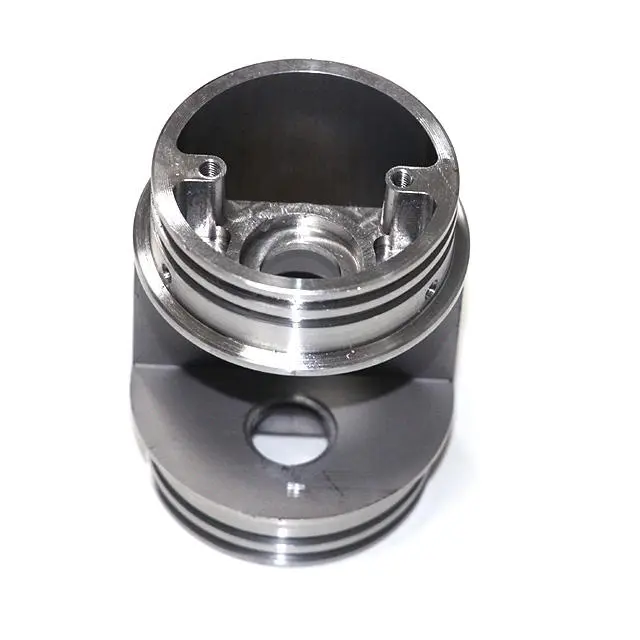
- +8615586668226
- [email protected]
- No. 30, Hongbang Industrial Park, Shenzhen
CNC machines are the backbone of modern manufacturing, offering unparalleled precision and efficiency. These machines, controlled by computer numerical control (CNC), are pivotal in various industries. But what are the different types of CNC machines, and which one best suits your needs? Broadly, they are categorized into CNC mills, CNC lathes, CNC routers, CNC plasma cutters, and CNC punch presses. Each machine serves a unique purpose. For instance, CNC mills are excellent for carving and cutting intricate designs, while CNC lathes are perfect for creating cylindrical shapes. In our facility, we utilize a range of these machines, enabling us to cater to diverse industry demands.
Choosing the right CNC machine hinges on understanding your specific manufacturing process. CNC punches, particularly turret punches, are ideal for sheet metal fabrication, especially when dealing with thin sheet metal and punching holes. On the other hand, if you’re working with thicker metal or require intricate 3D shapes, a CNC mill might be more appropriate. Consider the material you’re working with, for example, mild steel, carbon steel, or aluminum alloys. Each material requires a different approach, and the machine should be compatible with it. As an experienced CNC professional, I’ve seen how choosing the right machine can drastically improve production efficiency and part quality. The versatility and precision of CNC machines allow for the production of complex metal parts with tight tolerances, which is crucial in industries like aerospace and automotive.
A CNC punch press is a marvel of engineering, adept at shaping sheet metal with remarkable precision. But how does it work? Essentially, a punch press uses a punch and a die to create holes and shapes in metal sheets. The sheet metal is placed between the punch and the die, and force is applied, causing the punch to pierce through the sheet, creating the desired shape. CNC punch presses are computer-controlled, meaning every punch is executed with exactness, adhering to the programmed specifications. I often compare it to an artist’s precise brush strokes, each movement calculated and purposeful.
In CNC punching operations, the tool selection and setup time are crucial. A turret punch, for instance, houses multiple tools, allowing for quick changes and diverse punching operations. This machine is particularly useful for creating prototypes or handling short production runs in our metal fabrication services. It’s fascinating to see how these machines can transform a simple metal sheet into a complex sheet metal part, complete with intricate designs and precise dimensions. The ability to quickly and accurately create punching holes in different metal materials, like stainless steel or aluminum, makes the CNC punch press a vital component in metal fabrication. The precision and speed with which CNC punches operate significantly reduce production costs and time, making them a favored choice in the manufacturing industry.
Turret punches are a specific type of CNC punch that stands out in metal fabrication for their efficiency and versatility. But when is a turret punch the right choice? I recommend turret punches when you need to create multiple, consistent holes or shapes in sheet metal. They are particularly effective for projects that require a variety of tools and quick tool changes. With a turret punch, you can easily switch between different tools stored in its turret, making it ideal for complex fabrication projects. In my experience, turret punches excel in producing parts with numerous features like holes, notches, and forms.
Moreover, turret punches are suitable for both thin and thicker materials. They are an excellent choice for sheet metal work where precision is paramount. However, it’s important to note that while turret punches are great for punching operations, they might not be the best choice for cutting intricate contours. For such tasks, laser cutting or water jet might be more appropriate. Turret punches are widely used in industries such as automotive, aerospace, and in the production of metal products for consumer markets. Their ability to handle both short and long production runs efficiently makes them a staple in many metal fabrication shops. When faced with sheet metal fabrication tasks, I often find that a turret punch is the best suit due to its ability to quickly produce finished parts with high accuracy.
Selecting the right CNC machine for sheet metal involves careful consideration of several key factors. Firstly, assess the type of metal you’ll be working with. Different metals, such as aluminum alloys or stainless steel, have varying properties that affect how they should be machined. For instance, aluminum is generally easy to machine, while stainless steel requires a machine capable of handling its hardness and corrosion resistance. I always emphasize the importance of matching the machine’s capabilities with the material’s characteristics.
Another crucial factor is the complexity of your sheet metal parts. If your project involves intricate designs or requires tight tolerances, you’ll need a machine with high precision capabilities, like a CNC mill or a laser cutter. Setup time is also a consideration, especially for short production runs. A machine that allows for quick changes and minimal setup time, such as a turret punch, can significantly enhance efficiency. Additionally, consider the machine’s size and whether it fits your workspace, as well as its maintenance requirements. Some machines require more frequent maintenance than others, which can affect your production schedule. In our facility, we carefully evaluate each project’s requirements to select the most suitable CNC machine, ensuring optimal results.
Choosing the appropriate CNC machine for sheet metal fabrication is a critical decision that impacts the quality, efficiency, and cost-effectiveness of your production process. Factors to consider include the thickness of the metal sheet, the complexity of the part geometry, and the required production volume. For example, a punching machine or turret punch is ideal for creating holes and simple shapes in thin sheet metal, while a CNC milling machine is better suited for more complex shapes and thicker materials. Laser cutting and water jet are excellent options when it comes to cutting intricate patterns or working with materials that are sensitive to heat.
Tolerance in CNC machining is not just a technical term; it’s a measure of precision and quality. In simple terms, tolerance refers to the allowable deviation from a specified dimension. In CNC machining, achieving tight tolerances is often critical, especially in industries like aerospace and medical devices where precision is non-negotiable. I always tell my clients that the smaller the tolerance, the higher the precision of the finished part. However, it’s also important to understand that tighter tolerances can increase production costs and time.
CNC machines are capable of achieving remarkably tight tolerances, but the specific capability varies between different types of machines. For example, CNC mills and lathes are known for their high precision, while punch presses are more focused on speed and efficiency. When selecting a CNC machine, it’s essential to consider the tolerance requirements of your project and choose a machine that can meet those needs. In our operations, we always strive to balance precision with practicality, ensuring that we meet our clients’ specifications without unnecessarily driving up costs. The tolerance capability of a CNC machine is a direct reflection of its quality and sophistication. Achieving tight tolerances requires not only a high-quality machine but also skilled operators who understand the intricacies of CNC machining. In industries like aerospace and automotive, where components must fit together perfectly, the importance of tolerance cannot be overstated. It’s a critical factor in ensuring the functionality, safety, and reliability of the finished part.
CNC milling machines are a cornerstone of modern manufacturing, renowned for their versatility and precision. One of the primary benefits of using a CNC mill is its ability to create complex shapes and designs with high accuracy. Unlike punch presses, which are primarily used for creating holes and simple shapes, CNC mills can carve out intricate 3D designs from a solid block of material. This capability makes them ideal for creating prototypes, custom tools, and parts with complex geometries. I often recommend CNC milling for projects that require a high level of detail and precision.
Another significant advantage of CNC milling is its compatibility with a wide range of materials. Whether you’re working with metal, plastic, or even wood, a CNC mill can handle it. This versatility is particularly useful in industries that require parts made from different metal and non-metal materials. Additionally, CNC mills offer excellent repeatability, ensuring that each part produced is identical to the last. This consistency is crucial for production runs where uniformity is key. In our facility, we often use CNC milling to produce high-quality, precision parts for various applications, from automotive components to aerospace instruments. CNC milling machines offer several key benefits that make them an excellent choice for a wide range of metal fabrication projects. One of the most significant advantages is their ability to work with a variety of materials, including mild steel, carbon steel, and aluminum alloys. This versatility allows manufacturers to produce parts for various applications, from automotive and aerospace components to consumer products and industrial equipment.
When it comes to metal cutting, laser cutting and water jet are two of the most popular methods. But which one is better? The answer depends on your specific needs. Laser cutting uses a focused beam of light to cut metal, offering high precision and speed. It’s particularly effective for cutting thin to medium thickness sheet metal and can create intricate designs with clean edges. I often recommend laser cutting for projects that require fine details and smooth finishes.
On the other hand, water jet cutting uses a high-pressure stream of water mixed with an abrasive substance to cut through material. This method is incredibly versatile and can cut through virtually any material, including thick metal that might be challenging for laser cutters. Water jet cutting is also ideal for materials that are sensitive to heat, as it does not create a heat-affected zone. In our experience, water jet cutting is often the preferred choice for cutting thick materials or when working with materials that require a heat-free cutting process. Ultimately, the choice between laser cutting and water jet depends on factors like material thickness, type, and the desired finish. Both methods have their strengths, and the best choice varies from project to project. The choice between laser cutting and water jet for metal cutting depends on several factors, including the type of material, the thickness of the metal sheet, and the complexity of the cut. Laser cutting is known for its precision and speed, making it ideal for cutting thin sheet metal and creating intricate designs. It’s also a good option for materials that are reflective or have high strength, such as certain alloys. However, laser cutting can create a heat-affected zone, which might not be suitable for all materials or applications.
Choosing the right machining material for CNC is a critical decision that can significantly impact the success of your project. The first step is to understand the properties of different materials and how they interact with CNC machines. For instance, aluminum alloys are popular due to their lightweight and corrosion resistance, making them ideal for aerospace applications. Stainless steel, known for its strength and durability, is often used in medical devices and industrial equipment. I always advise clients to consider the end-use of their part when selecting a material.
Another important factor is the material’s machinability – how easily it can be cut or shaped by a CNC machine. Some materials, like brass and certain plastics, are easy to machine, resulting in lower production costs and faster turnaround times. In contrast, harder materials like titanium require more time and specialized tools, increasing costs. Additionally, consider factors like material cost, availability, and whether it meets specific industry standards or regulations. In our facility, we work closely with clients to help them select the best machining material for their CNC projects, ensuring optimal performance and cost-effectiveness. Choosing the right machining material for your CNC project is crucial for achieving the desired outcome. Factors to consider include the material’s strength, hardness, corrosion resistance, and strength-to-weight ratio. For example, aluminum is lightweight and has excellent corrosion resistance, making it a popular choice for aerospace and automotive applications. Stainless steel is known for its high strength and durability, while carbon steel offers a good balance of strength and cost-effectiveness.
CAD (Computer-Aided Design) and CAM (Computer-Aided Manufacturing) are integral to modern CNC machining. CAD software is used to create detailed 2D and 3D models of parts, providing a blueprint for the CNC machine to follow. I often describe CAD as the creative phase, where ideas are transformed into tangible designs. Once the CAD model is finalized, it’s converted into a format that the CNC machine can understand, typically a CAD file containing G-code. This is where CAM comes in.
CAM software takes the CAD model and generates the specific instructions that guide the CNC machine’s movements and operations. It’s like translating the design into the machine’s language, telling it exactly where to cut, how deep to go, and what tool to use. The synergy between CAD and CAM streamlines the manufacturing process, reducing errors and enhancing precision. In our operations, we utilize advanced CAD/CAM systems to ensure that every part we produce meets the exact specifications of our clients. This technology is a game-changer, allowing for the creation of complex and intricate parts that would be impossible to produce manually.
Maintenance is a critical aspect of operating CNC machines, ensuring they function at peak performance and longevity. Regular maintenance can prevent unexpected breakdowns, reduce downtime, and extend the lifespan of your machine. I always emphasize that a well-maintained machine is more reliable, produces higher quality parts, and is safer to operate. Maintenance tasks can range from simple cleaning and lubrication to more complex procedures like replacing worn-out parts or recalibrating the machine.
Moreover, maintenance schedules should be tailored to the specific machine and its usage. For instance, a machine that operates continuously or cuts hard materials may require more frequent maintenance than one used intermittently for lighter tasks. In our facility, we have a strict maintenance protocol to ensure our CNC machines are always in top condition. This proactive approach not only minimizes disruptions but also helps us maintain the high standards of quality and precision that our clients expect. Regular maintenance is crucial for ensuring the longevity and reliability of your CNC machine. Maintenance tasks may include cleaning the machine, lubricating moving parts, checking for wear and tear, and replacing worn components. It’s also important to follow the manufacturer’s recommendations for maintenance and to keep accurate records of all maintenance activities.
What is the difference between a CNC mill and a CNC lathe?
A CNC mill uses rotating cutting tools to remove material from a workpiece, while a CNC lathe rotates the workpiece against a stationary cutting tool. Mills are great for creating complex shapes, while lathes are ideal for cylindrical parts.
How do I choose between a punch press and a laser cutter for sheet metal fabrication?
Choose a punch press for high-volume punching operations on sheet metal, especially when creating holes or simple shapes. Opt for a laser cutter for intricate designs, high precision, and working with a variety of materials, including those sensitive to heat.
What are the most common materials used in CNC machining?
Common CNC machining materials include aluminum alloys, known for their lightweight and corrosion resistance; stainless steel, valued for its strength and durability; brass, which is easy to machine; and various plastics, each offering unique properties suitable for different applications.
How can I reduce production costs in CNC machining?
To reduce production costs, select materials that are easy to machine, optimize your designs for CNC processes, minimize setup time by using efficient tooling strategies, and consider the production volume – larger runs often reduce per-unit costs.
What are tight tolerances in CNC machining?
Tight tolerances refer to minimal allowable deviations from specified dimensions in CNC machining. Achieving tight tolerances is crucial in industries like aerospace and medical devices, where precision is paramount. It ensures parts fit and function correctly but can increase production time and cost.
Is CNC machining suitable for prototyping?
Yes, CNC machining is highly suitable for prototyping. It allows for the creation of high-precision, functional prototypes from various materials. CNC machines can quickly produce prototypes with complex geometries, enabling designers and engineers to test and refine their designs before full-scale production.
Here are the most important things to remember when selecting and using CNC machines for metal fabrication:
Understand the different types of CNC machines available, including mills, lathes, punches, and laser cutters, and choose the one that best suits your project’s needs.
Consider the properties of various machining materials, such as aluminum, stainless steel, and brass, and select the one that offers the best balance of performance, cost, and machinability.
Recognize the importance of tolerance in CNC machining and strive to achieve the tightest tolerances possible within your budget and time constraints.
Utilize CAD/CAM software to streamline the design and manufacturing process, reduce errors, and enhance precision.
Implement a regular maintenance schedule for your CNC machines to ensure their longevity, reliability, and safety.
Learn more about our machining services and how we can help you achieve your manufacturing goals.
Explore our fabrication services for comprehensive solutions tailored to your specific needs.
Discover the versatility of CNC solutions in various industries, from aerospace to consumer products.
Dive deeper into specific processes like CNC milling, understanding their unique advantages.
Understand how to leverage rapid prototyping for product development and innovation.
Consider your project requirements carefully, including material type, part complexity, production volume, and budget, to make informed decisions.
By understanding these key points and leveraging the expertise of experienced CNC professionals, you can optimize your metal fabrication processes, reduce costs, and achieve superior results.
We have extensive experience serving the automotive industry with precision CNC machining.
Our CNC fabrication services are trusted by the aerospace sector for critical components.
Partner with us for high-quality CNC solutions tailored to medical device manufacturing.
We offer rapid prototyping services to bring your innovative designs to life quickly.
Enhance your products with our comprehensive surface finishing options.
Get the latest trends and facts about CNC fabrication from our blog.
Shenzhen Runkey Precision Technology Co. Ltd, a subsidiary of the Tensun Group, is your trusted one-stop solution for custom manufacturing from prototyping to production.Transforming your idea into reality with digital manufacturing resources,streamlined processes, expert guidance,accelerated timelines, and uncompromising quality.
©2024. CNC Fabrication All Rights Reserved.