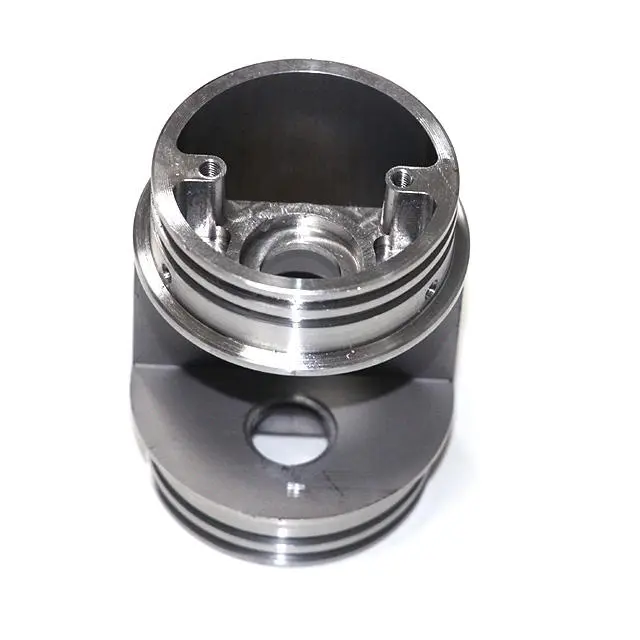
- +8615586668226
- [email protected]
- No. 30, Hongbang Industrial Park, Shenzhen
G50 is a powerful command in the realm of CNC machining, primarily used in lathe operations. It serves two primary functions: setting the coordinate system and establishing the maximum spindle speed. When G50 is executed, it informs the machine where the workpiece’s zero point is located, which is crucial for accurate machining. Secondly, it can be employed to clamp the spindle speed, preventing it from exceeding a specified RPM. This function is particularly valuable when using constant surface speed (G96) to protect both the tool and the workpiece.
Our extensive experience at CNC-Fabrication.com with diverse projects across industries such as Aerospace, Automotive, and Medical Devices underscores the importance of precise coordinate system setting. For instance, in aerospace components, even a slight deviation can lead to significant issues in the final product. The G50 command ensures that the machine accurately interprets the dimensions specified in the CNC program, resulting in parts that meet the stringent tolerances required by these high-precision industries. We offer comprehensive machining services to meet the precise needs of our clients. In many CNC controls, such as Fanuc, the G50 command can also be used to define the relationship between the machine’s absolute zero and the program zero, adding a layer of flexibility for the programmer.
Program zero is the reference point from which all coordinate positions in a CNC program are measured. G50 is often used to set the program zero on a lathe machine. For example, the command G50 X0 Z0 would set the current position of the tool as the origin (X0, Z0). This effectively tells the machine that the current tool position is the program zero, aligning the machine’s coordinate system with the workpiece.
Zero return, on the other hand, refers to the machine’s ability to return to its home position, also known as the reference point or machine home. This is typically accomplished using the G28 command, such as G28 U0 W0 for incremental movement. While G50 does not directly initiate a zero return, it can influence it indirectly. By setting the program zero with G50, you define the starting point for all subsequent machine movements, including the zero return. A clear understanding of these concepts is vital for industries like Electronics and Industrial Equipment, where precision is paramount. Our expertise extends to crafting detailed CNC solutions, ensuring accuracy and efficiency.
The G50 command is fundamental in defining the work coordinate system within CNC programming, especially on lathe machines. By executing a G50 command, such as G50 X… Z…, the programmer establishes a new coordinate system based on the current position of the tool. This is known as setting the absolute zero point. The machine then uses this point as the reference for all subsequent movements and calculations within the program.
This ability to set the coordinate system is particularly useful in several scenarios:
Multiple Workpieces: When machining multiple workpieces with different zero points, G50 can be used to shift the coordinate system for each piece without modifying the entire program.
Tool Changes: After a tool change, G50 can be used to adjust the coordinate system to compensate for differences in tool length or diameter.
Complex Parts: For parts with intricate features or multiple setups, G50 allows for defining different coordinate systems for various sections of the part, simplifying programming and improving accuracy.
Feature | Benefit |
Multiple Workpieces | Simplified programming, increased efficiency |
Tool Changes | Improved accuracy, reduced setup time |
Complex Parts | Enhanced precision, streamlined process |
The image below illustrates the concept of setting a new coordinate system with G50:
One of the critical uses of G50 is to set a maximum spindle speed limit, often referred to as G50 speed clamp. This is achieved by using the command in the format G50 S…, where “S” specifies the maximum RPM. For instance, G50 S2000 would limit the spindle speed to 2000 RPM. This function is especially crucial when working with constant surface speed (G96), as it prevents the spindle from exceeding safe operating limits, particularly when the tool approaches the centerline of the workpiece.
Managing spindle speed is essential for:
Tool Life: Prevents excessive tool wear and breakage.
Workpiece Quality: Ensures a consistent surface finish.
Machine Safety: Protects the machine from damage due to overspeeding.
For industries such as Consumer Products and Robotics, controlling spindle speed is vital for maintaining product quality and consistency.
While both G50 and G96 relate to spindle control, they serve different purposes. G96 initiates constant surface speed (CSS) mode. In CSS mode, the machine automatically adjusts the spindle RPM based on the tool’s distance from the centerline to maintain a constant cutting speed.
G50, when used with the “S” parameter, sets the maximum spindle speed limit. This acts as a safety measure when G96 is active. Without a speed clamp, the RPM could theoretically increase infinitely as the tool approaches the centerline, potentially damaging the tool, workpiece, or machine. Thus the G50 command is a necessary part of programs that use G96. The use of these codes together is standard Fanuc code.
Here’s a table summarizing the differences:
Feature | G50 | G96 |
Primary Function | Sets coordinate system, limits spindle speed | Activates constant surface speed mode |
Spindle Control | Clamps maximum RPM | Adjusts RPM based on tool position |
Yes, depending on the specific CNC control and the machine configuration, G50 can be used to manage tool offsets. Traditionally, tool offsets are managed using dedicated commands like G43 for length compensation in mills and using T words for lathes (T0101). However, on some older machines or in specific programming scenarios, G50 can be employed to shift the coordinate system to compensate for tool length or diameter variations, similar to a geometry offset. This is often done in conjunction with wear offset.
For example, after a tool change, a G50 command can be used to adjust the X and Z coordinates based on the new tool’s dimensions. This effectively updates the machine’s understanding of the tool’s position relative to the workpiece. However, it is worth noting that this method is less common on modern CNC controls, which typically have more sophisticated tool management systems. For precision applications like those in Medical Devices and Telecommunications, accurate tool offset management is essential. We excel in providing precise fabrication services, especially in areas like sheet metal fabrication.
While the fundamental principles of G50 remain consistent, its implementation and specific functionalities can vary slightly depending on the CNC control manufacturer. Fanuc is one of the most widely used CNC control systems, and its handling of G50 is considered the standard by many machinists.
On standard Fanuc controls, G50 is commonly used for both setting the coordinate system and clamping the spindle speed. However, some variations exist. For example, on older Fanuc 6T controls, G92 was used instead of G50 for coordinate system setting, while on newer controls like Fanuc 10T or later, both G50 and G92 are used for different functions. Other manufacturers like Haas or Mazak might have slightly different interpretations or additional features associated with G50 or might use a completely different G code for those purposes.
It’s crucial for programmers to consult the specific programming manual for their machine and control to understand the exact behavior of G50 in their particular context. The manual will provide detailed information on the command’s syntax, parameters, and any manufacturer-specific nuances.
Several common mistakes can occur when using G50:
Incorrect Coordinate Setting: Using G50 with incorrect X or Z values can lead to the machine misinterpreting the workpiece’s position, resulting in inaccurate cuts or even crashes.
Solution: Double-check the coordinate values before executing the G50 command. Use a tool setting probe or manually measure the tool’s position to ensure accuracy.
Forgetting to Cancel G50: If G50 is used for scaling, it needs to be canceled with another G50 X1. G50 is modal, meaning it remains active until canceled or overridden. Forgetting to cancel a G50 offset can lead to unexpected machine movements in subsequent operations.
Solution: Always cancel G50 explicitly with G50 or by using another coordinate system setting command like G54.
Confusing G50 with G92: Although they may seem similar, they have a different use. G92 is an older command that was used on older Fanuc controls.
Solution: Always be aware of what command your control uses.
In multi-axis machining, where a machine can move and rotate in more than three axes, G50 can play a significant role in enhancing efficiency and simplifying programming. By allowing the programmer to define multiple work coordinate systems, G50 enables the machining of complex parts with multiple features or orientations without requiring complex calculations or transformations in the CNC program.
For example, consider a part that needs to be machined on different faces using a 4-axis or 5-axis machine. Instead of manually calculating the coordinate shifts and rotations for each face, the programmer can use G50 to define a separate work coordinate system for each face. This simplifies the programming process and reduces the risk of errors. The machine can then seamlessly transition between different coordinate systems using simple G50 commands. The use of G50 in multi-axis applications requires careful planning and a thorough understanding of the machine’s kinematics and the specific CNC control’s capabilities.
In modern CNC lathe operations, G50 is often integrated into advanced programming techniques to enhance automation, flexibility, and precision. Some of these techniques include:
Parametric Programming: G50 can be used in conjunction with variables and macros to create parametric programs that can be easily adapted to different part sizes or configurations. For instance, a program could use variables to define the program zero and then use G50 to set the coordinate system based on those variables. This allows the same program to be used for a family of parts with only minor parameter adjustments.
In-Process Probing: Modern CNC lathes are often equipped with probing systems that can measure the workpiece during the machining process. G50 can be used in conjunction with probing routines to automatically update the work coordinate system based on the measured data, compensating for any variations or inaccuracies in the workpiece setup.
Automated Tool Setting: G50 can be integrated into automated tool setting routines, where a tool touch probe is used to measure the length and diameter of each tool. The measured values are then automatically used to update the coordinate system via G50, eliminating the need for manual tool offset entries.
These advanced techniques, often employed in industries like Energy and Renewable Energy and Aerospace, leverage the power of G50 to achieve higher levels of automation, accuracy, and efficiency in CNC lathe operations. Rapid prototyping is one area where these techniques are particularly beneficial.
What is the primary function of the G50 command in CNC programming?
The G50 command is primarily used to set the work coordinate system and clamp the maximum spindle speed in CNC programming, especially on lathe machines.
How does G50 relate to G96 in CNC turning?
G96 activates constant surface speed (CSS) mode, while G50 is used to set the maximum spindle speed limit, which is crucial for safe operation in CSS mode. They are very often used together.
Can G50 be used to manage tool offsets?
Yes, depending on the CNC control and machine configuration, G50 can be used to manage tool offsets by shifting the coordinate system to compensate for tool variations, although this is less common on modern machines.
What is the difference between G50 and G28 in CNC programming?
G50 sets the work coordinate system and clamps spindle speed, while G28 is used for zero return, sending the machine to its home or reference position.
How does the use of G50 vary across different CNC controls?
While the basic function of G50 is similar, its specific implementation, syntax, and additional features can vary slightly between different CNC control manufacturers like Fanuc, Haas, or Mazak.
What are some common mistakes when using G50 and how can they be avoided?
Common mistakes include incorrect coordinate setting, forgetting to cancel G50, and confusing it with G92; these can be avoided by double-checking values, always canceling G50 when appropriate, and understanding the specific commands used by your control.
Here are the key takeaways from this comprehensive guide to G50 in CNC lathe programming:
G50 is a fundamental command used for setting the work coordinate system and clamping maximum spindle speed.
It plays a crucial role in defining the program zero and ensuring accurate machining.
G50 is essential for managing spindle speed, especially when using constant surface speed (G96).
While traditionally used for tool offset management, modern CNC controls often have dedicated commands for this purpose.
The specific implementation of G50 can vary slightly between different CNC control manufacturers.
Common mistakes can be avoided by carefully checking coordinate values, canceling G50 when appropriate, and understanding your specific control’s commands.
G50 can enhance efficiency in multi-axis machining by simplifying the management of multiple work coordinate systems.
Advanced techniques like parametric programming, in-process probing, and automated tool setting often integrate G50 to achieve higher levels of automation and precision.
Our team at CNC-Fabrication.com is ready to assist with your most complex projects, delivering the highest quality results. Contact us today to discuss your needs!
We pride ourselves on being a leading CNC machining provider, offering top-notch services for various industries. Our capabilities also include specialized processes like 5-axis CNC machining and aluminum extrusion.
By understanding and correctly utilizing the G50 command, machinists can significantly enhance the accuracy, efficiency, and safety of their CNC lathe operations. As a leading provider of CNC fabrication services, we are committed to helping our clients achieve the highest levels of precision and quality in their manufacturing processes.
Get the latest trends and facts about CNC fabrication from our blog.
Shenzhen Runkey Precision Technology Co. Ltd, a subsidiary of the Tensun Group, is your trusted one-stop solution for custom manufacturing from prototyping to production.Transforming your idea into reality with digital manufacturing resources,streamlined processes, expert guidance,accelerated timelines, and uncompromising quality.
©2024. CNC Fabrication All Rights Reserved.