Adhesion Test: Measures the bond strength of the coating.
Thickness Measurement: Verifies the coating thickness.
These testing options for black oxide ensure the finish meets the required specifications. For more in-depth information on surface finishing, you can visit Surface Finishing.
Common applications for black oxide include:
Fasteners (Assembly)
Firearms components
Automotive parts (e.g., gears, shafts)
Medical instruments
Materials for tooling and dies
Black oxide finish stands out compared to other finishes due to its unique combination of corrosion resistance, minimal dimensional impact, and cost-effectiveness. While finishes like chrome offer superior corrosion resistance, they can significantly alter the dimensions of a part. Black oxide finish is one of the best options when maintaining tight tolerances is critical.
Black oxide finish is generally a cost-effective finishing process. Factors influencing cost include the type of black oxide process (hot, mid-temperature, or cold), the size and complexity of the parts, and the volume of production.
What is the difference between hot and cold black oxide? Hot black oxide offers superior corrosion resistance and durability compared to cold black oxide.
Can black oxide be applied to stainless steel? Yes, black oxide can be applied to stainless steel, providing enhanced corrosion resistance and a desirable aesthetic finish.
How long does a black oxide finish last? The lifespan of a black oxide finish depends on the environment and usage, but it can typically last for several years with proper care.
Is black oxide finish food safe? While black oxide itself is generally considered non-toxic, it’s essential to consult with a finishing expert to determine its suitability for specific food contact applications.
Black oxide finish is a versatile coating suitable for a wide range of precision machined parts.
Choosing the right type of black oxide finish (hot, mid-temperature, or cold) depends on the specific application requirements.
Proper surface preparation is crucial for a successful black oxide coating.
Testing the finish ensures it meets the necessary quality and performance standards.
By understanding the properties and application process of black oxide finish, you can enhance the durability, performance, and aesthetics of your precision machined parts. Contact us today at Fabrication Services to discuss your specific project needs.
Get the latest trends and facts about CNC fabrication from our blog.
Shenzhen Runkey Precision Technology Co. Ltd, a subsidiary of the Tensun Group, is your trusted one-stop solution for custom manufacturing from prototyping to production.Transforming your idea into reality with digital manufacturing resources,streamlined processes, expert guidance,accelerated timelines, and uncompromising quality.
©2024. CNC Fabrication All Rights Reserved.