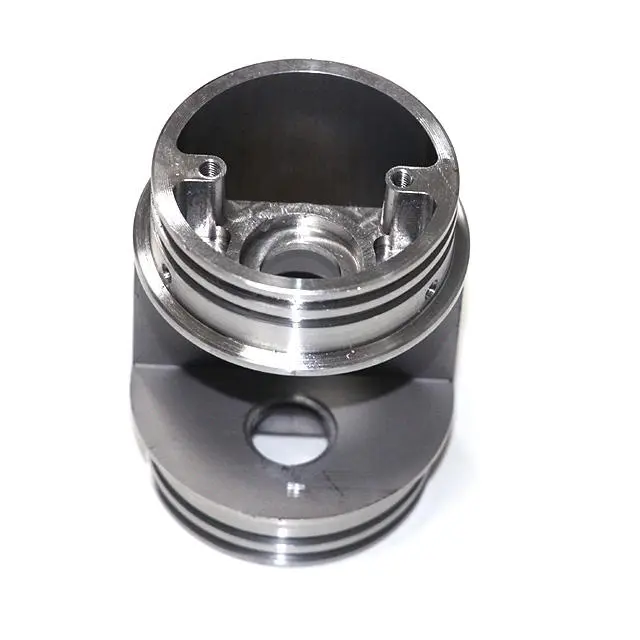
- +8615586668226
- [email protected]
- No. 30, Hongbang Industrial Park, Shenzhen
A CNC lathe is a type of machine tool that’s primarily used for shaping cylindrical workpieces. The workpiece is secured and rotated on a spindle, while a cutting tool is moved along the workpiece to remove material, creating the desired shape. Lathes are excellent for producing parts with features like threads, grooves, and tapers. Think of creating a chair leg or a baseball bat – those are perfect examples of lathe work. As a leading CNC fabrication service provider, we understand the nuances of CNC turning. Our expertise allows us to craft intricate components with exceptional accuracy.
Lathe machines are incredibly versatile, capable of performing a wide array of operations such as turning, facing, drilling, and threading. Some advanced CNC lathes even come equipped with live tooling, allowing for milling operations on the same setup. This capability significantly reduces production time and enhances the precision of complex parts. With decades of experience in metalworking, we leverage the power of CNC lathes to deliver superior quality and consistency.
A CNC mill is a versatile machine that uses a rotating cutting tool to shape a workpiece. Unlike a lathe, where the workpiece rotates, in a mill, the workpiece is typically stationary, and the cutting tool moves around it. CNC mills are ideal for creating flat surfaces, contours, and complex shapes. Milling machines offer greater flexibility in terms of the shapes and features they can produce. They’re commonly used for tasks like drilling, boring, and cutting slots or pockets. For example, if you need to create a mold for a plastic part or machine a complex gear, a CNC mill is the go-to machine.
Milling machines are classified by the number of axes they can move on. A 3-axis mill can move the cutting tool in three directions (X, Y, and Z), while a 5-axis mill adds two rotational axes, enabling the creation of highly intricate parts. Our machine shop boasts state-of-the-art CNC milling machines and is capable of handling projects of varying complexities. We specialize in producing precise components for a wide range of industries, including aerospace and automotive. We offer CNC milling services to our customers, ensuring high-quality and precise parts for their projects.
The primary difference between CNC lathes and CNC mills lies in how they operate and the type of parts they are best suited for. Lathes are designed for cylindrical work, where the workpiece rotates against a stationary tool. Mills, on the other hand, use a rotating tool that moves around a stationary or semi-stationary workpiece. This fundamental difference dictates the types of shapes and features each machine can effectively produce.
CNC Lathe:
Rotates the workpiece.
Ideal for cylindrical parts.
Creates features like threads, tapers, and grooves.
CNC Mill:
Rotates the cutting tool.
Ideal for flat surfaces and complex shapes.
Creates features like slots, pockets, and contours.
“The right machine for the job depends on the specific requirements of the part,” says John Smith, a veteran machinist with over 30 years of experience. “Understanding the capabilities of lathes and mills is essential for achieving optimal results.” Our extensive experience in CNC machining allows us to help our clients select the most appropriate process for their needs, ensuring both efficiency and precision.
Choosing between a CNC lathe and a CNC mill depends on several factors, including the shape of the part, the desired features, the material, and the required tolerance. If you need to produce a cylindrical part with features like threads or tapers, a lathe is likely the better choice. For parts with flat surfaces, contours, or complex shapes, a mill is generally preferred.
Here’s a simple table to guide your decision:
Feature | CNC Lathe | CNC Mill |
Cylindrical | Yes | No |
Threads | Yes | Limited |
Flat Surfaces | Limited | Yes |
Complex Shapes | Limited | Yes |
Tapers | Yes | Limited |
Important to consider are other factors, such as production volume and cost. Lathes are often faster for high-volume production of simple cylindrical parts, while mills may be more efficient for lower volumes of complex parts. As a full-service CNC fabrication service provider, we offer both CNC turning and milling services, allowing us to handle a wide range of projects with optimal efficiency.
CNC lathes and mills can process a wide variety of materials, including:
Metals (aluminum, steel, brass, copper, titanium)
Plastics (ABS, acrylic, nylon, polycarbonate)
Composites
Wood
Foam
The choice of material often depends on the application and the desired properties of the finished part. For example, aerospace components often require lightweight yet strong materials like aluminum or titanium, while medical devices may use biocompatible plastics. Our expertise extends to working with diverse materials, ensuring that we can meet the specific needs of our clients across various industries, including medical devices.
Lathes and mills each have their strengths when it comes to material processing. Lathes are particularly well-suited for machining metals that can be easily turned, while mills excel at shaping harder materials or those that require intricate detailing. We have extensive experience in machining various materials and can recommend the best option for your specific project requirements.
Yes, both CNC lathes and mills are excellent tools for rapid prototyping. They offer several advantages:
Precision: CNC machines can create prototypes with tight tolerances, ensuring that the prototype accurately reflects the design intent.
Speed: Compared to other prototyping methods, CNC machining can be relatively fast, especially for simple parts.
Material Variety: CNC machines can work with a wide range of materials, allowing prototypes to be made from the same material as the final product.
Repeatability: CNC machines can produce multiple identical prototypes, which is useful for testing and validation.
For example, if you’re developing a new automotive component, you can use a CNC mill to create a prototype from aluminum, allowing you to test its fit, form, and function before moving to mass production. Our prototyping services leverage the capabilities of both lathes and mills to help our clients bring their ideas to life quickly and accurately.
CNC lathes and mills are essential tools in a wide range of industries, including:
Medical
Energy
Consumer Products
Defense
In the aerospace industry, for example, CNC machines are used to produce precision components for aircraft engines, landing gear, and other critical systems. In the automotive industry, they’re used to manufacture engine parts, transmission components, and body panels. The medical industry relies on CNC machining for creating implants, surgical instruments, and diagnostic equipment. Our experience spans across these industries, and we pride ourselves on delivering high-quality CNC machined parts that meet the stringent requirements of each sector.
The versatility of lathes and mills makes them indispensable in modern manufacturing. They enable the production of complex, high-precision parts that would be impossible to create using traditional methods. “Without these machines, many of the products we rely on today simply wouldn’t exist,” notes Sarah Johnson, a manufacturing engineer at a leading aerospace company.
Regular maintenance is crucial for ensuring the longevity and optimal performance of CNC lathes and mills. Key maintenance tasks include:
Cleaning: Removing chips, dust, and debris from the machine and its components.
Lubrication: Ensuring that all moving parts are properly lubricated to reduce friction and wear.
Inspection: Regularly checking for signs of wear or damage, such as worn bearings or damaged cutting tools.
Calibration: Periodically calibrating the machine to maintain accuracy and precision.
Software Updates: Keeping the machine’s software up to date to ensure compatibility and access to the latest features.
Neglecting maintenance can lead to decreased accuracy, reduced efficiency, and even machine failure. “Proper maintenance is an investment that pays off in the long run,” says David Lee, a maintenance technician with over 20 years of experience. “It helps prevent costly downtime and ensures consistent quality.” Our commitment to quality extends to our maintenance practices, ensuring that our machines are always in top condition to deliver superior results.
CNC (Computer Numerical Control) technology has revolutionized manufacturing in several ways:
Increased Precision: CNC machines can produce parts with incredibly tight tolerances, far exceeding the capabilities of manual machines.
Improved Efficiency: Automation reduces labor costs and increases production speed, leading to greater efficiency.
Enhanced Consistency: CNC machines can produce identical parts repeatedly, ensuring consistency across large production runs.
Greater Flexibility: CNC machines can be easily reprogrammed to produce different parts, making them highly adaptable to changing production needs.
Reduced Waste: Precise cutting and optimized toolpaths minimize material waste, leading to cost savings and environmental benefits.
The introduction of CNC technology has enabled manufacturers to produce complex parts with unprecedented accuracy and efficiency. This has led to advancements in various industries, from aerospace to medical devices. “CNC technology has been a game-changer,” says Emily Carter, a production manager at a leading automotive manufacturer. “It’s allowed us to push the boundaries of what’s possible in manufacturing.” As a company at the forefront of CNC fabrication services, we’ve witnessed firsthand the transformative power of this technology.
The field of CNC machining is constantly evolving, with several key trends shaping its future:
Increased Automation: Integration with robotics and other automation technologies is further streamlining production processes.
Additive Manufacturing Integration: Combining CNC machining with 3D printing (additive manufacturing) to create hybrid manufacturing processes.
Artificial Intelligence (AI): Using AI for predictive maintenance, process optimization, and quality control.
Internet of Things (IoT): Connecting machines to the internet for real-time monitoring, data analysis, and remote control.
Advanced Materials: Developing new materials and machining techniques to meet the growing demand for lightweight, high-strength components.
These trends are driving innovation and pushing the capabilities of CNC machining to new heights. “The future of manufacturing is incredibly exciting,” says Michael Brown, a researcher specializing in advanced manufacturing technologies. “We’re on the cusp of a new era of intelligent, connected, and highly efficient production systems.” Our commitment to innovation keeps us at the cutting edge of these advancements, allowing us to offer our clients the most advanced CNC fabrication services available.
What is the difference between a manual lathe and a CNC lathe?
A manual lathe requires an operator to manually control the tool’s movement, while a CNC lathe is controlled by a computer program. CNC lathes offer greater precision, repeatability, and automation capabilities.
What is a 5-axis CNC mill?
A 5-axis CNC mill is a type of milling machine that can move the cutting tool in five different directions (X, Y, Z, A, and B). This allows for the creation of highly complex and intricate parts that would be impossible to produce on a standard 3-axis mill.
What is live tooling on a CNC lathe?
Live tooling on a CNC lathe refers to the ability of the machine to use powered tools, such as mills or drills, in addition to standard lathe tools. This allows for milling operations to be performed on the same setup as turning operations, increasing efficiency and reducing production time.
Can CNC machines be used for mass production?
Yes, CNC machines are widely used for mass production. Their ability to produce identical parts repeatedly with high precision and efficiency makes them ideal for large production runs.
What is the typical lifespan of a CNC machine?
The lifespan of a CNC machine can vary depending on factors such as usage, maintenance, and the quality of the machine. With proper maintenance, a high-quality CNC machine can last for 10-20 years or even longer.
What does CNC stand for?
CNC stands for Computer Numerical Control. It refers to the automation of machine tools by means of computers executing pre-programmed sequences of machine control commands.
CNC lathes and mills are essential tools in modern manufacturing, each with unique capabilities and applications.
Lathes are ideal for shaping cylindrical parts, while mills excel at creating flat surfaces and complex shapes.
Choosing between a lathe and a mill depends on the specific requirements of the project, including the shape of the part, the desired features, and the material.
Both machines can process a wide range of materials and are suitable for prototyping and mass production.
CNC technology has transformed manufacturing by increasing precision, efficiency, consistency, and flexibility.
The future of CNC machining is being shaped by trends such as increased automation, additive manufacturing integration, AI, IoT, and advanced materials.
Regular maintenance is crucial for ensuring the longevity and optimal performance of CNC machines.
Understanding the differences between CNC lathes and mills empowers informed decision-making in manufacturing.
We are a leading provider of CNC fabrication services, offering expertise in both turning and milling to meet the diverse needs of our clients across various industries.
Our commitment to quality, innovation, and customer satisfaction drives us to deliver exceptional results, leveraging the power of CNC technology to its fullest potential.
By understanding the nuances of CNC lathes and mills, manufacturers can optimize their production processes, enhance product quality, and stay ahead in today’s competitive landscape. As a trusted partner in CNC fabrication services, we’re dedicated to helping our clients achieve their manufacturing goals with precision, efficiency, and expertise. Contact us today to learn more about how our machining services can benefit your next project.
Get the latest trends and facts about CNC fabrication from our blog.
Shenzhen Runkey Precision Technology Co. Ltd, a subsidiary of the Tensun Group, is your trusted one-stop solution for custom manufacturing from prototyping to production.Transforming your idea into reality with digital manufacturing resources,streamlined processes, expert guidance,accelerated timelines, and uncompromising quality.
©2024. CNC Fabrication All Rights Reserved.