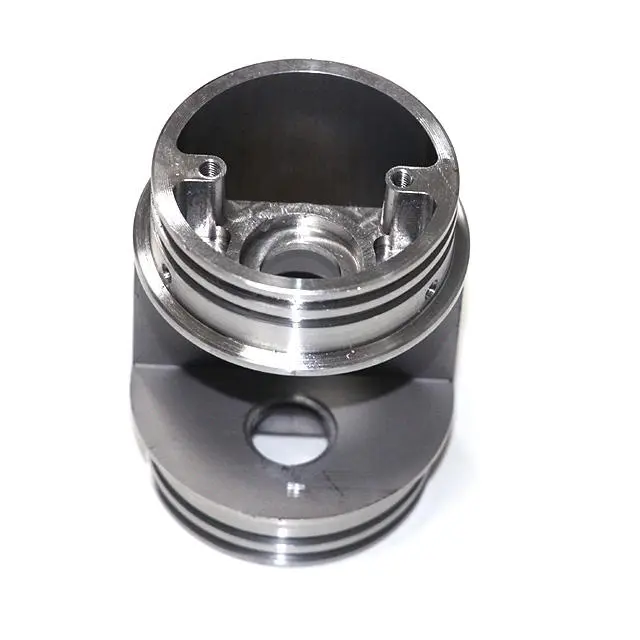
- +8615586668226
- [email protected]
- No. 30, Hongbang Industrial Park, Shenzhen
Electrical Discharge Machining (EDM) is a non-traditional machining method that uses electrical sparks to erode material from a workpiece. This process is particularly useful for cutting metal that is difficult to machine using conventional methods. EDM is widely used in industries requiring high precision, such as aerospace, automotive, and medical device manufacturing. The process involves a thin, electrically charged EDM wire that acts as an electrode, creating sparks that erode the workpiece to achieve the desired shape.
The importance of electrical discharge machining lies in its ability to create complex shapes and intricate designs with high accuracy. Unlike traditional machining methods, EDM can cut hard materials like tungsten and hardened steel without causing mechanical stress or distortion. This capability makes it invaluable for producing precision parts and components used in critical applications. At our CNC fabrication services plants, we leverage EDM to deliver exceptional results for our clients across various industries. As experts in this field, we understand the intricacies of EDM and continuously strive to improve our processes to offer the best solutions. We believe that our commitment to quality and precision sets us apart in the industry.
Selecting the right EDM wire machine is crucial for achieving optimal results in your machining operations. There are several factors to consider when making this decision, including the type of materials you will be machining, the complexity of the parts, and the required precision. Wire EDM machines are designed to handle a wide range of applications, from simple shapes to intricate designs. It’s important to evaluate the machine’s capabilities, such as its cutting speed, accuracy, and wire handling system.
Another critical factor is the machine’s ability to handle different types of EDM wire. Some machines are better suited for specific wire materials, such as brass wire or coated wire. Consider the machine’s wire rethreading system, which can significantly impact productivity. An automatic wire rethreading system allows the machine to automatically rethread the wire if it breaks, minimizing downtime. Our experience at CNC fabrication services has shown that investing in a high-quality EDM wire machine can lead to significant improvements in efficiency and product quality. We have seen firsthand how the right machine can transform a production process, making it faster and more reliable.
EDM wire comes in various types, each with its unique properties and applications. The most common type of wire used in EDM is brass wire, known for its excellent electrical conductivity and versatility. Other types of EDM wire include zinc-coated wire, copper wire, and various alloy wires. The choice of wire depends on the specific application and the desired results.
Brass EDM wire is widely used due to its balance of strength, conductivity, and cost-effectiveness. Zinc-coated wire offers improved cutting speed and surface finish, making it suitable for high-precision applications. Alloy wires, such as those with a steel core or copper core, provide enhanced strength and durability for demanding machining tasks. Understanding the characteristics of each type of wire is essential for selecting the best EDM wire for your application. At our facilities, we use a variety of EDM wires to meet the diverse needs of our clients, ensuring optimal performance and quality. We have found that experimenting with different wire types can lead to innovative solutions and better results.
Brass wire is a popular choice in EDM due to its excellent electrical conductivity and ability to maintain a consistent spark gap. Plain brass wire, typically composed of copper and zinc, offers a good balance of strength and conductivity. The zinc content in brass wire plays a crucial role in its performance, influencing factors such as cutting speed and surface finish. Hard brass wire, with a higher zinc content, provides increased strength but may be more prone to breakage. Soft brass wire offers better flexibility and is less likely to break during machining.
The choice between hard brass and soft brass depends on the specific application and the desired results. For example, soft brass is often preferred for intricate designs and thin workpieces where wire breakage is a concern. Hard brass is suitable for applications requiring higher cutting speeds and greater strength. Our experience at CNC fabrication services has shown that selecting the right type of brass wire can significantly impact the efficiency and quality of the machining process. We have seen how the right wire can enhance performance and reduce downtime.
Tensile strength is a critical factor in selecting EDM wire, as it determines the wire’s ability to withstand the forces exerted during the machining process. High tensile strength allows the wire to maintain its integrity under tension, reducing the risk of wire breakage. Low tensile strength can lead to frequent wire breaks, resulting in downtime and reduced productivity. The tensile strength of EDM wire is influenced by factors such as the wire’s diameter, material composition, and manufacturing process.
Different types of EDM wire offer varying levels of tensile strength. For example, zinc-coated wire typically has higher tensile strength compared to plain brass wire. The choice of wire should be based on the specific requirements of the application, considering factors such as the material being cut, the complexity of the design, and the desired cutting speed. At our CNC fabrication services plants, we carefully evaluate the tensile strength of our EDM wires to ensure optimal performance and reliability. We understand that using the right wire is essential for achieving consistent results and minimizing downtime.
The diameter of the EDM wire plays a significant role in the machining process, affecting factors such as cutting speed, accuracy, and surface finish. Thinner wires offer greater precision and are suitable for intricate designs and fine details. Thicker wires provide increased strength and are better suited for roughing operations and cutting thicker materials. The choice of wire diameter should be based on the specific requirements of the application.
For example, a smaller wire diameter is typically used for high-precision applications where accuracy is critical. A larger wire diameter may be preferred for applications requiring faster cutting speeds and greater strength. The diameter of the wire also affects the wire’s ability to flush debris from the cutting zone, which can impact the overall efficiency of the machining process. At our CNC fabrication services facilities, we offer a range of wire diameters to meet the diverse needs of our clients, ensuring optimal performance and quality. We have seen how the right wire diameter can significantly improve the precision and efficiency of the machining process.
Coated EDM wire, such as zinc-coated wire or gamma-phase coated wire, offers several advantages over plain brass wire. The coating enhances the wire’s cutting performance by improving its ability to generate sparks and remove debris from the cutting zone. Zinc-coated wire provides a faster cutting speed and a better surface finish compared to plain brass wire. The zinc coating also helps to reduce wire breakage, resulting in increased productivity and reduced downtime.
Gamma-phase coated wire offers even greater performance benefits, providing superior cutting speed, accuracy, and surface finish. This type of wire is particularly suitable for high-precision applications where quality is critical. The use of coated EDM wire can significantly improve the efficiency and quality of the machining process, making it a valuable investment for many industries. At our CNC fabrication services plants, we utilize coated EDM wires to deliver exceptional results for our clients, ensuring optimal performance and reliability. We have found that coated wires can significantly enhance the quality and efficiency of our machining operations.
Optimizing cutting speed and efficiency in EDM involves several factors, including the choice of EDM wire, the machine settings, and the machining process itself. Selecting the right type of wire is crucial for achieving optimal cutting speed. For example, zinc-coated wire and gamma-phase coated wire offer faster cutting speeds compared to plain brass wire. Adjusting the machine settings, such as the spark frequency and wire tension, can also impact cutting speed and efficiency.
Proper wire handling and maintenance are essential for optimizing machining performance. Ensuring that the wire is properly spooled and fed through the machine can help to prevent wire breakage and maintain consistent cutting speed. Regular maintenance of the EDM machine, including cleaning and replacing worn parts, is also crucial for optimal performance. At our CNC fabrication services facilities, we follow strict maintenance protocols to ensure that our machines are always operating at peak efficiency. We believe that a well-maintained machine is key to achieving consistent and high-quality results.
Wire straightness is a critical factor in EDM, as it affects the accuracy and consistency of the machining process. A straight wire ensures that the sparks are generated uniformly along the wire’s length, resulting in a consistent cut. Wire that is not straight can cause variations in the spark gap, leading to uneven cutting and reduced accuracy. Wire straightness is particularly important for applications requiring high precision and tight tolerances.
Ensuring wire straightness involves proper wire handling and storage. The wire should be stored on a spool in a way that prevents kinks and bends. The machine’s wire feed system should also be designed to maintain wire straightness during the machining process. At our CNC fabrication services plants, we use high-quality EDM wires and advanced wire handling systems to ensure optimal wire straightness and consistent performance. We understand that maintaining wire straightness is essential for achieving high precision and accuracy in our machining operations.
Ensuring consistent performance and high precision in EDM requires a combination of factors, including the use of high-quality EDM wire, proper machine settings, and regular maintenance. Selecting the right type of wire for the application is crucial for achieving consistent results. For example, zinc-coated wire and gamma-phase coated wire offer improved cutting performance and consistency compared to plain brass wire.
Proper machine settings, such as the spark frequency, wire tension, and flush settings, play a critical role in ensuring consistent performance. Regular maintenance of the EDM machine, including cleaning and replacing worn parts, is also essential for maintaining high precision. At our CNC fabrication services facilities, we follow strict quality control protocols to ensure that our machining processes deliver consistent and high-precision results. We believe that our commitment to quality and precision sets us apart in the industry.
What is EDM wire and how does it work?
EDM wire is a thin, electrically charged wire used in Electrical Discharge Machining (EDM) to erode material from a workpiece. The wire acts as an electrode, creating sparks that remove material to achieve the desired shape. It’s used extensively in our Machining Services to deliver precise and intricate parts.
Why is brass wire commonly used in EDM?
Brass wire is commonly used in EDM due to its excellent electrical conductivity, consistent spark gap maintenance, and cost-effectiveness. Its ability to balance strength and conductivity makes it ideal for various machining applications. Brass wire is a staple in our Fabrication Services.
What are the benefits of coated EDM wire?
Coated EDM wire, such as zinc-coated wire, offers enhanced cutting performance, faster cutting speeds, and a better surface finish compared to plain brass wire. The coating helps reduce wire breakage, increasing productivity. Our Precision Machining processes often utilize coated wires for superior results.
How does wire diameter impact EDM performance?
The diameter of the EDM wire affects cutting speed, accuracy, and surface finish. Thinner wires offer greater precision for intricate designs, while thicker wires provide increased strength for roughing operations. Choosing the right diameter is crucial for optimizing machining performance, a practice we emphasize in our CNC Solutions.
What is the role of tensile strength in EDM wire selection?
Tensile strength determines the wire’s ability to withstand forces during machining, impacting the risk of wire breakage. Higher tensile strength reduces breakage, ensuring consistent performance and minimizing downtime. This is particularly important in our 5 Axis CNC Machining services.
How can you optimize cutting speed and efficiency with EDM?
Optimizing cutting speed involves selecting the right EDM wire, adjusting machine settings, and ensuring proper wire handling and maintenance. Using coated wires and maintaining the machine regularly can significantly improve efficiency. These practices are integral to our On Demand Manufacturing services.
Get the latest trends and facts about CNC fabrication from our blog.
Shenzhen Runkey Precision Technology Co. Ltd, a subsidiary of the Tensun Group, is your trusted one-stop solution for custom manufacturing from prototyping to production.Transforming your idea into reality with digital manufacturing resources,streamlined processes, expert guidance,accelerated timelines, and uncompromising quality.
©2024. CNC Fabrication All Rights Reserved.