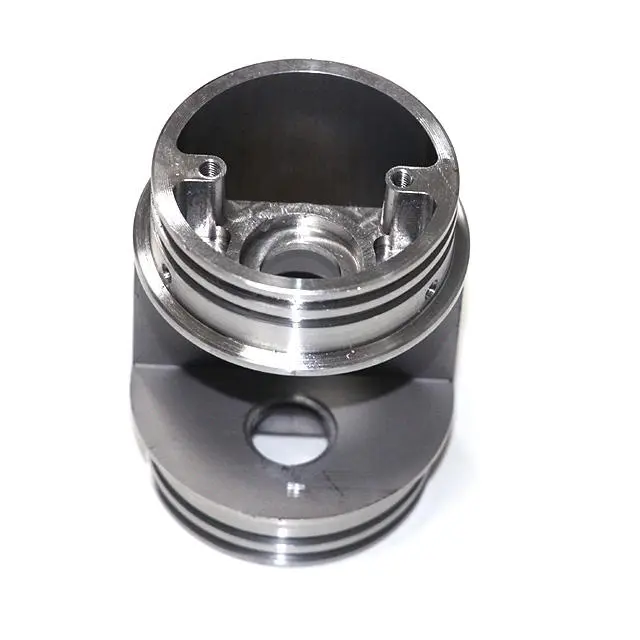
- +8615586668226
- [email protected]
- No. 30, Hongbang Industrial Park, Shenzhen
Carbide drill bits are cutting tools known for their exceptional hardness and heat resistance. These are important for cnc fabrication service plants, such as my plant, which serves industries like Aerospace, Automotive, and Medical Devices. Tungsten carbide, the primary component, is significantly harder than steel, making these drill bits ideal for drilling through tough materials. The use of carbide drill bits ensures precision and durability, especially in demanding applications.
Tungsten carbide is a chemical compound containing equal parts of tungsten and carbon atoms. This composition gives it remarkable hardness, ranking around 9 on the Mohs scale, just below diamond. This property allows carbide drill bits to maintain their sharpness longer and withstand high temperatures generated during drilling. As a result, they offer a longer tool life and require less frequent resharpening compared to hss drill bits, leading to higher productivity and cost-effectiveness.
When selecting a drill bit, it’s essential to understand the differences between carbide, cobalt, and high-speed steel (HSS). HSS drill bits are a common choice for general-purpose drilling. They are made from a steel alloy that includes elements like molybdenum and tungsten. HSS bits are known for their toughness and ability to withstand high temperatures, but they are not as hard as carbide or cobalt drill bits.
Cobalt drill bits are a step up from HSS in terms of hardness and heat resistance. They are made from a steel alloy that includes 5-8% cobalt. This addition of cobalt makes them harder and more resistant to heat than standard HSS bits. Cobalt bits are particularly effective for drilling stainless steel and other hard materials like cast iron. However, cobalt and carbide drill bits can be more brittle than HSS, making them prone to chipping if not handled carefully. Carbide drill bits are the hardest and most heat-resistant of the three. Carbide bits are suitable for the most demanding applications, such as drilling hardened steel or titanium alloys. Carbide cutting tools offer the longest tool life and can maintain their sharpness even at high cutting speeds.
Feature | Carbide Drill Bit | Cobalt Drill Bit | HSS Drill Bit |
---|---|---|---|
Hardness | Highest | High | Medium |
Heat Resistance | Excellent | Good | Fair |
Tool Life | Longest | Longer than HSS | Moderate |
Cost | Most expensive | More expensive than HSS | Least expensive |
Applications | Hardened steel, stainless steel, titanium, cast iron | Stainless steel, cast iron, tough alloys | General purpose, wood, plastic, soft metals |
Brittleness | Most brittle | More brittle than HSS | Least brittle |
Resharpening | Difficult, requires specialized equipment | Easier than carbide, but may still require special tools | Easiest to resharpen, can be done with standard tools |
Cutting Speeds | Can handle very high speeds | Can handle higher speeds than HSS | Lower cutting speeds compared to carbide and cobalt |
Material | Tungsten carbide | High-speed steel with 5-8% cobalt | High-speed steel |
Use Cases | Aerospace, Automotive, Medical, Industrial Equipment | Automotive, Metalworking, Construction | DIY, Woodworking, General Maintenance |
Choosing between carbide or cobalt drill bits depends on the specific material and application. While cobalt bits offer improved performance over HSS, carbide drills provide the ultimate solution for the most challenging drilling tasks. The last point is important. For instance, within the Medical Devices and Electronics sectors, the precision offered by carbide drill bits is essential.
Carbide drill bits come in various shapes and sizes, each designed for specific applications. Solid carbide drill bits are made entirely of tungsten carbide, offering maximum strength and rigidity. There are also carbide-tipped drill bits, which have a steel body with a carbide tip. These provide a balance of cost and performance.
The design of the drill bit‘s flutes, the spiral grooves that run along the length of the drill, also varies. For example, a twist drill with a high helix angle is effective for chip evacuation in deep hole drilling, while a straight flute drill is better suited for drilling brittle materials. Other specialized designs include step drills for creating holes of multiple diameters and center drills for accurately starting holes. For specialized tasks in the Energy, Robotics, or Telecommunications industries, selecting the appropriate type of drill bit can significantly impact the quality of the work. We at cnc fabrication service plants are equipped to handle such diverse requirements.
Drill bit selection depends on several factors, including the material you are drilling, the size of the hole, and the required precision. For soft materials like wood or plastic, HSS drill bits may suffice. However, when drilling tough materials like metal, especially hardened steel or stainless steel, carbide drill bits are the best choice.
The size of the hole also dictates the drill bit type. Small, precise holes often require solid carbide drills for accuracy and to prevent drill breakage. Larger holes may be more efficiently drilled with carbide-tipped drills. The depth of the hole is another consideration; deep holes require drills with good chip evacuation capabilities to prevent clogging and overheating. Look at our extensive selection of machining services, which includes specialized drill bit sets for different needs.
Hardness is a crucial factor in drill bit performance. The harder the drill bit, the better it can penetrate hard materials and maintain its sharpness. Tungsten carbide, with its exceptional hardness, allows carbide drill bits to outperform cobalt and carbide drill bits or HSS counterparts when drilling abrasive or hard materials.
However, hardness also comes with trade-offs. Harder materials are generally more brittle, meaning they are more susceptible to chipping or breaking under sudden impact or excessive force. This is why it’s essential to use carbide drills correctly, applying steady pressure and using the appropriate cutting speeds and feeds. Using a suitable cutting fluid can also help to reduce heat and friction, prolonging the drill bit’s life and preventing damage. As experts in cnc fabrication services, we emphasize the importance of using the right drill bit for each material to ensure both quality and safety.
Carbide drill bits are known for their ability to drill through a wide range of materials, particularly those that are difficult to machine with HSS or even cobalt drill bits. They are highly effective for drilling hardened steel, stainless steel, cast iron, titanium, and various alloys. In our operations, we frequently use carbide drill bits for projects in Aerospace, Defense, and Industrial Equipment, where high-strength materials are common.
In addition to metals, carbide drills can also be used to drill through composite materials, ceramics, and some types of hard plastics. However, when drilling non-metallic materials, it’s important to consider the specific properties of the material. For instance, some composites may require specialized drill geometries to prevent delamination or fiber pullout. Masonry bits are better for drilling into brick or concrete. They are very different from carbide drill bits.
Proper maintenance is key to extending the tool life of carbide drill bits. One of the most important practices is using the correct cutting speeds and feeds. Drilling too fast can generate excessive heat, leading to premature wear or even thermal cracking of the carbide. On the other hand, drilling too slowly can cause work hardening of the material, making it more difficult to drill.
Using a suitable cutting fluid is also crucial, especially when drilling metals. Cutting fluids help to reduce friction and heat, preventing the drill and workpiece from overheating. They also aid in chip evacuation, preventing the drill from clogging and reducing the risk of breakage. Regular inspection of drill bits for signs of wear or damage is also important. Dull or chipped drills should be replaced or resharpened to maintain drilling efficiency and prevent further damage to the drill or workpiece. With proper care, your carbide drill bits will last longer and perform better, reducing downtime and costs.
Carbide drill bits are generally more expensive than cobalt steel drill bits and HSS drill bits. This higher cost is due to the price of tungsten carbide and the more complex manufacturing processes involved. However, when considering the overall cost of drilling operations, the higher initial investment in carbide drills often pays off in the long run.
The longer tool life of carbide drill bits means less frequent replacements, reducing downtime and tooling costs. Their ability to drill at higher speeds and feeds also increases productivity, further reducing labor costs. Moreover, the superior precision and finish achieved with carbide drills can reduce or eliminate the need for secondary finishing operations, saving time and resources. While hss drill bits may seem more economical initially, they often require more frequent replacement and can lead to lower productivity.
The field of drill bit technology is constantly evolving, with ongoing research and development aimed at improving performance, durability, and efficiency. One area of focus is the development of advanced coatings, such as titanium nitride (TiN), titanium carbonitride (TiCN), and titanium aluminum nitride (TiAlN). These coatings further enhance the hardness, heat resistance, and wear resistance of carbide drill bits, allowing them to perform even better in demanding applications.
Another area of innovation is the optimization of drill geometries. Researchers are using advanced modeling and simulation techniques to design drills with improved chip evacuation, reduced cutting forces, and enhanced stability. These advancements lead to faster drilling, longer tool life, and better hole quality. Our commitment to staying at the forefront of technology ensures that we provide the best solutions for industries like New Energy and Custom Projects/Prototyping.
Choosing a reputable supplier is crucial when purchasing carbide drill bits. Look for suppliers like cnc fabrication service providers with a proven track record of quality and customer satisfaction. As a leading cnc fabrication service manufacturing plant, we pride ourselves on offering a wide range of high-quality drill bits suitable for various industries and applications.
Consider suppliers who offer technical support and guidance in selecting the right drill bit for your specific needs. A knowledgeable supplier can help you choose the optimal drill geometry, coating, and grade of carbide for your application, ensuring the best possible performance and tool life. We also offer comprehensive fabrication services and cnc solutions to meet diverse manufacturing needs.
The main advantage of using a carbide drill bit over an HSS drill bit is its superior hardness and heat resistance. Carbide drill bits can maintain their sharpness longer and withstand higher temperatures, making them ideal for drilling hard materials and for high-speed drilling operations.
Yes, carbide drill bits can be used to drill wood, but they may be overkill for softer woods. HSS drill bits are generally sufficient for most woodworking applications. However, carbide drills can be beneficial when drilling very hard woods or composite materials that contain wood fibers.
Signs that a carbide drill bit needs to be replaced include reduced drilling speed, increased force required to drill, excessive heat generation, poor hole quality, and visible wear or damage to the cutting edges. If you notice any of these signs, it’s time to replace the drill.
Solid carbide drill bits are made entirely of tungsten carbide, while carbide-tipped drill bits have a steel body with a carbide tip brazed or welded onto it. Solid carbide drills are generally more rigid and offer better performance in demanding applications, while carbide-tipped drills provide a more cost-effective solution for less demanding tasks.
Cobalt drill bits are an improvement over standard high-speed steel drill bits in terms of hardness and heat resistance. However, they are not as hard or heat-resistant as carbide drill bits. Carbide drill bits are generally considered the best option for drilling very hard materials or for high-volume production drilling where tool life and productivity are critical.
Yes, you can use a standard drill press with carbide drill bits. However, it’s important to ensure that the drill press is in good condition and capable of providing the necessary rigidity and power for the specific drilling application. For very demanding applications or high-precision work, a more robust and precise machine, such as a CNC milling machine, may be required.
By understanding the advantages of carbide drill bits and following the guidelines outlined in this article, you can make informed decisions when selecting and using these powerful tools. Whether you are in the Aerospace, Automotive, Medical Devices, or any other industry that requires precision drilling, carbide drill bits can help you achieve superior results and improve your overall productivity. As your trusted partner in cnc fabrication services, we are here to provide you with the expertise and high-quality tools you need to succeed. Contact us today to learn more about our offerings, including Rapid Prototyping and On Demand Manufacturing.
Get the latest trends and facts about CNC fabrication from our blog.
Shenzhen Runkey Precision Technology Co. Ltd, a subsidiary of the Tensun Group, is your trusted one-stop solution for custom manufacturing from prototyping to production.Transforming your idea into reality with digital manufacturing resources,streamlined processes, expert guidance,accelerated timelines, and uncompromising quality.
©2024. CNC Fabrication All Rights Reserved.