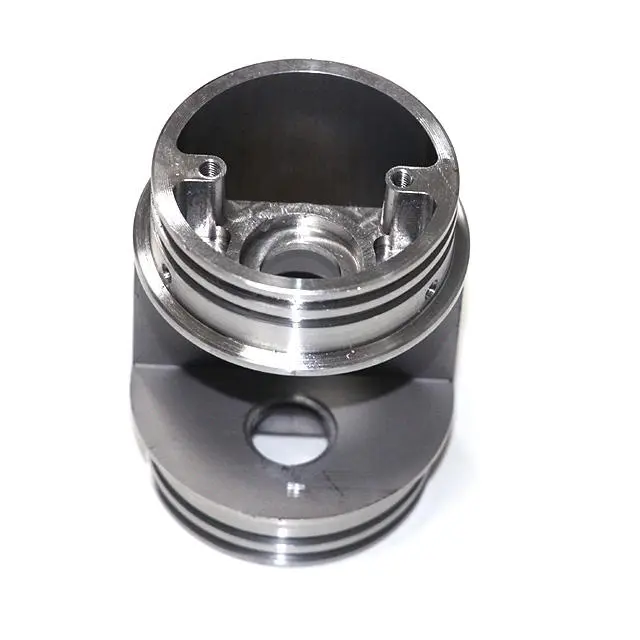
- +8615586668226
- [email protected]
- No. 30, Hongbang Industrial Park, Shenzhen
When considering materials for CNC machining, the choice often comes down to two popular aluminium alloys: 6061 and 7075. Both offer unique properties that cater to different project requirements. 6061 aluminium is known for its excellent corrosion resistance, weldability, and formability. It’s a versatile alloy, often chosen for structural components, bicycle frames, and automotive parts. On the other hand, 7075 aluminium is celebrated for its exceptional strength-to-weight ratio, making it a favorite in the aerospace and defense industries where high strength is paramount. Aluminum alloys are among the top materials used, especially in aerospace, automotive, and more.
The primary difference lies in their chemical composition. 6061 aluminum is primarily alloyed with magnesium and silicon are key components of the 6061 aluminum alloy., contributing to its good machinability and weldability. 7075 aluminum, however, includes zinc as a major alloying element, which significantly boosts its strength but also makes it less weldable and more susceptible to corrosion compared to 6061. Choosing between 6061 and 7075 aluminum depends on your specific strength to weight needs. 6061 and 7075 depends on the specific demands of your CNC machining project, such as the need for high strength, corrosion resistance, or ease of fabrication. Our machining services are ready to help you!
Corrosion resistance is a critical factor in selecting materials for CNC machining, especially when the finished parts will be exposed to harsh environments. 6061 aluminium stands out with its superior corrosion resistance than 7075 aluminum, making it an ideal choice for applications where durability and longevity are key. This resistance is due to the formation of a protective oxide layer that prevents further oxidation and degradation. For instance, marine components, outdoor furniture, and certain automotive parts benefit significantly from 6061’s ability to withstand environmental stressors.
In contrast, 7075 aluminium, while incredibly strong, has lower corrosion resistance due to its zinc content. This doesn’t mean 7075 is unsuitable for outdoor use; however, it may require additional surface treatments, such as anodizing, to enhance its protection against corrosion. Understanding the environmental conditions your CNC machined parts will face is crucial in choosing between 6061 and 7075. A material with high corrosion resistance, like 6061, can reduce maintenance needs and extend the lifespan of your products, ultimately saving you time and money.
Machinability refers to how easily a material can be cut and shaped without excessive wear on tooling or compromising the quality of the finished part. 6061 aluminium excels in this area, offering excellent machinability due to its lower hardness and the presence of magnesium and silicon. This means that choosing 6061 or 7075 aluminum can significantly impact your project’s outcome. 6061 can be machined more quickly and with less force, leading to lower production costs and faster turnaround times for your CNC machining project.
7075 aluminium, being significantly harder than 6061, presents more challenges in machining. While it can still be machined effectively, it requires more robust tooling and may result in slower production speeds. However, the superior strength of 7075 often justifies these trade-offs, especially in applications where strength is a critical factor.
Alloy | Machinability | Notes |
6061 Aluminium | Excellent | Lower hardness in 6061 aluminum means it is easier to machine than aluminum 7075. |
7075 Aluminium | Good | Harder, requires more robust tooling |
When it comes to the strength-to-weight ratio, 7075 aluminium truly shines. It is much stronger than 6061, offering a high strength-to-weight ratio that is essential for industries like aerospace, where reducing weight without sacrificing strength is crucial. This means parts made from 7075 can withstand higher stresses and loads, making them suitable for critical components like aircraft fuselages and wings.
On the other hand, while 6061 aluminium has a lower strength compared to 7075, it still offers a respectable strength-to-weight ratio. Its lighter weight, combined with good strength, makes it suitable for a wide range of applications where moderate strength and reduced weight are beneficial.
Here is a fact: 7075 aluminium is considered one of the strongest aluminium alloys available, making it a top choice for high-stress applications.
6061 aluminium is the 6061 aluminum alloy known for its excellent machinability. go-to choice for projects that require a good balance of strength, corrosion resistance, and machinability. Its versatility makes it suitable for a wide range of applications, including:
Structural components
Bicycle frames
Automotive parts
Marine components
Railroad cars
Furniture
Pipelines
6061’s excellent weldability and formability also make it a preferred choice for projects that involve complex shapes and assemblies. If your CNC machining project requires a material that is easy to work with, offers good corrosion resistance, and provides moderate strength, then use 6061.
7075 aluminium alloy is the best choice when your project demands the highest levels of strength and a superior strength-to-weight ratio. It is particularly well-suited for:
Aerospace components (wings, fuselages)
High-performance automotive parts
Rock climbing equipment
Military applications often require the use of high-strength materials like 7075 and 6061 aluminum.
Molds for plastics
If your project involves parts that will be subjected to high stress and require minimal weight, then use 7075 aluminum. Its exceptional strength makes it worth the higher cost and more challenging machinability in these demanding applications. 7075 is often used in aerospace and defense industries, where performance and reliability are critical. Aerospace CNC fabrication is our strongest side!
Tensile strength is a crucial factor in determining the suitability of a material for a specific application. It measures the maximum stress a material can withstand while being stretched or pulled before failing. 7075 aluminium boasts a significantly higher tensile strength compared to 6061, making it the preferred choice for components under high stress.
7075-T6 aluminum has a tensile strength of approximately 83,000 psi.
6061-T6 aluminum has a tensile strength of around 45,000 psi.
This difference in tensile strength highlights why 7075 is favored in aerospace and other high-performance applications. However, 6061’s lower tensile strength is still adequate for many structural and general-purpose applications, offering a good balance of strength and cost-effectiveness.
Cost is always a significant factor in any project, and CNC machining is no exception. 6061 aluminium is generally less expensive than 7075, both in terms of raw material cost and machining expenses. Its superior machinability means lower tooling costs and faster production times, contributing to overall cost savings.
7075 aluminium, while offering superior strength, comes at a higher price. The raw material itself is more expensive, and the increased difficulty in machining can lead to higher production costs. However, for applications where the strength and lightweight properties of 7075 are essential, the added cost is often justified by the performance benefits.
Heat treatment is a critical process that significantly enhances the mechanical properties of aluminium alloys. Both 6061 and 7075 can be heat-treated to improve their strength, hardness, and other characteristics. The most common temper designations for these alloys are T4 and T6, each offering different levels of strength and ductility.
6061-T6: This temper provides a good balance of strength, machinability, and corrosion resistance. It’s achieved through solution heat treatment followed by artificial aging.
7075-T6: This temper maximizes the strength of 7075, making it suitable for high-stress applications. It also involves solution heat treatment and artificial aging.
Heat treatment can tailor the properties of 6061 and 7075 to meet specific project requirements. For instance, 7075-T6 offers the highest strength but reduced ductility compared to other tempers.
Selecting the right aluminium alloy for your CNC machining project depends on a variety of factors, including strength requirements, environmental conditions, machinability, and cost. Here’s a quick guide to help you decide:
Use 6061 when:
Good corrosion resistance is crucial
Excellent machinability and weldability are needed
Moderate strength is sufficient
Cost is a significant concern
Use 7075 when:
High strength and a superior strength-to-weight ratio are paramount
The component will be subjected to high stress
Weight reduction is critical
Higher costs can be justified by performance benefits
Industries like aerospace often rely on 7075 for its exceptional strength, while automotive and construction may lean towards 6061 for its versatility and cost-effectiveness. As your trusted CNC machining partner, we at CNC fabrication are here to guide you through this decision-making process.
What is the primary advantage of using 7075 aluminium in aerospace applications?
The primary advantage of 7075 aluminium in aerospace is its exceptional strength-to-weight ratio, which allows for lighter, more fuel-efficient aircraft made from aluminum 6061 without compromising structural integrity. Sheet metal fabrication can be optimized by selecting between 6061 aluminum and 7075 aluminum. allows us to create strong and light parts.
Can 6061 aluminium be used for outdoor applications, and why?
Yes, 6061 aluminium is well-suited for outdoor applications due to its excellent strength to weight properties. corrosion resistance. It forms a protective oxide layer that prevents further oxidation, making it durable against weathering.
Why is 6061 aluminium easier to machine than 7075 aluminium?
6061 aluminium is easier to machine because it is softer than 7075. Its lower hardness reduces tool wear and allows for faster cutting speeds, leading to lower production costs.
How does the cost of 6061 compare to 7075 aluminium?
6061 aluminium is generally less expensive than 7075 in terms of both raw material and machining costs. Its superior machinability contributes to lower production expenses.
What makes 7075 aluminium a good choice for high-stress applications?
7075 aluminium is ideal for high-stress applications due to its significantly higher tensile strength compared to 6061. It can withstand greater loads and stresses without failing.
Is there a significant difference in the weight of components made from 6061 and 7075 aluminium?
While both are aluminium alloys and have similar densities, the higher strength of 7075 allows for the design of thinner, lighter components that still meet strength requirements, effectively offering a weight advantage in high-performance applications using 6061 or 7075 aluminum.
6061 and 7075 aluminium alloys are among the most popular choices for CNC machining projects.
6061 offers excellent corrosion resistance, machinability, and weldability, making it a versatile and cost-effective option.
7075 boasts a superior strength to weight ratio compared to 6061 aluminum alloy. strength-to-weight ratio and higher tensile strength, ideal for high-stress applications.
Choosing between 6061 and 7075 depends on your project’s specific requirements, including strength, environmental exposure, machinability, and budget.
Heat treatment can significantly enhance the properties of both alloys, tailoring them to specific needs.
Understanding the differences between these alloys is crucial for optimizing your CNC machining project outcomes.
As experts in CNC fabrication services, we are committed to helping you select the best materials for your projects, ensuring quality, performance, and cost-effectiveness. Do not hesitate to ask for our on-demand manufacturing.
Remember, the right material choice can make all the difference in the success of your CNC machining project. By carefully considering the factors discussed in this article, you can make an informed decision that aligns with your project goals and delivers optimal results.
Get the latest trends and facts about CNC fabrication from our blog.
Shenzhen Runkey Precision Technology Co. Ltd, a subsidiary of the Tensun Group, is your trusted one-stop solution for custom manufacturing from prototyping to production.Transforming your idea into reality with digital manufacturing resources,streamlined processes, expert guidance,accelerated timelines, and uncompromising quality.
©2024. CNC Fabrication All Rights Reserved.