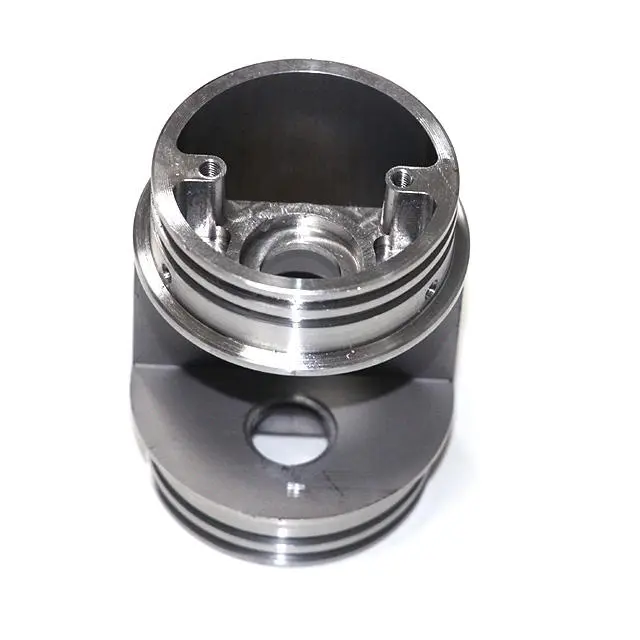
- +8615586668226
- [email protected]
- No. 30, Hongbang Industrial Park, Shenzhen
Drill bits are essential cutting tools used to create cylindrical holes in various materials. There are several types of drill bits, each designed for specific applications. The most common type is the twist drill bit, ideal for general-purpose drilling in wood, metal, and plastic. Masonry drill bits are designed for drilling into concrete, brick, and stone, featuring a carbide tip for durability. Spade bits have a flat, broad blade and are used for drilling large holes in wood. Other specialized drill bits include step bits for creating multiple-sized holes and auger bits for deep wood drilling.
Understanding the different types of drill bits is crucial for selecting the right tool for the job. For example, using a standard twist drill bit on concrete can damage the bit and result in poor-quality holes. Conversely, a masonry drill bit is unnecessary and potentially inefficient for drilling softwoods. Knowing the specific requirements of your project and the characteristics of each drill bit type helps ensure optimal performance and extends the life of your tools.
Carbide drill bits are favored in demanding applications due to their exceptional hardness and heat resistance. These drill bits are made from tungsten carbide, a material significantly harder than high-speed steel. This hardness allows carbide drill bits to maintain their sharpness longer, making them ideal for drilling through tough materials like stainless steel, hardened alloys, and cast iron. Additionally, carbide drill bits can withstand higher temperatures generated during drilling, reducing the risk of bit failure.
In industries such as aerospace, automotive, and medical devices, precision and durability are paramount. Carbide drill bits provide the necessary accuracy and longevity required for these applications. For instance, in aerospace manufacturing, carbide drill bits are used to create precise holes in aircraft components, ensuring structural integrity and safety. Similarly, in the automotive industry, they are essential for drilling through hardened steel parts, maintaining tight tolerances and high-quality finishes. The use of carbide drills also minimizes downtime caused by frequent bit changes, enhancing overall productivity.
The material properties of carbide drill bits significantly impact their performance. Tungsten carbide, the primary material, is known for its extreme hardness and wear resistance. However, the performance of a carbide drill bit also depends on factors such as grain size and the presence of binding agents like cobalt. Smaller grain sizes generally result in increased hardness and wear resistance, while cobalt enhances the bit’s toughness and ability to withstand impact.
The specific composition of the carbide material can be tailored to suit different applications. For example, material-specific carbide drills are designed to optimize performance when drilling particular materials. These bits may feature unique geometries and coatings that enhance chip evacuation and reduce heat generation. When drilling stainless steel, a material known for its toughness and tendency to work-harden, using a material-specific carbide drill can significantly improve drilling efficiency and bit life. It is a well-known fact that for instance when drilling through hardened steel parts, the right drill bit is needed, otherwise, the drill will be damaged.
Choosing the correct drill bit size is critical for achieving the desired results. The size of the drill bit determines the diameter of the hole it creates. Using the wrong size can lead to inaccuracies, damage to the workpiece, and even safety hazards. It’s essential to match the drill bit size to the specific requirements of the project, such as the size of the fasteners or the intended use of the hole.
When selecting a drill bit, consider the material being drilled and the type of hole needed. For example, if you need to drill a pilot hole for a screw, you’ll want a smaller bit that allows the screw threads to bite into the material. Conversely, if you need to create a clearance hole for a bolt, you’ll need a larger bit that allows the bolt to pass through freely. Many manufacturers provide drill bit size charts that can help you choose the right size for your application. Also when it comes to the size and type of drill, the decision is easier when you know what the exact purpose is.
Coatings and finishes play a crucial role in extending the life of a bit and enhancing its performance. Common coatings for carbide drill bits include titanium nitride (TiN), titanium carbonitride (TiCN), and titanium aluminum nitride (TiAlN). These coatings improve the bit’s hardness, reduce friction, and increase heat resistance. For instance, TiN coatings provide a gold-colored finish that enhances wear resistance, while TiAlN coatings are known for their excellent heat resistance, making them ideal for high-speed drilling.
The choice of coating depends on the specific application and the material being drilled. For example, TiCN coatings are particularly effective when drilling abrasive materials, as they offer superior wear resistance and reduced friction. Understanding the benefits of different coatings can help you select a carbide drill bit that will last longer and perform better in your specific application, whether it’s for general use or for specialized tasks like those encountered in CNC machining.
Selecting the right carbide drill bit for different materials requires considering the material’s hardness, toughness, and abrasiveness. For soft materials like aluminum and brass, standard carbide drill bits may suffice. However, for harder materials like stainless steel and titanium, it’s essential to choose material-specific carbide drill bits designed to handle these challenging materials.
When drilling stainless steel, a cobalt-alloyed carbide drill bit can provide superior performance due to its high heat resistance and ability to maintain sharpness. For extremely hard materials like Inconel, specialized carbide drill bits with advanced coatings and geometries are recommended. These bits are designed to reduce heat generation, improve chip evacuation, and minimize work hardening, ensuring efficient and precise drilling. For instance, when selecting the right carbide drill bit, it’s important to consider material hardness and abrasiveness.
Proper use and maintenance are essential for maximizing the performance and longevity of carbide drill bits. Always use the correct drilling speed and feed rate for the material being drilled. Excessive speed can generate too much heat, leading to premature bit wear, while insufficient speed can cause the bit to bind or break. Applying a suitable cutting fluid can help reduce heat, improve chip evacuation, and extend the life of the bit.
Regularly inspect your drill bits for signs of wear or damage. Dull or chipped bits should be replaced to prevent poor-quality holes and potential safety hazards. Store your drill bits in a dry, organized manner to protect them from damage and corrosion. Consider investing in drill bit sets that include a range of sizes and types, ensuring you have the right tool for various applications. Also, remember that the body of the bit should be examined for any signs of wear that could impact performance.
Finding high-quality carbide drill bits for specific industry needs requires careful consideration of the manufacturer’s reputation, product specifications, and customer reviews. Reputable manufacturers often provide detailed information about their products, including material composition, coatings, and recommended applications. Look for solid carbide drill bits from trusted brands known for their quality and reliability.
Customer reviews and industry forums can provide valuable insights into the performance of different carbide drill bits. Additionally, consider seeking recommendations from industry experts or colleagues who have experience with similar applications. For specialized industries like medical devices or robotics, it’s crucial to choose carbide drill bits that meet stringent quality standards and regulatory requirements. These bits should be capable of delivering the precision and reliability necessary for critical applications.
Innovations in carbide drill bit technology continue to improve performance, efficiency, and longevity. Advanced coatings, such as diamond-like carbon (DLC) and nanocomposite coatings, offer superior hardness, reduced friction, and enhanced heat resistance. These coatings can significantly extend the life of carbide drill bits and improve drilling performance in challenging materials.
Another area of innovation is the development of carbide drills optimized for specific applications. For example, researchers are developing new geometries and flute designs that improve chip evacuation and reduce cutting forces. These advancements can lead to faster drilling, improved hole quality, and reduced tool wear. Additionally, the integration of sensors and smart technology into drill bits is emerging, allowing for real-time monitoring of drilling parameters and predictive maintenance. When deciding to buy drill bits, it is important to consider how they perform in various conditions, especially if you’re dealing with tough materials.
As a CNC fabrication service provider, our expertise extends beyond machining to encompass a deep understanding of cutting tools, including carbide drill bits. Our experience in working with a wide range of materials, from aerospace-grade alloys to medical-grade plastics, gives us unique insights into the selection and use of drill bits. We understand that the right drill bit can make the difference between a successful project and a costly failure.
Our manufacturing plants leverage state-of-the-art CNC machines and cutting-edge technologies to produce high-quality products for various industries. This firsthand experience allows us to recommend the best carbide drill bit for your specific application, considering factors such as material properties, desired hole quality, and production volume. Whether you need to drill precise holes for consumer products or create intricate features for complex electronic components in electronics industry, we can guide you in choosing the right tool for the job.
Moreover, our commitment to quality and precision ensures that we use only the highest-quality carbide drill bits in our own operations. This commitment extends to our customers, as we provide expert advice and support to help them achieve optimal results in their projects. By partnering with us, you gain access to a wealth of knowledge and experience that can enhance your manufacturing processes and drive success.
What is a carbide drill bit?
A carbide drill bit is a type of drill bit made from tungsten carbide, a very hard and durable material. These bits are extremely resistant to heat and wear, making them ideal for drilling through tough materials like stainless steel and hardened alloys.
How do I choose the right drill bit for metal?
When choosing a drill bit for metal, consider the hardness and toughness of the metal. For softer metals like aluminum, a standard high-speed steel drill bit may suffice. For harder metals like stainless steel, a carbide drill bit is recommended due to its superior hardness and heat resistance.
Can carbide drill bits be used for drilling wood?
Yes, carbide drill bits can be used for drilling wood, but they may be overkill for softer woods. For most woodworking applications, high-speed steel drill bits or specialized wood drill bits like spade bits or auger bits are more suitable and cost-effective.
What is the difference between a twist drill bit and a masonry drill bit?
A twist drill bit is a general-purpose drill bit used for drilling into wood, metal, and plastic. It features a helical flute design that helps remove chips from the hole. A masonry drill bit is designed specifically for drilling into concrete, brick, and stone. It typically has a carbide tip and a more robust flute design to withstand the abrasive nature of these materials.
How can I extend the life of my carbide drill bits?
To extend the life of your carbide drill bits, use the correct drilling speed and feed rate for the material being drilled. Apply a suitable cutting fluid to reduce heat and improve chip evacuation. Regularly inspect your bits for signs of wear or damage, and store them in a dry, organized manner.
What are the benefits of using solid carbide drill bits?
Solid carbide drill bits offer several benefits, including exceptional hardness, heat resistance, and wear resistance. They are ideal for drilling through tough materials and maintaining precision in demanding applications. Solid carbide drills also tend to have a longer lifespan compared to other types of drill bits, reducing the need for frequent replacements. For example, the durability and precision of these drill bits are crucial for industries like medical devices.
Choosing the right carbide drill bit is essential for achieving precision, efficiency, and longevity in your drilling tasks. Here are the most important things to remember:
By understanding the different types of carbide drill bits available and considering the specific requirements of your project, you can choose the best tool to ensure success. Whether you’re working on a small DIY project or a large-scale industrial application, the right carbide drill bit can make all the difference. Remember that carbide drill bits are cutting tools designed to withstand tough conditions.
Get the latest trends and facts about CNC fabrication from our blog.
Shenzhen Runkey Precision Technology Co. Ltd, a subsidiary of the Tensun Group, is your trusted one-stop solution for custom manufacturing from prototyping to production.Transforming your idea into reality with digital manufacturing resources,streamlined processes, expert guidance,accelerated timelines, and uncompromising quality.
©2024. CNC Fabrication All Rights Reserved.