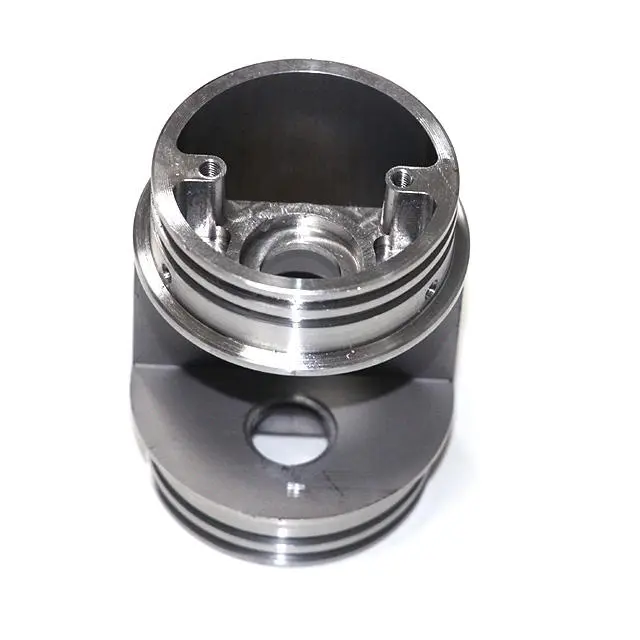
- +8615586668226
- [email protected]
- No. 30, Hongbang Industrial Park, Shenzhen
CNC woodworking involves using computer-controlled machines, like CNC routers, to cut, carve, and shape wood with high precision. As a CNC precision manufacturing plant, we understand that the type of wood you choose significantly affects the outcome of your project. Choosing the right wood is crucial for achieving the desired finish, ensuring the longevity of the product, and optimizing the efficiency of the machining process.
When it comes to CNC, the material’s hardness, density, and grain pattern can influence the machine’s feed rate, the quality of the cut, and the overall look of the finished piece. For example, a hardwood like maple might be ideal for intricate carvings requiring durability, while a softwood like pine might be better suited for projects where a rustic aesthetic is desired. Our expertise in CNC machining and precision machining ensures that we can guide you in making the best choice for your specific needs.
Wood is broadly classified into two main categories: hardwood and softwood. This classification is based on the type of tree from which the wood is derived, rather than the actual hardness of the wood. Hardwoods come from deciduous trees, which are angiosperms, meaning they produce seeds enclosed in nuts or fruits. Softwoods, on the other hand, come from gymnosperm trees, often referred to as coniferous trees, which produce seeds in cones.
Understanding this basic distinction is essential for anyone involved in woodworking projects, especially when selecting materials for CNC machining. Our team, specializing in products for industries like Aerospace and Aviation, Automotive, and Medical Devices, often helps clients navigate these choices to ensure optimal results. The difference between hardwood and softwood isn’t just academic; it directly impacts the practicality and feasibility of various CNC applications.
Hardwood
Origin: Deciduous trees (trees that lose their leaves annually)
Examples: Maple, walnut, beech, oak, birch
Characteristics: Generally denser, harder, and more durable than softwoods. They often have a more complex cellular structure.
Uses: High-end furniture, flooring, and applications requiring strength and longevity.
Softwood
Origin: Coniferous trees (trees that retain their needles year-round)
Examples: Pine, fir, spruce, redwood
Characteristics: Typically less dense, softer, and easier to work with than hardwoods. They have a simpler cellular structure with tracheids for transporting water and nutrients.
Uses: Construction, paper products, and some types of furniture where a rustic look is desired.
Feature | Hardwood | Softwood |
Origin | Deciduous trees | Coniferous trees |
Density | Generally higher | Generally lower |
Hardness | Typically harder | Typically softer |
Grain | Often more complex and varied | Usually straighter and more uniform |
Growth Rate | Slower | Faster |
Cost | Generally more expensive | Generally less expensive |
Common Uses | Furniture, flooring, intricate carvings | Construction, paper products, some furniture |
CNC Suitability | Excellent for detailed work, durable projects | Good for larger, less detailed projects |
It’s a common misconception that all hardwoods are harder than softwoods. For instance, balsa wood, classified as hardwood, is one of the softest woods available. At our manufacturing plants, we consider these nuances when recommending materials for clients in the Electronics, Defense and Military, and Industrial Equipment sectors.
The cellular structure of wood plays a significant role in how it behaves during CNC machining. Hardwoods, with their complex structure including vessels, fibers, and parenchyma cells, tend to be more stable and less prone to warping. This makes them ideal for precision CNC work where intricate details and tight tolerances are required.
Softwoods, with their simpler structure primarily composed of tracheids, are generally easier to cut and machine. However, their lower density can lead to issues like tear-out or fuzzing, especially when using a router with a dull bit or an incorrect feed rate. Our experience in serving industries like Consumer Products and Energy and Renewable Energy has taught us that understanding these structural differences is crucial for achieving a smooth finish and preventing damage to both the material and the machine.
When it comes to hardwoods for CNC projects, certain species stand out due to their favorable properties. Maple is one of the hardest woods commonly used in CNC machining. Its fine, even texture and strength make it perfect for detailed 3D carving and projects requiring a smooth, polished finish.
Maple
Hardness (Janka): 1450 lbf
Color: Creamy white to light reddish-brown
Characteristics: Hard, strong, with a fine, even texture. Resistant to shock and wear.
Best Uses: Musical instruments, high-end furniture, flooring, intricate CNC carvings.
Walnut
Hardness (Janka): 1010 lbf
Color: Rich, dark brown
Characteristics: Strong, stable, with a beautiful grain pattern. Works well with both hand and machine tools.
Best Uses: Fine furniture, gunstocks, interior paneling, high-quality CNC projects.
Beech
Hardness (Janka): 1300 lbf
Color: Pale cream, sometimes with a pink or brown hue
Characteristics: Hard, strong, with good wear resistance. Steams well for bending.
Best Uses: Furniture, flooring, tool handles, turned objects.
In our work with sectors like Robotics and Pharmaceuticals, we often recommend these hardwoods for components requiring durability, precision, and a high-quality finish. For instance, walnut’s rich, reddish-brown color and stability make it a popular choice for custom projects where aesthetics are as important as functionality.
While hardwoods are often preferred for their durability and fine finish, softwoods have their place in the CNC world. Softwoods tend to be more affordable and easier to machine, making them suitable for larger projects, prototypes, or applications where cost is a significant factor.
Redwood
Hardness (Janka): 450 lbf
Color: Light reddish-brown to deep reddish-brown
Characteristics: Naturally weather-resistant and decay-resistant due to its inherent oils. Lightweight yet relatively strong.
Best Uses: Outdoor furniture, decks, siding, decorative CNC projects.
Pine
Hardness (Janka): 380-420 lbf (depending on the species)
Color: Pale yellow to light brown
Characteristics: Soft, lightweight, with a straight grain. Easy to work with but may have knots.
Best Uses: Furniture, trim, paneling, prototyping, and some CNC projects.
For industries like Construction and Architecture or Heavy Equipment, where larger components or prototypes are often needed, softwoods like pine or redwood can be excellent choices. Their lower cost and ease of machining can lead to faster turnaround times without sacrificing too much in terms of quality. We can offer Rapid Prototyping and On Demand Manufacturing that fit your needs.
When selecting wood for CNC machining, several mechanical properties come into play:
Hardness: Measured using the Janka hardness test, this indicates the wood’s resistance to denting and wear. Higher Janka ratings are better for high-traffic areas or components subject to abrasion.
Density: This affects the wood’s weight and its ability to hold fine details. Denser woods generally provide a smoother finish in CNC work.
Stiffness: This property determines how much the wood will deform under load. Stiffer woods are better for structural components.
Decay Resistance: Important for outdoor applications or items exposed to moisture. Redwood, for instance, is naturally decay-resistant.
Stability: Refers to how much the wood will shrink, swell, or warp with changes in humidity. Stable woods like walnut are preferred for precision CNC work.
Understanding these properties helps in choosing the right wood for specific applications. For example, in the Food and Packaging or Tooling and Dies industries, we might recommend a wood with high stability and decay resistance to ensure the longevity and safety of the products.
The direction of the wood grain significantly affects the outcome of CNC routing and carving. Cutting with the grain generally results in a smoother finish and requires less force, while cutting against the grain can lead to tear-out or chipping, especially in softer woods.
When planning a CNC project, it’s essential to consider the grain direction and adjust the toolpath accordingly. Techniques like climb milling (where the cutter moves in the same direction as the feed) can help minimize tear-out when working with challenging grain patterns. Our experience in CNC milling and 5 Axis CNC Machining allows us to optimize toolpaths for various wood types and grain orientations, ensuring the best possible results for our clients.
Engineered woods, such as plywood and MDF (Medium-Density Fiberboard), can be suitable for CNC machining, especially for certain applications. Plywood, made by gluing thin layers of wood veneer together, offers good stability and strength. It’s often used for furniture, cabinetry, and larger CNC projects where a uniform surface is needed.
Advantages of using plywood for CNC:
Stability: Less prone to warping or twisting compared to solid wood.
Uniformity: Consistent density and no knots or voids.
Cost-effective: Generally cheaper than solid hardwood.
Large sheet sizes: Suitable for big projects.
Challenges:
Edge finishing: The layered structure can make edge finishing more difficult.
Tool wear: The adhesives used in plywood can dull cutting tools faster.
Potential for tear-out: Especially on the surface veneers.
In our work with sectors like Art and Design and Telecommunications, we’ve found that engineered woods can be excellent choices for creating prototypes or producing components with complex shapes. Their uniformity and stability make them well-suited for intricate CNC work, but careful tool selection and feed rate adjustments are necessary to achieve a clean finish.
Choosing the right wood for your CNC project involves considering several factors:
Project Requirements: What is the intended use of the final product? Will it be indoors or outdoors? Does it need to be structural or purely decorative?
Aesthetic Preferences: What look are you trying to achieve? Do you want a rich, dark wood like walnut, or a lighter, more neutral tone like maple?
Detail Level: How intricate is your design? Fine details are best achieved with dense, stable hardwoods.
Budget: Hardwoods are generally more expensive than softwoods. Engineered woods can offer a cost-effective alternative.
Machine Capabilities: What type of CNC machine are you using? Some woods are better suited for certain machines or cutting tools.
Finishing: How do you plan to finish the product? Some woods take stains and finishes better than others.
By carefully evaluating these factors, you can select the wood that best meets your project’s needs. Our team at CNC precision manufacturing is always available to provide guidance and recommendations based on our extensive experience across various industries. Whether you’re in Aerospace and Aviation, Automotive, or any other sector, we can help you make an informed decision that ensures the success of your project. Contact us for Assembly and Surface Finishing!
What is the best overall wood for CNC machining?
There isn’t a single “best” wood for all CNC applications. For intricate, detailed work requiring durability and a fine finish, hardwoods like maple or walnut are excellent choices. For larger projects or those where cost is a concern, softwoods like pine or engineered woods like plywood can be suitable.
Can I use any type of wood with my CNC machine?
While most CNC machines can handle a wide range of woods, it’s essential to consider the wood’s hardness, density, and grain pattern. Very hard woods might require more powerful machines and specialized cutting tools, while very soft woods might be prone to tear-out if not handled carefully.
How do I prevent tear-out when CNC machining wood?
To minimize tear-out, use sharp cutting tools, adjust the feed rate and spindle speed appropriately, and consider the grain direction when planning your toolpaths. Techniques like climb milling can also help reduce tear-out.
Is it better to use hardwood or softwood for outdoor CNC projects?
For outdoor projects, it’s crucial to choose a wood that is naturally weather-resistant and decay-resistant. Redwood and cedar are popular softwood choices for outdoor applications, while some hardwoods like ipe or teak are also highly durable in outdoor settings.
Can I CNC machine wood that has knots?
Yes, you can CNC machine wood with knots, but it requires extra care. Knots are denser than the surrounding wood and can dull cutting tools faster. They can also be prone to chipping or cracking during machining. Adjusting the feed rate and using sharp tools can help mitigate these issues.
How does the moisture content of wood affect CNC machining?
The moisture content of wood can significantly impact its machining properties. Wood that is too wet can be difficult to cut cleanly and may warp or crack as it dries. Ideally, wood for CNC machining should have a moisture content of around 6-8% for hardwoods and 8-10% for softwoods.
Understanding the differences between hardwood and softwood is crucial for successful CNC woodworking.
Hardwoods, like maple and walnut, are generally better for intricate, detailed work requiring durability and a fine finish.
Softwoods, such as pine and redwood, can be suitable for larger projects, prototypes, or applications where cost is a concern.
Mechanical properties like hardness, density, stiffness, and decay resistance should be considered when choosing wood for CNC.
Grain direction significantly impacts the outcome of CNC routing and carving.
Engineered woods like plywood can be suitable for CNC machining, especially for projects requiring stability and uniformity.
Choosing the right wood involves considering project requirements, aesthetic preferences, detail level, budget, machine capabilities, and finishing plans.
Proper tool selection, feed rate adjustments, and consideration of grain direction can help minimize issues like tear-out.
Moisture content affects the machining properties of wood, with an ideal range of 6-10% depending on the type of wood.
By carefully considering these factors and leveraging our expertise in CNC precision manufacturing, you can select the best wood for your specific project, ensuring high-quality results that meet your exact specifications.
Get the latest trends and facts about CNC fabrication from our blog.
Shenzhen Runkey Precision Technology Co. Ltd, a subsidiary of the Tensun Group, is your trusted one-stop solution for custom manufacturing from prototyping to production.Transforming your idea into reality with digital manufacturing resources,streamlined processes, expert guidance,accelerated timelines, and uncompromising quality.
©2024. CNC Fabrication All Rights Reserved.